Innovations in Friction Stir Additive Manufacturing
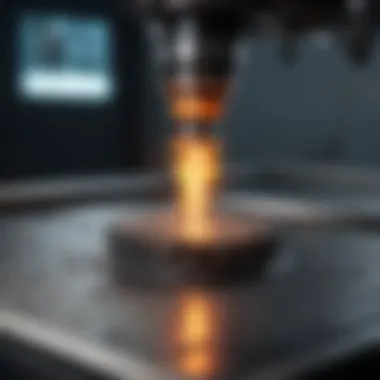
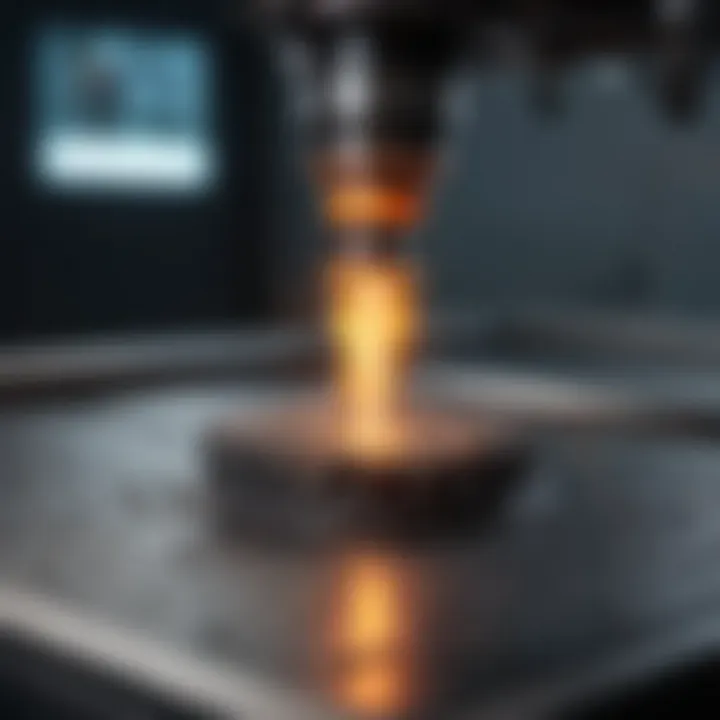
Intro
Friction stir additive manufacturing (FSAM) represents a significant leap in the realm of production techniques. This method fuses friction stir welding principles with additive manufacturing processes to create components. Key to its appeal is the capacity to fabricate parts from a variety of materials. The unique mechanisms involved make FSAM suitable for various sectors, including aerospace, automotive, and marine industries.
Understanding FSAM invites a deeper exploration of its core principles, technological advancements, and real-world applications. This article aims to elucidate these aspects, emphasizing the importance of this method in modern manufacturing. We will look at the latest advances, methodologies, and the implications of adopting FSAM in production environments.
Recent Advances
Latest Discoveries
Recent research highlights several breakthrough developments in friction stir additive manufacturing. Researchers have focused on improving material properties through optimized processing conditions. For instance, studies have shown that alterations in temperature control and feed rates can enhance mechanical properties like strength and ductility.
In particular, the use of alloys demonstrates promising results. For instance, Ti6Al4V, a titanium alloy, has displayed superior performance under friction stir conditions. This discovery shows that FSAM holds potential for creating lightweight yet robust components.
Technological Innovations
Various technological innovations have emerged in FSAM. Advanced robotics and automation have streamlined the process. These innovations allow for precision in material deposition and reduce production time. Furthermore, the integration of computer numerical control (CNC) machines with FSAM technologies has facilitated greater control over the welding process.
Another innovation includes the development of hybrid systems. These systems combine traditional techniques with FSAM, creating a synergistic effect. This merger allows for complex geometries and reduces residual stresses in the final product.
Methodology
Research Design
The research design for evaluating FSAM involves both qualitative and quantitative methods. Researchers often employ laboratory experiments in controlled settings to analyze the effects of different variables, such as temperature and feed rate, on the material properties of finished components. Following this, simulation studies are conducted to predict performance in real-world applications.
Data Collection Techniques
Data collection techniques are crucial for understanding the performance of friction stir additive manufacturing. Common practices include:
- Material characterization: Analyzing microstructural features and mechanical properties through methods such as scanning electron microscopy and tensile testing.
- Process monitoring: Utilizing sensors to gather real-time data on temperature variations and material flow during the FSAM process.
- Feedback loops: Implementing systems that allow for immediate adjustments based on monitored data, thus enhancing the effectiveness of the manufacturing process.
Through these methodologies, researchers can create a comprehensive picture of how FSAM can be leveraged in various applications, ensuring both efficiency and sustainability in production.
Prologue to Friction Stir Additive Manufacturing
Friction stir additive manufacturing is increasingly becoming a significant area of interest within modern manufacturing practices. As industries strive for more efficient production methods, understanding this technology provides critical insights into its pivotal role in shaping future capabilities. This form of manufacturing combines traditional friction stir welding with additive processes, unlocking new possibilities in creating complex geometries and optimizing material usage.
Definition and Overview
Friction stir additive manufacturing can be defined as a solid-state process that utilizes frictional heat generated between a rotating tool and the material it works upon. Unlike conventional welding, where materials essentially melt and then fuse, this approach allows metals to be 'stirred' together without reaching their melting point. This unique technique offers several benefits: it enhances mechanical properties, reduces defects, and typically results in better yield strength. The process is adaptable for various materials, including metals and polymers, allowing a broad range of applications.
Historical Development
The concept of friction stir welding was introduced in the early 1990s. Originally, it was primarily used for welding aluminum alloys. However, over time, researchers began exploring the potential to extend this method into additive manufacturing. Significant advancements have since occurred in technology and application.
By the 2000s, many industries began adopting this technique, primarily in aerospace and automotive sectors for producing lightweight components. The integration of friction stir technology into additive manufacturing is still evolving, pushing the boundaries of what can be achieved. For example, today, companies utilize sophisticated software and hardware systems to enhance precision and control during the additive processes.
In summary, friction stir additive manufacturing represents a convergence of established techniques and innovative practices, signifying a move toward efficiency and sustainability in production methods.
