Printing with 3D Printers: A Comprehensive Guide
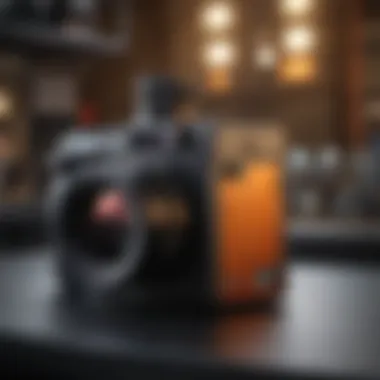

Intro
3D printing has reshaped how we think about manufacturing and design. The technology, which once felt like something straight out of science fiction, has become a crucial tool across various industries. From prototyping new products to creating intricate art pieces, the possibilities seem nearly endless. As more individuals and organizations dive into this world, understanding the nuances of 3D printing becomes increasingly important. This guide aims to provide an in-depth exploration of the technology, practical applications, and methodologies that define the 3D printing landscape.
Recent Advances
In recent years, the realm of 3D printing has witnessed remarkable growth, leading to innovative applications and methodologies that push the boundaries of what was once possible.
Latest Discoveries
Among the many intriguing discoveries, bioprinting has emerged as one of the most revolutionary. This technique allows for the creation of living tissues and even organs using 3D printing technology. Scientists have reported breakthroughs in vascularization – the process of creating blood vessels within printed tissues. This could potentially lead to regenerative medicine advancements and organ transplants in the future.
Moreover, metal 3D printing has matured significantly. Companies like Markforged and Desktop Metal have developed machines capable of producing high-strength metal parts with precision. These advancements reduce waste and energy consumption, making production processes more sustainable.
Technological Innovations
Technological innovations continue to redefine the landscape of 3D printing. For instance, advancements in materials science have led to the development of composites that possess unique properties. Materials infused with carbon fiber or Kevlar are used for applications requiring enhanced strength without adding significant weight. This is particularly valuable in the aerospace and automotive industries, where every gram counts.
Laser sintering and stereolithography have also seen enhancements. These processes are being fine-tuned for speed and accuracy, allowing for faster production cycles and more intricate designs.
"The future of 3D printing isn't just about creating objects; it's about revolutionizing entire industries."
Methodology
Understanding the methodology of 3D printing provides insight into its effectiveness and areas for improvement.
Research Design
Research in this field often takes a multidisciplinary approach, bringing together engineering, computer science, and materials science. This holistic perspective is essential as it allows researchers to tackle issues from various angles.
For example, researchers could evaluate the impact of different printing parameters on the mechanical properties of printed objects. They can design experiments to test the outcomes of modifying layer height, print speed, and material type.
Data Collection Techniques
Data is typically collected through several methods:
- Direct Measurement: Using tools and sensors to quantify dimensions and properties of printed items.
- Surveys and Interviews: Engaging with industry professionals to gather qualitative insights on their experiences and challenges.
- Case Studies: Analyzing specific applications of 3D printing to extract valuable lessons and identify best practices.
Prelude to 3D Printing
The world of technology has seen rapid advancements, but few innovations have had such a profound impact as 3D printing. This method has transformed not just manufacturing but also how creators, designers, and even enthusiasts approach their projects. Understanding the importance of 3D printing is crucial, as it lays the groundwork for delving into the complex components that make this practice so versatile and powerful.
One of the primary benefits of 3D printing is its ability to produce intricate designs with unparalleled accuracy. Unlike traditional manufacturing methods, where waste and excess materials are often the norm, 3D printing allows for a more efficient use of resources. This not only reduces costs but also lessens the environmental footprint—a consideration that is becoming increasingly critical in today’s world.
Moreover, it democratizes the field of production. With just a printer and a design, anyone from students to seasoned professionals can create functional models, prototypes, or even art pieces. This accessibility fuels creativity and innovation across diverse fields, ranging from healthcare to architecture. It's vital to highlight that learners and seasoned practitioners alike can both benefit from advanced techniques and best practices found in this guide.
Definition and Overview
To grasp the concepts surrounding 3D printing, it’s essential to start with a solid understanding of its definition. Simply put, 3D printing, also known as additive manufacturing, refers to processes that create objects by layering materials based on digital models. This innovative approach differs markedly from traditional subtractive manufacturing, where material is cut away from a larger block.
