Electropolishing 304 Stainless Steel: Detailed Insights
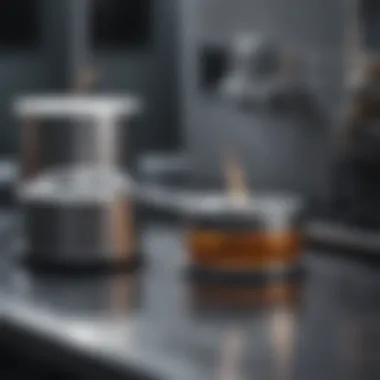
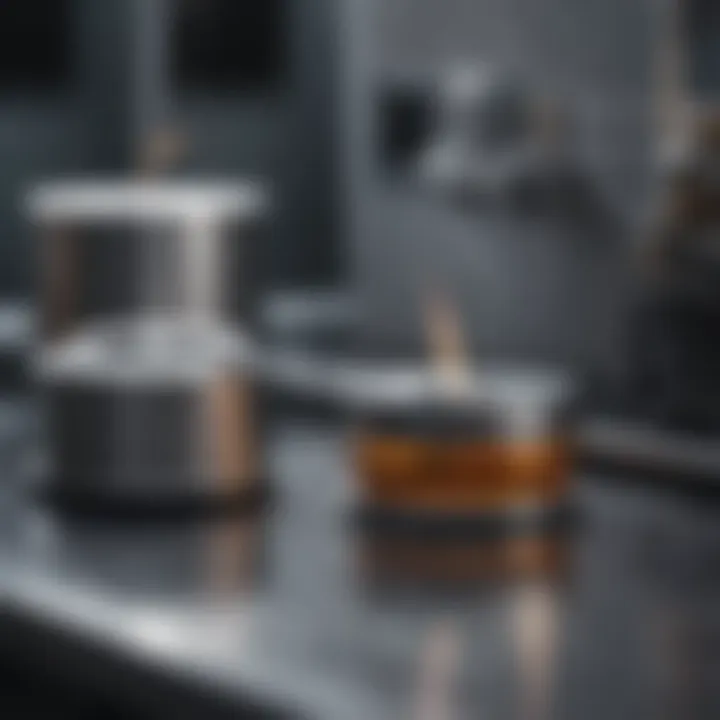
Intro
Electropolishing is a process that is often overlooked in discussions about metal finishing, yet its impact is significant, especially when talking about 304 stainless steel. It’s not just a fancy term thrown around in workshops; rather, it encapsulates key chemical and physical processes that enhance surface quality and performance. The process is integral across numerous industries, ranging from biomedical to food processing, owing to its ability to improve corrosion resistance and hygiene.
This comprehensive analysis seeks to peel back the layers of electropolishing, shining a spotlight on the chemistry involved, its myriad benefits, and real-world applications. A better grasp of this process holds value for students eager to deepen their understanding, researchers looking for fresh angles, and professionals who rely on high-quality metal finishes in their work.
As we delve deeper, it’s essential to consider how this technique not only transforms the material properties of stainless steel but also embraces challenges and safety protocols crucial to its application. Furthermore, staying abreast of the technological innovations shaping the future of electropolishing can give insights into its evolving role in industry.
The journey through electropolishing 304 stainless steel begins here, aiming to foster an appreciation for this intricate yet fascinating process.
Recent Advances
Latest Discoveries
In recent years, researchers have unearthed some intriguing insights about electropolishing. From optimizing the electrolyte compositions to understanding how varying voltage impacts the finish, the advancements are notable. One significant discovery is the role of temperature in achieving a desirable surface finish. Studies suggest that maintaining a specific thermal range during the electropolishing process can dramatically improve the end results. By controlling the environment, operators can tailor the outcome to specific requirements more effectively.
Additionally, the exploration into environmentally-friendly electrolyte solutions has gained traction, focusing on minimizing the carbon footprint of the process. This is crucial not only from a regulatory standpoint but also in meeting the expectations of increasingly eco-conscious industries.
Technological Innovations
The field of electropolishing is not static, and the infusion of advanced technologies is reshaping how the process is carried out. Automated systems that integrate Artificial Intelligence for process monitoring and control are becoming more prevalent. These innovations enable real-time adjustments based on quality data, which optimizes the electropolishing parameters practically on the fly.
Moreover, advancements in digital imaging techniques allow for impressive clarity when assessing the surface quality before and after processing. Utilizing such tech means deficiencies can be detected and rectified before the final product rolls out.
