A Detailed Study of Brass Alloys: Composition and Uses
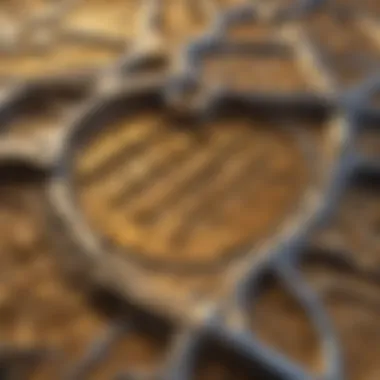
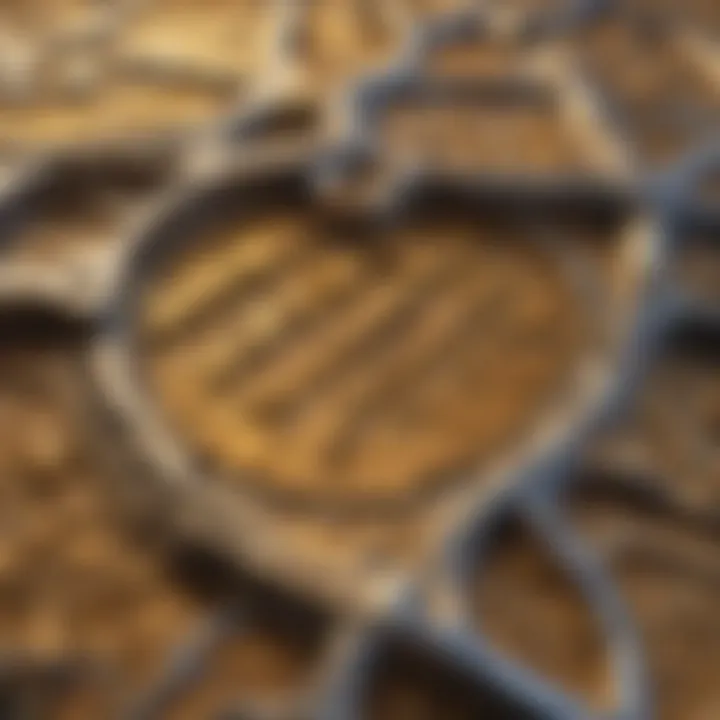
Intro
Brass, a versatile alloy primarily composed of copper and zinc, has captivated industries and craftsmen alike for centuries. Its distinct properties make it a beacon in construction, music, and art, to name just a few sectors. This article aims to traverse the landscape of brass alloys, navigating through their intricate compositions, functional properties, varied applications, and historical contexts, while also shedding light on the significance they hold in modern manufacturing.
Understanding brass is crucial, especially as it finds its place in a world where the demand for durable and malleable materials continues to grow. By employing a detailed examination of brass alloys, we aim to illuminate why they are the unsung heroes behind many everyday objects and specialized tools.
Recent Advances
Latest Discoveries
In the realm of metallurgical research, brass alloys have seen a plethora of recent advancements. Scientists and engineers are continually unraveling how to enhance the characteristics of these alloys, particularly through the addition of various elements such as lead or tin. Recent studies have revealed that incorporating small percentages of silicon into brass can significantly enhance its resistance to corrosion and degradation, making it a favored choice for marine applications.
Technological Innovations
Moreover, cutting-edge manufacturing techniques like additive manufacturing and advanced casting methods are redefining how brass alloys are produced. These innovations pave the way for highly customized applications, allowing for intricate designs that were once deemed impossible. For instance, tools and components can now be crafted with precision, reducing waste and improving overall efficiency.
The Essence of Brass Alloys
Brass alloys are not just a blend of metals; they are a symphony of different properties that come together to create materials that are both robust and aesthetically pleasing. The primary elements involved in making brass are copper and zinc, but other metals can be introduced to modify its qualities. Here, we'll take a closer look at some of these components and their roles:
- Copper: Known for its excellent conductivity, copper provides brass with electrical and thermal properties that are second to none.
- Zinc: This element lends brass its strength and malleability, allowing it to be easily shaped under pressure.
