Exploring the Multifaceted Applications of Titanium
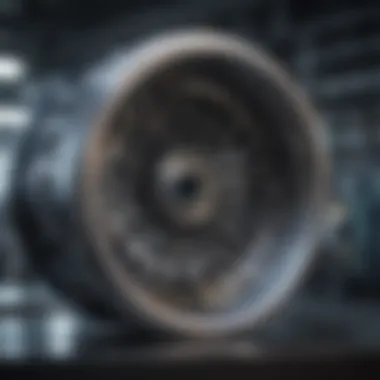
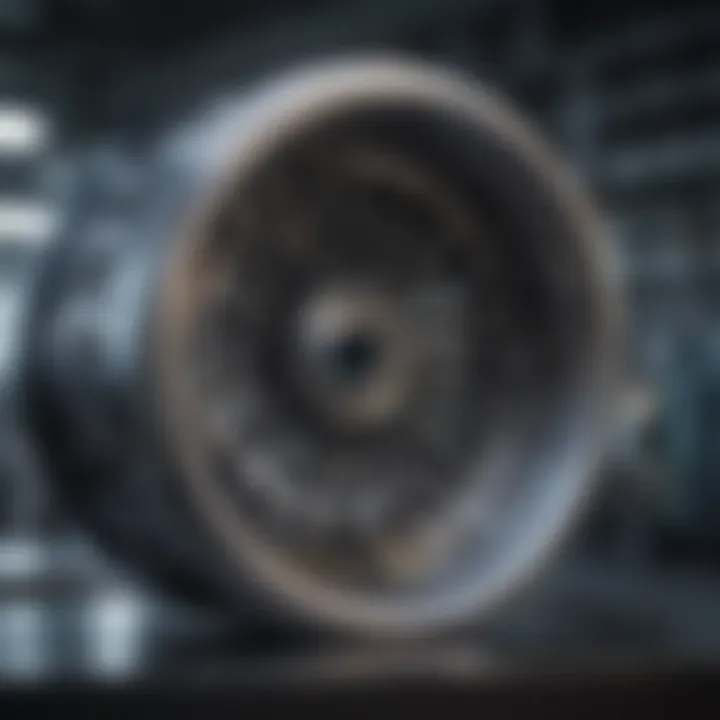
Intro
Titanium is a metal known for its robust yet lightweight characteristics. Its unique properties make it crucial in various fields, from aerospace to medical applications. As industries continue to innovate, titanium stands out due to its corrosion resistance, biocompatibility, and high strength-to-weight ratio. This article explores the different ways in which titanium contributes to advancements in technology and sustainability.
Recent Advances
Latest Discoveries
Research on titanium has discovered numerous advantages that can influence not just production but its applications. Innovations in extraction techniques have improved the efficiency of obtaining titanium ores. Scientists have also focused on developing new alloys. For instance, the titanium-aluminum-vanadium alloy is being used extensively in aerospace and automotive sectors. These discoveries highlight titanium's potential in enhancing performance under extreme conditions.
Technological Innovations
Manufacturing methods have evolved significantly. Additive manufacturing, or 3D printing, is becoming a prominent technique in creating titanium components. This process allows for intricate design possibilities, which traditional methods cannot achieve. Additionally, advancements in surface treatments are increasing titanium's fatigue resistance, making it even more desirable for high-stress applications.
Importance in Industries
Titanium is versatile. It's used in a wide range of sectors:
- Aerospace: Light and strong, titanium improves fuel efficiency in aircraft.
- Medical: Its biocompatibility allows for safe use in implants and surgical tools.
- Marine: Resistance to saltwater corrosion makes it ideal for maritime applications.
- Automotive: Weight savings can enhance performance and fuel efficiency.
Ending
In summary, titanium's unique properties make it invaluable across various industries. Ongoing research promises to unlock even more potential uses for this remarkable metal. Understanding and leveraging titanium can lead to innovative solutions for future challenges.
Prologue to Titanium
Titanium stands out as a versatile metal with extensive applications across various industries. Understanding titanium's fundamental properties offers insight into its effectiveness and adaptability in real-world scenarios. This section outlines the basic characteristics and historical context of titanium, laying the groundwork for its evaluation in specialized contexts.
