Elastic Resin 3D Printing: A Comprehensive Insight
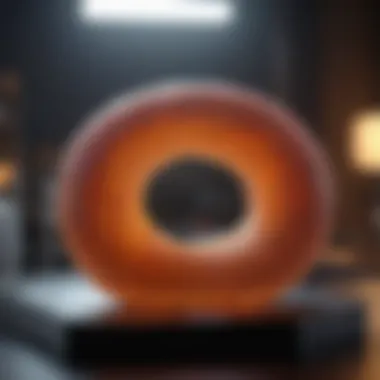
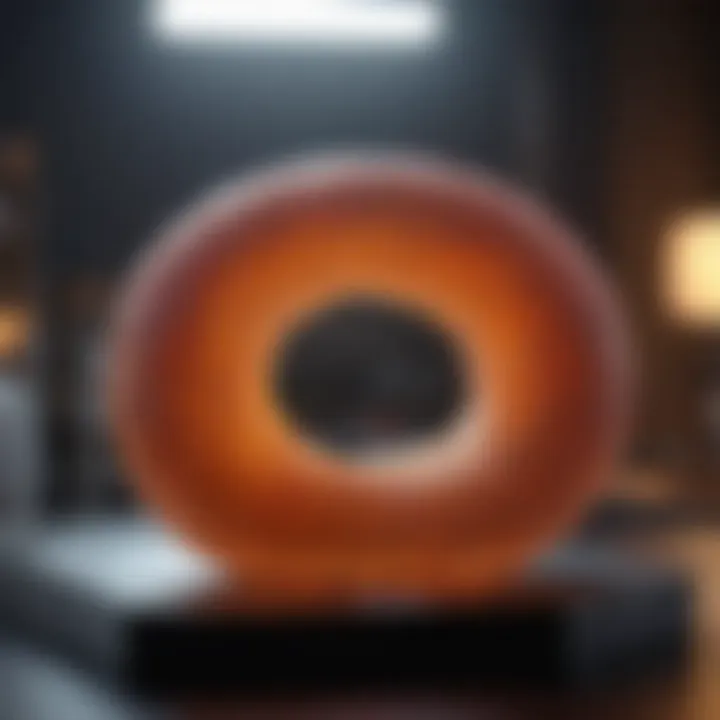
Intro
In the field of additive manufacturing, the exploration of material capabilities continues to push boundaries, and elastic resin 3D printing stands as a notable advancement. Elastic resins, with their unique properties, offer the ability to create items that not only maintain structural integrity but also exhibit flexibility and resilience. This makes them particularly valuable in various sectors, including medicine, automotive, and consumer products.
The rise in the adoption of elastic resin 3D printing highlights a shift in how industries view manufacturing techniques. By enabling the production of customizable, on-demand products, businesses can reduce waste and improve efficiency. Moreover, the applications are vast, ranging from creating medical implants that adapt to patient-specific anatomy to producing rubber-like components for automotive uses. Notably, the innovation does not stop at material composition; advancements in printing technology are on the rise, leading to refined techniques and applications.
However, diving deeper into this subject reveals complexities, both in terms of material science and the intricacies of the printing process itself. Understanding these factors is critical for researchers and practitioners who wish to leverage this technology effectively. In the upcoming sections, we will dissect the recent advances in elastic resin 3D printing, covering the latest discoveries in materials and the technological innovations that are shaping this field.
Preamble to Elastic Resin 3D Printing
Elastic resin 3D printing stands at the forefront of modern additive manufacturing, offering unique benefits that are becoming increasingly vital across various sectors. This technology enables designers and industries to push the boundaries of creativity and functionality, creating parts that are not just rigid and fragile but capable of bending and stretching without losing integrity. The versatility of elastic resins is a game-changer, particularly in applications where soft and flexible materials are demanded.
Definition and Overview
Elastic resin 3D printing refers to the process of creating three-dimensional objects using a liquid resin that, upon exposure to light, undergoes polymerization, leading to a solid product. Unlike traditional rigid materials, elastic resins yield a level of flexibility akin to rubber, making them suitable for applications where durability is essential, yet movement and adaptability are required.
