Exploring Mechanical Pressure Sensors: Principles and Uses

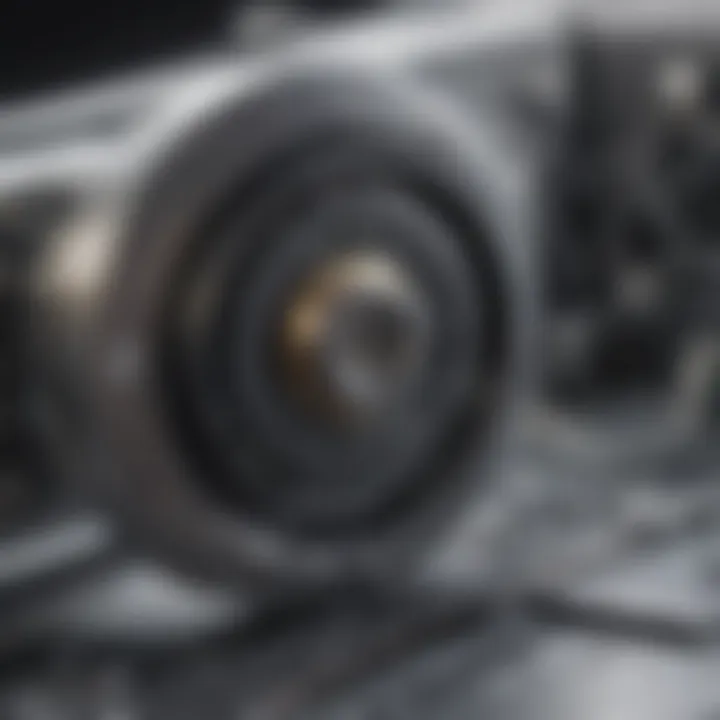
Intro
Mechanical pressure sensors play an essential role in measuring and regulating pressure across various sectors. Their functionality is not just a technicality; itβs an integral part of how systems operate efficiently and safely. These sensors harness the principles of mechanics to convert physical pressure into readable electrical signals. This conversion allows for precise monitoring and control necessary in numerous applications, from automotive to industrial machinery.
In this article, we delve into the nuts and bolts of mechanical pressure sensors, examining their core principles, practical applications, and the innovations driving their evolution. We aim to provide readers with a thorough understanding, making it relevant for students, researchers, educators, and professionals who deal with sensor technology on a daily basis.
Recent Advances
As industries evolve, so too does the technology behind mechanical pressure sensors. Recent advancements mark significant progress in terms of efficiency, accuracy, and functionality.
Latest Discoveries
Recent research has pinpointed new materials that improve sensor durability and responsiveness. For instance, the introduction of piezoresistive materials allows for greater sensitivity and stability in environments with fluctuating temperatures. Moreover, scientists are exploring nanotechnology to enhance the sensory effects further, creating more compact and lightweight designs.
Technological Innovations
Innovations in mechanical pressure sensors extend beyond materials. Smart sensors equipped with IoT capabilities are becoming standard. This integration facilitates real-time data transfer and monitoring, enhancing decision-making processes in real-time. Additionally, advancements in calibration techniques have improved accuracy and reliability, leading to a decrease in error rates.
"Understanding the advances in sensor technology is crucial for developing more efficient systems in a technology-driven world."
Methodology
To provide a comprehensive view of mechanical pressure sensors, a structured methodology was employed in gathering relevant information. Understanding the principles and innovations involves examining both theoretical frameworks and practical applications.
Research Design
By analyzing a variety of sources, which include academic journals, industry reports, and case studies, this article combines quantitative and qualitative insights. Each source is critical in painting a complete picture of mechanical pressure sensor technology.
Data Collection Techniques
Key techniques in data collection involve surveys conducted with industry professionals, interviews with engineers, and direct observations in industrial setups. These methods enable a well-rounded exploration of current practices and future trends, ensuring that the information is both reflective and anticipatory of where the field is heading.
Preface to Mechanical Pressure Sensors
The realm of mechanical pressure sensors stands as a cornerstone in numerous engineering disciplines and industrial applications. These sensors act as the vigilant watchdogs of our modern world, providing crucial data that informs decision-making processes across various settings. Understanding their importance is essential, not just for those working directly with them but also for students, researchers, and professionals who rely on accurate pressure measurements in their fields.
Mechanical pressure sensors convert physical pressure into an electronic signal, enabling real-time monitoring and control of systems. They are instrumental in processes such as manufacturing, healthcare, and environmental observations, where precise pressure readings can make or break the success of an operation. With the rise of smart technology, the role of these sensors has further expanded.
When delving into the core principles of these devices, we assure ourselves their effectiveness hinges on their design and operational parameters. However, despite their crucial role, many professionals may overlook important factors, such as calibration techniques and performance metrics, which can drastically affect data accuracy.