Physical and Chemical Properties
Atomic structure
Titanium has a unique atomic structure that contributes to its favorable physical properties. It has an atomic number of 22, meaning it consists of 22 protons and, typically, the same number of electrons. This configuration results in a relatively high melting point and enhances its strength. One noteworthy characteristic is its hexagonal close-packed arrangement at lower temperatures, then transforming to a body-centered cubic structure at elevated temperatures. This property makes titanium suitable for applications requiring high temperature stability.
Its atomic structure also underlies its mechanical resilience, allowing for its use in demanding industrial applications.
Mechanical properties
Titanium exhibits remarkable mechanical properties, such as a high strength-to-weight ratio. This makes it an ideal choice in industries like aerospace, where reducing weight while maintaining strength is crucial. The tensile strength of titanium often exceeds that of steel, making it an attractive material for aerospace components. Additionally, titanium is known for its ductility, allowing it to be shaped without fracturing. These characteristics render titanium a beneficial option in construction and manufacturing, where strength and flexibility are needed to enhance performance.
Corrosion resistance
One of titanium's most significant attributes is its exceptional corrosion resistance. It forms a thin oxide layer on its surface, protecting it from environmental degradation, including exposure to extreme conditions such as saltwater. This property is vital for industries like marine and chemical processing, where materials are subject to corrosive environments. The corrosion resistance also contributes to the longevity and reliability of titanium components, lowering maintenance costs over time.
History of Titanium
Discovery and naming
Titanium was discovered in 1791 by the British chemist William Gregor. He identified the element in a mineral sample he collected, subsequently naming it after the Titans of Greek mythology, denoting strength and power. Understanding the history of its discovery illustrates how titanium emerged as an important metal in both academic and industrial circles. The initial difficulties in isolating pure titanium limited its early applications, which is important to consider when analyzing its growth in various fields.
Industrial introduction
In the 20th century, titanium began to enter industrial usage thanks to advancements in extraction methods. The Kroll process invented in the 1940s enabled the extraction of titanium from titanium tetrachloride. This breakthrough made it economically viable to produce titanium on a large scale. The introduction of titanium into industries like aerospace and defense was particularly significant, paving the way for its wider adoption in different sectors.
Evolution of applications
Over the years, the evolution of applications for titanium has been remarkable. Initially limited to niche usages, titanium found its place in the aerospace industry due to its lightweight yet strong nature. This was soon followed by its application in medical devices, where biocompatibility was vital. Today, titanium is also utilized in electronics and automotive industries, showcasing its ability to adapt across various contexts. Understanding this evolution helps to appreciate titanium's role in technological advancements and its ongoing relevance in modern engineering.
Titanium in Aerospace Engineering
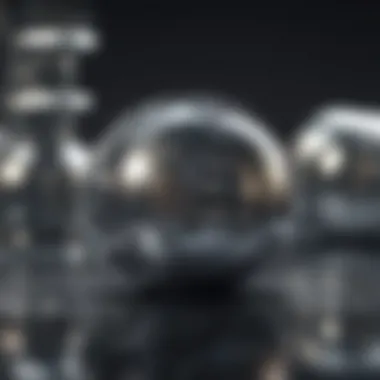
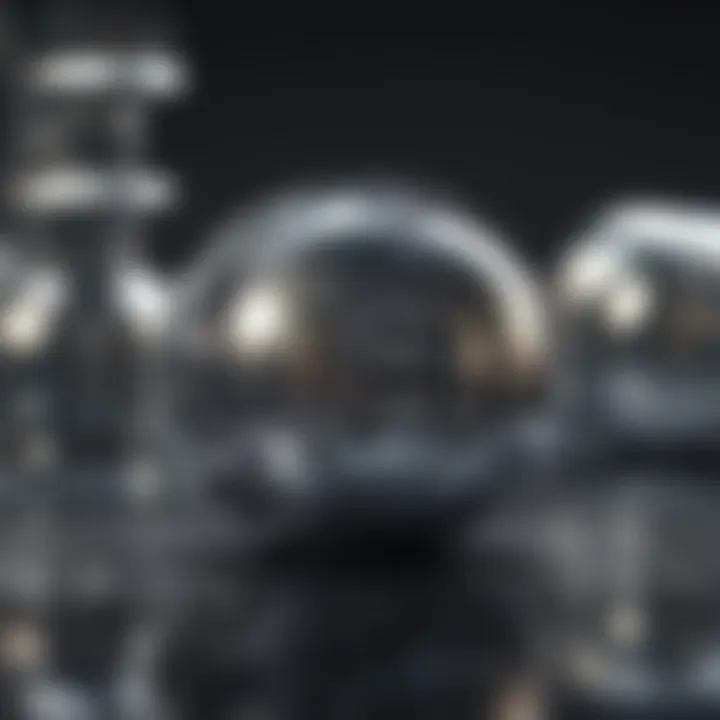
The role of titanium in aerospace engineering is of great significance. Given the stringent requirements for aircraft performance, titanium offers a suitable blend of strength and lightness. The aerospace sector demands materials that maintain structural integrity while minimizing weight, and titanium meets these standards comfortably. Its ability to withstand harsh environments, coupled with its versatility in manufacturing processes, makes titanium a preferred choice in this industry.