- Lead: Often added for machinability, lead makes manufacturing easier, but its use is dwindling due to health concerns.
- Tin: Enhancing corrosion resistance, tin can expand the lifespan of brass items significantly, making it suitable for outdoor use.
These components combine to form a material that can withstand a variety of stresses and strains, whether in a bustling musical instrument or a hard-working plumbing fixture.
"The beauty of brass lies not just in its appearance, but in its ability to adapt and perform across diverse settings."
Historical Context
Tracing back to antiquity, brass has played an instrumental role in the development of civilizations. The earliest uses date back to the Roman Empire, where it was valued for its resemblance to gold and its useful properties. Over time, advancements in metallurgical techniques have facilitated the growth of brass products into modern times.
The End
As we peel back the layers of brass alloys, we find a rich tapestry of history, innovation, and application. Their relevance is not merely historical; it inspires ongoing research and application as the world looks for more effective materials to meet its needs. By comprehensively exploring the realm of brass, one begins to appreciate its significance within various fields, from art to engineering.
In the following sections, we will delve deeper into the methodologies that have shaped our understanding, the dynamics of brass production, and the wide-ranging applications that continue to evolve in today's industries.
Intro to Brass Alloys
The study of brass alloys serves as a foundation for understanding a material fundamental to both historical and modern technological advancements. Brass itself is not a single entity; rather, it is a fascinating amalgamation of metals, primarily copper and zinc, with characteristics that can change significantly based on its specific formulation. Delving into brass alloys allows us to appreciate their importance across various industries from plumbing to electronics, and even in the arts through musical instruments.
Definition and Composition
Brass alloys are categorized under the umbrella term of copper-zinc alloys. The basic composition of brass can vary widely, but typically consists of about 55% to 95% copper and the remainder primarily being zinc. This variation in composition leads to different types of brass with distinct properties which can be tailored for specific applications.
In addition to copper and zinc, various alloying elements can be added to enhance certain characteristics. For instance:
- Lead may be added to improve machinability.
- Tin enhances corrosion resistance.
- Aluminum imparts strength and improves tarnish resistance.
- Nickel can increase toughness and resistance to corrosion, as well.
Each of these elements modifies the final properties of the brass, making it suitable for a vast range of applications.
The History of Brass Alloys
The journey of brass alloys dates back to ancient civilizations. Evidence suggests that brass was produced as early as 500 B.C. in what is today known as the region of the Middle East. The alloy was widely used in coins and decorative items. The invention of new smelting techniques allowed artisans to explore various combinations of metals to create alloys that had specific functional benefits.
As we move through history, the role of brass alloys continued to evolve. The Industrial Revolution spurred advancements in metallurgy and metalworking, leading to the mass production of brass components. By the late 19th century, brass found widespread use in musical instruments, plumbing fixtures, and electrical connectors, even sparking innovations in marine and aerospace engineering.
"Brass is not merely a metal; it is a material of evolution, echoing the progress of human ingenuity through time."
The historical significance of brass alloys illustrates not just their utility but underscores an ongoing relationship between material science and technological innovation, making an exploration of their properties, production methods, and applications essential for modern engineers, historians, and artisans alike.
Understanding the intricacies of brass, the journey it has taken through history, and its evolving role in society sets the stage for a deeper investigation into the scientific principles that govern its properties.
The Science Behind Brass Alloys
Understanding the science behind brass alloys invites an exploration into their very structure and behavior. The materials involved play distinct roles in shaping not only the properties of brass, but also its applications in various industries. Brass is appreciated for its corrosion resistance, strength, and aesthetic qualities.