The Mechanics of Friction Stir Processing
The mechanics of friction stir processing (FSP) is a critical aspect of friction stir additive manufacturing (FSAM). Understanding this area is essential for comprehending how FSP influences the efficiency and quality of the additive manufacturing processes. At its core, FSP integrates thermal and mechanical principles to facilitate the consolidation of materials. This enables effective layering and bonding of materials, which is vital in creating complex geometries with high precision.
Core Principles of Friction Stir Welding
Friction stir welding (FSW) is the foundational principle behind friction stir processing. It employs a rotating tool, which generates heat through friction as it moves along the workpiece. The combination of this heat and the forging action creates a softened zone where the material can be easily plasticized. The primary elements of this technique include:
- Heat Generation: The friction between the tool and the workpiece induces heat. This raises the temperature of the material to a level that allows it to become malleable without reaching its melting point.
- Tool Design: The geometry of the tool plays a crucial role in the welding process. Different designs can optimize heat distribution and material flow, which directly affects the strength and integrity of the joint.
- Material Flow: Controlled flow of the material around the tool is essential. In FSW, the material moves in a specific manner, allowing for effective mixing of different materials, if required.
In essence, the core principles of friction stir welding are critical in ensuring that the resulting joints are strong and reliable, making this technology beneficial for various applications.
Additive Manufacturing Techniques Integration
Integrating additive manufacturing techniques with friction stir processing enhances the versatility of this technology. Unlike traditional additive methods that often rely on melting and solidification, the FSP approach focuses on solid-state processing. This results in a number of advantages:
- Enhanced Material Properties: The solid-state processes involved in FSP tend to produce parts with superior mechanical properties. Moreover, they minimize defects commonly seen in molten processes.
- Broader Material Range: FSP allows for the use of a wider variety of materials, including certain alloys that may not be suitable for conventional additive manufacturing methods.
- Layered Manufacturing: This technique promotes consistent layering, which is key in building up components layer by layer without losing structural integrity.
"Friction stir processing leverages the principles of welding and integration with additive techniques to redefine the possibilities of material application."
Understanding the mechanics of friction stir processing provides insights into how these advancements can significantly influence manufacturing practices. By employing the principles of heat generation, material flow, and tool design, the adaptation of FSP techniques opens new avenues in material science and application development.
Material Considerations in Friction Stir Additive Manufacturing
Understanding material considerations in friction stir additive manufacturing is essential for developing effective and reliable products. This bottom-up approach allows for the precise manipulation of material properties, ensuring optimal performance under various conditions. As the field evolves, recognizing the right materials and their behavior becomes vital for advancements in the technology itself.
Suitable Materials
Friction stir additive manufacturing can utilize a range of materials, but certain criteria must be met for optimal outcomes. Commonly suitable materials include aluminum alloys, titanium alloys, and magnesium alloys. These metals are known for their favorable mechanical properties, high strength-to-weight ratios, and good weldability. However, some others like polymer composites and certain steels are also gaining traction in the industry.
- Aluminum Alloys: Particularly those from the 2xxx and 6xxx series, are frequently employed. Their lightweight composition is beneficial for aerospace and automotive industries.
- Titanium Alloys: Valued for their corrosion resistance and strength, they are particularly essential in medical and aerospace applications.
- Magnesium Alloys: Known for their low density, they are increasingly used in sectors requiring lightweight solutions.
The choice of material impacts both the technical outcomes and cost-effectiveness of the manufacturing process. Factors like thermal conductivity, melting point, and ease of processing play vital roles. A deep understanding of these materials ensures that the manufactured parts will meet the required specifications.
Material Properties and Behavior
The properties and behavior of materials during friction stir additive manufacturing significantly affect the final product quality. Key considerations include:
- Thermal Properties: Understanding how materials react under heat is crucial. The process involves heating materials sufficiently for plastic deformation without reaching melting points.
- Mechanical Properties: Strength, ductility, and fatigue resistance are critical. Different materials exhibit varying performance during and after the process.
- Microstructure: The process influences the microstructure of the material, which in turn affects strength and durability. Fine grain structures are generally desirable for enhanced mechanical properties.
Analyzing these factors helps engineers design better components that utilize the benefits of friction stir additive manufacturing.
"The interaction of material properties with processing conditions determines the success of friction stir additive manufacturing processes."
In summary, selecting suitable materials and understanding their properties is key to enhance performance and reliability in friction stir additive manufacturing.
Applications Across Industries
The significance of friction stir additive manufacturing extends across various sectors. This technology combines the robustness of friction stir welding with the adaptability of additive processes. In the face of modern industrial demands, its application enhances production efficiency, material performance, and environmental sustainability.
Aerospace Engineering
In aerospace engineering, the application of friction stir additive manufacturing proves crucial. It allows for the creation of complex and lightweight structures essential for modern aircraft. Traditional methods often struggle with material integrity and weight limitations. However, the innovative approach of friction stir enhances bonding strength due to its solid-state processing nature.
The aviation industry prioritizes safety and reliability. The method facilitates the production of aerodynamically optimized components, like aircraft wings and fuselage sections. These parts benefit from reduced weight, leading to improved fuel efficiency and lower emissions.
Key benefits include:
- Improved mechanical properties compared to traditional welding.
- Reduction of defects common in fusion-based processes.
- Ability to use advanced alloys, enhancing overall performance.