In this section, we break down the basic definition and concept underlying mechanical pressure sensors as well as trace their historical evolution. This will provide a framework that frames our subsequent discussions around the principles, types, and real-world applications of these devices. Moreover, such insights pave a pathway to understand contemporary challenges and future trends that continue to shape sensor technology.
"A sensor is only as good as its calibration; take it lightly, and your results can be all over the map."
Definition and Concept
Mechanical pressure sensors are devices that measure the force exerted by a fluid or gas within a given space. The central concept revolves around the detection of pressure changes, which are then converted into quantifiable electrical signals.
These sensors come in a variety of designs, each serving unique purposes based on the specific environments and types of pressure they are designed to measure. For example, Strain Gauge sensors operate on the principle of resistance changes due to deformation when pressure is applied, while capacitive sensors measure pressure through changes in capacitance based on the physical properties of a diaphragm under stress.
As such, understanding the basic working principles and functions of these sensors not only helps in selecting the right type for a specific application but also aids in troubleshooting and enhancing device performance later down the line.
Historical Evolution
The journey of mechanical pressure sensors can be traced back to the early days of industrialization, when the need emerged for more accurate measurements in steam engines and other pressure-dependent machinery. Early pressure measurement relied heavily on liquid column methods, such as manometers, where mercury levels indicated pressure changes. These methods, although effective, posed safety and accuracy issues.
As technology adapted and advanced, the introduction of mechanical sensors, such as Bourdon tubes, revolutionized the industry in the 19th century. These tubes convert mechanical movement into readable measurements, paving the way for more sophisticated sensor designs. Over time, the integration of electronic components allowed for data to be logged and analyzed in real-time, thus enhancing the functionality and reliability of pressure measurements.
Today, mechanical pressure sensors have evolved into complex systems with integrated features that provide not just measurement, but also data processing and communication abilities. Their development reflects a continuous push towards precision, robustness, and versatility to tackle the ever-changing demands of modern technology.
Principles of Operation
Understanding the principles of operation for mechanical pressure sensors is crucial. It lays the foundation for comprehending how these devices function, their accuracy, and overall effectiveness in various applications. By grasping the basic mechanisms at work, one can appreciate the nuances that may influence measurements in real-world scenarios.
Basic Working Mechanism
The basic working mechanism of mechanical pressure sensors primarily revolves around how they convert pressure into a quantifiable electrical signal. Most of these sensors depend on a mechanical element that transforms pressure changes into displacement.
When pressure is applied, it stretches or compresses the sensing element, often a diaphragm. This deformation is then translated into an electrical signal by the transducer. Essentially, the transformation from a physical force to an electrical signal is what allows for pressure readings to be monitored and analyzed.
This transformation requires a careful design that ensures high sensitivity and accuracy. For instance, as the pressure varying over time, the diaphragm's response also varies, which directly influences the readings. Therefore, understanding how these movements translate to data is vital for accurate pressure measurement.
Key Components
A mechanical pressure sensor comprises several key components that work in coordination to achieve accurate readings. Here, we discuss three essential parts: the diaphragm, the transducer, and the signal processing unit.
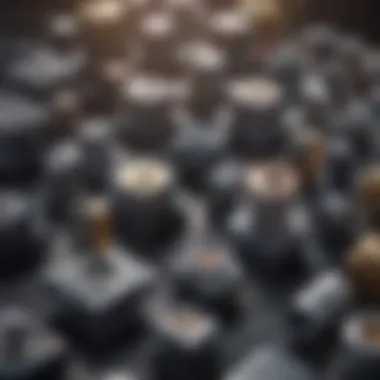
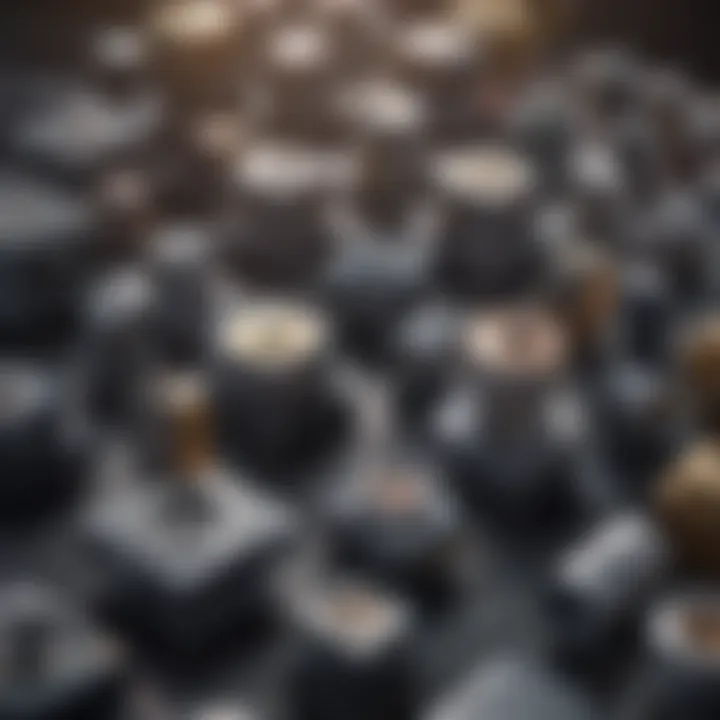
Diaphragm
In the realm of pressure measurement, the diaphragm serves as a critical component. It acts as the first point of interaction with the pressure being measured. Typically made from a flexible material, the diaphragm can easily displace under pressure.
