RMS Roughness: Exploring Surface Profile Impacts
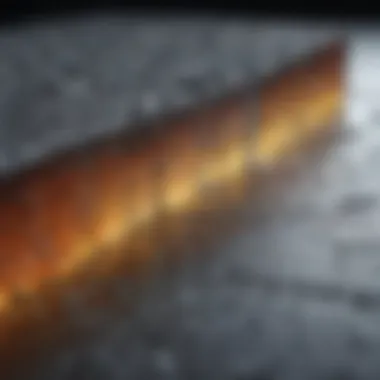
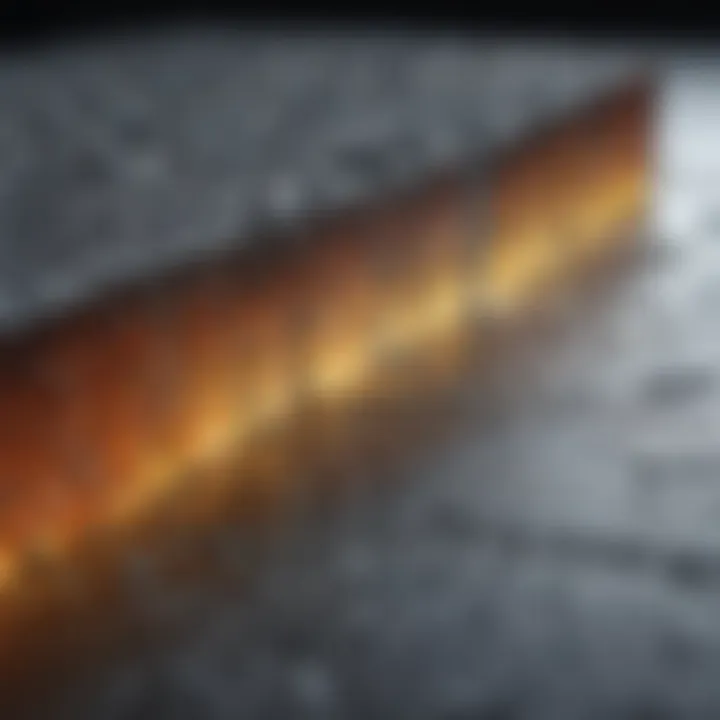
Intro
Understanding RMS roughness is essential for various industries focusing on surface quality. This term, short for Root Mean Square roughness, quantifies the texture of a surface, indicating its irregularities. It plays a key role in how materials perform, from adhesion and friction to wear and corrosion resistance.
Through technological advancements, the methods to measure RMS roughness have improved significantly. Researchers now utilize various techniques, allowing them to obtain more accurate and reliable data. This article aims to shed light on these advancements, explore methodologies for measuring RMS roughness, and discuss its significance across different fields. By doing so, we provide a framework for educators, students, and professionals to grasp this complex yet critical parameter.
Recent Advances
Latest Discoveries
Recent studies have highlighted significant developments in understanding the effects of RMS roughness on material behavior. Discoveries indicate that even minor variations in surface texture can lead to substantial differences in performance metrics. For example, research from various institutions has shown that the microstructure of polished surfaces can alter how a material interacts with liquids, affecting properties like wettability.
Another key finding is related to the relationship between surface roughness and fatigue life in materials. Investigations show that surfaces with lower RMS roughness tend to exhibit increased fatigue resistance, particularly in metals and alloys. This insight informs better design strategies in engineering applications, where durability is paramount.
Technological Innovations
Technological progress has introduced new measurement tools that enhance the precision of RMS roughness assessments. Scanning probe microscopy and atomic force microscopy are just two examples, providing unprecedented details of surface profiles. These instruments allow researchers to measure surface features at the nanoscale, offering a deeper understanding of how micro and nano-scale roughness affect material properties.
Moreover, advancements in software for data analysis have made it easier for scientists to interpret RMS roughness metrics. Enhanced algorithms can now process large datasets quickly, improving the accuracy of evaluations. As a result, industries can implement better quality control measures, thus increasing overall productivity and material reliability.
"RMS roughness assessment is not merely a measure; it lays the groundwork for strategic decisions in design and manufacturing."
Methodology
Research Design
The investigation into RMS roughness typically involves a cross-disciplinary approach. Researchers often establish a framework that includes both theoretical modeling and experimental validation. This structure allows for comprehensive insights that can be applied in industrial settings.
Data Collection Techniques
Various techniques for data collection exist. The common methods for measuring RMS roughness include:
- Contact Profilometry: Measures surface profiles by using a stylus that travels across the surface.
- Non-contact Optical Methods: Employ laser or white light to assess surface texture without physical contact.