Structural Applications
Airframe components
Airframe components are critical for the overall stability and durability of an aircraft. The use of titanium in these parts enhances fuel efficiency and flight safety. One of the key characteristics of airframe components made from titanium is their lightweight nature. This is advantageous as it leads to reduced overall aircraft weight without compromising structural strength. Titanium's unique feature lies in its high tensile strength and resistance to fatigue, which are essential in high-stress environments like those experienced during flight. While titanium components are often more expensive than alternatives, the long-term benefits in performance and safety justify the initial investment.
Engine parts
Engine parts are among the most crucial components of any aircraft. The integration of titanium in engine parts improves both performance and efficiency significantly. The key characteristic here is the material's remarkable heat resistance. This allows engine parts made of titanium to function effectively in extreme temperatures, which is vital for safety and reliability. Additionally, titanium's capability to withstand oxidation at high temperatures is another unique feature that enhances its desirability in aerospace. However, the complexities in machining and forming titanium can be viewed as a disadvantage, requiring specialized equipment and processes.
Landing gear
Landing gear is subject to substantial mechanical stress during takeoff and landing. Titanium's unique combination of strength and lightness makes it an excellent choice for these components. The key characteristic that benefits landing gear is its resistance to corrosion. This property is essential, especially considering the exposure to various environmental conditions during an aircraft's operational life. A unique feature of titanium in this application is its excellent load-bearing capacity, allowing for the safe handling of heavy loads during landings. However, the high cost of titanium could be seen as a disadvantage when compared to traditional materials like steel.
Performance Benefits
Weight reduction
Weight reduction is a fundamental factor in enhancing aircraft performance. The use of titanium contributes significantly to this goal. The key aspect is that lighter aircraft translate to better fuel efficiency and increased payload capacity. The unique feature of titanium is its ability to offer a high strength-to-weight ratio, which is critical in aerospace design. However, the lower availability of titanium materials compared to more common metals may pose supply chain challenges.
Strength-to-weight ratio
The strength-to-weight ratio of titanium is one of its most compelling attributes. This characteristic is particularly crucial in aerospace engineering, where materials must endure great forces while keeping weight minimal. Titanium alloys provide an exceptional balance between robustness and lightness, making them highly desirable. The unique feature here is that this favorable ratio allows designers to innovate without the limitations posed by heavier materials. The significant cost of titanium can be a drawback, but the performance enhancements often outweigh this factor in high-end applications.
Temperature resistance
Temperature resistance is another area where titanium excels. In aerospace applications, components are frequently subjected to extreme thermal environments. The key characteristic of titanium's thermal stability allows parts to maintain integrity even under such conditions. Its unique ability to resist deformation and loss of strength at elevated temperatures is important during operation. However, the processing of titanium at high temperatures can present challenges, requiring careful management of manufacturing techniques to prevent defects.
"Titanium plays a pivotal role in aerospace engineering due to its unmatched combination of properties, addressing the demanding challenges of modern aviation."
In summary, titanium's applications in aerospace engineering highlight its structural and performance benefits, making it an essential material in aviation technology. The integration of titanium in various components ensures not just compliance with safety standards but also enhances overall operational efficiency.