Copper: The Backbone of Brass
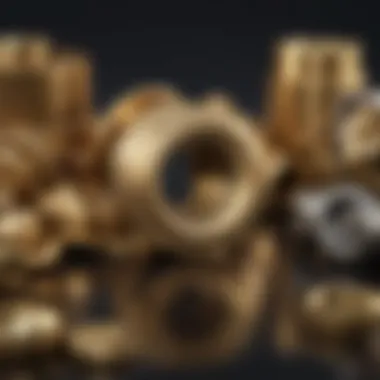
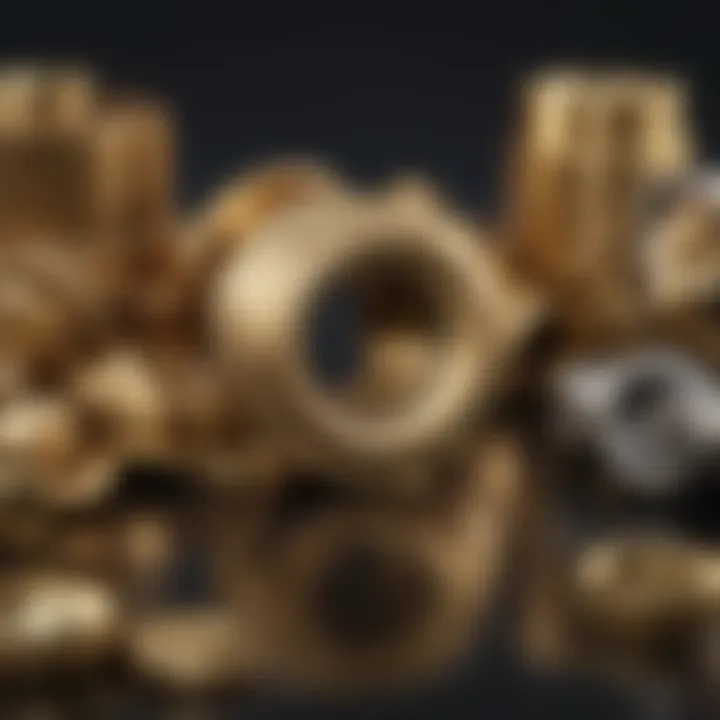
Copper is undeniably the heart of brass. This element contributes significantly to the durability, malleability, and workability of the alloy. Its natural conductivity enhances brass's ability to transfer heat and electricity, making it indispensable in many electrical applications. Moreover, copper lends brilliant luster to brass, which explains why you'll find this alloy in decorative pieces—from jewelry to music instruments.
Just as an oak tree is known to provide sturdy support for various branches, copper holds brass together. Many look for copper-rich alloys, typically above 60%, due to their superior characteristics. This reliance on copper makes the choice of sourcing and quality paramount.
Zinc: Its Role and Impact
Zinc enters the equation as the co-star of brass alloys, providing a fine balance. While copper is the muscle, zinc brings resilience. Mixing zinc into copper creates a lower melting point, which benefits fabrication processes. Zinc also reduces the brittleness of brass; without it, the material might not be suitable for applications requiring flexibility.
On the flip side, high concentrations of zinc can cause some drawbacks, such as susceptibility to corrosion in specific environments. It's like cooking; too much salt can spoil the dish. The key lies in achieving the right ratio, typically around 30% to maintain the perfect balance of strength and ductility while keeping costs manageable.
Additional Alloying Elements
Brass alloys are more than just copper and zinc; additional elements play a vital role in enhancing properties. Let's dive into four alloying elements that significantly influence the overall characteristics of brass.
Lead
Adding lead facilitates machining, allowing for a smoother production process. It's like adding a little grease to a squeaky wheel—everything turns smoothly. This addition is common in free-cutting brass applications found in precision machining. However, the challenge lies in lead leaching, posing environmental concerns. Thus, while it improves machinability, careful consideration is needed in its application to avoid public health risks.
Tin
Tin serves primarily to enhance corrosion resistance. This element improves the overall protective barrier of brass—think of it as putting on a raincoat on a drizzly day. Its contribution is particularly notable in marine environments where moisture and salty air can wreak havoc on materials. However, the costs associated with tin can make it a less common choice when budgeting is a priority.
Aluminum
Incorporating aluminum makes for a lightweight yet strong alloy. Aluminum's oxidation resistance bolsters brass's durability, especially in outdoor applications. It’s like having an extra layer of armor on your favorite coat. Yet, aluminum-rich brass is slightly harder to weld, so the application must consider this trade-off for optimal performance.