The process of additive manufacturing allows for complex geometries, enabling the creation of designs that might be impractical or impossible to achieve with conventional methods. For instance, consider the production of a bespoke prosthetic limb. Utilizing 3D printing means that the prosthetic can closely match the individual’s specific measurements, thus enhancing comfort and utility.
In this guide, we will explore the practical applications of 3D printing and its relevance in various industries, underscoring how it represents a shift towards more personalized and customizable production.
Historical Context
The journey of 3D printing began in the 1980s and has only gained momentum since then. The technology was pioneered by Charles Hull, who developed stereolithography, a technique that uses ultraviolet light to solidify liquid resin, creating three-dimensional objects layer by layer. This early model set the stage for a variety of techniques that would emerge in subsequent years.
As the 1990s rolled around, other processes like Selective Laser Sintering (SLS) and Fused Deposition Modeling (FDM) started to proliferate. These advancements introduced new materials, expanding the horizons of what could be printed. For example, FDM, which extrudes thermoplastic filaments, has become one of the most widely used methods, popular among hobbyists and professionals alike. Meanwhile, SLS opened doors for the use of powdered materials, pushing the technology closer to rapid prototyping.
Over the past two decades, the adoption of 3D printing has surged dramatically, not just in industrial settings but within personal and educational realms. As technology has become more accessible, there has been a notable increase in the number of startups and innovators focused on utilizing 3D printing in cutting-edge applications, hinting that this journey is just getting started.
Fundamentals of 3D Printing Technology
Understanding the fundamentals of 3D printing technology is crucial for grasping how this innovation works and how it reshapes manufacturing and design across numerous industries. At its core, 3D printing transforms digital models into tangible objects. This process allows for a level of customization and complexity that traditional methods often struggle to achieve.
Types of 3D Printing Techniques
3D printing isn’t just a single technique; it encompasses various methods, each with its unique characteristics and applications. Recognizing the main types of printing techniques is essential to choose the right one for a specific project or task. Below, we delve into three of the most well-known methods used today.
Fused Deposition Modeling (FDM)
Fused Deposition Modeling, commonly known as FDM, is perhaps the most recognized 3D printing method due to its accessibility and simplicity. Here, melted thermoplastic filament is extruded, layer by layer, to create an object. One of its key characteristics is its affordability. FDM printers are widely available, and materials like PLA and ABS filament are relatively inexpensive.
The main feature of FDM that sets it apart is its versatility. It works with a variety of materials, ranging from biodegradable options like PLA to tougher plastics like ABS. This adaptability makes FDM a popular choice for both hobbyists and professionals alike.
Advantages:
- Cost-effectiveness: FDM printers tend to be cheaper, making them suitable for beginners.
- Material range: Offers a variety of filaments that suit different needs.
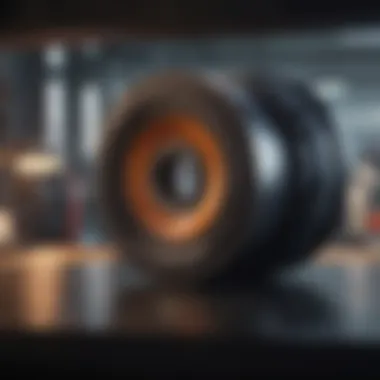
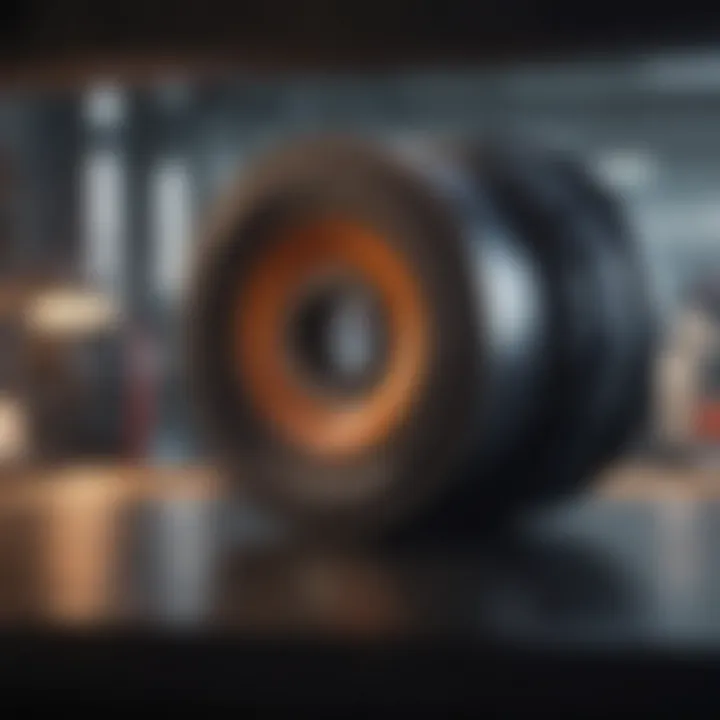
Disadvantages:
- Surface Quality: The layers can sometimes be visible, necessitating post-processing for a smooth finish.