- Scanning Electron Microscopy: Offers high-resolution images for detailed surface analysis.
Choosing the appropriate method depends on the material being studied and the level of detail required. Understanding the strengths and limitations of each technique is crucial to obtaining reliable results.
Prelude to RMS Roughness
RMS roughness plays a significant role in the field of surface science. It provides essential details about the topography of a surface. Understanding this concept is vital for researchers, engineers, and designers, as surface quality often dictates material performance in various applications. From manufacturing processes to biomedical devices, the implications of surface roughness are extensive. By analyzing RMS values, one can gain insights into how surfaces interact in real-world conditions, influencing friction, wear, and adhesion, among other factors.
Definition of RMS Roughness
RMS roughness, or Root Mean Square roughness, is a statistical measure used to quantify surface irregularities. Specifically, it calculates the average height deviations of a surface profile from the mean line. This mathematical approach gives a clear representation of the roughness characterizing the textured surfaces. It is commonly applied in engineering and materials science fields to assess quality and performance, making it a vital concept to understand.
The formula for calculating RMS roughness is defined as follows:
Where:
- ( Z_i ) represents the height of each sample point,
- ( \barZ ) is the average height,
- ( N ) is the total number of sample points.
This calculation method is crucial in determining how surface features will affect various physical properties, such as mechanical strength or thermal behavior.
Historical Context
The study of surface roughness has evolved significantly over time. Initially, roughness was assessed qualitatively, often through visual methods. However, as technology advanced, the need for precision became evident. The development of measurement techniques, such as stylus profilometers and optical sensors, revolutionized the ability to quantify surface texture.
In the early 20th century, engineers began adopting standardized measures that allowed for consistent analyses across different materials and applications. The introduction of mathematical definitions provided a framework that scientists could use to communicate effectively about surface characteristics. Over the decades, RMS roughness emerged as a standard figure to express surface quality in many industries, supporting a wide array of technological advancements.
Mathematical Foundations
Understanding RMS roughness requires a solid grasp of its mathematical underpinnings. As a fundamental measure of surface texture, the mathematical foundations of RMS roughness encompass various calculations and statistical methods that define how surface roughness is quantified and analyzed. This section aims to elucidate the critical mathematical concepts and techniques essential for assessing surface roughness, which can pave the way for improved manufacturing processes, enhanced material performance, and better quality control in various industries.
Mathematics of Roughness Calculation
The calculation of RMS roughness hinges on the concept of surface profile. To compute the RMS roughness, one must first obtain a surface profile using either direct measurements or stylus tracing methods. The formula for calculating RMS roughness is defined mathematically as:
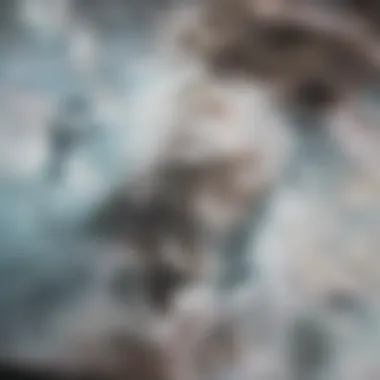
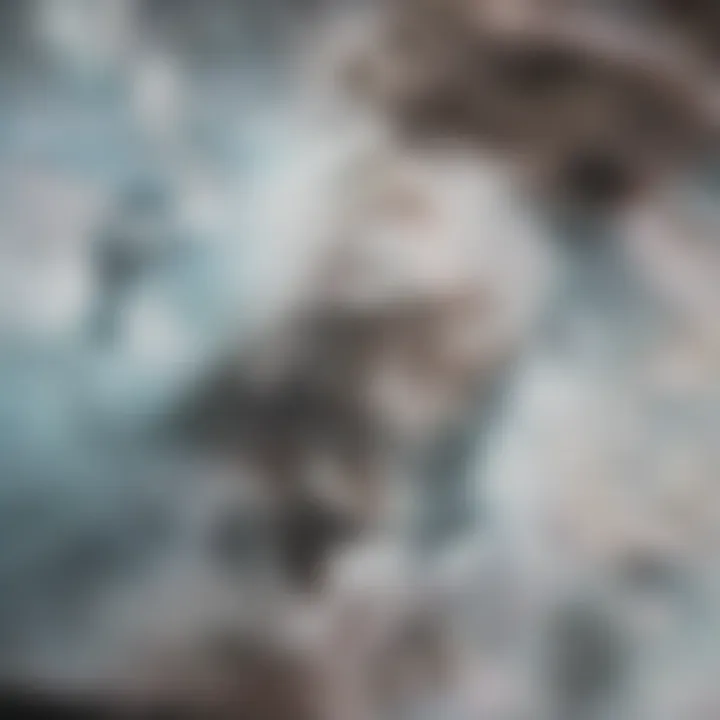
[ \textRMS = \sqrt\frac1N \sum_i=1^N z_i^2 ]
In this equation, (z_i) represents the height of each point on the surface profile, and (N) is the total number of sampled points. The formula illustrates that the RMS roughness accounts for both the magnitude and distribution of surface deviations from the mean line. By emphasizing the quadratic nature of height deviations, it provides a more sensitive measure of roughness than basic average height measures.