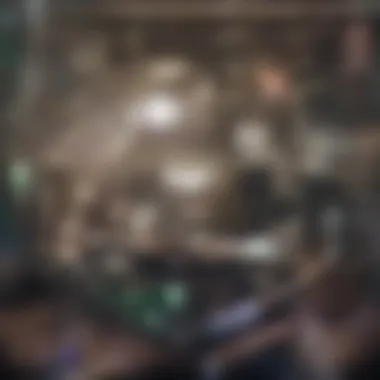
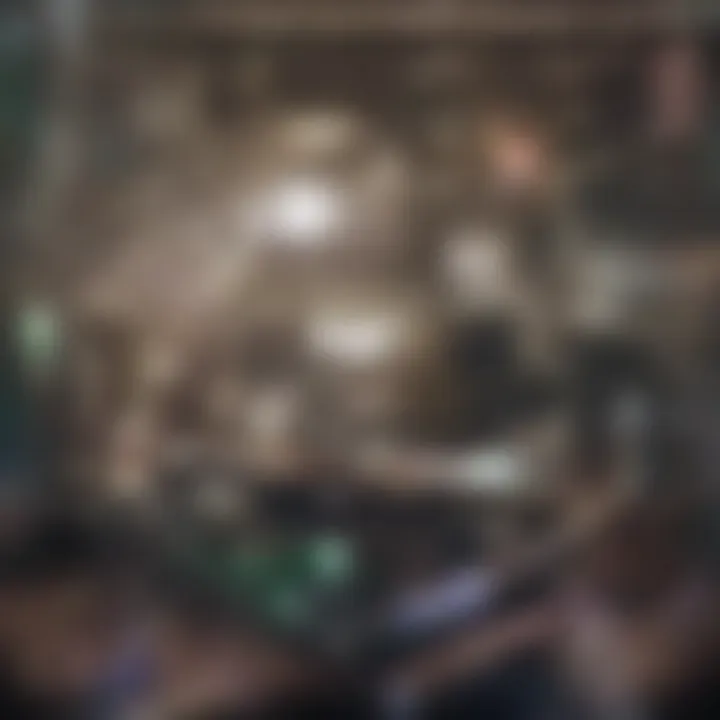
Overall, friction stir additive manufacturing is paving the way for the next generation of aircraft that are lighter, stronger, and more efficient.
Automotive Manufacturing
In the automotive sector, friction stir additive manufacturing plays a transformative role in producing components that meet the demands of performance and sustainability. As vehicles become increasingly complex, manufacturers seek methods that allow for design flexibility.
Using this technique, manufacturers can create intricate geometries with enhanced mechanical strength. Notably, the process allows the blending of different metals, such as aluminum and magnesium, which expands design possibilities.
Advantages include:
- Integration of parts that reduces assembly time.
- Enhanced durability and crashworthiness.
- Lower overall weight of vehicles, contributing to fuel efficiency.
Additionally, the environmental aspects are noteworthy. Automotive companies can minimize material waste during production, which is a growing need as sustainability becomes a central focus in the industry.
Medical Device Development
The medical device industry benefits substantially from the adoption of friction stir additive manufacturing. This sector demands precision and reliability, crucial for devices that directly affect patient outcomes. The ability to produce customized implants and devices is a significant advantage.
Friction stir processes allow for the crafting of complex shapes that can be tailored to individual considerations, such as anatomy and specific procedural requirements. This customization leads to devices that fit better and function more effectively.
Key benefits encompass:
- Reduced manufacturing time.
- Improved material properties which enhance biocompatibility.
- Capability to produce structures with complex microgeometries, which can facilitate biological integration.
The consequences of these advancements are profound. Enhanced implant performance directly correlates to improved patient recovery times and overall satisfaction with medical interventions.
Advantages of Friction Stir Additive Manufacturing
Friction stir additive manufacturing (FSAM) is an innovative approach that combines the principles of traditional friction stir welding with additive manufacturing techniques. This hybrid process offers unique advantages that might prove beneficial for a variety of industries. As global manufacturing trends shift towards more sustainable and efficient methods, FSAM presents an array of benefits worth considering.
Sustainability Factors
Sustainability is a critical concern in todayโs manufacturing environments. Friction stir additive manufacturing enhances sustainability significantly. The process generates less waste compared to traditional subtractive methods. This is because FSAM adds material layer by layer, using only the necessary quantities to build the desired component.
- Energy Efficiency: FSAM requires less energy than conventional processes. The methodโs utilization of heat input reduces electrical consumption during production.
- Material Utilization: Different materials can be used for less volume. Materials like aluminum and titanium can be effectively implemented, promoting recycling.
- Lower Emissions: With reduced energy needs and waste, the carbon footprint diminishes. This contributes to a more eco-friendly approach in manufacturing.
"Friction stir additive manufacturing transforms how materials are used, promoting a remarkable reduction in environmental impact."
Cost Efficiency and Waste Reduction
Cost is an indispensable factor for manufacturers. Friction stir additive manufacturing can lead to considerable reductions in production costs. The mechanics of the process inherently limit waste, allowing organizations to maximize their resource efficiency.
- Reduced Material Costs: By layering materials instead of cutting them away, manufacturers save substantial amounts of raw material.
- Shorter Production Times: FSAM can cut down on lead times significantly. The expedient nature of the additive process accelerates production cycles, enabling quicker turnarounds and increased output.
- Lower Labor Costs: As automation and improved techniques take effect in FSAM, the reliance on manual labor decreases, driving down associated costs.
- Long-term Savings: While initial investments in FSAM technology might be higher, the long-term savings from decreased material waste and lower energy consumption will likely offset these costs.
In summary, the advantages of friction stir additive manufacturing extend from improved sustainability efforts to significant cost efficiencies. These benefits indicate a promising future for its adoption in various sectors, making it a crucial area to explore in modern manufacturing.
Challenges and Limitations
Understanding the challenges and limitations of friction stir additive manufacturing (FSAM) is crucial for assessing its viability and future prospects. While FSAM offers various advantages, such as reduced waste and enhanced material properties, it is not without complications that can hinder implementation. The landscape of this technology is shaped by multiple factors that must be navigated carefully.
Technical Hurdles
One of the primary technical hurdles in FSAM involves process optimization. The parameters for friction stir welding, while known, do not directly transfer to additive methods. For example, the rotation speed, stirring depth, and travel speed can significantly affect the quality of the final product. Optimizing these parameters requires extensive experimentation and a thorough understanding of the material being processed.
Additionally, maintaining thermal control during the process is critical. Elevated temperatures can facilitate bonding but also cause material degradation. Thus, the challenge lies in balancing the temperature to achieve ideal conditions without compromising material integrity.
Machine flexibility is another technical consideration. Not all current machines used for friction stir welding are capable of performing FSAM. Upgrades or entirely new machines may often be necessary, introducing additional costs.
Moreover, the scalability of FSAM poses a challenge. While small to medium-scale production may be feasible, large-scale manufacturing may face difficulties in achieving consistent quality across different batches. The integration of this technology into existing production lines can also present logistical complications.
Material Limitations
Material limitations present another formidable challenge in FSAM. Not all materials are suitable for additive manufacturing through this technique. For instance, certain alloys do not flow properly when subjected to friction stir processing. This results in inadequate bonding or suboptimal mechanical properties in the final product.