Stereolithography (SLA)
Stereolithography, or SLA, sets itself apart from FDM by utilizing a liquid resin that hardens when exposed to ultraviolet (UV) light. This technique is renowned for its precision and ability to produce intricate details. The main characteristic of SLA is its capacity to create objects with excellent surface quality. As such, it is often used in industries that require detailed prototypes, like jewelry and dental applications.
What makes SLA unique is the process of building in a layer-by-layer manner while simultaneously solidifying the resin. This results in extremely accurate prints and a smooth finish without the need for extensive post-processing.
Advantages:
- Detailing: Produces more intricate designs than many other methods.
- Smooth finishes: Quality surpasses that of FDM in terms of surface smoothness.
Disadvantages:
- Cost: The initial investment can be higher due to the specialized equipment and materials needed.
Selective Laser Sintering (SLS)
Selective Laser Sintering, or SLS, takes a different approach altogether. This technique uses a laser to fuse powdered material into solid structures. A significant characteristic of SLS is its ability to work with a wide array of materials, including nylon, glass-filled nylon, and even metals.
This method is particularly beneficial for creating functional parts that need to withstand mechanical stresses. The unique feature of SLS is that it creates self-supporting structures, meaning there is no need for additional support materials during printing, which simplifies the post-processing stage.
Advantages:
- Durability: Parts created through this method are often more robust than those made with FDM or SLA.
- Design freedom: Allows for complex geometries that other techniques struggle with.
Disadvantages:
- Post-processing requirements: Parts need to be cleaned of excess powder, which can be a meticulous process.
Understanding CAD Models
Before any 3D printing can take place, a digital model must be created, usually through CAD software. Understanding how to design effective models for printing can significantly improve the quality and success of your prints. CAD models should be optimized in terms of geometry, size, and the complexity of features to ensure a seamless printing process.
Materials Used in 3D Printing
Understanding the materials involved in 3D printing is crucial, as they are fundamental to the quality and functionality of the final product. In addition to shaping the physical properties of printed items, the choice of material influences everything from durability to aesthetic appeal. As 3D printing continues to evolve, exploring different materials can unlock innovative applications across various fields.
Common Filaments and Resins
PLA
PLA, or Polylactic Acid, a bioplastic derived from renewable resources like corn starch, is touted for its ease of use. This makes it an ideal option for beginners and educational settings. A major perk is its low warping tendency, which promotes successful prints even without a heated bed. Plus, it comes in vibrant colors, appealing to those focusing on aesthetics. However, while it's biodegradable, its heat resistance isn't stellar, limiting its use in applications where strength and thermal stability are critical.
ABS
Next up is ABS, or Acrylonitrile Butadiene Styrene. Renowned for its strength and durability, ABS is often used for functional parts and prototypes. One of its standout features is the ability to withstand higher temperatures, making it great for items exposed to heat. However, users should be cautious as it emits a distinctive odor during printing and does require a heated bed to prevent cracking, thus it can prove tricky for novice users.
PETG
PETG, short for Polyethylene Terephthalate Glycol, is gaining traction in the 3D printing realm mainly due to its impressive impact resistance. It's less brittle than ABS and boasts excellent adhesion between layers, resulting in cleaner prints. Moreover, PETG is food-safe, broadening its application in creating containers and tools. Still, print settings need to be fine-tuned since it can produce stringing, which might complicate the print quality.
Resin Types
When it comes to resin, various types can cater to specific needs and effects. Photopolymer resins are commonly used in SLA and are capable of producing highly detailed prints with smooth finishes. This material shines in applications like jewelry and dental products. However, users must navigate the post-processing carefully to ensure a safe use of the final products, as many resins can be toxic if not handled properly. Additionally, the need for UV light exposure during curing can be an added consideration when working with resin types.