"Understanding the nuances of electropolishing is not just about achieving shine; it’s about enhancing performance and extending the lifespan of components."
Methodology
Research Design
The analysis of electropolishing methodologies is multifaceted. It involves both qualitative and quantitative research techniques, tracing past studies and juxtaposing them against contemporary practices. The crux of this research design is to gather comprehensive data that elucidates how electropolishing affects 304 stainless steel specifically.
Data Collection Techniques
Data collection can take several forms. Observational studies, where real-time processes are monitored, provide insight into operational efficiency and outcome quality. Interviews with industry professionals further enrich our knowledge, offering firsthand accounts of the processes employed and the challenges faced. Laboratory tests that gauge corrosion resistance before and after electropolishing present empirical evidence of its efficacy.
Techniques may also include surveys designed for those involved in sectors where electropolishing is commonplace. Through these avenues, a well-rounded perspective is attained, illuminating the relevance and viability of electropolishing in various applications.
In summary, electropolishing 304 stainless steel holds great significance in an amalgam of industries. By considering recent advancements and a structured methodology for research, we can unveil the true potential of this essential process.
Understanding Electropolishing
The electropolishing process of 304 stainless steel is a vital aspect, not only for improving the material's properties but also for expanding its applications in various industries. To grasp the significance of this topic, it's essential to look closely at what electropolishing is and how it impacts stainless steel. While some may view it as just another surface treatment method, the intricacies and benefits that come along with it suggest that it holds much more importance than meets the eye.
One of the primary advantages of electropolishing is its ability to enhance surface finish. When it comes to stainless steel, appearances matter. A high-quality finish not only looks better but also reduces the likelihood of bacterial growth, making it indispensable in sectors like pharmaceuticals and food processing. Moreover, it can lead to increased corrosion resistance, a critical factor for materials subjected to harsh environments. Improved corrosion resistance contributes to the longevity of the product and reduces maintenance costs, which is a win-win for manufacturers and consumers alike.
Electropolishing is not merely about aesthetics or surface cleanliness, either. It also relates to mechanical properties such as friction and wear resistance. Materials that have undergone electropolishing tend to exhibit lower friction, which translates into better operational efficiency in various mechanical systems. This reflects the multifaceted benefits of understanding electropolishing, especially when considering the broader context of applications.
To truly appreciate the relevance of this process, it is essential to delve deeper into its definition, historical context, and the methods involved, which lays the groundwork for a more profound understanding of its role in the treatment of 304 stainless steel.
Definition and Overview
Electropolishing essentially functions as an electrochemical process that removes material from a metal workpiece, resulting in a smooth and shiny surface. To put it simply, think of it as "reverse plating." During the process, stainless steel is submerged in a conductive electrolyte solution. The surface areas of the material lose microscopic layers through anodic dissolution, which eliminates imperfections and irregularities present on the surface.
The ramifications of this process extend beyond just the visual impact. The removal of surface contaminants not only enhances the appearance but also helps in achieving a level of cleanliness that is critical in sensitive applications. Electropolishing can lead to a finish that goes beyond what mechanical polishing can achieve, often providing a surface that is not only smoother but also more resistant to corrosion.
In the grand scheme of manufacturing and processing, electropolishing stands out as a method to improve surface integrity while also making materials easier to clean and maintain.
Historical Background
The roots of electropolishing can be traced back to the early 20th century when scientists and engineers were probing the interaction between electrical currents and chemicals. Recognizing the potential to refine metal surfaces seemed like an ideal solution to the persistent challenges posed by rough surfaces and chemical corrosion. The process saw early adoption in sectors that required high cleanliness standards.
While the principles of electropolishing were documented, it gradually evolved with innovations in technology and materials science. As the industrial demand for enhanced corrosion-resistant materials burgeoned, so did the popularity and refinement of electropolishing techniques.
