The Acheson Furnace: A Comprehensive Overview
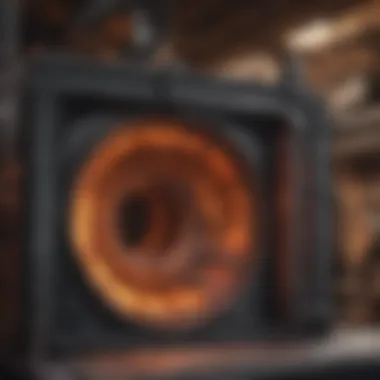
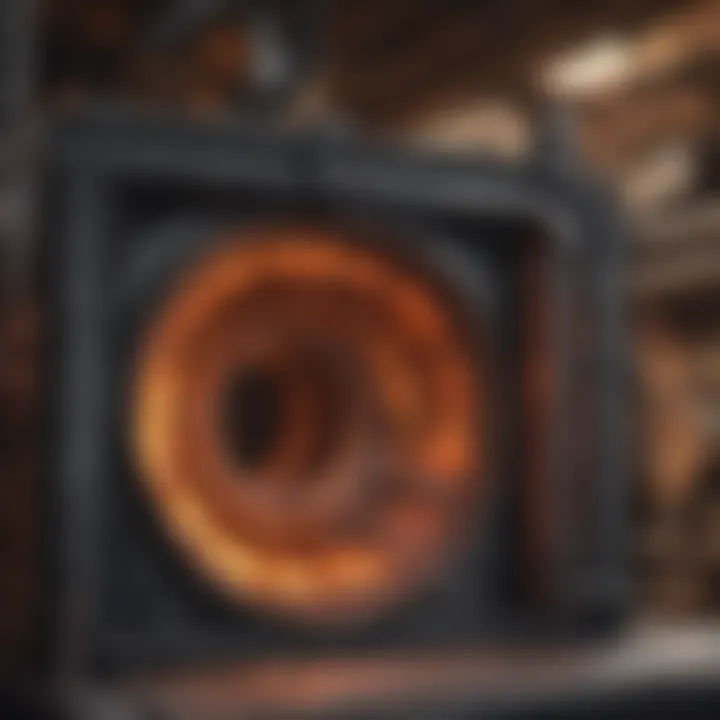
Intro
The Acheson furnace stands as a testament to the evolution of metallurgy and material science. Developed by Edward Goodrich Acheson in the late 19th century, this furnace didn’t just make a splash; it sent ripples through industries. The process of producing silicon carbide—an essential material used in abrasives and other applications—was revolutionized. But, the story of the Acheson furnace stretches far beyond its humble beginnings; it weaves a narrative filled with innovation, persistence, and an ever-growing relevance to modern technology.
Understanding this furnace is pivotal for students, researchers, educators, and professionals alike, as its implications extend into various fields of study and application. From its operational mechanics to its environmental impacts, there's much more than meets the eye in this domain of material science.
Recent Advances
As the world pushes toward more sustainable solutions, recent years have seen significant strides in understanding and optimizing the Acheson furnace's processes and technology.
Latest Discoveries
Researchers have spotlighted the role of silicon carbide in electronics and renewable energy, enhancing the focus on the furnace's production efficiencies. For instance, studies have demonstrated a reduction in energy consumption through innovative techniques in furnace design. These advancements contribute significantly to reducing the carbon footprint associated with silicon carbide production.
Furthermore, scientists have explored the properties of byproducts created during the Acheson process. Incorporating waste streams into other industrial processes is not just good practice; it's a pathway toward circular economy principles. Such findings are fundamental in promoting environmental stewardship and fostering a dialogue around industrial innovation and sustainability.
Technological Innovations
The Acheson furnace has also felt the impact of digital technology. Recent applications of machine learning and artificial intelligence are beginning to find their way into the operational sphere. Utilizing predictive models tailored for real-time monitoring allows for significant improvements in the control of temperature and electric consumption.