Key Characteristic: The sensitivity of the diaphragm to small pressure changes is what makes it a popular choice in mechanical pressure sensors. This characteristic allows it to detect minute shifts, making the readings reliable.
Unique Feature: The unique aspect of a diaphragm lies in its ability to be designed for various pressure ranges. From low pressures in medical devices to high pressures in industrial applications, diaphragms can be tailored accordingly.
Advantages: Its flexibility results in relatively low hysteresis, ensuring that the readings are consistent even when the pressure fluctuates over time. However, a disadvantage could be its susceptibility to wear and tear, especially in harsh environments.
Transducer
The transducer is the component responsible for converting the mechanical movement caused by pressure on the diaphragm into an electrical signal. It amplifies the slight changes in resistance or capacitance produced by the diaphragm's deformation.
Key Characteristic: The transducer's ability to provide precise and quick responses to pressure variations makes it essential within the system.
Unique Feature: Many transducers used today are piezoelectric, allowing for the generation of electronic signals from mechanical stress. This attribute is particularly beneficial in high-frequency applications.
Advantages: Its responsiveness allows for real-time monitoring of pressure changes. However, they can be costly and may require careful calibration to maintain accuracy.
Signal Processing Unit
Lastly, the signal processing unit plays a pivotal role in this operation. This component takes the raw signals from the transducer and processes them to produce readable output.
Key Characteristic: The ability of the signal processing unit to filter, amplify, and convert signals ensures higher quality data is available for analysis.
Unique Feature: Many advanced units incorporate digital processing capabilities, allowing for better accuracy and the ability to interface seamlessly with other devices for data logging or remote monitoring.
Advantages: Its integration capabilities make it versatile across a range of applications, but it can also introduce complexity in terms of requirements for power supply and potential system failures.
In summary, each component of a mechanical pressure sensor plays its part in delivering accurate and reliable measurements. Understanding these principles aids in recognizing how pressure sensors can be optimized and applied across various sectors.
Types of Mechanical Pressure Sensors
Understanding the different types of mechanical pressure sensors is crucial for anyone working in engineering and technology fields. Each type offers unique characteristics, advantages, and limitations that can significantly affect its application in various industries. The choice of sensor often hinges on the specific requirements of the project, such as sensitivity, response time, and environmental conditions. This section explores three primary types of mechanical pressure sensors: Strain Gauge Sensors, Capacitive Pressure Sensors, and Optical and MEMS Sensors.
Strain Gauge Sensors
Strain gauge sensors are among the most widely used mechanical pressure sensors due to their versatility and accuracy. Their operation is based on the principle of resistance change when the sensor undergoes deformation. When pressure is applied, the strain gauge stretches or compresses, leading to a shift in electrical resistance, which can then be measured and translated into a pressure reading.
The advantages of strain gauges include:
- High sensitivity and accuracy: They can detect minute pressure changes, making them ideal for precision applications.
- Wide range of pressure measurements: They can measure both very low and very high pressures, which is essential in various industrial contexts.
- Cost-effectiveness: Strain gauges are relatively inexpensive to produce, making them accessible for many applications.
However, they do have some downsides. Their performance can be affected by temperature variations, which may introduce errors in measurements. Additionally, they require careful setup and calibration to ensure accurate results, making them somewhat less user-friendly for those unfamiliar with the technology.
Capacitive Pressure Sensors
Capacitive pressure sensors are another significant type used in various applications. These sensors operate based on the change in capacitance between two conductive plates separated by a dielectric material. When pressure is applied, the distance between the plates changes, leading to a variation in capacitance, which can be quantified.
Among the benefits of capacitive sensors are:
- Excellent accuracy and stability: Due to their non-contact nature, they are less sensitive to environmental factors and offer high-resolution measurements.
- Small size: Their compact design makes them suitable for applications where space is an issue.
- Resistance to contamination: Capacitive sensors are less likely to be affected by dirt, moisture, or other environmental contaminants compared to other types.
Nevertheless, they come with limitations as well. Capacitive sensors tend to have a more limited pressure range than strain gauges, and their performance may degrade over time if exposed to extreme conditions for prolonged periods. Moreover, they can be more expensive because of their complex design and manufacturing processes.