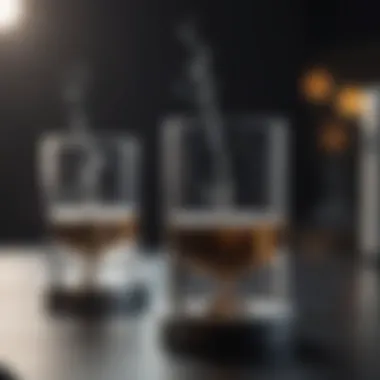
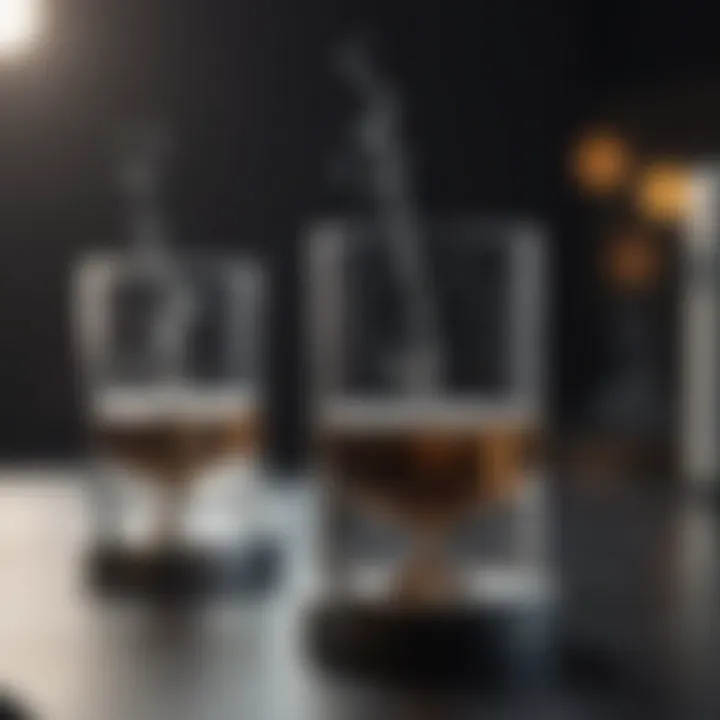
Over the decades, distinctive improvements were made in the types of electrolyte solutions used and the electric current applications, allowing more control over the polishing process. These changes significantly enhanced the effectiveness and efficiency of electropolishing, making it a cornerstone in the processing of stainless steel and various other metals. As the industry adapted to new challenges and requirements, the role of electropolishing only became more pronounced, demonstrating its significance in both historical and contemporary contexts.
Properties of Stainless Steel
Understanding the properties of 304 stainless steel is crucial when discussing electropolishing, as these characteristics significantly impact how the material behaves during and after the process. 304 stainless steel, also known as A2 stainless steel, is one of the most commonly utilized alloys within the industry due to its robust mechanical properties and excellent corrosion resistance. This section sheds light on its composition, mechanical performance, and ability to withstand corrosive environments, all of which underscore its relevance in applications where electropolishing provides added benefits.
Composition and Structure
304 stainless steel is primarily composed of iron, with significant amounts of chromium (18%) and nickel (8%). This particular blend grants it both durability and resilience, making it ideal for a variety of applications, from kitchen appliances to chemical equipment. The chromium content not only contributes to the alloy's strength but also forms a protective layer of chromium oxide, which is crucial for its corrosion resistance.
On a microscopic level, the structure of 304 stainless steel is largely austenitic. This means that it maintains a face-centered cubic (FCC) crystal structure, which provides higher ductility and workability compared to ferritic or martensitic stainless steels. Such structural properties are what allow 304 stainless steel to be easily formed and welded, making it a favorite in many manufacturing environments.
Mechanical Properties
The mechanical properties of 304 stainless steel are marked by an impressive balance between strength and ductility. Yield strength generally sits around 215 MPa, while tensile strength can reach approximately 505 MPa. This combination allows it to endure considerable stress without permanent deformation.
Ductility is also an important feature; the material can be stretched or shaped without fracturing, making it suitable for applications where complex shapes are needed. This property benefits from the electropolishing process. Electropolishing does not compromise strength; rather, it enhances the surface finish, which may contribute to a more uniform stress distribution across the material.
"The properties of 304 stainless steel make it compatible with a vast range of industrial applications, and electropolishing can elevate those properties substantially."
Corrosion Resistance
304 stainless steel is renowned for its corrosion-resistant capabilities, a quality that stems from its chemical composition. The chromium in the alloy forms a passive oxide layer that combats corrosion, particularly against oxidizing acids and various atmospheric conditions. Additionally, the nickel content further enhances this resistance by providing stability to the austenitic structure, making it less susceptible to corrosion than other stainless steel types.
However, it's essential to recognize that while 304 stainless steel offers substantial resistance to corrosion, it is not entirely invulnerable. Under certain conditions, such as exposure to chlorides found in saltwater or harsh cleaning agents, even 304 can suffer from pitting or crevice corrosion. This is where electropolishing shines—by smoothing out surface imperfections and removing any surface contaminants, it maximizes the protective layer's effectiveness, further enhancing the material's durability in hostile environments.