Nickel
Nickel enhances both the appearance and overall strength of brass, improving its resistance to corrosion. This alloying element can yield a shiny finish, making it attractive for decorative purposes. While nickel's contribution is significant, it often comes with a price, raising production costs. So, when choosing nickel, it's a balancing act between aesthetic appeal and cost constraints.
By understanding the science behind the alloying elements, one can appreciate the diverse range of properties each brings to the material, influencing selection choices across industries.
The interplay of these elements defines brass alloys as versatile materials, charged with potential. Ultimately, the synergy of copper, zinc, and other alloying elements enables brass to shine in its myriad applications, from faucets to musical winds.
Properties of Brass Alloys
Understanding the properties of brass alloys is crucial, especially given their wide-ranging applications in various fields. These properties highlight not only the functionality but also the aesthetic appeal that brass brings to the table. The blend of copper and zinc, along with other elements, results in a material that possesses distinct advantages tailored to specific uses. When considering brass alloys, one must pay close attention to mechanical properties, resistance to corrosion, and the ability to conduct heat and electricity.
Mechanical Properties
When it comes to mechanical properties, brass alloys are prized for their duability and malleability. The tensile strength of brass makes it suitable for a variety of engineering applications where resilience is key. Most brass alloys exhibit good strength, which means they can endure pressure and stress without failing. This property is particularly relevant in structural components and fasteners, where precision and reliability are essential.
Brass also scores high on the ease of fabrication. It can be easily drawn into wires, rolled into sheets, or cast into intricate shapes. This versatility is often a deciding factor for manufacturers when selecting materials for production processes. Additionally, the low friction of brass gives it an edge in applications that require moving parts, such as gears and bearings. Thus, mechanical attributes play a vital role in the decision-making process for engineers and designers alike.
Corrosion Resistance
Another significant aspect of brass alloys is their corrosion resistance. Brass does not rust like iron or steel, thanks to the protective oxide layer that forms on its surface when exposed to air. This natural defense mechanism extends the life of brass components, especially in environments where moisture is a concern.
Brass alloys find use in plumbing and marine environments precisely because of this durability.
However, not all brass alloys are created equal when it comes to resisting corrosion. Elements like zinc can be beneficial, but excessive zinc can lead to dezincification, where zinc is leached away, compromising the structural integrity of the alloy. Therefore, selecting the appropriate brass alloy for specific environments is crucial in achieving optimal performance.
"The longevity of brass alloys in marine environments highlights the blend of aesthetics and functionality that they offer, making them a favorite choice among designers."
Thermal and Electrical Conductivity
Lastly, we must consider the thermal and electrical conductivity of brass alloys. Brass is known for its excellent conductivity, which makes it a preferred material in applications such as electrical connectors and heat exchangers. Copper's presence in brass contributes significantly to its ability to transfer heat and electricity efficiently.
In terms of thermal conductivity, brass allows for quick heating and cooling, making it ideal for heat-sensitive applications. The ability to conduct electricity is relevant in electrical wiring where safety and efficiency are paramount. Depending on the specific alloy composition, the levels of conductivity can vary, so careful selection is needed depending on the application requirements.
For more insights on brass and its properties, feel free to explore resources like Wikipedia and Britannica.
Production Methods of Brass Alloys
Understanding the production methods of brass alloys is not just about metalworking; it reflects the intersection of art and science. The methods used to create these alloys affect their overall characteristics, which in turn determine their applications in various industries. The choice of production technique can influence mechanical properties, durability, and even aesthetic qualities. This section digs into the traditional and modern techniques, shedding light on how each method contributes to the formation and functionality of brass alloys in today's landscape.
Traditional Casting Techniques
Traditional casting has roots that run deep into the history of metallurgy. This method involves pouring molten metal into a mold, allowing it to solidify. While it may sound straightforward, the details can be intricate. Traditional casting techniques enable the creation of intricate shapes and forms that are otherwise hard to achieve. The molds can be made from various materials, including sand, clay, and metal, each offering different traits and usability.