Optical and MEMS Sensors
Optical and MEMS (Micro-Electro-Mechanical Systems) sensors represent the cutting edge of pressure sensing technology. Optical sensors utilize light signals to measure pressure changes, typically through shifts in wavelength or intensity caused by pressure-induced strain. MEMS sensors, on the other hand, integrate mechanical and electrical components at a microscale, enabling highly precise measurements in a compact form factor.
The key advantages of these sensors include:
- High precision and miniaturization: They are capable of delivering extremely sensitive measurements while taking up minimal space.
- Multifunctionality: Many MEMS sensors can measure pressure, temperature, and even acceleration, making them versatile for various applications.
- Integration with digital systems: Their compatibility with modern electronic devices enables seamless integration into complex systems, particularly useful in industries like automotive and consumer electronics.
However, optical and MEMS sensors can have considerable drawbacks, generally related to their cost and fragility. They are often more expensive than traditional mechanical sensors and may require specialized handling or installation, making them less accessible for some projects. Their complex design can also lead to challenges in terms of maintenance and repairs.
In summary, each type of mechanical pressure sensorβstrain gauge, capacitive, and optical/MEMSβcomes with its unique set of benefits and challenges. The decision on which sensor to utilize in a given application must account for several factors, including cost, required precision, and operating environment. Ultimately, a deeper understanding of these types will guide professionals in selecting the appropriate technology for their specific needs.
Calibration Techniques
Calibration of mechanical pressure sensors plays a crucial role in ensuring their accuracy and reliability. It can be viewed as a quality checkpoint where sensors are fine-tuned to provide precise measurements under varying conditions. Without proper calibration, even the most advanced sensor can deliver misleading data. In various industrial applications, accurate pressure readings can influence everything from safety protocols to product quality. Thus, calibration techniques are not just technicalities; they are foundational processes that validate the integrity of data, thereby facilitating well-informed decisions.
Importance of Calibration
The significance of calibration cannot be overstated. In an age where data drives decisions, precision is paramount. Calibration directly influences:
- Accuracy: A calibrated sensor ensures that the measurements it reports align closely with actual values. This accuracy is vital for critical applications such as medical devices where incorrect pressure readings could have dire consequences.
- Consistency: Regular calibration maintains the performance of sensors over time, allowing for consistent data collection. This consistency is particularly important in long-term projects involving environmental monitoring or industrial manufacturing, where trends and patterns become essential.
- Compliance: Many industries are governed by strict regulations requiring products to meet certain performance standards. Proper calibration helps ensure that sensors comply with these laws, reducing legal liability and promoting safety.
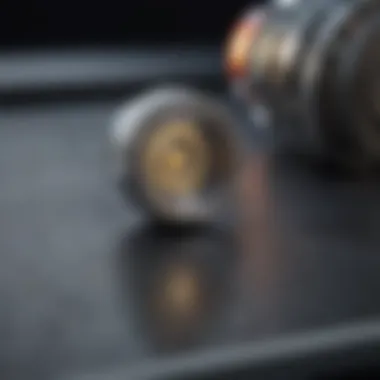
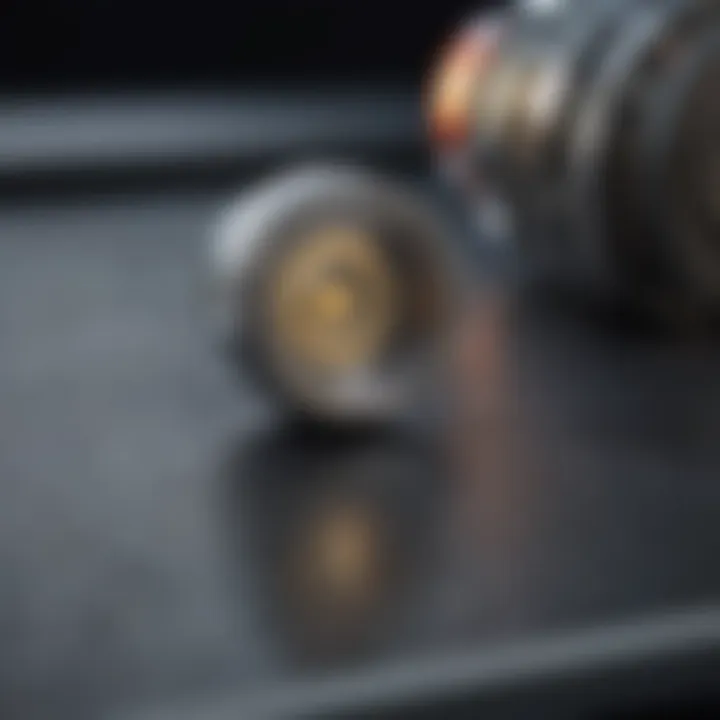
Calibration Methods
The methods of calibration can broadly be categorized into two types: static calibration and dynamic calibration. Each method has its unique application and brings specific benefits to different contexts.