Advanced Materials
Metal Infused Filaments
Metal-infused filaments are noteworthy for their ability to combine the ease of plastic printing with the aesthetic and weight of metals. Often consisting of a mix of plastic and metal particles, these filaments create prints that have a metallic look and feel, which is appealing for decorative items and art. The added weight can also enhance the perceived value of the printed item. However, it's essential to recognize that these filaments require specialized nozzles and altered slicer settings due to their abrasive nature.
Flexible Materials
Flexible materials, such as TPU (Thermoplastic Polyurethane), can create products that require bending, stretching, or elasticity, like phone cases and grips. This adds versatility to the types of models that can be produced. A key characteristic of flexible materials is their rubber-like qualities, known for high resilience. Nevertheless, printing with flexible filaments can sometimes be a finicky process, as they can jam in standard extruders, requiring specific setups for successful outcomes.
Composite Materials
Composite materials, which blend different types of filaments—like wood, carbon fiber, or even glass with a base plastic—bring enhanced properties into the mix. For instance, carbon fiber composite can offer increased strength-to-weight ratios, making them attractive for industries such as aerospace. On the flip side, these special filaments often necessitate optimized settings in printers, and some may not be suitable for all types of printers, limiting accessibility for casual users.
Engaging with the various materials used in 3D printing opens up a realm of possibilities for innovation and creativity. Each type brings its own set of advantages and limitations, making the material choice pivotal in the printing process.
Setting Up a 3D Printer
Setting up a 3D printer might seem straightforward, but it’s actually a multifaceted process that requires careful consideration. The right setup ensures that your printer functions at its best, ultimately producing high-quality prints. Getting everything right from the beginning can save you a heap of trouble down the road and enhances your overall printing experience.
Choosing the Right Printer
Selecting the right 3D printer is akin to picking out a trusty steed for a long journey. Your choice influences not only the kind of projects you’ll undertake but also how satisfied you’ll be with the results. There are several key factors you should consider:
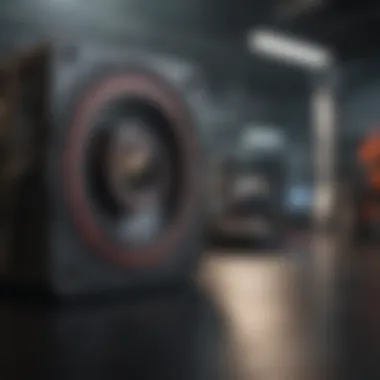
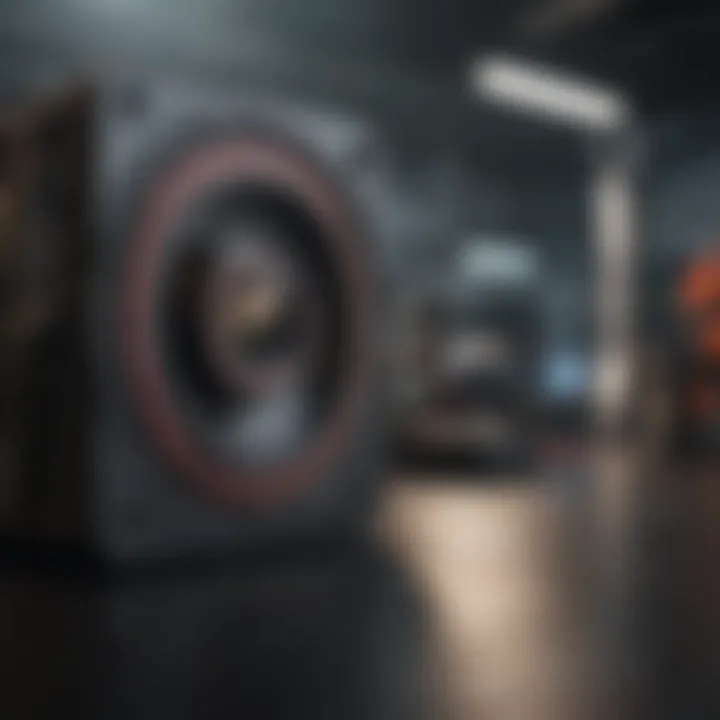
- Purpose: Are you printing prototypes for complex designs or crafting models for aesthetic pleasure? Knowing your end goal helps narrow down your choices.
- Print Volume: If you're planning on printing larger objects, look for a model with a substantial build volume. For small gadgets, however, a compact printer could suffice.