Another aspect related to materials is the issue of heterogeneity. The microstructure of materials can vary with processing conditions. Variations in grain size and phase distribution may create inconsistencies in mechanical properties. For instance, while some materials may exhibit better ductility when processed via friction stir, others can become brittle.
Limited understanding of new materials is a barrier as well. The field of materials science is continually evolving, but many innovations have yet to be fully tested under FSAM conditions. For example, advanced composites and novel alloys may require specific processing strategies that are still under investigation.
"The evolution of materials intended for FSAM could significantly enhance its applicability, but current limitations need addressing first."
Integrating these considerations into the production process is essential in developing robust and reliable outputs. Addressing both technical hurdles and materials limitations is vital for harnessing the full potential of friction stir additive manufacturing.
Future Trends in Friction Stir Additive Manufacturing
The landscape of friction stir additive manufacturing is evolving rapidly. As industries seek more efficient and sustainable production methods, understanding these future trends becomes crucial. This section will explore emerging technologies and cutting-edge research developments that can shape the future of this domain. By examining these elements, we can gain insights into the benefits and considerations that will influence the adoption of friction stir additive manufacturing.
Emerging Technologies
Advancements in technology are fundamental to the evolution of friction stir additive manufacturing. Several key areas are poised for significant growth:
- Automation and Robotics: Integrating robotics into the manufacturing process can enhance precision and efficiency. Automated systems can perform repetitive tasks with high accuracy, reducing the margin for error.
- Machine Learning and AI: The incorporation of machine learning algorithms helps in optimizing operational parameters. By analyzing large datasets, AI can provide insights that improve process control and enhance material properties.
- Hybrid Systems: Combining friction stir additive manufacturing with other technologies, such as laser processing, can yield superior materials and component properties. Hybrid systems allow for greater flexibility in design and manufacturing processes.
- Advanced Sensor Technologies: Real-time monitoring of manufacturing processes through advanced sensors facilitates quick feedback loops. This capability can ensure the integrity of produced parts and enhance overall quality control.
The significance of these technologies cannot be overstated. They not only streamline operations but also open avenues for innovation in product design and development.
Research Developments
Ongoing research is exploring several critical aspects of friction stir additive manufacturing:
- Material Development: Researchers are investigating new alloys and composite materials that can withstand the rigors of modern applications. This includes studies on shape memory alloys and high-strength composite materials, which may offer superior performance in demanding environments.
- Process Optimization: Innovative techniques such as multi-step friction stir processes may be on the horizon. These approaches aim to refine material properties and improve mechanical performance by regulating heat input and processing speed.
- Ecological Impact Studies: As sustainability becomes a focal point in manufacturing, research is increasingly attentive to the ecological consequences. Life cycle assessments and waste reduction strategies will continue to be pivotal in understanding the full impact of friction stir additive manufacturing.
- Collaborative Research Platforms: There is a growing movement towards collaborative research between industry and academia. This cooperation fosters knowledge sharing, speeding up the innovation cycle and promoting the practical application of new findings.
"The future of friction stir additive manufacturing will largely depend on the ability to integrate new technologies and innovative research into practical applications."
Comparative Analysis with Other Additive Manufacturing Processes
The exploration of friction stir additive manufacturing (FSAM) cannot be fully appreciated without examining its place within the broader spectrum of additive manufacturing processes. Understanding these general methods is crucial for identifying the advantages and limitations of FSAM. This analysis sheds light on key elements such as scalability, material versatility, and overall efficiency.
Fused Deposition Modeling
Fused Deposition Modeling (FDM) stands out among the most widely used additive manufacturing techniques. In this method, a thermoplastic filament is heated to its melting point and extruded layer by layer to create a three-dimensional structure. The process is relatively simple and cost-effective, making it a popular choice for prototyping and educational purposes.
Key characteristics of FDM include:
- Material Range: FDM can utilize a variety of thermoplastics such as PLA, ABS, and PETG. However, the material properties in terms of strength and heat resistance can be limiting compared to FSAM.
- Build Speed: FDM typically has slower build rates, particularly for complex geometries, which can affect throughput in production scenarios.
- Post-Processing Needs: Often, FDM parts require support structures that need to be removed after printing, which can add to the time and labor required for finalizing the product.
FDM is seen more suitable for applications where detail and precision are less critical. However, when structural integrity and mechanical properties are paramount, FSAM offers distinct advantages, utilizing solid-state joining mechanisms that enhance bonding strength.
Selective Laser Sintering
Selective Laser Sintering (SLS) employs a different principle, using a laser to fuse powdered material into a solid structure. This process allows for greater design complexities and fewer restrictions regarding shapes compared to FDM. SLS is favored in fields requiring highly durable and complex parts, particularly in aerospace and medical sectors.
Here are some salient points about SLS:
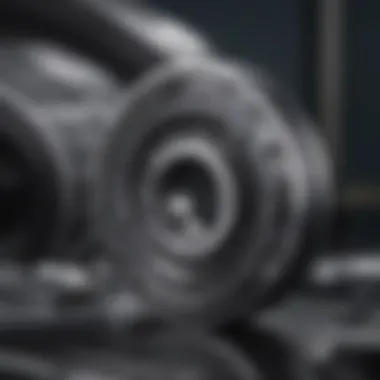
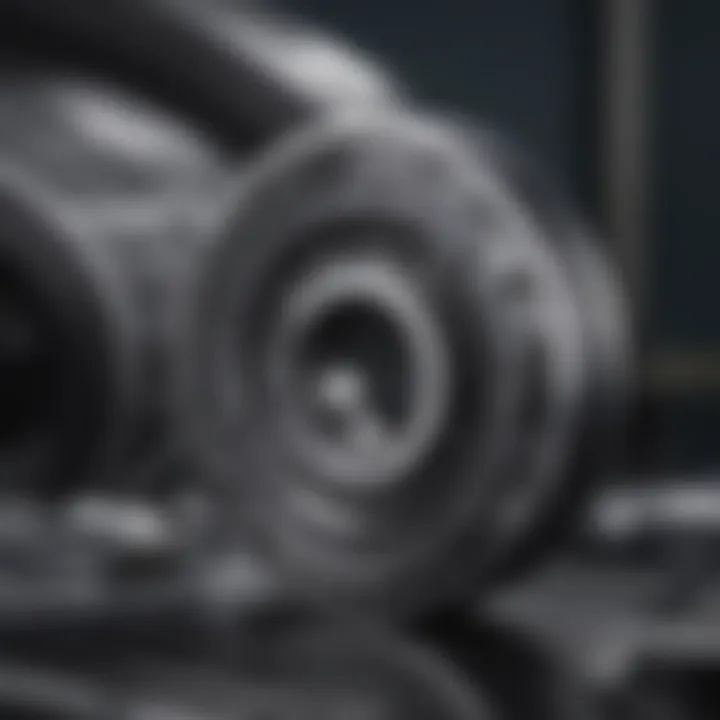
- Material Diversity: SLS supports a wide range of materials, including polymers, metals, and composites. This versatility surpasses what is typically feasible with FDM, but it often lacks the tailored finishing and structural properties provided by FSAM.