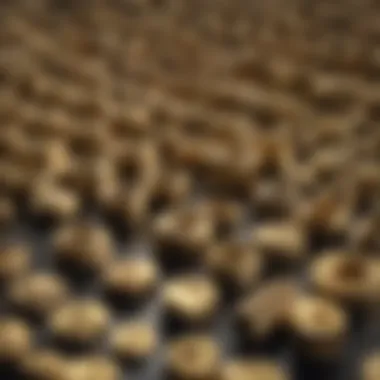

In terms of benefits, traditional casting methods often allow for large-scale production and can be economically feasible, especially for simpler designs. However, they also come with a set of limitations, such as a longer turnaround time and the potential for defects like air pockets. A savvy craftsman must carefully consider these aspects to avoid compromising quality.
Modern Fabrication Processes
Modern fabrication methods bring a blend of precision, efficiency, and versatility to the production of brass alloys. Three prominent techniques stand out: extrusion, forging, and cold working. Each of these methods carries its own unique features and benefits.
Extrusion
Extrusion is a process where heated brass is pushed through a die to create specific shapes, like rods or tubes. This method adds a high degree of control over dimensions, which is crucial for many applications. The key characteristic of extrusion is its ability to produce uniform cross-sections, making it a popular choice in industries that demand precision, such as plumbing and electrical wiring.
One unique feature of extrusion is its adaptability to various alloys, allowing for changes in material properties through slight adjustments in the composition or temperature. This can enhance the workflow by reducing waste, as it often uses the material more efficiently. Yet, the drawback lies in the initial tooling costs, which can be high, especially for customized dies. Still, the long-term benefits often outweigh these upfront expenses.
Forging
Forging involves shaping brass alloys using compressive forces. This method can be performed hot or cold, each offering distinct advantages. Hot forging improves ductility, which is vital for attaining specific shapes without cracking. The remarkable strength that forged materials possess cannot be understated; this characteristic makes it an excellent choice for high-stress applications like automotive parts or aerospace components.
A unique aspect of forging is its ability to enhance the grain structure of the metal, which leads to improved strength and toughness. However, the process can be labor-intensive and requires significant energy input, making it less suited for smaller production runs. Still, the mechanical properties gained from forging usually justify the investments in many cases.
Cold Working
Cold working refers to shaping the brass alloys at or near room temperature. This technique is often employed for refining dimensions and improving surface quality. One of its standout features is that cold working can significantly increase strength through strain hardening. This process is beneficial when producing detailed components like fittings and valves.
However, cold working does bring its own challenges. Materials can become too hard after extensive manipulation, making further shaping difficult. Additionally, there is a risk of introducing residual stresses in the material, which can lead to deformation later on. But for industries that require precise shapes and tolerances, cold working remains a vital tool in the production toolkit.
Applications of Brass Alloys
The utility of brass alloys spans a remarkable range of applications across different sectors. Employed in a variety of products, these alloys showcase properties that offer significant advantages including durability, malleability, and aesthetic appeal. The applications of brass alloys not only highlight their versatility but also provide insights into their tangible relevance in daily life and industrial practices.
Industrial Uses
Brass alloys are a cornerstone in the industrial sector. Their mechanical properties make them suitable for many applications. For instance, they are widely used in manufacturing gears, valves, and pumps. These components benefit from brass's resistance to corrosion and wear, which extends their lifespan and reduces maintenance costs.
Brass's ability to be machined easily also makes it a preferred choice for producers. Industries such as automotive and aerospace rely on brass for machine components, ensuring reliability under stress. A noteworthy mention is the production of electrical connectors, where brass’s excellent conductivity is critical.
- Applications in Industrial Sectors:
- Automotive parts: Used in wheels, fasteners, and radiators.
- Aerospace fittings: Essential for safety and performance in flight.
- Electrical components: Perfect for connectors and terminals due to conductivity.
Instrumentation and Plumbing
This alloy truly shines in plumbing and instrumentation. The combination of corrosion resistance and strength makes brass alloys ideal for faucets, fittings, and pipes. These installations are subject to constant stress from temperature fluctuations and water pressure. Brass is able to withstand such conditions, which minimizes leaks and maintenance needs.