Medical Applications of Titanium
The role of titanium in the medical field is significant, owing to its unique properties that make it ideal for various medical applications. The material’s combination of strength, lightweight design, and biocompatibility contribute to its widespread use in healthcare. Especially in producing biomedical implants, titanium offers benefits that have revolutionized surgical procedures and patient care.
Biomedical Implants
Joint replacements
Joint replacements are among the most common uses of titanium in medicine. These implants are used to substitute damaged joints, restoring mobility and function in patients suffering from arthritis or injury. The lightweight nature of titanium reduces stress on surrounding tissues during movement, which can lead to a quicker recovery and less pain post-operation. Importantly, titanium's strength allows it to withstand the substantial weight and pressure the joint endures during daily activities.
One key characteristic of joint replacements made from titanium is their excellent integration with bone, a process known as osseointegration. This property enhances the longevity of the implant, providing a highly beneficial option for patients with severe joint issues. However, one of the challenges is the potential for infection or complications at the implant site, which need to be monitored carefully.
Dental implants
Dental implants made of titanium represent a reliable option for replacing missing teeth. The specific aspect of these implants is their ability to fuse with jawbone, creating a stable foundation. Patients appreciate this because it mimics the feel and function of natural teeth. Moreover, titanium’s resistance to corrosion ensures the longevity of these implants, making them a popular choice in dentistry.
A key characteristic of dental implants is their biocompatibility, which minimizes the risk of rejection. This encourages many dental professionals to recommend titanium implants. However, aesthetics can be a concern for some patients, as the metal may not blend as seamlessly as ceramic materials in some cases.
Bone fixation devices
Bone fixation devices are crucial in the treatment of fractures and bone injuries. Titanium is often used for plates, screws, and rods that hold bones together during the healing process. One significant aspect of these devices is their strength-to-weight ratio. This ensures that they are robust enough to support bone healing while being light enough to facilitate easier surgical procedures.
The unique feature of titanium bone fixation devices is their excellent mechanical properties, which help to maintain stability in healing bones. However, some complications, such as metal fatigue over time, can occur and must be considered in long-term treatment plans.
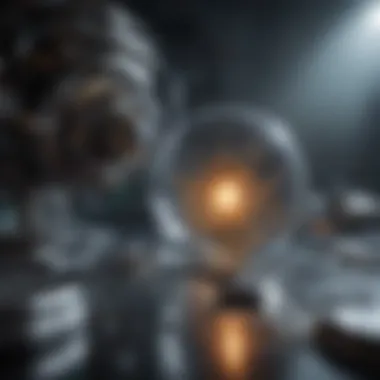
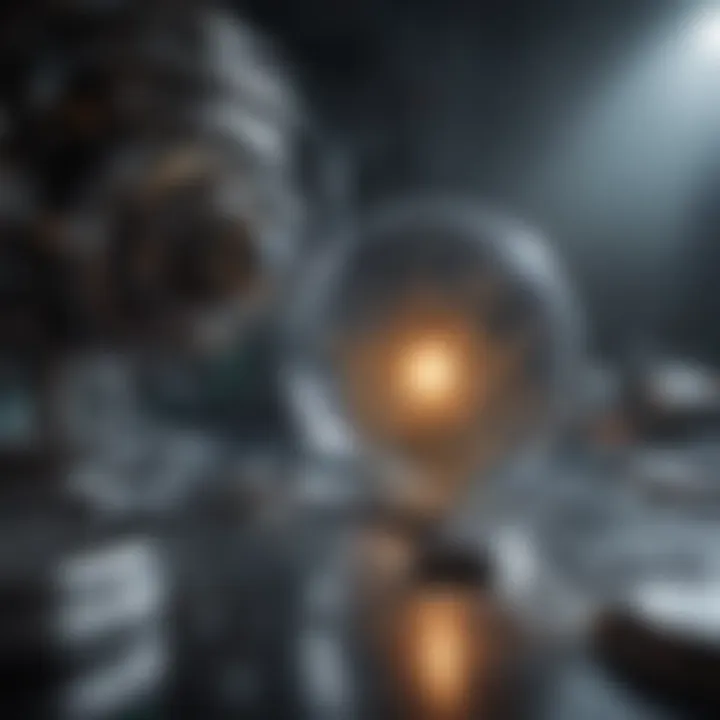
Advantages in Healthcare
The advantages that titanium brings to healthcare are broad and impactful. The material excels in numerous areas, particularly in aspects like biocompatibility, durability, and radiopacity. Each of these characteristics enhances its suitability for medical applications, ensuring better patient outcomes.