In practice, this means industries can develop prototypes and finished goods that were previously unimaginable. From custom-fit prosthetics to flexible components in consumer products, elastic resin 3D printing opens up a world of possibilities. This approach not only enhances functionality but also contributes to more efficient manufacturing processes, reducing waste and time.
Historical Context
The journey of elastic resin 3D printing began in earnest in the late 20th century with the development of stereolithography - the bedrock of resin printing technology. Early models produced rigid and brittle materials that hardly met the needs of sectors demanding flexibility. But as research advanced, scientists and engineers started to experiment with various formulations and additives. The goal was to produce a resin that could endure bending and stretching while maintaining a high-resolution print.
By the time the 21st century rolled around, the emergence of advanced chemical compositions led to notable strides in this technology. Today, companies focus on tailoring elastic resins for specialized uses, such as creating biocompatible materials for the medical field.
To summarize, the evolution of elastic resin 3D printing showcases a remarkable transition from basic stereolithography models to sophisticated materials that cater to complex requirements.
"This technology has evolved from simple concepts into dynamic solutions that are reshaping industries, evidently highlighting the intricate relationship between material science and engineering."
Understanding elastic resin 3D printing is essential for students, researchers, and professionals alike, as it paves the way for innovations that could redefine product design and manufacturing methodologies in the years to come.
Fundamental Principles of Resin 3D Printing
In the world of 3D printing, understanding the fundamental principles is like having the map before embarking on a journey. This section unpacks the inner workings of resin 3D printing, specifically elastic resin, shedding light on the processes and mechanics that make it a transformative technology in various fields. With a reliable grasp on these principles, one can appreciate both the opportunities it presents and the challenges it poses.
Additive Manufacturing Process
At its core, the additive manufacturing process is what sets resin 3D printing apart from traditional methods, which often involve subtracting material. This technique builds objects layer by layer, adding material only where it’s needed. The elastic resin comes into play prominently in this scenario.
- Layer by Layer Construction: The process begins with a digital model, usually created in software like AutoCAD or SolidWorks. The printer interprets this model into many thin layers, each representing a cross-section of the final product.
- Printer Setup: The resin is placed in a vat, and the printer uses a light source—often ultraviolet light—to cure the resin layer by layer. Stereolithography (SLA) and Digital Light Processing (DLP) are popular technologies that follow this principle.
- Post-Processing: Once printing concludes, the model typically undergoes some cleaning and curing processes to ensure the print achieves its full strength. This might entail rinsing off excess resin and exposing it to additional UV light.
This method not only allows for complex geometries but also produces high-resolution parts with smooth surfaces. The flexibility of elastic resin adds a new dimension, enabling the creation of objects that can bend and absorb shocks, suited for practical applications.
Mechanics of Light Polymerization
Diving deeper, let’s consider the mechanics behind light polymerization, a crucial aspect that governs the entire printing process. In resin 3D printing, light does not just serve as a tool; it’s the catalyst that transforms a liquid material into a solid object.
- Photoinitiators: The resin contains photoinitiators, compounds that absorb light and trigger polymerization. When the light is directed onto the resin, these initiators break down, releasing reactive species that start a chain reaction.
- Chain Growth Reaction: Through a process known as chain-growth polymerization, the reactive species bond with the resin molecules, resulting in a solid network. This happens rapidly, allowing each layer to harden almost instantaneously under specific light wavelengths.
- Curing Depth and Resolution: The depth of cure is influenced by the intensity and duration of the light, which means both speed and resolution can be finely tuned. This aspect also shapes the mechanical properties of the printed item, affecting its flexibility and durability.
"Understanding the mechanics of light polymerization helps in customizing the resin formulations, significantly impacting the finished product's properties."
Being aware of these principles not only enhances the practical use of elastic resin but also opens pathways for innovation. The combination of additive processes and the chemistry of light-driven curing allows manufacturers to create products that were previously unimaginable.
Properties of Elastic Resins
Understanding the properties of elastic resins is central to grasping the nuances of 3D printing technologies. These materials stand out due to their unique characteristics, which offer numerous advantages in various applications. The core essence of elastic resins lies not just in what they are made of, but in how those materials behave when transformed into end products.