Moreover, in instrumentation, brass is prevalent due to its tactile feel and appearance. For pressure gauges, fittings, and valves used in scientific applications, precision is key, and brass provides the necessary mechanical stability and reliability.
Some advantages in this area include:
- Durability: Withstands high-pressure systems without risk of failure.
- Precision engineering: Ideal for gauges and measurement tools.
- Aesthetic appeal: Often chosen for its visual characteristics in visible plumbing applications.
Musical Instruments
Interestingly, brass alloys are not just for the practical; they also have a substantial role in the world of music. Instruments such as trumpets, trombones, and saxophones are frequently made from brass, taking advantage of the metal’s acoustic properties. The alloy's ability to produce a rich, resonant sound is profoundly valued in music education and performance.
Several factors contribute to brass’s role in musical instruments:
- Sound Quality: Brass has unique resonant qualities that enrich the sound.
- Workability: Allows for intricate designs and finishes for aesthetic and functional purposes.
- Versatility: Different mixtures provide varied tonal qualities, making it adaptable across genres.
"The sound produced by brass instruments is often described as bright and vibrant, captivating audiences around the globe."
Advantages of Brass Alloys
Brass alloys stand out in various applications due to a multitude of advantages, making them a popular choice across diverse industries. Understanding the specific benefits and considerations of these alloys can help one appreciate their value. Let's dive into two key aspects that exemplify why brass alloys remain significant in today's material landscape: their cost-effectiveness and their aesthetic qualities.
Cost-Effectiveness
When it comes to cost considerations, brass alloys often present a compelling case. They are generally less expensive to produce than many other metals while still providing superior performance traits. This affordability comes from several factors:
- Raw Material Availability: Copper and zinc, the primary components of brass, are readily available metals. Their abundant supply helps keep production costs lower.
- Ease of Fabrication: Brass alloys are easier to machine and shape than some more complex metals. This means reduced labor costs during the manufacturing process, passing savings on to consumers and businesses.
- Longevity: Due to their corrosion resistance, brass alloys often have a longer lifespan, which translates to less frequent replacement or maintenance costs over time.
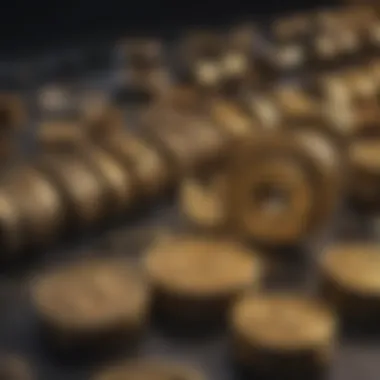
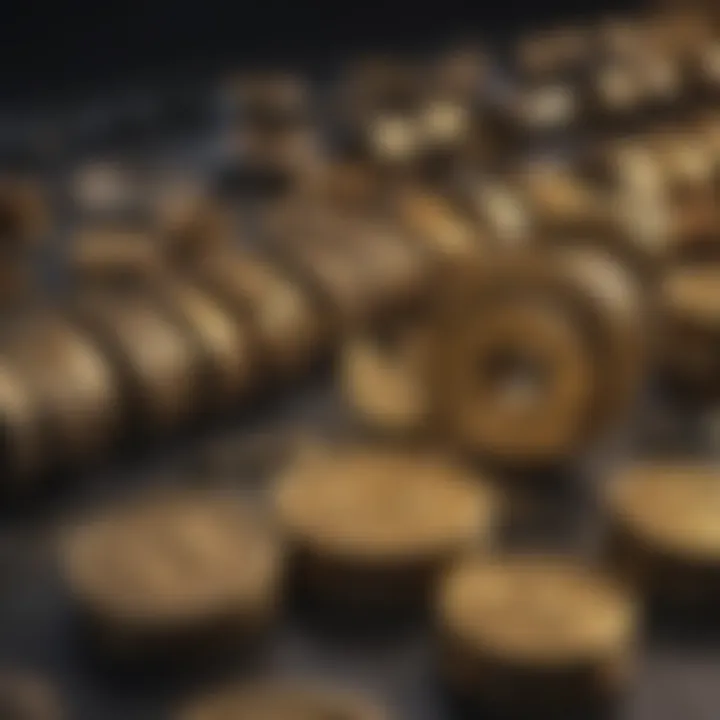
In many applications, like plumbing and electrical fittings, this cost-effectiveness combines with performance reliability, making brass a go-to option for engineers and designers.