- Layer Adhesion: The thermal mechanisms used in SLS can lead to issues with anisotropic properties, meaning the strength of the final part can significantly differ depending on the orientation of its build.
- Production Speeds: Though SLS can have higher build speeds compared to FDM, the energy and time required to heat and cool the entire build chamber can limit the overall efficiency.
In summary, while FDM and SLS present substantial capabilities, friction stir additive manufacturing offers unique benefits through its solid-state process. The inherent characteristics of FSAM allow for superior mechanical properties and are increasingly recognized in specialized applications. The comparative analysis highlights the evolving landscape of additive manufacturing, encouraging exploration into how FSAM integrates and perhaps improves traditional and contemporary methodologies.
Case Studies: Successful Implementations
Case studies act as a lens through which the practical applications of friction stir additive manufacturing can be examined. They provide concrete examples that illustrate how this technology has been successfully implemented across various industries. These implementations showcase the versatility and efficiency of the method. They also highlight the real-world benefits and considerations that come with adopting such advanced manufacturing techniques.
Aerospace Component Manufacturing
In the aerospace sector, the demand for lightweight yet strong materials is critical. Friction stir additive manufacturing meets this need effectively by merging strength with reduced weight in components. For instance, Boeing has explored the potential of this technology for manufacturing structural components.
The advantages of using friction stir additive manufacturing here include:
- Enhanced Material Properties: The process leads to superior mechanical properties, such as increased fatigue resistance, which is essential for aerospace applications.
- Design Flexibility: Aerospace components can be designed in complex shapes, which are often not feasible with traditional methods.
- Reduced Waste: By adding material only where necessary, this method minimizes excess, lowering costs and environmental impact.
A specific project by NASA involved producing lightweight components for aircraft systems. The results demonstrated significant improvements in weight reduction while maintaining strength requirements. As a result, friction stir additive manufacturing has started to change the landscape of aerospace manufacturing.
Custom Medical Implants
In the medical field, the customization and precision of implants are crucial. Friction stir additive manufacturing allows for the production of bespoke implants that perfectly fit a patient's unique anatomy. This technique has been utilized in creating titanium-based implants for orthopedic surgery.
Key considerations include:
- Patient-Specific Solutions: Each implant can be tailored specifically to an individual's needs, improving outcomes and recovery times.
- Biocompatible Materials: The use of suitable materials ensures that there is minimal reaction from the body, promoting quicker healing.
- Complex Geometries: The ability to create intricate structures allows for better integration with natural bone, encouraging osseointegration, which enhances stability.
A notable case is the collaboration between medical device manufacturers and research institutions where friction stir additive manufacturing was used for creating intricate spinal implants. The results showed not only higher effectiveness but also reduced surgery times, benefiting both patients and healthcare providers.
"The practical examples of friction stir additive manufacturing demonstrate its potential to revolutionize production processes across various industries."
In summary, these case studies underline the significance of friction stir additive manufacturing, confirming its value in aerospace and medical fields. They show a clear trend towards innovation, sustainability, and efficiency, making a compelling case for further adoption in manufacturing.
Regulatory and Standards Considerations
The realm of Friction Stir Additive Manufacturing (FSAM) is not just defined by technological advancements; it also exists within a framework of regulatory and standardization necessities. These frameworks play a critical role in ensuring safety, quality, and overall effectiveness in manufacturing processes. When designing and implementing new manufacturing techniques, like FSAM, it is essential to understand how regulations interact with industry operations and outcomes. This section explores the main regulatory considerations, the importance of safety standards, and the protocols that govern quality assurance within this innovative domain.
Safety Standards
Safety standards are paramount in any manufacturing environment, particularly in one that employs advanced techniques such as FSAM. These standards are established by various organizations to protect workers, ensure proper equipment usage, and minimize risks of accidents during production.
Before implementing FSAM, manufacturers must consider the following key elements related to safety standards:
- Regulatory Compliance: Adhering to established regulations like OSHA (Occupational Safety and Health Administration) guidelines. It ensures the workplace is free from serious recognized hazards.
- Material Safety Data Sheets (MSDS): Essential for understanding the materials used within FSAM processes and their potential hazards.
- Equipment Standards: The machinery used in FSAM must adhere to specific safety protocols to prevent malfunctions and injuries. This includes regular maintenance and inspections to ensure operational integrity.
- Training Programs: Comprehensive training for workers on safety procedures and proper equipment handling is crucial. This facilitates a culture of safety and responsibility.
By emphasizing safety standards, companies can reduce accident rates, enhance worker morale, and ensure a smoother workflow. The upholding of these standards is a cornerstone for successful FSAM applications.
Quality Assurance Protocols
Quality assurance (QA) is another significant aspect in the field of FSAM. It involves systematic processes designed to ascertain that the manufacturing outputs meet the desired standards consistently. Effective QA protocols ensure the reliability and safety of the final products.
Key aspects of quality assurance in FSAM include:
- Standards and Guidelines: Familiarity with ISO and ASME guidelines is vital for maintaining quality. These standards lay out the expectations for manufacturing processes and final product capabilities.
- Regular Testing and Inspections: Implementation of rigorous testing methods at various stages of production to verify quality and consistency. This can involve both non-destructive testing and other evaluation techniques.
- Feedback Loops: Establishing communication channels for continuous improvement. By gathering feedback from processes and products, manufacturers can promptly address issues and enhance quality.
- Documentation: Maintaining clear, extensive records of production processes, tests conducted, and inspections aids in ensuring traceability and accountability. This documentation can be vital for audits and regulatory compliance.
Incorporating these QA protocols not only enhances the quality of products produced using FSAM but also builds trust with clients and stakeholders.