Biocompatibility
Biocompatibility is a crucial aspect of titanium that allows it to coexist with human tissues without causing adverse reactions. This property is vital in ensuring that implants do not provoke inflammatory responses. Many surgeons prefer titanium for surgeries due to this particular advantage, as it significantly enhances the outcomes of treatments and medical procedures.
A key feature of biocompatibility is how well titanium integrates with bone tissue. There are minimal risks of rejection, making it an attractive option for various implants. However, allergic reactions to metals, although rare, can occur in some patients, which is a concern that must be addressed prior to surgery.
Durability
Durability in medical implants ensures that devices can withstand the rigors of daily use over many years without degrading. Titanium exhibits exceptional strength and toughness, allowing it to last longer than many alternative materials. It is a preferred option for weight-bearing implants due to this characteristic.
While titanium offers extensive durability, factors such as wear and corrosion must also be monitored. The longevity of implants directly correlates with patient satisfaction and quality of life post-surgery.
Radiopacity
Radiopacity refers to the property of a material to be visible on X-rays, which is essential for both diagnosis and surgical planning. Titanium is radiopaque enough to be easily seen in imaging studies. This characteristic allows for effective monitoring of implant positions or the progression of healing post-surgery.
The unique feature of radiopacity helps surgeons to make informed decisions during and after surgical procedures. However, one disadvantage might be the potential need for additional imaging to assess surrounding tissues, adding complexity to patient care.
Titanium's unique properties not only enhance medical applications but also significantly improve patient outcomes, marking its importance in the healthcare sector.
Titanium in Manufacturing
Titanium plays a significant role in manufacturing across multiple sectors. Its unique properties, such as high strength, low density, and excellent corrosion resistance, make it an ideal choice for various applications. As the world focuses on sustainability and efficiency, titanium emerges as a material that not only meets these requirements but also offers enhanced performance. Understanding titanium's role in manufacturing aids industries to innovate and improve their processes.
Welding and Fabrication Techniques
TIG welding
TIG (Tungsten Inert Gas) welding is a widely used method for joining titanium materials. It involves a non-consumable tungsten electrode and an inert gas shielding to protect the weld area from contamination. The precision of TIG welding allows for excellent control over the heat input, which is crucial for titanium due to its sensitivity to temperature fluctuations. This makes it a preferred technique for intricate and high-quality welds. However, it can be slower compared to other welding methods, requiring skilled personnel to achieve optimal results.
Laser cutting
Laser cutting employs focused light beams to slice through titanium sheets effectively. This method is known for its accuracy and ability to create complex shapes with a high degree of detail. The non-contact nature of laser cutting reduces the risk of material distortion. However, it can be more costly than traditional cutting methods. The process does demand significant energy input, which raises considerations regarding overall energy consumption in titanium manufacturing.
Powder metallurgy
Powder metallurgy is a process that involves the compaction of titanium powder into desired shapes, followed by sintering to form a solid structure. This method allows for precise control over material composition and density. It is particularly advantageous for producing high-performance components with unique properties tailored for specific applications. While powder metallurgy can be economically advantageous for large-scale production, its initial setup costs may be higher.
Applications in Various Industries
Automotive
The automotive industry harnesses titanium for parts such as exhaust systems and engine components. The lightweight nature of titanium contributes to weight reduction in vehicles, improving fuel efficiency. This characteristic makes it a popular choice among manufacturers looking to meet strict emissions regulations. However, the cost of titanium can be a barrier, limiting its use primarily to high-performance vehicles.
Marine
Titanium’s resistance to seawater corrosion makes it particularly valuable in marine applications. It is used in components such as propellers, hulls, and fasteners. The longevity of titanium parts in the harsh marine environment can lead to lower maintenance costs over time. However, its high initial cost can deter some manufacturers from utilizing it extensively in production.