- Technology: Whether you go for an FDM, SLA, or SLS printer can dictate your material options and finish quality. Each technology has its strong points and drawbacks, so research thoroughly before settling.
- User Feedback: Chat forums or Reddit pages can provide honest experiences from fellow users. Knowing what worked or didn’t can save you from landing in a pitfall.
Ultimately, the right printer complements your specific needs, be it for hobbyist tinkering or professional development. Not every model fits every purpose; striking a balance that's tailored to your objectives will yield better outcomes.
Calibration and Maintenance
Once you've made your choice, calibration and maintenance are paramount. They form the bedrock of consistent print quality and extend the life of your machine. Calibration includes leveling the print bed and setting the nozzle height correctly. A bed that's not level can lead to a host of printing issues, from poor adhesion to uneven layers—pushing you down the rabbit hole of troubleshooting.
Regular maintenance is equally critical. Here are some aspects to keep in mind:
- Cleaning: Dust and debris can play havoc with sensitive components. Regularly clean the printer to remove residues that could affect performance.
- Lubrication: Keeping the mechanical parts well lubricated can prevent premature wear and keep things running smoothly.
- Firmware Updates: Manufacturers often release updates to enhance functionality. Staying current can improve your printer's performance and address bugs.
"An ounce of prevention is worth a pound of cure." This old saying rings true for printer setup; devoting time to get things right initially pays off.
By treating calibration and maintenance as part of your routine, you're not just ensuring optimal functioning; you also foster a greater understanding of the machine itself. A well-set-up printer is your best ally in turning creative ideas into tangible objects.
The Printing Process
The process of printing in three dimensions stands as a pivotal phase in the 3D printing ecosystem. This stage integrates various preparatory steps, such as model preparation, slicing, and initiating the print itself. Understanding the nuances of this process can spell the difference between a successful print and a failed attempt.
In essence, not only does it streamline your workflow, but it also minimizes errors and enhances the quality of the finished product. Engaging thoroughly with this phase allows one to appreciate the technical subtleties that ultimately yield a superior print outcome.
Preparing the Model for Printing
Scaling and Orientation
Scaling and orientation represent the foundation of preparing a model for printing. Scaling involves adjusting the dimensions of the 3D model to fit specific requirements, while orientation addresses the positioning of the model on the print bed. These two elements are particularly crucial because they heavily influence both the stability of the print and the amount of material used.
A notable characteristic of scaling is its potential impact on printing time. Larger models take longer to print, and smaller models may sacrifice detail. Therefore, finding the right size is akin to striking gold in a mine. By ensuring the orientation is optimized, you can reduce the need for excessive support structures, improving the overall aesthetics and stability during printing.
However, this approach isn’t without its pitfalls. An improperly scaled or oriented model may lead to complications like warping, which can render the print unusable. Thus, methodical attention at this juncture in the process can yield significant benefits for the overall endeavor.
Support Structures
Support structures are auxiliary frameworks required to stabilize certain parts of a print, most notably overhangs and intricate geometry. Their significance cannot be overstated. Without adequate support, parts of the model can sag or collapse under their weight, resulting in extensive printing issues.
The defining feature of support structures is their ability to be removed after the print is completed, often leaving only minor marks on the surface if used correctly. Popular among users, particularly in complex designs, they allow for more creative freedom in model design, facilitating prints that would otherwise be unachievable.
Still, reliance on supports can consume additional material and extend printing time. The key to efficiency lies in designing models that minimize support needs while ensuring safety during the printing process.
Slicing Software
Slicing software acts as the intermediary between the 3D model and the printer. It translates the model into layers, generating a G-code that the printer can read. Selecting suitable slicing software tailored to specific needs is crucial, as it influences the precision and quality of the print. With myriad options available, each comes with unique features, such as customizable supports and advanced slicing parameters.
Understanding how to use this software effectively can elevate one's printing capabilities. The goal is to ensure that the model's intricate features are preserved while maintaining optimal print time and material use.
Starting the Print
Monitoring the First Layers
Monitoring the first few layers of a print is a critical practice that can save time and materials. The initial layers form the foundation of the structure, and any imperfections here can spiral into significant problems later on. Notably, watching the initial layers allows for immediate corrections should an issue arise, be it an improper bed adhesion or incorrect feeding of filament.