Aesthetic Qualities
Aside from financial advantages, the aesthetic appeal of brass alloys cannot be overlooked. Brass has a warm, golden hue that's visually pleasing and lends it an air of sophistication. Its aesthetic qualities make it a desirable choice in various designs and finishes:
- Versatility in Design: Brass can be polished to a glossy finish, brushed for a more subdued look, or even antiqued for a rustic appearance, making it suitable for a wide range of applications, from decorative hardware to musical instruments.
- Warm Tones: The color of brass complements many design schemes, standing out without being overwhelming. This makes it ideal for applications where visual appeal is paramount, such as in musical instruments like trumpets and saxophones or in interior decoration.
- Age and Character: Unlike some materials, brass develops a patina over time which can enhance its appearance, adding character in a way that synthetic finishes cannot replicate.
"The visual warmth of brass, when combined with its practical benefits, makes it a favorite of both artisans and engineers alike."
In summary, the advantages of brass alloys—ranging from cost-effectiveness to aesthetic beauty—offer a balanced package that serves multiple needs in today’s industrial and artistic domains. This versatility is essential for various stakeholders involved, from manufacturers to end-users, helping them navigate the myriad choices in materials available today.
Challenges and Limitations
The discussion around the challenges and limitations of brass alloys is an essential aspect to consider in the broader conversation about their usage and sustainability. While the unique properties of brass alloys make them a preferred choice for many applications, it is vital to address the challenges that manufacturers, users, and the environment face. Gaining insight into these areas allows for better decision-making and innovation in the alloying process, leading to improvements in quality and sustainability.
Alloy Degradation
Alloy degradation is one issue that looms over the brass industry. Over time, brass can suffer from various types of degradation, particularly stress corrosion cracking and dezincification. Stress corrosion cracking (SCC) occurs when brass is exposed to both tensile stress and a corrosive environment, leading to the sudden failure of components, often without warning. This risk makes it central for engineers and designers to account for the environments in which brass will be employed. Tightening quality control measures, using protective coatings, and monitoring stress levels can help mitigate these risks.
Another significant form of degradation is dezincification, a process where the zinc is selectively leached out of the alloy, resulting in a porous copper-rich layer. This deterioration not only affects the appearance of brass but also its mechanical integrity. To combat dezincification, modifications in the alloy composition can be a viable solution. Resistance can be enhanced by incorporating more alloying elements like aluminum or tin, which create a stronger, more resilient structure. These decisions, however, must be balanced with cost and availability of materials.
Environmental Concerns
When delving into the realm of brass alloys, one cannot overlook the environmental concerns associated with their production and disposal. The mining of copper and zinc has various ecological impacts, including habitat destruction, water pollution, and significant energy consumption in the extraction and refining process.
Better practices within the industry have emerged, aiming for a greener approach. One such example is the increasing adoption of recycling methods. Using recycled metals can drastically reduce the environmental footprint associated with virgin material extraction. Recent advancements in smelting and refining techniques can enhance the efficiency of utilizing scrap brass, thus promoting sustainability.
On a larger scale, as regulatory measures become more stringent, industries are compelled to adopt sustainable practices. Moving forward, there's an increasing need for developing novel, eco-friendly production methods that not only address resource management but also the long-term effects on the environment.
"Sustainability isn't just a buzzword; it's a necessity for the survival of every industry today."
In summary, while brass alloys have stood the test of time thanks to their diverse applications and remarkable properties, there remains a critical need to address the challenges they present, especially concerning alloy degradation and environmental impact. A proactive approach in addressing these challenges not only ensures the longevity of the materials but also signifies a commitment to environmental health and innovation.