In summary, the properties of 304 stainless steel play a foundational role in its performance and suitability for various applications. The right understanding of its composition, mechanical properties, and corrosion resistance not only emphasizes the necessity of proper treatment processes like electropolishing but also underscores its significance across myriad industries.
The Electropolishing Process
The electropolishing process is a transformative technique that can significantly enhance the characteristics of 304 stainless steel. This process is not just about aesthetics; it substantially improves the material’s functionality through various chemical and physical principles. Understanding how electropolishing operates is crucial, as it allows us to appreciate its applications and benefits in various industries.
Chemical Principles
Electropolishing is fundamentally an electrochemical process, which implies that it involves both chemical and electrical reactions. When 304 stainless steel is immersed in a specially designed electrolyte solution, a direct current is applied. The outcome is a selective dissolution of surface material. Essentially, protrusions on the surface lose material faster than the recessed areas, effectively smoothing the surface on a microscopic level.
This can be likened to a group of kids on a seesaw; the one who is raised higher is at risk of being lowered quicker, while the one below is kept from descending as rapidly. In electropolishing, the peaks of the surface are reduced, whereas the valleys are protected, leading to a polished finish. This characteristic makes electropolishing a beneficial method for improving not just appearance but also the overall performance of the stainless steel.
Electrolyte Solutions
Choosing the right electrolyte solution is key in the electropolishing process as it directly influences the rate of material removal and the quality of the final finish. Commonly used solutions are mixtures of phosphoric acid, sulfuric acid, or other proprietary formulas designed for 304 stainless steel. Each solution has its unique characteristics.
For instance, a phosphoric acid-based solution often provides a smoother finish than one using sulfuric acid. However, it is also essential to consider factors like temperature and concentration, as they can affect the reaction rates. Ultimately, finding the right balance may require some trial and error, but it's well worth the effort in achieving a pristine surface.
"The choice of electrolyte can mean the difference between a mediocre and an exceptional finish in electropolishing."
Process Parameters
The variables involved in the electropolishing process—voltage, time, and temperature—must be carefully controlled to ensure optimal results.
Voltage
Voltage plays a critical role in electropolishing. It determines how much current flows through the system and influences the rate at which material is removed from the stainless steel surface. Typically, a higher voltage results in faster processing times, but it can also lead to poor surface quality or even damage to the material if not managed properly.
Voltage needs to be high enough to encourage effective electropolishing but careful dosing is important to achieve a balance. Most processes operate effectively in the range of 6-12 volts. This range is often seen as a sweet spot—sufficient to get the job done without causing undue harm. Remember, fluctuating voltage can yield inconsistent results, either leading to burnt surfaces or inadequate polishing.
Time
Time is another crucial factor in the electropolishing process. How long the stainless steel is subjected to the electrolyte can dramatically influence the outcome. Short exposure may not remove enough surface material, while long exposure may erode the base material or alter its properties.
Careful planning often entails running preliminary tests to establish the ideal time needed based on the desired surface finish. Typically, the process can last from a few minutes to several hours. The flexibility in timing offers a tailored approach to achieve the desired smoothness and reflectivity without compromising the material’s structure.
Temperature
Temperature also plays a significant role in the efficiency of the electropolishing process. Higher temperatures usually accelerate chemical reactions and can enhance overall throughput. However, too high a temperature may lead to undesirable effects, including unintentional metal loss or discoloration.