This attentiveness is a hallmark of a savvy 3D printer operator. If the first layers are successful, the rest of the printing process tends to progress more smoothly, leading to a better overall result. The idea is to establish a reliable groundwork ensures the model's stability and minimizes the likelihood of failure.
Unexpected Interruptions
Unexpected interruptions can be the bane of any 3D printing project, arising from equipment malfunction, power outages, or even human error. These interruptions pose a challenge not only to the current print but potentially to future projects if not addressed properly.
A critical feature of modern printers is the ability to pause. A strategic pause can allow you to troubleshoot issues without losing the progress already made. Still, users have to be cautious of unwarranted pauses as they can lead to defects or gaps in the prints.
Understanding how to mitigate these interruptions through proper maintenance and preparation is essential for anyone seeking to maximize the potential of their 3D printing adventures.
"The success of a 3D print hinges on the details within the process; attention here can turn experimentation into triumph."
In short, navigating the printing process from preparing the model to starting the print requires a careful blend of technical know-how and practical skills. By honing these elements, one sets the stage for impressive results that can truly showcase the capabilities of 3D printing.
Post-Processing Techniques
Post-processing techniques are those finishing touches that transform a 3D printed object from a simple rendition of digital design into a polished, functional piece. It’s akin to fine-tuning a musical instrument after the initial build; without that crucial step, what you’ve created may not play in harmony with your expectations. These techniques significantly determine the final quality, usability, and aesthetic appeal of the printed object.
Among the prime reasons to engage in post-processing is the elevation of the surface quality. Fresh off the printer, a piece often carries layer lines, a product of the additive manufacturing process. Engaging in post-processing not only smooths out those unsightly seams but also enhances material integrity and overall durability.
Importance of Post-Processing Techniques
The significance of post-processing can be underscored through a few pivotal elements:
- Aesthetic Enhancement: Individuals, especially those in artistic or design-focused fields, often desire prints that are visually captivating. Techniques like sanding or polishing can elevate the item's appearance significantly.
- Structural Modification: Sometimes, the initial design may not provide sufficient strength or stability. Methods such as adding a coating or reinforcing options can be considered to enhance durability.
- Functional Improvement: Certain applications might require specific attributes like smooth movement or better fitting of components. Adjustments made during post-processing can ensure parts function harmoniously together.
Post-processing is not without its challenges and considerations, though. Time management becomes essential, as these techniques can often elongate the project timeline. Knowing when to opt for post-processing, and what to focus on, can make all the difference to your final result.

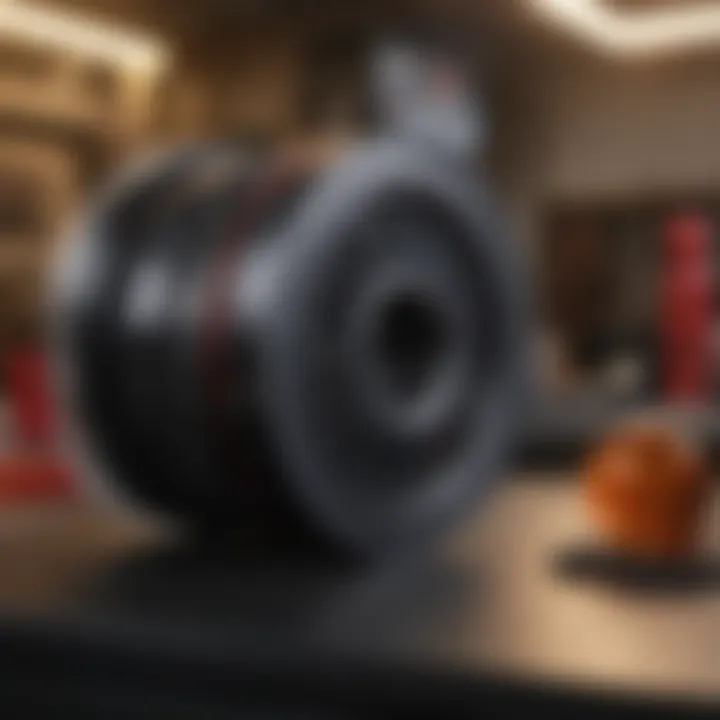
"The quality of a work piece often lies in the detail and precision of its finishing, turning mere prints into exemplary products."
Removing Supports and Finishing
Removing support structures after printing can be tedious, yet it forms an essential part of the post-processing workflow. Support structures are necessary during the print to ensure overhangs and complex shapes hold their form without collapsing. However, they often leave marks and seams on the final product.