This not only enhances production efficiency but also optimizes the quality of the end product. It's an intersection of traditional metallurgy and cutting-edge technology—truly a fascinating area for anyone deeply invested in the industrial and scientific landscapes.
Methodology
When delving into the Acheson furnace, the complexity of its operation necessitates a structured methodology. A comprehensive understanding can be gained through both qualitative and quantitative approaches.
Research Design
The research design typically employs case studies, laboratory experiments, and field studies where the furnace is operational. By examining various setups and configurations, researchers can evaluate the effectiveness of differing methodologies in silicon carbide production and ultimately contribute to scientific knowledge.
Data Collection Techniques
Data collection methods might include:
- Surveys conducted among industry personnel to gather views on operational efficiency
- Interviews with experts in metallurgy for insights into emerging trends
- Direct observations in facilities employing the Acheson furnace to note best practices
Such a meticulous approach ensures that findings are well-rounded and reflective of the furnace's role across varied settings, providing a deeper understanding of its relevance in today’s industrial landscape.
The Acheson furnace is more than an apparatus for silicon carbide production; it is at the confluence of innovation, sustainability, and technological advancement.
Prolusion to the Acheson Furnace
The Acheson furnace stands as a cornerstone in the world of metallurgy and material science, holding significance that extends far beyond its practical function. This furnace not only allows for the production of silicon carbide—a compound gaining prominence in various industries—but also reflects the evolution of industrial processes and technological advancements. Understanding its foundational components and historical backdrop is essential for grasping its enduring impact on modern applications.
Why focus on the Acheson furnace? For students, researchers, and professionals, it represents a focal point in the study of material properties and production techniques. By exploring this furnace, one can unveil the intricate balance between chemical processes and metallurgical science that plays out within its walls. The furnace's operation illuminates vital principles that govern energy efficiency and material integrity, offering a gateway to deeper knowledge in the field.
"Understanding the mechanisms behind the Acheson furnace is key to leveraging its benefits across various technological domains."
Historical Background
To appreciate the Acheson furnace fully, we must first turn back the clock to its inception. Developed by Edward Acheson in the late 19th century, the furnace was born out of necessity; the demand for materials like silicon carbide in abrasives and refractories prompted innovation. At that time, conventional methods of material synthesis were often too inefficient or costly, leaving industry players yearning for an alternative.
Acheson's breakthrough was not merely an accident; it was the result of experimentation and a keen understanding of electrical heating. By introducing electrical current into the production equation, Acheson enabled much higher temperatures, which in turn facilitated the chemical reactions necessary for silicon carbide synthesis. This innovation marked a significant leap in materials science, paving the way for its broader applications in electronics, automotive, and other fields.
Foundational Principles
To grasp how the Acheson furnace operates, one must familiarize oneself with its foundational principles. At its core, the furnace functions on the principle of electrical resistance heating, a method that transforms electrical energy into thermal energy. This is done through the application of powerful electric currents across a carbon-rich charge, primarily consisting of silica and carbon. The ensuing reactions generate the temperatures necessary for silicon carbide production.
Key aspects of these foundational principles include:


- Chemical Reactions: The high-temperature environment within the furnace allows silicon dioxide (SiO2) to react with carbon (C), producing silicon carbide (SiC) and carbon monoxide (CO) as byproducts.
- Energy Considerations: The design of the furnace optimizes energy use. Unlike traditional kilns that may waste heat, the Acheson furnace recycles energy efficiently, thereby reducing operational costs and improving sustainability, which is crucial in today’s eco-conscious landscape.
In deep examining the Acheson furnace, one deduces not only about materials but also about sustainable production practices and innovative methodologies that cut across various domains. With such insights, researchers can make informed decisions as they engage with this technology within their respective fields.