Static Calibration
Static calibration is primarily concerned with measuring pressures in a steady state. It involves using controlled pressure sources to check the sensor readings against known values. The key characteristic of static calibration is its simplicity. Many industries favor this method because it can quickly verify the accuracy of sensors without the complexities introduced by changing conditions.
- Key Advantage: The process is straightforward; one can achieve high precision without needing sophisticated equipment.
- Disadvantage: On the flip side, static calibration doesnβt account for variations that might occur in real-time scenarios. This limitation makes it less suitable for applications where pressure changes rapidly, like in some automation processes.
Dynamic Calibration
Dynamic calibration, in contrast, involves assessing sensors during changing pressure conditions to account for their response over time. This technique might involve introducing rapid pressure variations and checking how the sensor responds.
- Key Advantage: One standout feature of dynamic calibration is its capacity to reveal hysteresis or lag in sensor responses. This can be particularly useful for applications with fluctuating pressures, like in aerospace testing or automotive systems.
- Disadvantage: However, dynamic calibration often demands more sophisticated and costly equipment, making it more resource-intensive than static calibration.
"To calibrate a pressure sensor is to treat the sensor as a musical instrument. Each requires precise tuning to perform correctly in its environment."
In summation, both static and dynamic calibration techniques hold their own merits and demerits. Understanding the appropriate context for each can significantly enhance the accuracy and reliability of measurements in mechanical pressure sensors.
Performance Factors
Understanding performance factors is crucial when discussing mechanical pressure sensors. These elements directly influence how accurately and reliably a sensor performs its intended function. In an era where precision governs many industries, the need for high sensitivity and accurate readings cannot be overstated. Variations in these performance factors can have ripple effects across entire operations, highlighting the importance of meticulously considering them in both design and application stages.
Sensitivity and Accuracy
Sensitivity refers to the sensor's ability to detect minute changes in pressure and respond accordingly. A highly sensitive sensor can discern even the smallest fluctuations, which is vital in applications such as medical devices and scientific research. For instance, in a hospital setting, monitoring patientsβ blood pressure requires sensors that can accurately register even slight variations to ensure proper treatment decisions are made. Without this level of sensitivity, a sensor may fail to provide critical data, leading to possible misdiagnoses or delayed responses.
Accuracy, on the other hand, defines how close the sensor reading is to the actual pressure value. A sensor can be sensitive without being accurate; thus, both elements must be in harmony to produce reliable results. For example, a piezoresistive pressure sensor used in aerospace applications is expected to not only detect pressure changes but also provide data that measures those changes correctly. A fault in accuracy can result in catastrophic failures, proving that neither sensitivity nor accuracy can be treated lightly.
"In the world of pressure sensors, losing precision even by a fraction can lead to serious consequences. Every reading counts."
Temperature Effects
Temperature plays a significant role in the performance of mechanical pressure sensors. Various sensors have different thermal coefficients, meaning they respond differently to changes in temperature. Thermal expansion of materials used in the sensor, like metal diaphragms, can alter pressure readings if not properly managed. For instance, when deployed in environments with fluctuating temperatures, a capacitive pressure sensor could yield results that are skewed unless compensatory mechanisms are in place.
There are two main effects that temperature can have:
- Drift: Over time, varying temperatures can lead to drift in the sensorβs readings. For instance, a sensor calibrated at room temperature might show inaccuracies in extreme cold or heat.
- Material Properties: The mechanical properties of materials used in sensors can also shift with temperature. This shift could affect the elasticity of a diaphragm in a strain gauge sensor, leading to misinterpretation of pressure.
To combat these issues, industries often invest in advanced calibration techniques that account for temperature effects, ensuring that performance remains uncompromised despite environmental changes. Understanding and managing these factors can drastically enhance the reliability and longevity of mechanical pressure sensors across various applications.
Applications Across Industries
Mechanical pressure sensors have become indispensable tools in various sectors, playing a crucial role in the monitoring and regulation of processes. Their applications span across numerous industries, each utilizing these sensors in ways that enhance operational efficiency, ensure safety, and promote innovation. Understanding the significance of these applications aids in recognizing the broader impact of pressure sensors in contemporary engineering and technology.
For instance, in manufacturing, pressure sensors are integral for maintaining optimal pressure levels which can prevent equipment failure and enhance product quality. Moreover, in the realm of healthcare, these devices are pivotal for patient monitoring systems, ensuring precise readings which can result in better patient outcomes. Environmental monitoring, too, benefits from pressure sensors by enabling real-time data collection that supports sustainability initiatives and disaster preparedness.
The versatility of pressure sensors thus contributes to improved performance and reliability across various operations. In each application, there are considerations like sensor type, calibration requirements, and environmental factors that significantly affect effectiveness and accuracy. With this foundation, we can explore specific applications in greater detail.
Manufacturing and Automation
In the manufacturing sector, mechanical pressure sensors are primarily used to monitor and control production processes.