Electronics
In the electronics sector, titanium finds applications in devices requiring high thermal and electrical conductivity. Its use in various components, including connectors and casings, enhances durability and performance. The non-reactive nature of titanium adds to its attractiveness in this industry. Nonetheless, titanium’s cost may impact its adoption in lower-end consumer electronics.
Overall, titanium offers substantial advantages across manufacturing sectors. Understanding its applications and processing techniques proves essential for leveraging its benefits.

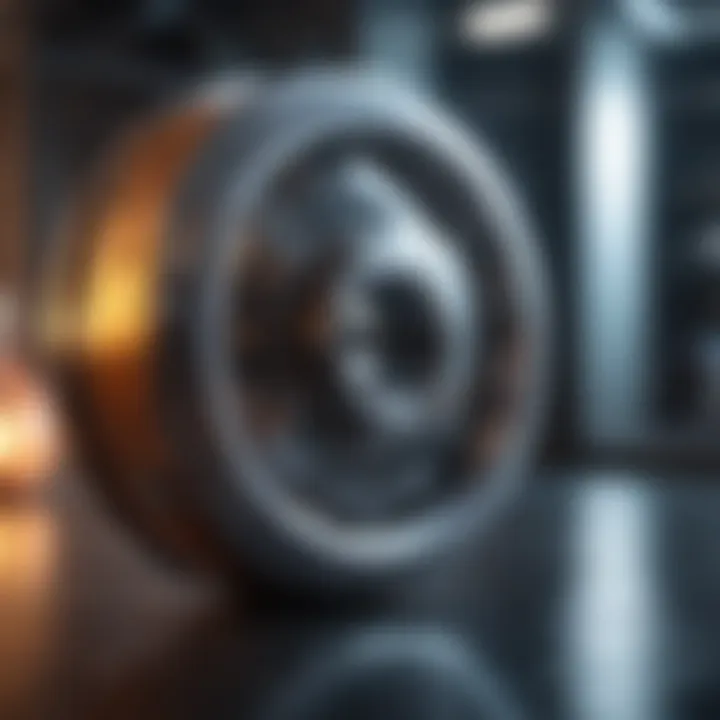
Environmental Considerations of Titanium Use
Understanding the environmental considerations of titanium use is essential in today's industrial context. As industries explore sustainable practices, recognizing the environmental impact of materials is key. Titanium, with its unique properties, offers opportunities for reducing ecological footprints. This section will discuss sustainability factors and improvements in extraction processes, both contributing to a more conscientious approach towards titanium applications.
Sustainability Factors
Recyclability of titanium
Recyclability is one of the most compelling qualities of titanium. This metal can be recycled without losing its intrinsic properties. Its high melting point and durability make it suitable for numerous cycles of reclaiming. When considering titanium for production processes, organizations can benefit from its recyclability. It reduces waste, conserves raw materials, and lowers landfill contributions. This characteristic is beneficial in efforts to create a circular economy, where materials are reused instead of discarded. In addition, the recycling process itself typically requires less energy than extracting new titanium, making it a more sustainable choice.
LCA (Life Cycle Assessment)
Life Cycle Assessment is a crucial tool for analyzing the environmental impacts of titanium throughout its entire lifespan. This strategic method evaluates all stages from raw material extraction, production, usage, and disposal. The strength of LCA lies in its comprehensive nature. It helps industries identify areas for improvement regarding sustainability. By quantifying environmental effects, stakeholders can make informed decisions about sourcing and utilizing titanium in a more eco-friendly way. However, LCA analyses can sometimes be complex, and their accuracy depends heavily on the data available, which may vary.
Energy consumption
Energy consumption during the extraction and processing of titanium can negatively influence its environmental footprint. Titanium requires significant energy to extract, making it crucial to explore methods that minimize energy usage. Reducing energy consumption not only lowers costs but also diminishes greenhouse gas emissions. Innovative extraction techniques and improved production processes focus on balancing energy input with output efficiency. Therefore, addressing energy consumption contributes significantly to enhancing the overall sustainability of titanium use.