Operational Mechanisms
Understanding the operational mechanisms of the Acheson furnace is pivotal for grasping its significance in metallurgy and material science. This section delves into the intricate design, production processes, and the science behind electrical resistance and heat generation. The prominence of these elements cannot be overstated, as they contribute directly to the efficiency and effectiveness of silicon carbide production, which is a cornerstone in various industrial applications.
Design of the Furnace
The Acheson furnace, in essence, is a marvel of engineering. Its cylindrical structure primarily facilitates the uniform heating of materials. Traditionally, the furnace's body is made from refractory materials, capable of withstanding extreme temperatures that can soar above 2,000 degrees Celsius.
One notable feature of the design is its arrangement of electrodes that are often placed both above and within the charge. This strategic positioning is essential for optimizing heat transfer to the raw materials, ensuring that the silicon carbide crucible operates efficiently. The furnace does not rely solely on ambient heat; instead, it employs a resistive heating mechanism. When electric current flows through the electrodes, it encounters resistance, leading to the generation of heat. This process highlights not only the ingenuity of the design but also its effectiveness in achieving desired thermal conditions.
"The design principles of the Acheson furnace underline its capability to transform raw materials into high-value products through carefully controlled thermal dynamics."
Process of Silicon Carbide Production
Silicon carbide production in the Acheson furnace is a multi-step process. Initially, the furnace requires a mixture of silica and coke with particular ratios. Silica (SiO2) serves as the silicon source, while coke acts as a reducing agent, stripping the oxygen from silicon dioxide to yield silicon. The careful control of these feedstock ratios is critical; an imbalance can lead to inefficiencies or compromise product quality.
- Charging the Furnace - Once the raw materials are prepared, they are charged into the furnace.
- Heating Phase - The electrodes supply the electric current that heats the charge, generating temperatures that enable the reaction between silica and coke to proceed.
- Reaction Phase - The carbon from the coke reacts with silicon dioxide, resulting in silicon carbide (SiC) and carbon monoxide gas. This phase is vital as it determines the properties of the end product, including its strength and conductivity.
After several hours—the duration depends on various factors, including the desired purities and production rates—the furnace is cooled, and the silicon carbide product is extracted. This non-linear heat profile is critical in producing high-quality silicon carbide, which can be tailored for numerous applications ranging from abrasives to semiconductor materials.
Electrical Resistance and Heating
At the core of the Acheson furnace's operation lies the principles of electrical resistance and heat generation. The electrical resistivity of the charge and the furnace's construction significantly influence the heating process. The key to effective resistance heating is the careful selection of the raw materials and the furnace’s geometry.
Key Considerations:
- Material Choice - The type of coke and silica used affects both the quality and efficiency of heat generation. Different grades can lead to variations in resistance.
- Temperature Gradient - The design aims to achieve a consistent temperature gradient throughout the charge. Hot spots can lead to material degradation.
- Power Input - The electrical input is adjusted based on the resistance encountered; this adaptability is essential for maintaining desired operating conditions.
Thus, the interconnected design of the furnace with its heating methods exemplifies innovative principles of physics and material science. Here, efficiency and adaptability are of paramount importance, and engineers continue to explore ways to enhance these aspects for improved production outcomes.
Understanding these operational mechanisms not just fosters a deeper appreciation for the Acheson furnace but also emphasizes its vital role in advancing material technology. This insight is encourged for all those involved in research, education, and industry.
Applications of the Acheson Furnace
The Acheson furnace plays an indispensable role in various industries, demonstrating its significance beyond mere silicon carbide production. This furnace allows for remarkable company innovations and advancements in materials, making it a cornerstone technology. Understanding its applications across different fields can elucidate how integral this furnace is to both existing methodologies and new research avenues.
Electronics Industry
The electronics industry sits at the forefront of technological advancement, and the Acheson furnace is pivotal in the production of silicon carbide, a crucial substrate for many electronic devices. Silicon carbide has superior thermal conductivity and is exceptionally durable, making it an excellent choice for high-performance electronic components. In power electronics, which include devices like MOSFETs and diodes, silicon carbide helps manage higher voltages efficiently, thus enhancing energy efficiency in electronic circuits. The Acheson process provides a more economical way to produce this essential material compared to other synthesis methods. Consequently, the furnace not only empowers the electronics sector but also contributes to the broader goal of sustainability and reduced environmental impact.