Key applications include:
- Process Control: Sensors ensure that pressure levels remain within specified limits, allowing for efficient operations without the risk of equipment damage.
- Quality Assurance: Precise pressure readings help maintain quality in products ranging from food packaging to automotive components. For example, in pneumatic systems, pressure sensors ensure the right amount of force is applied during assembly, leading to better product integrity.
The advantages of employing these sensors in manufacturing are manifold. They automate pressure monitoring, reducing human error and labor costs, thus supporting lean manufacturing principles. Also, fewer defects translate to lower waste, enhancing sustainability efforts.
Healthcare Devices
In healthcare, mechanical pressure sensors are critical in various applications ranging from invasive procedures to patient monitoring systems. They play a pivotal role in:
- Vital Signs Monitors: Devices like sphygmomanometers depend on pressure sensors to provide accurate blood pressure readings.
- Respiratory Monitors: These sensors are used in ventilators to gauge airway pressures, ensuring patients receive appropriate ventilation.
The benefits of mechanical pressure sensors in healthcare cannot be overstated. Their ability to deliver high precision under varied conditions is paramount in emergencies. Additionally, real-time monitoring can enable immediate medical responses, targeting life-saving care where it counts the most. The integration of pressure sensors in devices provides healthcare professionals with reliable data, ultimately improving patient management and outcomes.
Environmental Monitoring
Environmental applications of mechanical pressure sensors extend from weather monitoring to flood detection systems. Key uses include:
- Weather Stations: By measuring atmospheric pressure, these sensors help predict weather changes, providing crucial data for climate studies and public safety.
- Hydrological Systems: In flood-prone areas, pressure sensors monitor water levels, enabling early warnings and preventive measures against natural disasters.
The impact of these sensors in environmental monitoring cannot be taken lightly. Accurate pressure readings contribute to better predictive models and resource management strategies. As environmental concerns intensify globally, the data provided by pressure sensors will support sensors into more sustainable practices, aligning with conservation efforts and disaster readiness initiatives.
With the ever-increasing demands of various sectors, mechanical pressure sensors are instrumental in bridging gaps between technology and real-world applications. Each industry, from manufacturing to healthcare and environmental systems, highlights the crucial role these sensors play in driving efficiency, safety, and innovation.
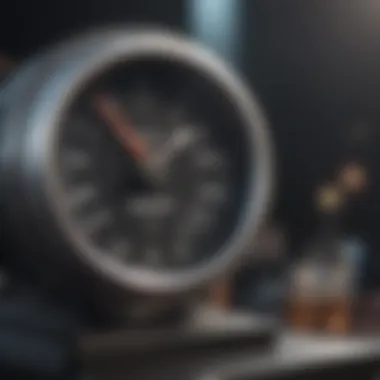
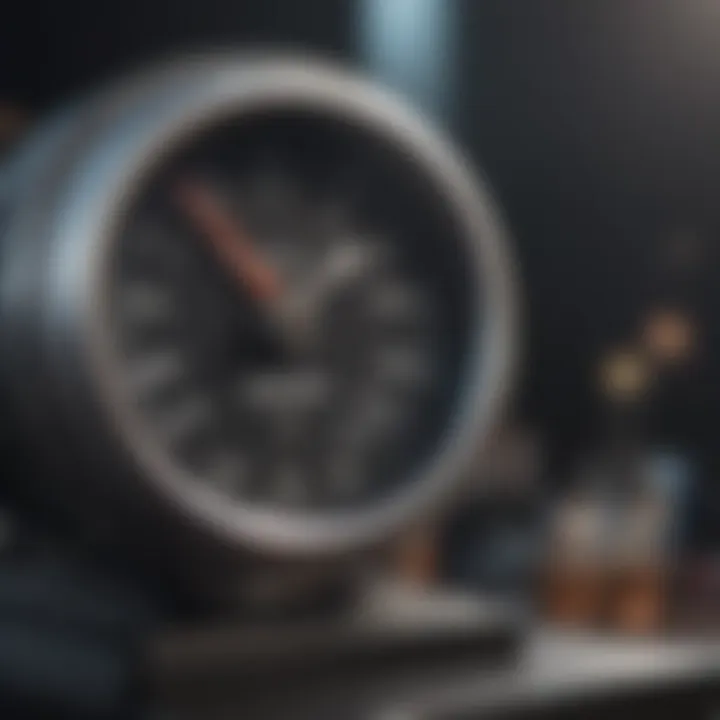
"In the age of data, the precision of measurements like those from mechanical pressure sensors turns into the backbone of analysis and decision-making across industries."
Challenges in Pressure Measurement
Understanding the difficulties that come with measuring pressure is crucial in the field of mechanical sensors. Pressure measurement is not just a straightforward task of attaching a sensor and reading a value; it involves intricate processes, many variables, and numerous potential pitfalls. As we delve into the realm of mechanical pressure sensors, recognizing these challenges becomes vital. Essentially, these issues can impact the accuracy, reliability, and overall performance of pressure measurements across applications ranging from industrial automation to healthcare devices.