When it comes to practical techniques, here are some commonly used methods:
- Breaking Away: For simpler structures, white-knuckle hand techniques may suffice. With cautious force, supports can be snapped off along natural seams.
- Cutting Tools: More complex models may demand blade or razor tools for precision. Always ensure blades are sharp to avoid jagged edges.
- Chemical Methods: In some cases, using chemicals like acetone (for ABS prints) can smoothen out surfaces where supports were connected. This method requires a delicate approach to avoid damaging the print.
A good finishing step follows support removal. This could include light sanding with various grit sandpapers, or using files for detailing. The goal is to make the surface uniform, which not only looks nicer but also improves the material’s ability to bond if additional layers are required later.
Painting and Assembly
The final phase of many post-processing workflows is painting and assembly. These steps can take an ordinary print and make it extraordinary. The use of paint piques interest as it can add life and character to a piece. Just like a blank canvas transformed by a brush, a painted model can stand out vividly.
A few considerations for painting 3D print:
- Surface Preparation: Ensure your print is free from dust and oils. A small wash with soap and water can go a long way. After drying, sand any rough spots to allow paint to adhere better.
- Priming: Applying a primer not only improves paint adhesion but also helps in achieving an even finish. Choose a primer compatible with your base material.
- Color Application: Airbrushes, spray cans, or paintbrushes — each has its merits. Choose based on the level of detail you aim to achieve. For intricate designs, an airbrush might be the way to go.
For assembly, accuracy is everything. Depending on your model’s complexity, you may need adhesives or mechanical fasteners. Iterate carefully as you fit pieces together; transitioning from individual parts to a completed model relies heavily on precision.
In essence, while the printing process is without doubt a remarkable feat of technology, it’s the post-processing techniques that lend the final flair and functionality, transforming your 3D printed item into something truly valuable.
Common Challenges in 3D Printing
3D printing may seem like a walk in the park, but it often holds its own set of challenges that can trip up even the most seasoned operators. Recognizing these common challenges is essential for not just avoiding pitfalls but also for enhancing the quality of prints. Grasping what to expect can save time, resources, and a fair bit of frustration. From print failures to material issues, these challenges warrant attention for anyone keen on mastering the craft.
Print Failures
Warpage
Warpage is a common but tricky issue in the world of 3D printing. This occurs when parts of a print lift from the build plate, leading to distortions in the final product. A key characteristic of warpage is that it typically happens during the cooling phase when different parts of the print contract at varying rates. As a result, you end up with a product that's not only off design but could also be structurally weak. It’s a major concern, particularly when working with materials like ABS that warp more easily due to their high thermal shrinkage.
One might wonder why understanding warpage is crucial in this guide. It's like learning to dodge potholes on a road; knowing they exist is the first step to avoiding costly repairs. The unique feature of warpage is that it can often be mitigated through good practices. A heated print bed, for instance, can help keep the temperature uniform during the printing process. However, some readers might consider it a disadvantage, as adding a heated bed can increase the cost of a 3D printer. In terms of benefits, a successful management strategy for warpage can significantly improve print quality, making it a critical element to grasp.
Layer Separation
Layer separation, another frequently encountered issue, arises when the layers of a print do not bond adequately with one another. This weak adhesion can lead to parts splitting during or after the printing process, which impacts the integrity of the final product. A key characteristic of layer separation is that it is often visible in prints with horizontal splits, essentially leading to a weakened structure.
This aspect is particularly important to discuss in a comprehensive guide, as it can diminish the effectiveness and utility of a 3D-printed object significantly. Understanding the roots of layer separation opens the door to better adhesion techniques, such as adjusting the extrusion temperature or modifying print speed. On the downside, inspectors may find that correcting layer separation issues might prolong the printing process. However, the advantage of producing solid and reliable prints far outweighs this inconvenience, making it essential knowledge for both newcomers and veterans.
Material Issues
Filament Quality
The quality of filament used in 3D printing can make or break a project. Lower-grade filaments may seem appealing at first glance due to their reduced cost, but they can lead to significant print failures, affecting everything from layer adhesion to surface finish. A key factor here is the consistency in diameter; uneven filament can create clogs or inconsistencies during the extrusion process. Because of this, sourcing high-quality filament is essential for reliable output.