Material Science and Engineering
In the realm of material science and engineering, the Acheson furnace is a valuable asset. Its ability to produce highly pure and finely controlled silicon carbide opens doors to advanced research and development in composites and nanomaterials. Researchers can tailor the properties of silicon carbide to create custom materials suitable for various applications, such as cutting tools, abrasives, and even as a semiconductor material in some experimental technologies.
Moreover, the operational aspects of the Acheson furnace enable scientists to explore complex behaviors of materials under varying temperatures and reactions. This insight leads to creative solutions in material engineering challenges, eco-friendly alternatives to traditional materials, and innovations that could change how we think about composite creation.
Refractories and Ceramics
The Acheson furnace's utility extends to the production of refractories and ceramics. With its capability to reach high temperatures and maintain them with remarkable consistency, the furnace allows for the synthesis of high-performance ceramic materials. These materials are vital in environments where heat resistance is non-negotiable, like furnace linings, kilns, and other high-temperature applications.
Different ceramics produced through the Acheson process can handle thermal shock and chemical erosion effectively. This resilience contributes to improved lifespans and reduced maintenance costs in industries that rely heavily on these materials.
Additionally, hybrids made from silicon carbide and other ceramic components can lead to lighter, more efficient materials suitable for aerospace and automotive applications. Such adaptability signifies the significant impact of the Acheson furnace on the field of ceramic engineering.
In summary, the applications of the Acheson furnace are diverse and transformative, influencing sectors from electronics to material science and beyond. Each application not only highlights the furnace’s contribution but also underscores its potential in fostering innovations that benefit many industries.
Environmental Considerations
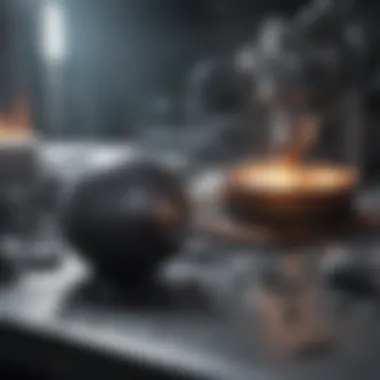
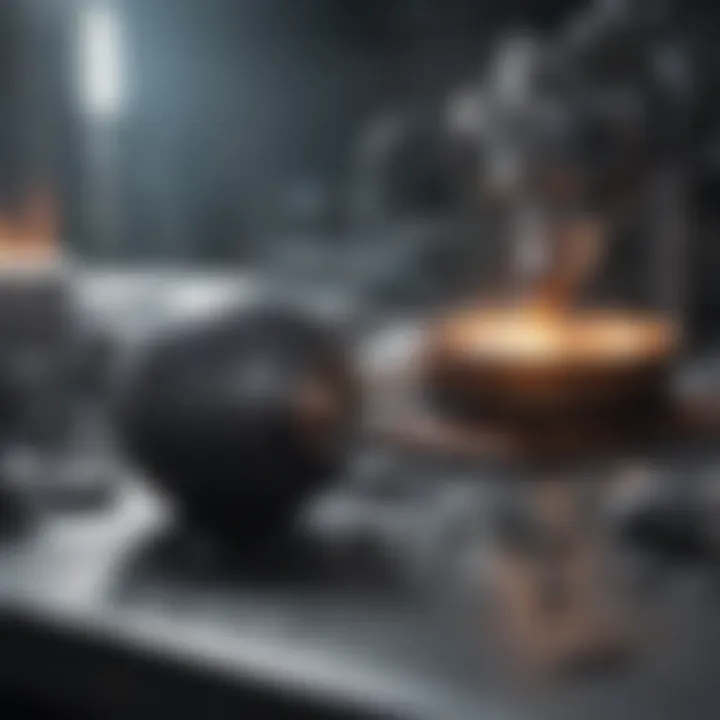
Understanding the environmental considerations related to the Acheson furnace is crucial not only for the sustainability of operations but also for compliance with modern regulations. As industries have evolved, so has the need to minimize their ecological footprint. The Acheson furnace, prominent in silicon carbide production, does represent both technological achievement and environmental responsibility. This section discusses three vital aspects: energy consumption and efficiency, emission profiles, and regulatory compliance.