Mechanical Limitations
Mechanical pressure sensors have inherent constraints that can affect their performance. One of the most significant issues is their sensitivity to mechanical stress. Mechanical deformation can occur during the operation, leading to hysteresis and errors in measurement. For instance, a sensor designed to handle a specific range might not perform accurately if subjected to higher or lower pressures than intended. This can cause readings to lag behind true values, leading to faulty data and potentially catastrophic results in critical systems.
Moreover, the material properties of the sensor components also play a critical role. Variations in material strength and fatigue can lead to failure over time, which is a common problem in environments with extreme temperatures or corrosive substances. When pressure sensors are exposed to these conditions, they may experience degradation, resulting in inaccurate measurements. Engineers must consider these drawbacks when designing systems utilizing mechanical pressure sensors.
Environmental Influences
Environmental factors can greatly impact the performance of pressure sensors, making them susceptible to a wide array of conditions. Fluctuations in temperature, humidity, and even electromagnetic interference can cause significant errors. For example, high temperatures can lead to expansion of sensor components, affecting calibration and potentially causing drift in readings. Similarly, extreme humidity might result in condensation within sensors, leading to erroneous data.
Furthermore, the installation location of the pressure sensor cannot be overlooked. In industries like oil and gas, sensors placed in outdoor environments can face challenges from elements such as wind, rain, or even physical obstructions.
To sum up, engineers and technicians must take into account these environmental influences and mechanical limitations when deploying mechanical pressure sensors. Proper planning, robust design, and regular maintenance can alleviate many of these challenges, ensuring accurate and reliable measurements.
"Understanding the challenges in pressure measurement is as important as the measurement itself."
Future Trends in Sensor Technology
In the ever-evolving field of sensor technology, mechanical pressure sensors stand out as vital components that continue to adapt to new challenges and opportunities. The exploration of future trends not only sheds light on the trajectory of these sensors but also highlights their growing importance in various applicationsβfrom industrial automation to healthcare. This section articulates how integration with the Internet of Things (IoT) and advancements in miniaturization are shaping the future landscape of mechanical pressure sensors.
Integration with IoT
The Internet of Things has revolutionized many sectors, and mechanical pressure sensors are no exception. This integration offers a barrage of benefits that can enhance functionality and usability. For example:
- Real-Time Data Acquisition: Pressure sensors connected to IoT networks can relay data instantly, enabling real-time monitoring of critical systems. This immediacy allows for quicker reactions to anomalies, potentially saving time and resources.
- Predictive Maintenance: By continuously monitoring equipment, IoT-enabled pressure sensors facilitate predictive maintenance, reducing the risk of failure. This is particularly crucial in industries like oil and gas, where downtime can be significantly costly.
- Enhanced Data Analytics: With the integration of IoT, data collected from pressure sensors can be analyzed for trends and anomalies, leading to more informed decision-making.
As industries increasingly rely on big data for operational efficiencies, the interconnectedness provided by IoT will become indispensable for mechanical pressure sensors. The potential for improved accuracy and the ability to reach previously unmonitored locations opens doors to innovative applications.
Advancements in Miniaturization
As technology advances, the demand for smaller, more compact devices has surged. In the realm of mechanical pressure sensors, miniaturization is not just about saving space; it's about unlocking a suite of capabilities that were previously inconceivable.
- Space-Saving Design: Smaller sensors can fit in tighter spaces without compromising performance. This is crucial in industries like automotive manufacturing, where every inch counts.
- Lower Power Consumption: Miniaturized sensors tend to require less power, making them more efficient. This is particularly beneficial in remote applications, such as environmental monitoring stations, where battery life can be a limiting factor.
- Increased Versatility: Smaller sensors can be integrated into a wider variety of devices, from wearables to smart home appliances. This versatility is essential as demand grows for consumer-level applications that rely on precision.
"As we refine sensor technology, the shrinking of mechanical pressure sensors paves the way for creativity in design and functionality. These advancements will likely lead to an exciting and adaptable future."
In essence, the future trends in sensor technology highlight significant shifts in how mechanical pressure sensors will be used and integrated into broader systems. Both integration with the IoT and advancements in miniaturization promise to enhance the capabilities and applications of these essential devices, ultimately transforming the landscape of pressure sensing. As these trends evolve, they will not only improve the current methods of measurement but also open avenues for innovative applications and solutions across various sectors.
Case Studies and Real-Life Applications
Examining case studies and real-life applications of mechanical pressure sensors serves a dual purpose: it illustrates the practical significance of these devices and showcases their versatility across different sectors. These stories illuminate the journey from theory to application, revealing not just how pressure sensors work, but why they are crucial in solving real-world problems. The insights gathered from these examples enable readers to appreciate the practicality and adaptability of mechanical pressure sensors, fueling further interest in the field.