Improvements in Extraction Processes
Challenges in extraction
Extraction of titanium comes with notable challenges. The primary method, the Kroll process, is energy-intensive and involves hazardous chemicals. These factors contribute to negative environmental impacts. However, understanding these challenges is essential for potential advancements. Finding ways to streamline extraction while minimizing pollution and energy consumption is vital. One present disadvantage is the current reliance on traditional methods which may hinder progress in discovering and implementing greener alternatives.
Emerging technologies
Advancements in technology hold promise for improving titanium extraction. Innovative approaches like biotechnological methods allow for less hazardous and more efficient extraction processes. These technologies could potentially reduce pollution and make extraction processes more sustainable. Highlighting the importance of investment in research, industries can become more efficient in recovering titanium. Nonetheless, emerging technologies often require upfront investments which may limit their adoption among smaller companies.
Reducing environmental impact
Efforts to reduce environmental impact involve integrating sustainable practices into titanium-related industries. Emphasizing responsible sourcing and energy-efficient processes is crucial. Initiatives focusing on reducing overall waste during production and promoting recycling further enhance the material’s eco-friendly profile. Future developments targeting reduction in ecological footprints will be beneficial. This is especially important as society increasingly demands sustainable materials that support environmental stewardship.
Future Prospects and Innovations
The exploration of titanium's future prospects and innovations is essential in understanding how this metal can continue to evolve and improve across different sectors. Titanium's unique properties, such as its remarkable strength-to-weight ratio and corrosion resistance, make it a valuable material. As industries seek to enhance performance and sustainability, advancements in titanium alloys and ongoing research in application methods will be critical. These elements not only pave the way for new products but also contribute to better environmental practices, ensuring that titanium remains a vital resource in a changing world.
Advancements in Alloy Development
New alloy compositions
New alloy compositions expand the usability of titanium significantly. They enable engineers to tailor the properties of titanium to meet specific requirements of various applications. A key characteristic of new alloy compositions is their potential to provide enhanced mechanical properties while maintaining low weight. For instance, innovations in titanium-aluminum alloys improve thermal stability, making them suitable for high-temperature applications such as aerospace.
However, developing these alloys can be complex, as it requires precise understanding of material science to balance strength and ductility.
Properties enhancement
Properties enhancement is another area where titanium shines. The ongoing research and development efforts focus on improving attributes like fatigue resistance and ductility. A prominent feature is the treatment processes that modify the microstructure of titanium alloys. Such treatments can lead to significant improvements in performance under mechanical loads. The benefits are clear: stronger and more durable components lead to longer service life and reduced maintenance costs in industries such as automotive and aerospace. Yet, one must balance enhancement processes with the costs associated with production.
Application-specific alloys
Application-specific alloys enable optimized performance in targeted sectors. These alloys are designed with particular use cases in mind, such as the aerospace or biomedical fields. A beneficial feature of application-specific alloys is that they can be engineered to exhibit properties that cater to specific environmental or mechanical conditions. For example, alloys used in implants must prioritize biocompatibility alongside strength. This specificity can also limit their use outside intended applications, which may restrict widespread adoption.
Research Trends in Titanium Applications
Emerging fields of study
Emerging fields of study in titanium technology are significant as they drive new applications and possibilities. Researchers are investigating titanium's potential in areas such as additive manufacturing and nanotechnology. The key characteristic of these studies is a focus on novel uses that go beyond traditional sectors. For instance, 3D printing of titanium parts offers improvements in material efficiency and design freedom. However, while promising, these emerging studies also face challenges in scaling and production economics.
Investment in titanium research
Investment in titanium research is crucial to ensure continued innovation. Increased funding leads to advancements in material properties and processing techniques. A crucial aspect of this is the development of new machinery and methodologies that improve efficiency. The unique feature of such investments is their ability to create a ripple effect, benefiting not only aerospace and medical industries but also sectors like energy and automotive. Nevertheless, it's important to prioritize allocating resources wisely to maximize returns in research outputs.
Collaboration between industries and academia
Collaboration between industries and academia fosters innovation and practical application of research findings. This partnership allows for a merging of theoretical knowledge with practical insights, enhancing the relevance of research. The key characteristic of such collaborations often results in projects that address real-world challenges, ensuring that findings translate into applicable technologies. However, maintaining effective communication and alignment of goals can sometimes be a hinderance in these partnerships, potentially slowing down progress.