Energy Consumption and Efficiency
Energy efficiency is a significant matter when it comes to industrial furnaces. The Acheson furnace operates on principles that can lead to both high energy consumption and efficiency. Its design facilitates optimal heating, which is a double-edged sword. While it can achieve specified temperatures quickly, the demand for high-energy input remains substantial.
For instance, the construction of the Acheson furnace allows for efficient energy transfer. The electrical resistance heating method ensures that energy is utilized effectively to convert carbon and silica into silicon carbide. Nonetheless, energy consumption must be balanced with output. Excessive energy use not only inflates production costs but also raises concerns about long-term sustainability. Some organizations have started to adopt smart energy management solutions that monitor and optimize energy use.
Key Points in Energy Consideration:
- Maximizing Efficiency: Employing modern insulation materials can improve energy conservation.
- Alternative Sources: Investigating renewable energy sources for powering operations is becoming increasingly popular.
- Cost Management: Reducing energy consumption directly impacts the cost of production, making it a financial as well as environmental concern.
Emission Profiles
Emissions from the Acheson furnace are another crucial environmental aspect. The production of silicon carbide does emit various gases, among which siloxanes and carbon dioxide are of significant concern. Gaseous emissions from industrial processes can lead to air quality deterioration and contribute to climate change.
Moreover, the challenge lies in quantifying the emissions produced. It often varies by production method, raw materials used, and specific operational practices. Implementing effective venting and filtering systems can drastically reduce those unwanted byproducts. An understanding of the emission profiles can guide companies toward more environmentally friendly practices while maintaining their operational goals.
"A comprehensive emission monitoring system not only aids in compliance, but also enhances environmental stewardship and corporate responsibility."
Regulatory Compliance
Tying the various elements discussed, regulatory compliance looms large over the operational practices involving the Acheson furnace. Regulations differ widely from region to region, and keeping abreast of these requirements is essential for ongoing operational viability. Moreover, non-compliance risks hefty fines and long-term damage to a company’s reputation.
Regulatory bodies often set limits on permissible emissions, mandating companies to implement necessary pollution control devices or practices.
Areas for Compliance Focus:
- Monitoring and Reporting: Haphazard data collection can lead to underreporting emissions, so regular and systematic efforts in tracking are essential.
- Adoption of Best Practices: Learning from industry best practices can fulfill regulatory mandates while enhancing operational efficiency.
- Stakeholder Engagement: Engaging communities it operates within not only aids in compliance but also builds goodwill and support.
In summary, examining the environmental considerations surrounding the Acheson furnace underscores a holistic approach to its operations. Institutions must continually assess energy efficiency, emissions, and compliance to promote sustainable practices in pursuit of technological advancement.
Advancements in Furnace Technology
The pace at which furnace technology evolves is nothing short of remarkable. In the realm of the Acheson furnace, innovations are continually shaping operational efficiency and output quality. Understanding these advancements is crucial, not just for professionals in metallurgy, but for anyone invested in the future of industrial processes. The emergent technologies are not merely incremental changes; they can lead to substantial benefits, including improved sustainability, enhanced production rates, and greater economic viability.