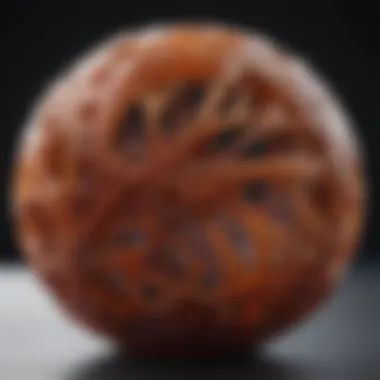
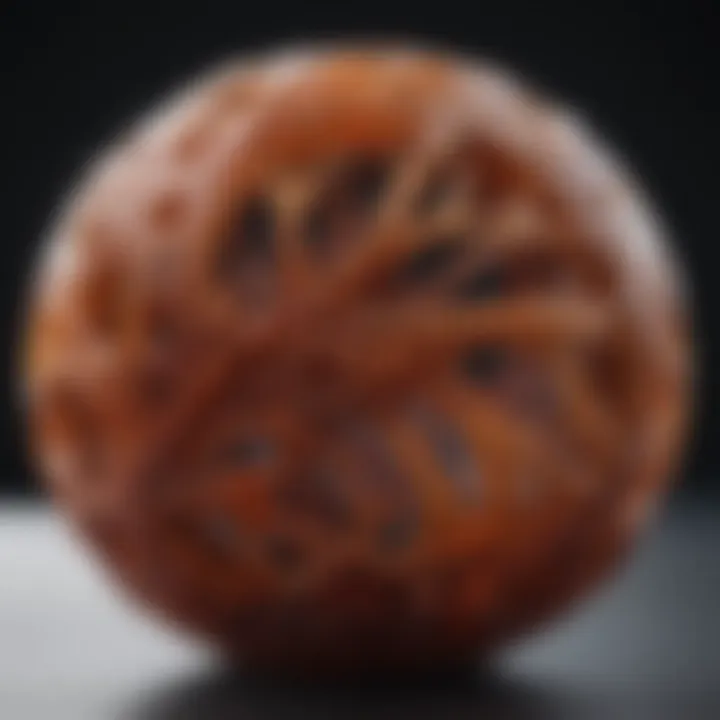
Elastic properties not only enhance the functionality of 3D printed items but also broaden their applicability in industries ranging from medical to consumer goods. Therefore, delving into the composition and mechanical traits of these resins can shed light on their extensive potential in the realm of modern manufacturing.
Material Composition
The material composition of elastic resins is what primarily dictates their performance in the printing process and end-use applications. These resins typically consist of a combination of polyurethanes and other polymers, which confer flexibility and resilience.
- Polyurethane Base: Most elastic resins start with a polyurethane base. Polyurethanes are known for providing excellent elasticity and are traditionally utilized in various industries due to their flexibility, hardness, and durability.
- Additives: Beyond the base polymer, multiple additives can be integrated to alter specific properties. For instance, colorants enhance aesthetic appeal, while various stabilizers can improve resistance to degradation from environmental factors.
- Cross-Linking Agents: These agents are included to adjust how the resin cures. A higher degree of cross-linking generally results in a more rigid structure, while lesser cross-linking will yield a more soft and flexible end product.
This careful balance in material composition ensures that elastic resins fulfill the demands of diverse applications effectively.
Mechanical Properties
The mechanical properties of elastic resins define how these materials perform under stress and over time. Three critical aspects of mechanical properties are flexibility, durability, and tensile strength. Each of these traits contributes to functionality, longevity, and overall user satisfaction.
Flexibility
Flexibility is perhaps the defining characteristic of elastic resins. This property allows for products that can bend and stretch without breaking, making it a popular choice for various applications.
- Key Characteristic: Elastic resins demonstrate remarkable elongation under tensile loads without permanent damage.
- Beneficial Use: This flexibility makes them ideal for components that experience dynamic forces, such as parts in footwear or shock-absorbing elements in prosthetics.
- Advantages/Disadvantages: While flexibility fosters versatility in design, it can also lead to potential concerns regarding stability under high load conditions, which isn’t an issue with more rigid materials.