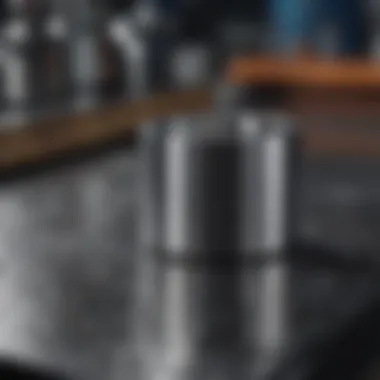
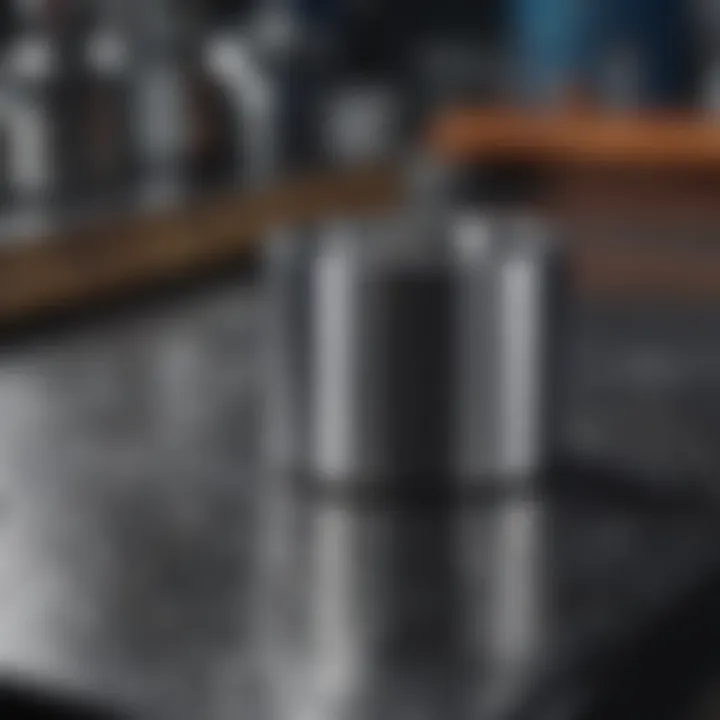
Generally, maintaining a steady temperature is advised, around 50-70 degrees Celsius, depending on the electrolyte used. This controlled environment ensures that the chemical reaction occurs at a pace that is both effective and safe for 304 stainless steel, allowing for the achievement of the best possible finish.
Overall, the control of these process parameters is essential to achieving a polished surface that not only meets aesthetic expectations but also offers enhanced performance. Understanding the interplay among voltage, time, and temperature can greatly improve the electropolishing outcomes of 304 stainless steel.
Advantages of Electropolishing Stainless Steel
When it comes to enhancing the utility of 304 stainless steel, electropolishing serves not just as an option, but as a game changer. This section lays out the myriad advantages that come with this very specific surface treatment process. From improving surface aesthetics to bolstering corrosion resistance, electropolishing aligns itself with the demands of a variety of industries. Let’s break down some of the critical benefits that make electropolishing an appealing choice for industrial applications.
Surface Finish and Aesthetics
One of the primary draws of electropolishing is the striking surface finish it imparts on 304 stainless steel. Think about how first impressions matter; the surface finish often defines one’s initial thoughts on a product. After electropolishing, the surface acquires a shiny, reflective quality, making it look sleek and professional. This aesthetic appeal isn't merely for show, though. A high-quality finish also facilitates easy cleaning and maintenance, reducing the chances of contamination in sensitive environments.
Moreover, a smoother surface means fewer crevices for dirt and grime to hide. This is particularly valuable in industries like food processing or pharmaceuticals, where hygiene is paramount. Simply put, a polished surface is not only easier on the eyes but also contributes to efficiency in cleaning and hygiene maintenance.
Improved Cleanliness
Linked closely with surface aesthetics, electropolishing also offers advanced cleanliness benefits. The process removes surface impurities and contaminants that traditional mechanical polishing might miss. By effectively decreasing the surface roughness, electropolished stainless steel minimizes the adhesion of bacteria and other harmful pathogens, a crucial factor in sterile environments.
In fact, electropolished surfaces exhibit significantly less surface area to trap soil and debris. Therefore, those in food manufacturing or healthcare settings can sleep better at night knowing their equipment is up to snuff. And it’s not simply about the immediate aesthetics; this level of cleanliness directly affects the durability and lifespan of the material in long-term usage scenarios.
Enhanced Corrosion Resistance
One of the standout highlights of electropolishing is its notable enhancement of 304 stainless steel's corrosion resistance. While 304 stainless steel is already well-respected for its resistance to rust and pitting, the electropolishing process intensifies this level of protection. Through the removal of microscopic pits and fissures, electropolishing helps to create a more uniform and dense passive chromium oxide layer, which defends against corrosive environments.
Stainless steel exposed to harsh chemicals, humidity, or salty air can experience corrosion if not treated properly. Electropolishing acts like putting armor on your metal, extending its lifespan significantly. In industries such as marine or chemical processing, this extra layer of security from corrosion can mean the difference between longevity and costly replacements.
Diminished Friction
Last, but certainly not the least, electropolishing plays a role in reducing friction on stainless steel surfaces. The smoother the surface, the less resistance it creates when in contact with other materials. This characteristic is especially crucial in applications involving moving parts or machinery, where reduced friction can lead to improved efficiency and reduced wear over time.