In summary, maintaining high standards in safety and quality assurance is essential in the evolving landscape of Friction Stir Additive Manufacturing. These elements foster confidence in technology while promoting responsible manufacturing practices.
Economic Implications
In the realm of friction stir additive manufacturing, understanding the economic implications is crucial. This insight provides a larger context for its adoption in various industries. The integration of friction stir processes with additive techniques represents not only a technological advancement but also a paradigm shift in economic structuring for manufacturing.
Market Trends
Market trends indicate a growing acceptance of friction stir additive manufacturing across diverse sectors. This acceptance is driven by several factors. Firstly, the demand for lightweight and high-strength materials is surging in industries such as aerospace and automotive. These sectors are focusing on innovative manufacturing techniques to enhance performance while reducing weight. This ties into the broader trend of sustainability, where industries seek to minimize ecological footprints and optimize resource use.
The continuous evolution of technology also plays a vital role in shaping market trends. As friction stir techniques become more refined, their efficiency increases. This efficiency enhances competitiveness among manufacturers, resulting in a shift towards more advanced production methods. Moreover, the parallel advancement of automation and digitalization complements friction stir additive manufacturing. Automated systems can improve precision and speed, leading to lower operational costs over time.
Friction stir additive manufacturing stands at the intersection of technological evolution and sustainable practices, illustrating a vital trend in modern manufacturing.
Investment Opportunities
Investment opportunities in friction stir additive manufacturing are expanding. As awareness grows, so does funding for research and development. Investors see the potential for significant returns as this technology matures. Companies that incorporate friction stir techniques can benefit from operational efficiencies, which can translate to cost savings.
The potential for new applications in various fields generates further investor interest. For instance, customized solutions in medical implants can create niche markets with limited competition. Additionally, as regulatory frameworks evolve, ensuring compliance with industry standards presents opportunities for companies focused on quality assurance and reliability in their products.
Investors are also urged to consider partnerships with research institutions. These collaborations can accelerate advancements in materials science and process optimization, maximizing the value derived from investments.
Environmental Impact Assessment
Understanding the environmental impact of production methods is critical for modern manufacturing processes, especially in the context of friction stir additive manufacturing (FSAM). This section explores the significance of conducting an environmental impact assessment (EIA) and the underlying components that contribute to sustainable manufacturing practices.
An EIA serves as an essential tool in evaluating the potential environmental effects associated with the production techniques utilized. For FSAM, applying such an assessment aids in identifying resource consumption, waste generation, and emissions resulting from the process. The importance of such analyses cannot be overstated, especially as industries face increasing scrutiny regarding their environmental footprints.
Life Cycle Analysis
Life Cycle Analysis (LCA) is a pivotal component of the EIA, providing a comprehensive perspective on the environmental impact of various processes from cradle to grave. In relation to FSAM, LCA encompasses stages such as raw material extraction, manufacturing, use, and end-of-life disposal. By analyzing each phase, manufacturers can identify areas for improvement and focus on reducing negative environmental impacts.
Key points of LCA in FSAM include:
- Resource Utilization: Assessing raw material usage helps in selecting materials that minimize energy consumption.
- Energy Consumption: Understanding the energy demands during each stage can guide efforts to use renewable resources.
- Waste Management: Evaluating waste during production aids in developing recycling and reuse strategies.
- Emissions Analysis: Monitoring greenhouse gas emissions produces data essential for compliance with regulations.
Through LCA, stakeholders can make informed decisions that advance sustainable practices in manufacturing while maintaining efficiency and productivity.
Sustainable Practices in Manufacturing
Sustainable practices in friction stir additive manufacturing contribute significantly to minimizing environmental impacts. Several approaches are being integrated into FSAM processes to promote sustainability effectively.
Some sustainable practices include:
- Material Selection: Choosing recyclable and less harmful materials influences the sustainability of the final product.
- Energy Efficiency: Implementing energy-efficient machines and techniques helps in lowering the overall energy consumption.
- Process Optimization: Streamlining operations to reduce cycle times and steps can enhance output while decreasing waste.
- Closed-loop Systems: Adopting closed-loop systems for material reuse reduces the need for virgin materials and minimizes waste.
By prioritizing these practices, manufacturers can not only decrease their environmental impact but also improve their market competitiveness.
"Engaging in environmental impact assessments, particularly through life cycle analyses, is crucial for understanding and improving the sustainability of friction stir additive manufacturing processes."
As this field evolves, ongoing research will be essential. The integration of innovative technologies and sustainable practices will pave the way for a more environmentally responsible manufacturing landscape.
Ethical Considerations in Manufacturing
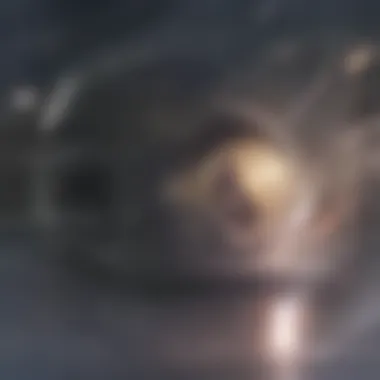
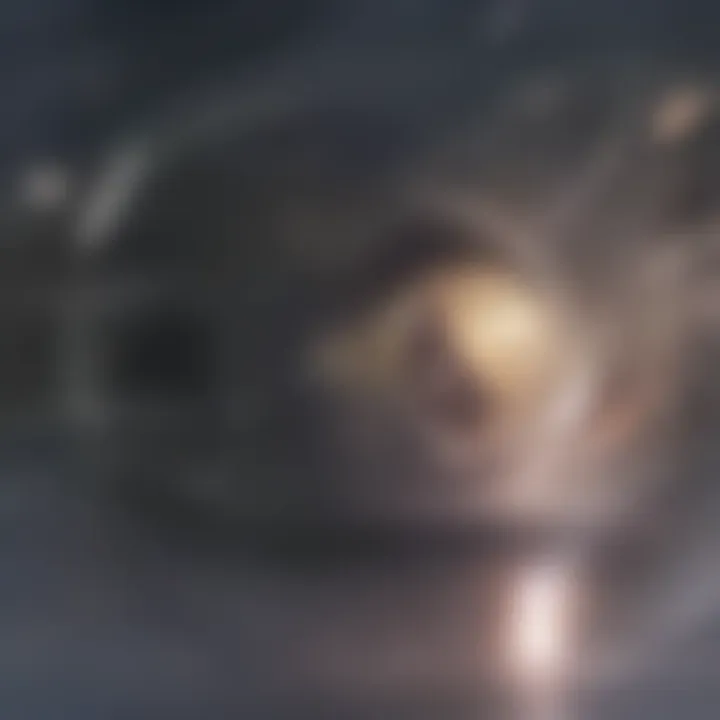
In the domain of friction stir additive manufacturing, ethical considerations are paramount. They encompass a range of subjects including sourcing of materials, labor practices, environmental impact, and the implications of automation. As the industry evolves, questions regarding the responsibility of manufacturers grow increasingly complex. Each decision made in production not only affects economic aspects but also social and environmental landscapes. This section will explore these elements, emphasizing the significance of ethical practices in modern manufacturing.