Innovative Materials
When it comes to innovation, the materials used in the construction and functioning of the Acheson furnace stand at the forefront. Presently, researchers are exploring materials that can withstand extreme temperatures while providing excellent thermal efficiency. For instance, advanced ceramics and high-performance alloys have been noted for their resilience and superior thermal properties. This transition towards more robust materials enables the furnace to operate at higher temperatures without compromising structural integrity, thus facilitating the production of high-purity silicon carbide.
In addition, these innovative materials often contribute to reduced maintenance costs. By minimizing wear and tear over time, facilities can significantly lower their operational expenditures.
Automation and Precision Control
Automation has become a game changer in furnace technology. The integration of smart control systems enhances the operational precision of the Acheson furnace, leading to optimized performance and reduced waste. These systems utilize real-time data analytics to monitor various parameters, such as temperature gradients and material flow rates, allowing operators to adjust settings instantly to maintain optimal conditions.
This shift toward automation not only boosts productivity but also enhances safety by minimizing human error.
Moreover, intelligent algorithms can predict potential failures by analyzing historical data patterns, thus enabling preemptive measures. Consequently, plant managers can schedule maintenance in advance—hardly a small feat when every hour of downtime can mean lost profits.
Future Trends and Research
Looking ahead, the trajectory of furnace technology suggests a landscape rich with possibilities. Research is currently focused on integrating renewable energy sources into furnace operations, aiming to reduce dependency on fossil fuels and decrease carbon footprints. Innovations like solar-assisted heating and hydrogen fuel usage are gaining traction, representing not just a shift in techniques but a fundamental change in how we view energy consumption in industries.
Furthermore, advancements in machine learning are set to provide new insights into material behaviors at molecular levels, paving the way for tailored formulations of silicon carbide and other materials produced. This would not only enhance the furnace's output quality but also offer customized solutions for specific applications across various sectors.
Comparative Analysis
The comparative analysis of the Acheson furnace is a crucial aspect of understanding its position within the broader context of metallurgical methods and technologies. By contrasting the Acheson furnace with alternative approaches, one can appreciate not only its unique advantages but also the challenges it faces. This analysis sheds light on various elements that are beneficial for industry professionals and researchers alike.
While discussing the comparative benefits, one must consider:
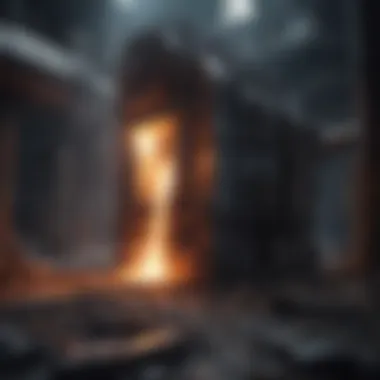
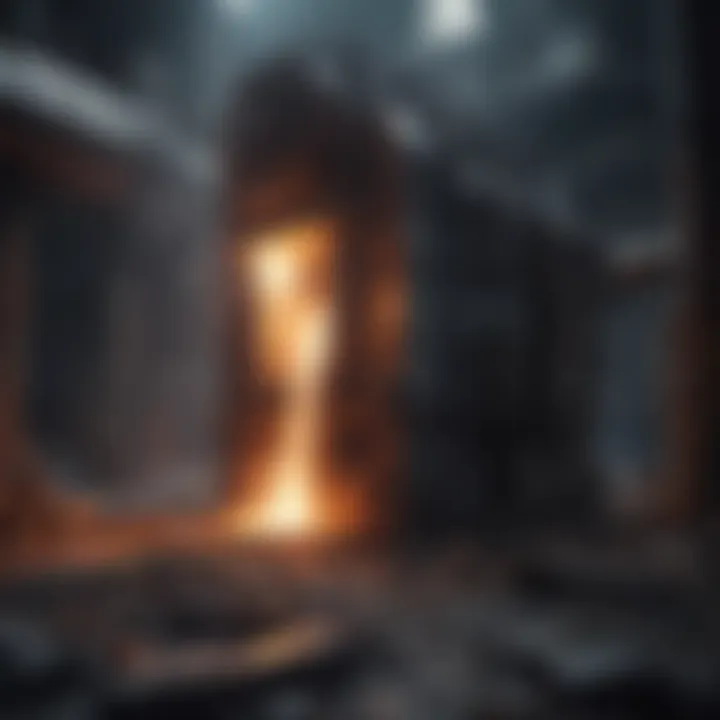
- Efficiency - The Acheson furnace is often touted for its energy efficiency compared to traditional methods like electric arc furnaces. Its design allows for continuous operation, which can significantly lower energy costs over time.