Less friction not only enhances performance but also aids in energy conservation. In environments where machinery runs continuously, such as manufacturing plants, every bit of efficiency counts, translating into cost savings and improved productivity.
In summary, the advantages of electropolishing 304 stainless steel range from aesthetically pleasing finishes and improved cleanliness to enhanced corrosion resistance and diminished friction. These benefits are indispensable across various sectors, making electropolishing a crucial step in the treatment of stainless steel components.
Applications in Various Industries
Electropolishing 304 stainless steel serves multiple industries, playing a pivotal role in enhancing not just the material properties but also the overall functional efficacy of products. Each sector has distinct requirements, but the underlying necessity for high hygiene standards, corrosion resistance, and aesthetic appeal is what unites them. Below, we delve into how electropolishing benefits three key industries: pharmaceutical, food processing, and aerospace and defense.
Pharmaceutical
In the pharmaceutical domain, the sanitation of equipment is crucial. Electropolished stainless steel is indispensable in this field due to its remarkable ability to reduce surface defects that harbor microorganisms. The smooth surface created during the electropolishing process minimizes the risk of contamination, which is vital in environments where sterile conditions must be maintained.
One specific benefit is that electropolishing can enhance the cleanability of medical devices, ensuring they comply with stringent regulatory standards. This is not simply a benefit but a necessity for health practices worldwide. Moreover, when machinery and manufacturing devices are constructed from electropolished stainless steel, the likelihood of corrosion is diminished, further ensuring patient safety and the longevity of the equipment.
"In pharmaceutical settings, where every detail counts, the use of electropolished materials isn’t just beneficial—it is non-negotiable."
Food Processing
The food processing industry requires materials that both meet hygienic standards and resist corrosion due to contact with various food substances. Electropolishing stainless steel enhances not just the aesthetics of equipment but makes it more functional. When food-processing tools and machinery are electropolished, their surfaces become less intrusive to cleaning processes, promoting better hygiene and less risk of cross-contamination.
In addition, the durability provided by the electropolished finish helps equipment withstand harsh cleaning processes, including steam and chemical washes. This robustness extends the lifespan of the equipment while maintaining a high standard of cleanliness. Furthermore, the attractive finish of electropolished stainless steel often boosts the visual appeal of food facilities, thereby enhancing brand image for consumer-facing operations.
Aerospace and Defense
In the aerospace and defense sectors, 304 stainless steel components must endure extreme conditions. Electropolishing not only protects these components from atmospheric corrosion but also helps to reduce friction on moving parts, thus enhancing their performance. The importance of precision in these industries cannot be understated; even minor imperfections can lead to significant safety issues.
Electropolished stainless steel components contribute to weight reduction in aircraft and defense vehicles, offering a way to lighten the load without compromising integrity. It also helps in maintaining aerodynamic efficiency—an essential factor in aerospace design. This showcases not just the resilience required in such applications but also the versatility of electropolished surfaces in demanding settings.
To sum up, electropolishing 304 stainless steel reaps advantages across diverse industries, contributing to both performance and safety. The need for materials that are robust and hygienic will only increase, making the techniques discussed here fundamental for future advancements.
Challenges and Limitations
The discussion surrounding challenges and limitations of electropolishing 304 stainless steel holds significant importance within this article. Recognizing both the hurdles and the potential setbacks provides a foundation for industry professionals aiming to maximize the process's effectiveness. By addressing these specific elements, the reader can better appreciate the complexities involved in achieving optimal results while maintaining efficiency. Moreover, understanding these limitations allows for the development of strategies to mitigate potential problems, thus enhancing the reliability and effectiveness of electropolishing.