Responsibility in Production
Responsibility in production goes beyond just creating effective products. It involves recognizing the entire supply chain and the implications of sourcing materials. Manufacturers must understand where materials come from and assess their environmental and social impact. For instance, utilizing recycled materials can reduce environmental footprints, whereas mining for raw materials may lead to ecological harm and social displacement.
Moreover, manufacturers have an ethical duty to ensure fair labor practices. This means providing safe working conditions, fair wages, and job security for all employees involved in the manufacturing process. The integration of friction stir additive manufacturing technology can create new job opportunities while raising the standard of working environments. By prioritizing ethical labor practices, companies contribute to social sustainability.
"Manufacturers must not only focus on profit but also consider the welfare of communities and the environment."
Implications of Automation
Automation brings numerous advantages such as increased efficiency and reduced costs. However, it also raises significant ethical concerns. The potential displacement of workers by automated systems poses a moral dilemma for corporations. Job losses can impact individuals and families, creating socioeconomic challenges.
Friction stir additive manufacturing has the potential to mitigate some of these effects by creating new types of jobs that require different skills, especially in programming and maintenance of automated systems. Companies must address the transition by investing in training and education for their workforce. This approach enhances both productivity and workforce satisfaction, helping employees adapt to new roles.
Another consideration is the impact of automation on product quality and safety. Automated processes must be rigorously monitored to ensure they meet necessary standards. Ensuring compliance with safety regulations is crucial, as failure to do so can lead to both safety incidents and legal ramifications, ultimately affecting consumer trust.
In summary, ethical considerations in friction stir additive manufacturing encompass a wide array of responsibilities. By prioritizing ethical sourcing, labor practices, and addressing implications of automation, manufacturers can create a more sustainable and equitable industry.
Technical Innovations and Research
Technical innovations and research play a crucial role in the evolution of friction stir additive manufacturing. As this field grows, understanding new developments helps to drive efficiency, improve material use, and broaden the potential applications for the technology. Innovations in equipment and novel materials contribute significantly to the viability of innovations while satisfying stringent quality and performance standards.
Advancements in Equipment
The equipment used in friction stir additive manufacturing has seen remarkable advancements over recent years. These improvements have been driven by the demand for more efficient production processes, higher quality outputs, and reduced operational costs. The integration of automation in equipment has greatly enhanced the precision and reliability of the manufacturing processes.
For instance, the development of CNC (Computer Numerical Control) systems has allowed for highly customizable and repeatable processes. This enables manufacturers to create complex geometries that were previously difficult or impossible to achieve.
Additionally, specialized tooling designed for specific materials and applications has emerged. This tooling not only maximizes material utilization but also enhances the overall performance and durability of the manufactured components. The use of real-time monitoring systems in the equipment further optimizes the process, allowing for immediate adjustments to be made based on feedback, thus minimizing defects and waste.
Novel Materials Development
Another critical aspect of technical innovations in friction stir additive manufacturing is the development of novel materials. Research in this area focuses on creating composite materials that enhance the properties of traditional metals.
Materials like Aluminium-Lithium alloys and Titanium-based composites are gaining traction due to their excellent mechanical properties and lightweight characteristics. These materials open up new avenues for applications, particularly in aerospace and automotive industries where weight reduction without compromising strength is essential.
"The advancement of materials in friction stir additive manufacturing not only influences performance but also dictates the feasibility of designs in modern engineering."
In addition, the exploration of multifunctional materials is becoming prominent. These materials can possess properties such as thermal conductivity, electrical conductivity, and corrosion resistance, all in a single component. These capabilities mean enhanced performance in applications spanning multiple industries.
Lastly, the incorporation of smart materials that can respond to environmental changes can transform manufacturing processes. These innovations allow for adaptive structures or systems that can automatically adjust to changing operational conditions.
In summary, technical innovations and research are integral to the advancement of friction stir additive manufacturing. The continuous evolution of equipment and exploration of novel materials significantly enhance the effectiveness and scope of this manufacturing technique.
Incorporating Industry Standards
The integration of industry standards in friction stir additive manufacturing is crucial for ensuring quality, safety, and interoperability across various applications. These standards guide manufacturers in creating consistent and reliable products that meet both regulatory requirements and market expectations. As the industry evolves, adhering to established standards can help businesses maintain a competitive edge and foster trust among stakeholders.
Industry standards address critical aspects such as material specifications, process parameters, and testing methodologies. By following these guidelines, companies can streamline operations, reduce errors, and facilitate smoother communication with clients and partners. Most importantly, incorporating standards can enhance the reproducibility of components, which is central to achieving high precision in manufacturing.
ISO and ASME Guidelines
The International Organization for Standardization (ISO) and the American Society of Mechanical Engineers (ASME) provide important frameworks for quality assurance in manufacturing processes. ISO standards focus on various aspects, including quality management, environmental management, and safety protocols. For instance, the ISO 9001 standard emphasizes the importance of quality management systems in organizations, ensuring that products meet customer and regulatory requirements consistently.
Similarly, ASME standards are pivotal when it comes to mechanical and structural components, offering valuable insights into design and manufacturing processes. Compliance with ASME standards assures that components can withstand the rigorous conditions they may encounter in real-world applications. These guidelines are particularly relevant in industries like aerospace and automotive, where safety and performance are non-negotiable.
By adhering to ISO and ASME guidelines, manufacturers can not only enhance the quality of their products but also open avenues for collaboration with international partners. Moreover, these standards assist in reducing the risk of product failure and increase customers' confidence in the services and products provided.