Durability
Durability plays a crucial role in determining how long a printed object lasts under typical use conditions. Elastic resins, when formulated correctly, can withstand significant wear and tear.
- Key Characteristic: One of the standout traits is their resistance to impact.
- Beneficial Use: This feature is especially beneficial in products like toys, where resilience against repeated use is necessary.
- Advantages/Disadvantages: However, the longevity can depend heavily on the resin formulation. Some formulations might sacrifice durability for flexibility, which could be detrimental in extreme use conditions.
Tensile Strength
Tensile strength is the measure of how much pulling force a material can withstand before breaking. In the context of elastic resins, this metric indicates the balance of flexibility and strength.
- Key Characteristic: Elastic resins can have a fluctuating tensile strength that varies based on the specific formulation used.
- Beneficial Use: Strong tensile strength is crucial for applications where structural integrity is vital, such as in prosthetic devices that must support variable loads.
- Advantages/Disadvantages: The downside? It often necessitates compromises in the flexibility of the material, posing challenges for designers aiming to blend both properties into their products.
Applications of Elastic Resin in Industry
Elastic resin 3D printing has become an essential player in various realms of manufacturing and design. The ability to print items with flexibility and resilience has opened doors that were previously difficult to navigate. This technique presents numerous advantages, including rapid prototyping capabilities, customization potentials, and a broad spectrum of applications across diverse sectors. Industries harness these properties to push boundaries, creating products that meet both consumer needs and regulatory standards.
Medical Sector
Elastic resin's role in the medical field is profound. Especially in developing devices and aids, this material stands out for its ability to mimic the natural movements of human tissues with impressive accuracy.
Prosthetics and Orthotics
Prosthetics and orthotics benefit greatly from elastic resin 3D printing. This technology enables the creation of customized, lightweight prosthetic devices that can adapt to the wearer's lifestyle. The key characteristic here lies in the material's flexibility, allowing for comfortable fitment. This aspect is particularly popular as it assures users that their prosthetics won't just be functional but also user-friendly. A standout feature of prosthetics made from elastic resin is their ability to withstand daily wear without breaking down easily, providing durability that users desire. However, it's worth mentioning that while elastic resin offers great advantages, there remains a substantial initial cost involved in the production, which might be a barrier for some patients.
Biocompatible Devices
Moving onto biocompatible devices, this area has seen significant advances thanks to elastic resin. The ability to print devices that the body can accept without adverse reactions is a game changer. The major quality of these devices is, of course, biocompatibility, which simply means they can interact safely with biological systems. This makes them an excellent choice for applications such as dental aligners, surgical guides, and even implants. A unique feature of these devices is that they can be designed to specifically fit the anatomical features of a patient, improving serviceability and comfort. The downside could be the stringent regulatory requirements that accompany the use of biocompatible materials, potentially slowing down the time it takes for these innovations to reach the market.
Consumer Products
On the other side of the spectrum, the consumer products market reaps considerable benefits from elastic resin 3D printing. Whether it’s footwear or children's toys, the versatility of this material becomes highly apparent.
Shoes and Apparel
When it comes to shoes and apparel, elastic resin is gaining traction for its breathability and custom-fit capabilities. One of the significant advantages is the ability to prototype designs quickly, allowing brands to bring their ideas to life with less risk. The unique feature here is the seamless integration of comfort and style, a combination that appeals to a diverse audience. Nonetheless, the production scaling can become tricky; while small batches are a breeze, larger productions can introduce inconsistency if not managed properly, which is something to always keep in mind.