The importance of accurate mathematical calculations cannot be overstated. Any inconsistencies in the measurement process can lead to significant errors in the calculated RMS values, ultimately affecting material performance and quality assessments. Therefore, precise measurement techniques are essential to uphold the integrity of the roughness values derived.
Statistical Methods in Surface Analysis
Statistical methods play a vital role in the analysis of surface roughness. These methods help in interpreting the surface characteristics more effectively by analyzing large datasets obtained from multiple measurements. Descriptive statistics, such as mean, standard deviation, and skewness, provide a dataframe for understanding the distribution and spread of surface heights, while inferential statistics help in determining the reliability and significance of these measurements.
Additionally, techniques like regression analysis can establish relationships between surface roughness and other factors affecting performance, such as wear resistance and adhesiveness. Statistical models can also simulate potential outcomes of various treatments on surface roughness, offering insights into optimal approaches for manufacturing and engineering processes.
Using statistical software or programming languages like Python or R can streamline the processing of surface roughness data. This analytical capability is pivotal for researchers and professionals aiming to draw meaningful conclusions from complex datasets derived from empirical measurements.
In summary, the mathematical foundations of RMS roughness calculations and the role of statistical methods in surface analysis form a comprehensive framework. This knowledge enhances the understanding of surface profiles and allows best practices to be applied in different fields, such as material science, engineering, and quality control.
Measurement Techniques
The assessment of RMS roughness heavily relies on precise measurement techniques. Such techniques are fundamental in determining the surface profile of materials. A thorough understanding of these methods enhances the accuracy of surface characterization, influencing decisions in material selection and processing. The selection of a measurement method may depend on several factors including the type of material, the required precision, and the intended application. Thus, mastering these techniques is crucial for students, researchers, and professionals alike.
Contact Methods
Contact methods of measurement involve the physical interaction of a probe with the surface being analyzed. This technique is widely used due to its ability to provide direct readings of surface roughness. The most common instrument in this method is the stylus profiler. In this process, a diamond-tipped stylus traverses the surface. The vertical movements of the stylus, caused by surface irregularities, are recorded and converted into a profile.
Some key benefits of contact methods include:
- High accuracy and resolution of measurements
- Established and widely accepted protocols
- Ability to provide detailed surface profiles
However, there are also considerations:
- Potential damage to soft materials
- Limited applicability on very soft or fragile surfaces
- The need for careful calibration to ensure precision
Non-contact Methods
In recent times, non-contact methods have gained popularity in surface measurement. These techniques eliminate the potential for surface damage, making them ideal for sensitive materials. Non-contact methods include optical methods like laser scanning and interferometry. These techniques utilize the reflection of light to gauge surface characteristics without direct contact.
Advantages of non-contact methods include:
- No risk of altering the surface being measured
- Faster data acquisition
- Suitability for a variety of surface types, including very rough or delicate surfaces
Nevertheless, they also face some issues:
- Higher initial investment in equipment
- Sensitivity to surface contaminants, which can affect results
- Calibration complexities
Comparative Analysis of Techniques
When selecting a measurement technique, a comparative analysis is essential. Understanding the strengths and weaknesses of both contact and non-contact methods can guide users to make informed decisions based on their specific measurement needs.
Factors to consider include:
- Accuracy: Contact methods often offer higher accuracy for detailed profiles. Non-contact methods can sometimes provide less precise readings, but advancements in technology are closing this gap.
- Material Compatibility: Certain materials are better suited for one method over the other. For example, delicate materials may prefer non-contact techniques.
- Cost-Effectiveness: While non-contact methods often have higher equipment costs, the potential for long-term savings should be considered based on the usage frequency and wear on probes in contact methods.
In summary, each measurement technique has its own unique advantages and limitations. A careful evaluation of these aspects is needed to select the most suitable method for a specific application.
Important Note: The choice of measurement technique can significantly affect the results obtained in surface roughness analysis and therefore the subsequent material performance.
To learn more about surface profiling and measurement techniques, please visit Wikipedia or explore more resources on Britannica.