- Product Quality - The furnace produces high-purity silicon carbide, a crucial material in numerous applications, from semiconductors to abrasives, thus fulfilling stringent quality requirements better than many competing methods.
- Scalability - The Acheson process can be scaled up to meet industrial demands, making it a versatile choice for manufacturers wishing to remain competitive in a rapidly evolving market.
- Environmental Impact - Compared to other methods, particularly those that rely heavily on fossil fuels, the Acheson furnace can produce fewer emissions and align better with modern sustainability goals.
However, it is equally important to consider the challenges that come with its use and the capacity to adapt:
- Initial Setup Costs - Installing an Acheson furnace might involve higher upfront investments compared to simpler setups, which can deter smaller enterprises.
- Operational Expertise Required - The furnace demands knowledgeable personnel to operate effectively, which poses challenges for training and maintaining skilled workers in environments with frequent technology shifts.
"By examining the Acheson furnace in comparison to other methods, stakeholders can better strategize their material production capabilities and align with industry standards. Quality, efficiency, and environmental concerns remain at the forefront."
Acheson Furnace vs. Other Methods
To draw a meaningful distinction, it helps to look at the Acheson furnace alongside its closest competitors. When weighed against methods such as the electrothermal processing used in arc furnaces, or the traditional methods of producing silicon carbide via carbothermal reduction, some clear differences surface.
- Electrothermal Processing
- Carbothermal Reduction
- Energy Use: Higher energy consumption due to drastic temperature fluctuations.
- Material Purity: Varies significantly based on process control, while Acheson offers consistent results.
- Material Cost: Initial material costs might be lower.
- Control over Product: Acheson’s controlled environment yields more predictable outcomes, which is vital in applications where precision matters.
These comparisons reveal that while alternatives exist, the Acheson furnace holds its ground as a reliable choice in many instances.
Case Studies: Success Stories
Exploring the success stories that emerge from the Acheson furnace application can offer deeper insight into its real-world impact. For instance:
- Silicon Carbide in the Electronics Sector: One notable case involves a semiconductor company that shifted to the Acheson process for silicon carbide production. By opting for this method, they increased their silicon purity levels by over 15%, which significantly enhanced their product performance.
- Automotive Industry Applications: A responsibly sourced silicon carbide was used in electric vehicle batteries, demonstrating long-lasting benefits over competing materials and ensuring better efficiency in power output.
- Research Institutions: Several universities have utilized the Acheson process in their material science programs, leading to innovative research on new composites that promise even more effective applications in various fields.
These success stories not only amplify the credibility of the Acheson furnace but also highlight how its applications can evolve alongside technological advancements and market needs. They ensure that stakeholders in metallurgy and material science appreciate the real-world implications of adopting this method.
Challenges and Limitations
When discussing the Acheson furnace, it's vital to address the challenges and limitations that come hand-in-hand with its operation. Such considerations not only highlight areas where improvements can be made but also provide a realistic view of its prevalence in modern industry. Understanding these aspects is crucial for students, researchers, and professionals who are diving into the intricacies of metallurgy and materials science.
Technical Limitations
The Acheson furnace, while a marvel of engineering, does not come without its technical hurdles. Some notable limitations include:
- Heat Control Issues: Maintaining precise temperature levels throughout the furnace can be tricky. Variations can lead to inconsistent product quality, which is detrimental in high-stakes applications like electronics.