Toys and Figurines
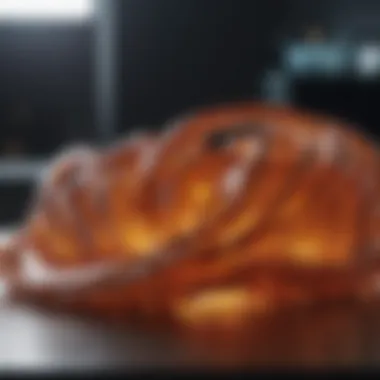
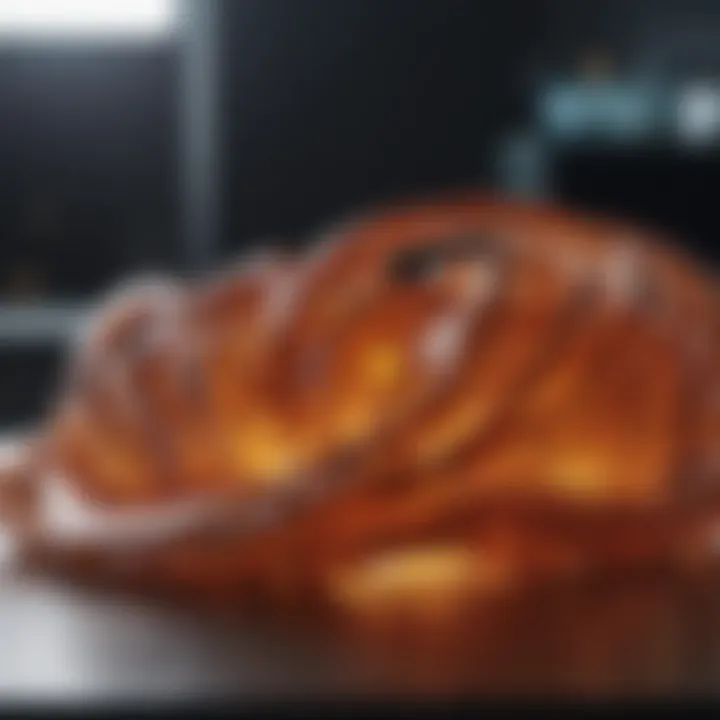
Toys and figurines represent another remarkable application. Here, the key attraction is the precision of the prints. Elastic resin allows designers to create intricate designs that would be tough to achieve with traditional materials. This quality, along with the safety standards achieved through its non-toxic properties, makes it a beloved choice for manufacturers. A notable feature of toys made from this material is their durability, which often means they withstand the rigorous play of children better than their rigid counterparts. Still, there could be concerns over recyclability, as not all elastic resins are made for easy disposal, which is a growing concern for eco-conscious consumers.
By exploring these applications, it becomes evident that elastic resin 3D printing has a significant role across industries, enhancing productivity and allowing for creativity that benefits both manufacturers and consumers alike.
Technical Challenges in Elastic Resin 3D Printing
Elastic resin 3D printing, while a remarkable advancement in technology, is not without its set of challenges. Understanding these technical issues is crucial for designers and engineers who are aiming to push the boundaries of what this technology can achieve. The success of printing with elastic resins relies heavily on overcoming these obstacles, which can significantly affect the quality of the final output as well as the efficiency of the manufacturing process.
This section will delve into the quality issues and material limitations that practitioners frequently face and suggest pathways to address these challenges.
Print Quality Issues
Print quality serves as a cornerstone in the effectiveness of elastic resin 3D printing. Achieving high-resolution prints that maintain the integrity of elastic properties requires meticulous calibration and tuning of both equipment and settings. There are several critical factors that impact print quality:
- Layer adhesion: Elastic resins often need specific curing times and light exposure to bond properly between layers. Insufficient curing can lead to parts that delaminate or tear easily.
- Resolution and detail: Many applications require fine details, especially in medical devices or customized consumer goods. The printer’s resolution limits, as well as resin viscosity, can profoundly affect the ability to produce intricate designs.
- Surface finish: The final texture of printed models depends not just on the chosen resin but also on the workflow. Post-processing steps like sanding or coating can be crucial for achieving a smooth surface but often require additional time and resources.
"The balance between speed and quality is a tightrope walk; cross it wisely to avoid a tumble into poor print outcomes."
As we can see, balancing all these factors is like juggling flaming torches. One miscalculated move and the quality can fall apart, sometimes literally.
Material Limitations
Elastic resins, while versatile, come with their own set of limitations that can impede their widespread adoption or effective usage. These limitations can directly affect the physical attributes of finished products:
- Mechanical properties: While elastic resins are designed to be flexible, certain formulations may not deliver the desired flexibility and tensile strength. For instance, a resin may be too soft for a particular application, causing it to deform under stress.