In this article, understanding filament quality serves to highlight why it’s not just about what you print, but how you print it. Investing in quality filaments can mean the difference between a professional-grade final product and a sorry excuse for one. A common pitfall is the temptation to save on filament costs, often leading to more extensive troubleshooting in the long run. Ultimately, choosing quality filaments is aimed at enhancing the overall print experience.
Moisture Absorption
Moisture absorption is an often-overlooked issue that can severely impact the performance of filament, particularly in materials like Nylon or PLA. When filament takes on moisture from the air, it can lead to bubbling, stringing, or poor layer adhesion when printing. A hallmark of moisture-affected filament is that it often produces inconsistent extrusions due to the water vapor escaping during the heating process.
Addressing moisture absorption is crucial for maintaining high print quality. A key takeaway here is that storage matters; filaments should ideally be stored in airtight containers with desiccants. This notion isn’t just beneficial; it’s essential for achieving optimal results, especially in humid environments. That said, it does require an extra layer of diligence from users, but the rewards include higher fidelity and longer-lasting prints, making it a non-negotiable consideration in 3D printing.
Future Perspectives on 3D Printing
The future of 3D printing is a landscape ripe with opportunity and innovation. As advancements continue to push the boundaries of this technology, understanding the emerging trends and prospective applications in various industries becomes essential. Three critical themes in the domain of 3D printing's future are the expansion of its industry applications, the potential breakthroughs in technology, and the socio-economic implications it heralds. By examining these elements, one can grasp not just the significance of 3D printing today, but also the profound impact it may have on our lives and industries in the years to come.
Industry Applications
Aerospace
In aerospace, 3D printing stands as a game-changer, introducing streamlined manufacturing processes with considerable cost benefits. The ability to produce complex geometries that were previously deemed impractical contributes significantly to weight reduction in aircraft components. This is crucial; lighter planes translate to fuel savings and reduced emissions. Another beneficial aspect is rapid prototyping, which allows aerospace companies to iterate designs swiftly. However, the unique challenge here is the stringent regulatory requirements that ensure safety and reliability, introducing a sizable barrier to widespread adoption.
Healthcare
The healthcare sector is witnessing a surge in the application of 3D printing, primarily in the realm of personalized medical devices and prosthetics. This specificity allows for tailor-made solutions that can fit an individual's anatomical needs, offering much better comfort and functionality than traditional, one-size-fits-all products. Moreover, 3D printing facilitates the creation of complex structures, like tissue and even organs, though this technology is still in its infancy. The primary disadvantage remains the high cost of the initial investment in specialized equipment, which can deter smaller medical facilities from adopting this transformative technology.
Automotive
3D printing in the automotive industry emphasizes customization and flexibility in production. The capability to produce bespoke parts on-demand can drastically reduce inventory costs and improve the ability to respond to market changes. One notable feature is the opportunity for lightweight components, improving overall vehicle efficiency. However, a noteworthy consideration is the trade-off between speed and material properties; while 3D printing speeds up the manufacturing process, ensuring that parts meet the required performance standards remains a challenge.
Innovations on the Horizon
Bio-printing
Bio-printing represents a frontier in the field of 3D printing, where living cells are printed to create tissues that mimic natural biological functions. This technology could revolutionize drug testing and organ transplantation, offering a solution to the pressing shortage of donor organs. The ability to produce human-compatible tissues has made bio-printing a focal point of research and investment. Nevertheless, ethical concerns around bioprinting and the long-term viability of printed tissues present significant challenges that need addressing before it can be widely adopted.
Construction Printing
Construction printing, or 3D printing in the field of construction and architecture, has the potential to reshape how buildings are designed and constructed. Utilizing large-scale printers, entire structures can be created layer by layer using various materials—this approach can significantly cut labor costs and construction time. A key characteristic is the ability to create unique and complex architectural designs that would be hard to achieve via traditional methods. Yet, the definitive hurdle lies in the need for regulatory adjustments that can keep pace with these innovations and ensure that safety codes are upheld in this new paradigm of building.
"With emerging technologies, 3D printing is expected to redefine several industries, not just in terms of efficiency but also in the ways products are conceptualized and created."
The evolution of 3D printing offers a glimpse into a future filled with possibilities. Each innovation brings with it both unique advantages and noteworthy challenges, as industries adapt to integrate this disruptive technology into their operations. The symbiotic relationship between 3D printing and various sectors heralds an era of increased efficiency, personalization, and innovation that promises to alter the fabric of industry as we know it.