Best Practices in Implementation
Implementing industry standards effectively necessitates a systematic approach. Key best practices include:
- Training and Development: Ensuring employees understand the standards relevant to their roles is vital. Regular training sessions can help maintain high standards of practice and awareness.
- Quality Control Protocols: Establishing strict quality control measures can ensure that each produced item adheres to industry standards. This might involve regular audits, inspections, and certifications.
- Documentation and Record Keeping: Keeping detailed records of processes and compliance with standards allows for easy examination and demonstrates commitment to quality. This documentation can be beneficial in case of audits or inspections.
- Continuous Improvement: Industry standards evolve, and so should manufacturing practices. Encouraging a culture of continuous improvement helps organizations stay ahead in implementing the latest standards and maintaining high-quality outputs.
In summary, incorporating industry standards such as ISO and ASME guidelines into friction stir additive manufacturing is not just a regulatory necessity but a strategic advantage. Best practices in implementation ensure consistency and quality, paving the way for sustainable practices and fostering innovation in manufacturing.
"Standards are the foundation of an effective manufacturing system that ensures safety, quality, and efficiency."
Interdisciplinary Approaches to Friction Stir Additive Manufacturing
Interdisciplinary approaches are crucial in expanding the horizons of friction stir additive manufacturing. This field merges knowledge from mechanical engineering, materials science, robotics, and computer-aided design (CAD). By integrating various disciplines, practitioners can develop more efficient processes and innovative solutions to existing challenges.
Collaboration among specialists allows for comprehensive exploration of how different elements interplay within friction stir additive manufacturing. Engineers can apply traditional principles of friction stir welding to innovative additive techniques, thus creating a unique synergy of methodologies. This integrative strategy not only enhances manufacturing capabilities but also fosters a more sustainable production environment. This is significant as industries face increasing pressure to reduce waste and environmental impact.
Each discipline contributes its perspective, whether itโs materialsโ properties, design nuances, or applications in various contexts. Studies and practical applications from different fields can provide insightful methodologies that enhance overall effectiveness. For example, insights from material scientists regarding thermal behaviors can inform engineers while they design components. Similarly, input from roboticists can enhance automation processes, streamlining production cycles.
Collaboration Between Disciplines
The act of collaboration between disciplines is a cornerstone of advancing friction stir additive manufacturing. As different experts work together, they can share knowledge and techniques that amplify innovation.
- Engineering and Materials Science: Engineers benefit from understanding the crystalline structure and mechanical properties of various materials. This allows for better decision-making concerning material selections and processing parameters.
- Robotics and Automation: Automation specialists can offer valuable insights into how to optimize production lines. Automated systems can help maintain quality and increase consistency, which are essential in demanding industries like aerospace and medical.
- Computer Simulations and Modeling: Collaboration with computer scientists can enhance simulation accuracy. Using predictive modeling can reduce trial-and-error in the design process, saving time and resources.
Collaborative projects between universities and industries have shown promising results. Research initiatives that draw from multiple disciplines create a fertile ground for groundbreaking advancements. These integrations not only pave the way for innovative designs but also address engineering challenges more effectively.
Impact on Engineering Education
The incorporation of interdisciplinary approaches affects engineering education significantly. As industries evolve, educational institutions must adapt their curricula to include concepts from different fields relevant to friction stir additive manufacturing. Students who gain exposure to various disciplines are better equipped for future careers.
- Holistic Learning: Students learn to think critically across different domains. This holistic education enables them to navigate complex problems and derive effective solutions.
- Hands-On Projects: Implementing projects that require collaboration strengthens their teamwork skills. These projects can involve real-world applications, enhancing their capability to work in diverse teams.
- Research Opportunities: Encouraging students to partake in research that involves multiple areas of expertise fosters an environment of innovation.
The shift towards interdisciplinary education not only enhances students' knowledge but also prepares them for the collaborative nature of modern engineering practices. Graduates who understand both the technical requirements and the broader implications of their work will become valuable assets in the manufacturing industry.
"Collaboration across disciplines is not just beneficial; it is necessary for the evolution of friction stir additive manufacturing."
By recognizing and cultivating the interplay between disciplines, the industry can look forward to sustained innovations that will redefine manufacturing capabilities.
Finale and Future Perspectives
As the exploration of friction stir additive manufacturing comes to a close, it is essential to underscore the various implications this technology holds for the future of manufacturing. Friction stir additive manufacturing (FSAM) integrates the precision of friction stir welding with contemporary additive techniques. This synergy paves the way for enhanced production processes across multiple industries. The ability to optimize material properties while minimizing waste is a significant asset in todayโs environmentally-conscious landscape.
Moreover, FSAM contributes to cost efficiency both in terms of resource utilization and production timelines. This is particularly relevant as industries seek to balance quality with affordability. The ongoing advancements in this method will likely encourage broader adoption and innovation, leading to new applications previously unconsidered. Ensuring that manufacturers are equipped with the knowledge and resources to embrace these changes is imperative. It stands as a testament to how evolving manufacturing practices can redefine product development landscapes.
"The integration of traditional and modern manufacturing methods creates a fertile ground for innovation."
Summary of Key Findings
The analysis revealed several critical findings regarding friction stir additive manufacturing:
- Material Versatility: FSAM allows a diverse range of materials to be used, including metals and polymers.
- Sustainability: The technology substantially reduces material waste compared to other manufacturing methods. This aligns well with increased regulatory pressures around environmental impacts.
- Economic Efficiency: By reducing production time and resources, FSAM presents a competitive advantage in various sectors, particularly in aerospace and automotive.
- Compatibility with Existing Technologies: FSAM can be integrated with current production techniques, facilitating smoother transitions for manufacturers.
Call for Further Research
While the accomplishments in friction stir additive manufacturing are notable, there remain several areas ripe for further exploration. Investigating the nuances of this manufacturing process can yield significant benefits. Key areas for study include:
- Material Science Innovations: More in-depth research into new materials suited for FSAM could greatly enhance its applications.
- Process Optimization: Understanding the specific parameters that affect the quality and integrity of the final products is crucial.
- Automation Integration: Exploring how automation can streamline FSAM processes will be essential to keep pace with industry needs.
- Market Acceptance: Research on how FSAM can penetrate various markets will help shape its adoption strategies.