- Chemical resistance: Different applications demand resistance to various chemicals. Some elastic resins may not withstand exposure to oils, solvents, or extreme temperatures, limiting their usability in certain environments.
- Shelf life and storage: Elastic resins can degrade over time, especially if not stored correctly. This risk can lead to wasted materials and increased costs when resins need to be disposed of or replaced more frequently.
Indeed, recognizing and addressing these material limitations is vital for those venturing into the field of elastic resin 3D printing. Extensive material testing and iteration are often necessary to achieve the desired properties for specific applications. In summary, understanding these technical challenges can provide a solid groundwork for advancements in the technology.
Ultimately, navigating these waters of print quality and material limitations is essential to ensure that the full potential of elastic resin 3D printing is realized.
Innovations in Resin Formulation
The landscape of elastic resin 3D printing is continually evolving, primarily driven by innovations in resin formulation. This segment emphasizes the significance of these advancements, illustrating how they enhance the quality and versatility of printed objects. In an industry that thrives on precision and creativity, the formulation of resin plays a pivotal role in determining not just the mechanical properties but also the overall usability of final products.
With every breakthrough in resin chemistry, manufacturers are able to push the boundaries of what’s possible in additive manufacturing. These innovations not only cater to current demands but also anticipate future requirements from various sectors.
Advancements in Chemical Engineering
Chemical engineering has propelled the development of elastic resins into new realms. Researchers have been experimenting with varied polymer blends, curatives, and additives, each aimed at achieving specific outcomes. For instance, incorporating nano-fillers can dramatically improve the strength and thermal resistance of active materials. This is no mere exercise in tinkering; such advancements allow for the production of extremely lightweight yet durable components.
Moreover, advancements in polymerization technologies, such as double cure systems, enable a faster conversion process, which enhances productivity without compromising the quality. The creation of new, tailored resins using methods like 3D printing-based synthetic polymer processing opens doors to countless applications that were not feasible previously.
Customization of Properties
Customization in resin formulation has become crucial for meeting diverse application needs. Just like a chef who adjusts flavors to suit a dish, 3D printing specialists can now modify resin properties to match specific performance metrics. This customization ranges from altering the hardness and flexibility of a resin to adjusting its opacity and color.
Various sectors can benefit from this tailored approach. For example, the medical industry may need a softer, more biocompatible resin for implants, while the automotive industry may prioritize strength and heat resistance. Additionally, end-users can fine-tune their resin blends based on real-time feedback from their printing workflows, creating a responsive, iterative design process.
The advancements in resin formulation highlight a trend towards not only enhanced performance but also greater adaptability in the face of changing market demands. Innovations here indicate a promising future, suggesting that as designers and engineers, we can expect ever more imaginative solutions to rise from the realms of elastic resin 3D printing.
"The transformation in resin formulation is not just about new recipes; it's about the birth of entirely new paradigms in manufacturing."
Environmental Implications of Elastic Resin Use
Understanding the environmental implications of elastic resin use in 3D printing is crucial for both current and future practices in the technology. As with any manufacturing process, it’s essential to consider various factors that affect sustainability and environmental health. The rise of elastic resin printing, while advantageous in many applications, also brings several challenges that need addressing for a more sustainable future. Let’s dive into the specific aspects of material recyclability and the sustainability of manufacturing practices.