Surface Contamination
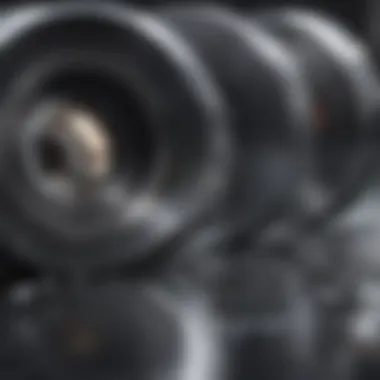
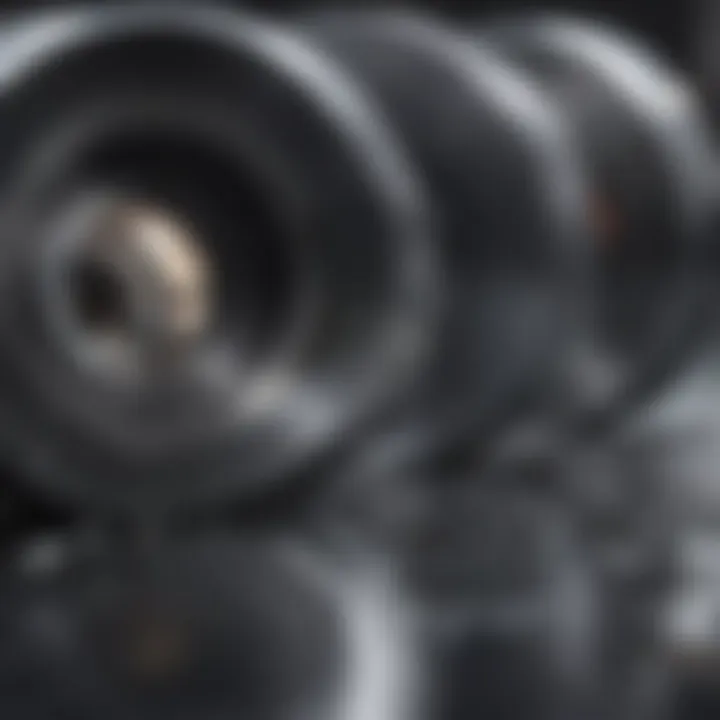
Surface contamination is arguably one of the most significant challenges faced during the electropolishing process. While electropolishing is designed to improve surface quality, any residual contaminants can lead to undesirable results, such as uneven finishes or compromised durability. Contaminants can come from varied sources, including production environment dust, oils from the manufacturing process, or even residues from previous cleaning methods.
The presence of these unwanted substances can adversely affect the electrochemical reaction that takes place during electropolishing. When the surface is not adequately cleaned, it can inhibit the uniform removal of material, leading to an inconsistent finish.
To ensure effective surface polishing, rigorous cleaning protocols are essential.
- Techniques such as ultrasonic cleaning, chemical baths, or high-pressure washing are often employed to ensure all contaminants are removed before the electropolishing begins.
- The material's surface needs to be as pristine as a new pin, or else the electropolishing system will be inefficient. A minute speck of some contaminant can throw the entire process off balance.
Adhering to proper pre-treatment measures can therefore be paramount to achieving the desired results.
Control of Process Parameters
Another critical concern in the electropolishing of 304 stainless steel is the control of process parameters. This includes the voltage, time, and temperature, which all play vital roles in achieving a successful outcome. If even one of these parameters is not correctly regulated, it can lead to surface issues or compromising the structural integrity of the stainless steel.
- Voltage: Higher voltages may speed up the polishing process but could also lead to burning or excessive material removal, further affecting the finish. Conversely, lower voltages might fail to achieve the desired smoothness.
- Time: Determining the optimal duration for the electropolishing process is equally vital. Spending too little time may leave the surface rough, while an overly long process can thin the material too much, stripping away essential protective features.
- Temperature: The temperature of the electrolyte bath also significantly affects the efficiency of the electropolishing process. If it's too high, it can react adversely with the chemicals involved, leading to unwanted side effects.
The balancing act here is critical; finding the sweet spot for all these variables ensures a polished surface while retaining the material's inherent qualities. Regular monitoring and adjustments may be necessary to maintain this equilibrium and yield consistent results.
Equipment and Cost Considerations
When considering electropolishing for 304 stainless steel, potential users must also contend with equipment and cost considerations. The initial investment can be daunting. Specialized equipment is needed to undertake electropolishing correctly; this includes bespoke tanks, power supplies, and certain safety gear.
- Many businesses may face substantial upfront costs associated with purchasing or leasing this equipment. However, it’s important to recognize that the long-term benefits may outweigh these costs if the investment leads to improved product quality and reduced defects in the final products.
- Additionally, there are maintenance and operational expenses to keep in mind. Regular upkeep of equipment is required to ensure peak performance, and the chemicals used must be sourced responsibly, as they can be costly and require careful handling.
Despite the challenges, organizations are often willing to invest in this technology, as the resultant benefits—such as improved product quality and reduced finishing time—can significantly influence operational efficiency. However, making informed financial decisions that account for both immediate costs and long-term gains is essential.