- Material Constraints: Certain materials used in the furnace's structure may not withstand extreme conditions over extended periods. For instance, refractory linings can degrade, impairing operational effectiveness.
- Scaling Challenges: As the furnace operates at high temperatures, some energy may be wasted in heating the furnace structure rather than the material being processed. This aspect can lead to energy inefficiency, prompting discussions around better thermal management.
- Environmental Impact: While strides have been made regarding emissions, there still exist technical questions regarding waste management associated with certain raw material inputs, making compliance with environmental standards a continual challenge.
These technical limitations necessitate ongoing research and development to ensure that the Acheson furnace can meet the demands of modern applications effectively.
Economic Viability
Economic factors also greatly influence the effectiveness of the Acheson furnace in current markets. Several key aspects can affect its viability:
- Capital Expenditure: The upfront costs of acquiring and setting up an Acheson furnace can be daunting for some companies. This includes not only the purchase price but also the expenses related to installation, safety systems, and maintenance infrastructure.
- Operational Costs: The ongoing expenses related to energy consumption are significant, particularly in a world increasingly focused on sustainability. High energy prices can eat into profit margins, compelling businesses to find ways to optimize operations.
- Market Demand Fluctuations: Changes in the demand for products made from silicon carbide can directly affect economic stability. If demand plummets due to market saturation or the emergence of alternative materials, it could lead to an economic strain on firms relying heavily on this technology.
- Return on Investment: Companies need to carefully consider whether the investment in Acheson furnace technology will yield a worthwhile return. This factor becomes even more pressing in a competitive market where innovation is rapid and consumer preferences shift.
It's essential to balance these economic considerations against the furnace's benefits, such as high production efficiency and product quality, to formulate an informed perspective on its role in the future of material sciences.
"Assessing both the technical limitations and economic viability of the Acheson furnace is imperative for ensuring its sustainable operation in an evolving industrial landscape."
Ending
The discussion surrounding the Acheson furnace reaches a fitting culmination, one that underscores its importance in both historical and contemporary contexts. Throughout this narrative, several key points illuminate just how instrumental this furnace is to the fields of metallurgy and material science. From its inception to its ongoing applications, the Acheson furnace has cemented its place in the development of silicon carbide and beyond.
Summarizing Key Points
- Historical Significance: The Acheson furnace has a storied past, evolving from a novel concept in the early 20th century to a cornerstone of modern industrial processes.
- Operational Mechanisms: Its unique design and electrical resistance heating processes enable efficient silicon carbide production, showcasing how innovative engineering shapes material properties.
- Industrial Applications: The Acheson furnace serves diverse sectors including electronics and ceramics, illustrating its versatility and importance in technology advancement.
- Environmental Impact: As industries increase their focus on sustainability, understanding the energy consumption and emission profiles of the Acheson furnace becomes vital for compliance and innovation.
- Future Directions: Innovations in materials and automation stand ready to propel the Acheson furnace to new heights, ensuring its relevance in an ever-changing market.
These points combine to illustrate why the Acheson furnace is not just a relic of industrial history but a dynamic contributor to future advancements in material science.
Looking Forward
When pondering the future of the Acheson furnace, one can’t help but feel an air of excitement about the possibilities ahead. As research continues, several considerations loom large:
- Emphasis on Sustainability: In an age where energy efficiency and reduced emissions guide development, modifications to the Acheson furnace must align with these principles. This means not just optimizing for productivity but creating greener processes.
- Enhanced Automation: With the rise of Industry 4.0, incorporating advanced automation and precision control into furnace operations could lead to enhanced accuracy and reduced human error, ensuring consistent output quality.
- Diverse Applications: Emerging fields such as nanotechnology and renewable energy could see a significant influence from Acheson technology. The potential to manipulate material properties at a microscopic scale could yield breakthroughs in various industries.
As we look to the future, it’s essential to keep an eye on innovations that can re-shape our processes and materials, pushing boundaries in the name of efficiency and sustainability.