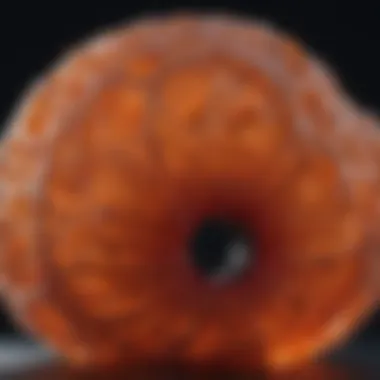
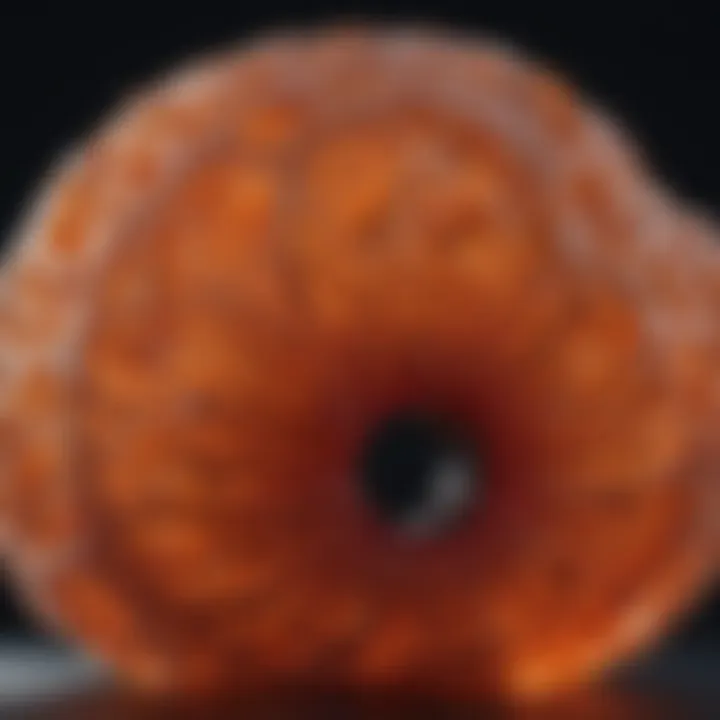
Recyclability of Materials
One of the most pressing concerns regarding elastic resin is its recyclability. Many elastic resins, currently used in 3D printing, struggle with being recycled effectively. Their complex chemical structures often render them incompatible with conventional recycling processes. Consequently, discarded prints may either end up in landfills or require specialized recycling techniques, which could be cost-prohibitive.
However, some companies are already on the ball by developing resins that can be recycled. These innovations not only address waste management issues but also encourage a circular economy in the additive manufacturing sector. Commonly cited benefits of recyclable materials include:
- Reduced Waste: Reusing materials can significantly lower the number of products tossed aside after single use.
- Conservation of Resources: Recycling means less demand for new raw materials, which can help protect natural resources.
- Lower Carbon Footprint: The process of recycling generally consumes less energy than producing new materials, leading to reduced greenhouse gas emissions.
In summary, while traditional elastic resins can pose challenges in terms of recyclability, the advancement in eco-friendly formulations holds promise for reducing environmental impact.
Sustainability in Manufacturing
When we talk about sustainability in manufacturing elastic resin for 3D printing, we need to look beyond just the end-of-life disposal of products. It’s important to consider the entire production cycle, from sourcing raw materials to the energy consumed during printing.
The manufacturing process for these resins often involves complex chemical reactions and high energy consumption, which can contribute to environmental degradation if not managed properly. Here are some elements establishing sustainability in this context:
- Responsible Sourcing: Using bio-based feedstock for resin production can drastically alter the footprint. Companies exploring renewable materials are setting an example for sustainable approaches.
- Energy Efficiency: Adoption of advanced manufacturing technologies that aim to reduce energy consumption during production is essential for a greener future.
- Waste Minimization: Efficient printing techniques that reduce the quantity of support structures needed can lead to less wasted material. Moreover, post-processing methods can also impact sustainability positively.
The demand for more sustainable practices in elastic resin manufacturing is growing. The industry is evolving, but manufacturers need to be proactive about tackling these issues.
"The path to sustainability is not a straight line but a winding road requiring continual evaluation and adaptation."
As elastic resin technologies propel forward, encouraging responsible practices can bolster the environmental integrity of 3D printing as a whole. Furthermore, ongoing research and innovation may yield new approaches that will make elastic resin printing not just efficient, but also environmentally sound.
Future Trends in Elastic Resin 3D Printing
The future of elastic resin 3D printing stands at a fascinating crossroads, where innovation intersects with practicality. As industries continue to evolve, new trends are emerging that promise to enhance both the capabilities of elastic resin materials and the efficiencies of the printing processes involved. Understanding these trends is not just academic; it carries significant implications for those involved in design, manufacturing, and research.