Health and Safety Protocols
The thorough understanding of health and safety protocols in the context of electropolishing 304 stainless steel cannot be underestimated. This process involves the use of synthetic chemicals and equipment that expose practitioners to various hazards. Recognizing these threats is pivotal, as is implementing the necessary measures to mitigate them effectively. The information presented here endeavors to illuminate the importance of safety in industrial processes, particularly those related to chemical handling and electrical operations.
Chemical Hazards
Electropolishing employs acids such as sulfuric acid and phosphoric acid. These substances, potent in their ability to enhance finish quality and improve corrosion resistance, carry significant risks. Contact with these chemicals can result in severe skin burns or respiratory tract irritation if vaporized.
"Safety is a continuous journey, not a destination. Always be prepared and vigilant."
Some specific hazards include:
- Corrosiveness: Direct skin or eye contact can lead to tissue damage.
- Toxicity: Inhalation of fumes can lead to respiratory issues or systemic toxicity.
- Chemical Reactions: Improper handling might lead to unintended reactions that could be explosive or release harmful gas.
Before initiating any electropolishing procedure, it’s critical to conduct a thorough risk assessment, identifying potential hazards particular to the workspace and processes involved. Moreover, maintaining accurate material safety data sheets (MSDS) for every chemical involved serves as an essential reference.
Protective Measures
Adopting protective measures is paramount in ensuring safety during the electropolishing process. The following precautions should be integral to any operational protocol:
- Personal Protective Equipment (PPE): Ensure that all personnel wear appropriate PPE, including gloves, goggles, and face shields.
- Ventilation: Working in well-ventilated areas or using fume hoods can mitigate the level of exposure to harmful vapors.
- Training and Awareness: Regular training sessions can keep staff updated on safety protocols and usage of equipment safely.
- Emergency Procedures: Establish and communicate emergency procedures in case of chemical spills or accidents. This includes having access to eyewash stations and first aid kits.
- Storage Protocols: Store chemicals in clearly labeled, secure containers away from incompatible substances to prevent accidental reactions.
By taking these measures, companies can foster a culture of safety that not only minimizes health risks but also promotes operational efficiency. Individual accountability, paired with comprehensive training, paves the way towards an environment where safety comes first.
Future Trends in Electropolishing
The landscape of electropolishing, particularly concerning 304 stainless steel, is continually evolving. Understanding future trends can illuminate the path forward for various industries relying on this process. Emerging technologies and changing environmental policies are reshaping the industry, making it crucial for professionals to stay informed. As electropolishing processes adapt, the benefits extend beyond mere surface enhancement; companies focused on these innovations can gain a competitive edge in their respective fields.
Technological Advancements
In recent years, technological advancements in electropolishing have changed the game dramatically. Innovations in equipment design and process automation are becoming standard. For instance, automated electropolishing machines, equipped with IoT capabilities, enable real-time monitoring and control of environmental factors such as temperature and flow rate. This automation minimizes human error and improves consistency.
Another aspect worth noting is the role of advanced electrolytes. Traditionally, standard electrolyte solutions have worked well. However, new formulations are being developed that enhance performance while reducing harmful by-products. The creation of environmentally friendly solutions can attract companies looking to improve their ecological footprint.
Furthermore, 3D printing technologies have also influenced electropolishing. As more components are produced using additive manufacturing, the need for specialized polishing techniques is rising. Traditional electropolishing methods may not adequately reach intricate geometries of 3D-printed parts. Therefore, new methods must be researched and developed to effectively polish these unique surfaces.
Sustainability Considerations
Being environmentally friendly isn't just trendy anymore; it's essential in today's world. The push for sustainability in industrial processes has prompted companies to rethink their electropolishing strategies. Circular economy principles are coming into play, urging businesses to consider not just the output of the process but also its overall environmental impact.
The use of green electrolytes, which are less toxic and biodegradable, is gaining traction. Switching from traditional methods to more sustainable alternatives can significantly reduce the environmental footprint. Regulatory compliance is another factor driving this trend. Stricter regulations are pushing industries toward cleaner practices, demanding more transparency in chemical usage and waste management.
Moreover, embracing a more sustainable electropolishing process exerts positive pressure on suppliers and manufacturers to reconsider their material sourcing and production processes. By enhancing the sustainability of electropolishing, companies not only align with regulatory demands but also meet consumer expectations for ethical practices.
"Embracing sustainable practices is not merely a regulatory requirement; it’s an opportunity for innovation and differentiation in the marketplace."