Future Trends in Brass Alloy Development
The exploration of brass alloys is far from static; it’s a continually evolving field influenced by new technologies and changing industry demands. Understanding the future trends in brass alloy development is crucial for various stakeholders, from manufacturers to researchers and environmentalists. This section dives deeper into two critical areas: innovative alloy design and sustainability in production.
Innovative Alloy Design
As technology progresses, so does the methodology in alloy creation. New design paradigms are emerging, steering brass alloy development towards specific mechanical and chemical properties that meet modern needs. This doesn’t merely imply adding new elements; it incorporates computational metallurgy and simulations to predict how different combinations will behave under stress or during corrosion.
For instance, imagine developing a brass alloy that maintains optimal strength while minimizing weight. This can** significantly** benefit industries like aerospace, where every gram counts. Adjacent fields are already employing advanced materials design and alloy optimization to cater to niche applications. The possibilities seem endless.
Moreover, these innovative designs often involve creating alloys tailored for specific environments, such as seawater applications, where corrosion resistance is non-negotiable. Such targeted approaches could revolutionize industries that require specialized materials, leading to a new wave of brass products with unparalleled durability. However, it’s vital to understand the implications of chemically modifying traditionally established formulas. Rigorous testing must be part of every new design to ensure safety and functionality.
Sustainability in Production
In an era increasingly focused on minimizing environmental impact, the sustainability of brass production processes has become a hot topic. Several trends are beginning to shape the way brass is manufactured, reflecting a broader commitment to eco-friendliness.
One promising development is the integration of recycled materials into the brass alloy mix. With copper and zinc being expensive to extract and process, utilizing scrap metal could not only minimize costs but also significantly reduce the carbon footprint associated with mining. The drive for recycling has prompted initiatives that not only meet consumer demand for eco-friendly products but also align with stringent regulations aimed at curbing industrial emissions.
Another focus is on employing cleaner manufacturing processes. The shift towards utilizing renewable energy sources in production plants is gaining traction. This is a game changer. Not only does it lower emissions, but it can also reduce production costs in the long run. Some manufacturers are even looking into additive manufacturing for creating brass parts, which minimizes waste compared to traditional methods.
"The future of brass alloys lies in the intersection of innovation and sustainability. Innovation drives us forward, while sustainability ensures that we leave the planet intact for future generations."
In summary, as we turn our eyes toward the future, it’s clear that the brass industry must adapt to meet evolving demands—both in terms of advanced properties and environmental stewardship. Whether through innovative designs or sustainable practices, the next wave of brass alloys promises not only to advance engineering but also to align closely with a more sustainable world.
Concluding Remarks
Brass alloys hold a significant place in both historical and contemporary contexts, serving diverse functions across various industries. Their unique blend of properties originated from the amalgamation of copper and zinc, complemented by other alloying elements. This descriptive exploration emphasizes not only the scientific underpinnings but also the practical applications that underscore their importance.
The Enduring Relevance of Brass Alloys
In today's world, the utility of brass alloys shines through in multiple domains. From engineering to art, brass continues to prove its mettle. Here are specific elements that underscore the enduring relevance:
- Versatility: Brass alloys can be tailored for specific applications by adjusting their composition, offering wide-ranging versatility in use.
- Economic Viability: Despite fluctuations in raw material prices, brass remains a cost-effective solution compared to newer materials due to its durability and longevity.
- Aesthetic Qualities: The beauty of brass surfaces makes them popular in jewelry, instruments, and decorative architecture.
"Brass has had an enduring presence in the materials world, continually being refined and reimagined to meet the needs of an ever-evolving industry."
Additionally, brass alloys are finding traction in modern applications as industries seek sustainable solutions. The move toward eco-friendly practices in production techniques has elevated interest in brass, especially considering its recyclability.
Brass alloys will likely remain a staple for the foreseeable future, adapting to the challenges posed by both technological advancements and environmental concerns. Indeed, the importance of brass alloys is not merely historical; it resonates in today’s innovations, wrapped in a rich narrative of resilience and adaptability.