Emerging Technologies
In recent years, several emerging technologies have made waves in the realm of 3D printing with elastic resins. One of the most noteworthy advancements is the development of faster printing processes. Traditional resin printers often took significant time to cure layers. Now, with the introduction of LCD and DLP printers, curing times have been reduced dramatically, enabling quicker turnarounds for prototypes and custom projects.
Additionally, multi-material printing is becoming more prevalent. This capability allows designers to blend multiple elastic resins, creating parts that combine different mechanical properties. Imagine a wearable device that is soft in some areas for comfort but firm in others for support. This innovation could revolutionize industries such as orthotics, where tailored and functionally diverse solutions are vital.
Furthermore, artificial intelligence is making strides in optimizing print settings. Through data analytics, AI can adapt parameters dynamically, ensuring optimal results with minimal waste, therefore addressing one of the main challenges of printing with elastic resins. The automation in either setup or tuning processes makes the whole endeavor more efficient, ultimately saving time and money.
Potential Market Growth
As the capabilities of elastic resin printing continue to expand, so too does the market potential. Industry experts suggest that the demand for customizability is on the rise, particularly in sectors like healthcare and fashion. The global 3D printing market is expected to witness compound annual growth rates that far exceed those of previous years, driven largely by advancements in elastic resin technologies.
- Medical Applications: Custom prosthetics and surgical models printed with elastic resin are becoming more common. The ability to create personalized devices based on patient-specific data enhances the efficacy of treatment plans.
- Fashion Industry: Elastic resins lend themselves well to the production of unique, tailored apparel. With consumers seeking more personalized styles, designers are embracing 3D printing to craft one-off pieces that resonate with individual tastes.
- Consumer Goods: The toy industry, for instance, is witnessing a trend towards customizable designs, where children can create their own toys using 3D printed elastic resins. This encourages creativity and personal ownership.
Epilogue: The Evolution of Elastic Resin 3D Printing
The topic of elastic resin 3D printing holds profound significance not just within the industry, but also for designs and applications across various sectors. This innovation has expanded the horizons of what’s possible in additive manufacturing, reflecting both creativity and technical prowess.
Understanding the evolution of this technology is crucial, as it elucidates how far we’ve come and where we might be headed. For instance, the material advancements have facilitated better performance in flexible applications, allowing designers to create products that can withstand the rigors of real-world use.
Moreover, this discussion highlights the balances that practitioners must navigate—between innovation and sustainability, customization and production cost. Innovations in resin formulation increase the versatility of applications, enabling the creation of everything from intricate prosthetics to vibrant toys and functional consumer goods.
**"Elastic resin 3D printing is not only about flexibility; it’s about shaping the future of manufacturing with precision and purpose."
In sum, the evolution of elastic resin 3D printing is a blend of scientific advancements, market demands, and the exploration of new design frontiers. This sophisticated interplay is what makes this subject an exciting area of study and practice.
Summary of Key Points
- Technological Advancements: The development of elastic resins has far-reaching implications for various industries, enabling more flexible and durable products.
- Wider Applications: From medical devices to consumer goods, the scope of elastic resin applications continues to expand.
- Challenges and Innovations: Addressing print quality and material limitations is crucial for future advancements.
- Sustainability Considerations: The need for environmentally friendly practices is more pertinent than ever, pushing for innovations in material recyclability and overall manufacturing processes.
- Market Growth Potential: As industries embrace 3D printing, the elastic resin market is poised for significant expansion, inviting investment and research into better formulations and techniques.
Final Thoughts
Elastic resin 3D printing has arrived at a pivotal moment, intersecting creativity, science, and market demand. Its trajectory suggests a bright future, riddled with opportunities for innovation and growth. While strides have been made, continued exploration and application of elastic resins will be key in maximizing their potential.
For students, researchers, and professionals alike, diving deeper into this field is not merely an option—it’s an imperative. As the technology matures, the conversations and studies surrounding it will only grow richer, providing valuable insights and tools needed to navigate this evolving landscape. Engaging with this topic opens doors not just to understanding the current state of the art but also to contributing actively to its future.