Industrial Use Cases
In the industrial landscape, mechanical pressure sensors are employed in various settings, including manufacturing, aerospace, and oil and gas sectors. Each use case highlights different functionalities and challenges, enriching our understanding of these sensors.
- Oil and Gas Sector: Pressure sensors are essential in monitoring pipeline integrity. They help detect leaks before they escalate into catastrophic events, ensuring safety and compliance with environmental regulations. By leveraging sensors that can withstand extreme conditions, companies protect assets and the environment effectively.
- Aerospace Engineering: In aviation, mechanical pressure sensors play a significant role in flight control systems. Altitude detection relies on precise pressure measurements, enabling pilots to navigate safely. Here, the reliability of these sensors directly ties to safety. If they fail, it could spell disaster.
- Manufacturing Automation: Many production lines use mechanical pressure sensors to monitor equipment and processes. For example, hydraulic systems utilize pressure sensors to maintain optimal fluid levels, ensuring consistency and quality. Sensors can trigger alarms or shut down machinery when pressure rises beyond safe limits, preventing costly accidents.
- Food and Beverage Industry: Quality control in food production often involves monitoring the pressure in sterilization processes. Maintaining the correct pressure can determine the shelf life and safety of products. By integrating effective mechanical pressure sensors, companies can enhance product reliability.
Each of these cases illustrates that the integration of mechanical pressure sensors not only improves operational efficiency but also significantly mitigates risks in high-stakes environments.
Innovative Research Projects
The realm of mechanical pressure sensors is evolving, driven by innovative research projects that promise to push the boundaries of what these sensors can achieve. A few notable directions of research illustrate this shift:
- Smart Textiles: Researchers are now embedding pressure sensors into fabrics, creating smart textiles that can monitor vital signs in real-time. This innovation has profound implications for healthcare, especially for elderly or bedridden patients who require continuous monitoring without cumbersome equipment.
- Flexible Sensors: The development of flexible pressure sensors is making waves in the field of wearable technology. This kind of sensor can conform to various shapes, providing accurate readings in diverse conditions. Future applications could include monitoring pressure in rehabilitation settings or even enhancing virtual reality experiences.
- Microfabrication Techniques: Utilizing advanced microfabrication techniques, researchers are creating miniature pressure sensors. These tiny devices could be integrated into drones or environmental sensors, allowing for extensive monitoring capabilities in remote or hard-to-reach areas.
- AI Integration: Some projects focus on integrating artificial intelligence with mechanical pressure sensors to predict failures before they occur. By analyzing pressure data trends, AI can help in preventive maintenance, reducing downtime and extending the lifespan of crucial machinery.
These innovative projects not only showcase the evolving landscape of mechanical pressure sensors but also underscore their potential in enhancing everyday applications, ultimately contributing to safer and more efficient systems in various domains.
"The future of mechanical pressure sensors lies in their integration with cutting-edge technologies, promising an array of applications that can redefine standards in safety and efficiency."
Closure and Implications
The exploration of mechanical pressure sensors has revealed their integral role in engineering and technology today. These sensors are much more than mere devices measuring pressure; they embody essential components within complex systems across various industries. Understanding their principles of operation, types, and calibration techniques is crucial for students, researchers, and professionals to fully grasp their applications and implications.
Summary of Key Insights
To recap, mechanical pressure sensors operate through mechanisms such as strain gauges, capacitive elements, and MEMS technology. These devices have historically evolved, advancing from simple mechanical measurements to sophisticated electronic interfaces. Not only do they improve efficiency in manufacturing and healthcare, but they also play a vital part in environmental monitoring. These insights reveal how critical reliable pressure measurement is for achieving operational success and ensuring safety.
Additionally, limitations such as mechanical constraints and environmental influences present challenges that must be understood and addressed. Calibration remains pivotal in maintaining measurement integrity, impacting accuracy and performance. These elements highlight the complexity surrounding pressure sensors, making it vital for any stakeholder in these fields to stay updated on these topics.
The Future of Mechanical Pressure Sensors
Looking ahead, the future of mechanical pressure sensors appears ripe with opportunities for innovation. The integration with the Internet of Things (IoT) stands as a hallmark of this transformation. As sensors become increasingly interconnected, they promise to facilitate real-time data transmission and monitoring, enhancing automation and control.
Moreover, advancements in miniaturization are set to revolutionize how these sensors are incorporated into devices. Smaller sensors will not only broaden applications in fields like wearables and mobile tech but will also reduce costs and increase accessibility for smaller enterprises.
In sum, the significance of mechanical pressure sensors stretches across sectors, and their evolution will undoubtedly influence future technological developments. Itβs clear that understanding these mechanisms today will better prepare engineers and business leaders for tomorrow's challenges and solutions.