Industry Standards and Protocols
The examination of RMS roughness cannot be comprehensive without addressing the crucial role of industry standards and protocols. These standards provide essential guidelines that ensure consistency, accuracy, and reliability in surface roughness measurement and reporting. They serve as a framework for professionals across disciplines to assess and communicate surface quality in a standard format, fostering clarity and reducing misunderstandings in both research and practical applications.
Incorporating established protocols helps mitigate variability in measurement techniques and enables comparative analysis across different studies and industrial applications. Without these standards, interpreting measurement results could become subjective, leading to discrepancies and potential failures in material performance. Therefore, understanding these industry standards is paramount for engineers, material scientists, and quality control professionals.
ISO Standards for Surface Roughness
ISO (International Organization for Standardization) has developed specific standards governing the measurement of surface roughness. The ISO 4287 and ISO 4288 series are the most pertinent. These guidelines detail how to measure surface roughness efficiently using various parameters, including RMS, average roughness (Ra), and maximum height of the profile (Rz).
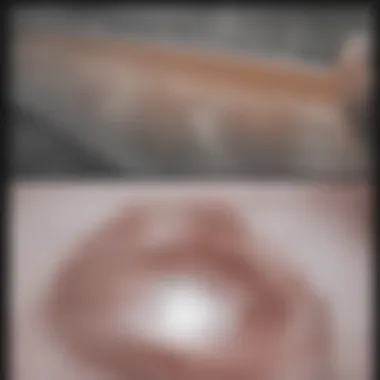
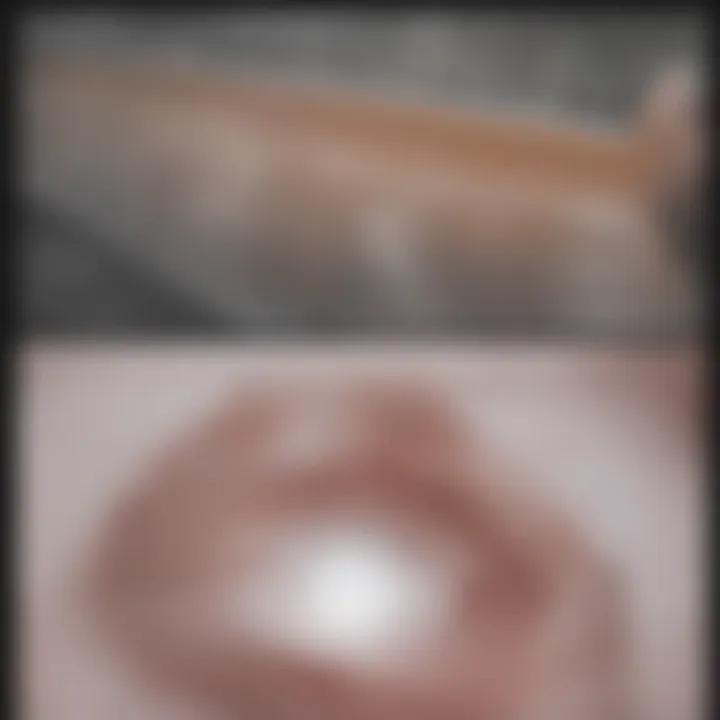
These ISO standards delineate:
- Measurement Techniques: They provide specifications on how to conduct measurements, ensuring uniformity in tool usage and operational procedures.
- Roughness Parameters: Definitions and calculations of parameters like RMS roughness help clarify which measurements should be taken based on a surfaceβs intended application.
- Reporting: Standards outline best practices for documenting measurements which are crucial for quality assurance and compliance with industry regulations.
Adhering to ISO standards not only ensures a level of quality and precision but also enhances the reliability of data shared among scientists and engineers, facilitating cooperation across international projects and initiatives.
ASTM Guidelines
ASTM International also provides standards relevant to surface roughness measurement and its implications in practice. For instance, ASTM E1921 outlines guidelines concerning the evaluation of surface roughness under specific conditions and materials. These guidelines are integral in various sectors, from aerospace to automotive, where surface quality directly influences performance and safety.
Key aspects of ASTM guidelines include:
- Material Testing: ASTM protocols specify procedures for testing surface roughness on different materials, which is vital for ensuring performance criteria are met.
- Industrial Applicability: Each guideline provides context for industry-specific applications, allowing professionals to align measurements with their operational requirements.
- Updated Practices: Regular updates ensure the guidelines reflect the latest technological advancements and methodologies in surface analysis.
"Standards set in ISO and ASTM are more than just guidelines; they are the foundation for enhancing quality and performance in material applications."
By adhering to these standards, stakeholders can ensure a consistent approach toward understanding and applying RMS roughness in their respective fields.
Applications of RMS Roughness
The topic of RMS roughness is integral to various industries, particularly in manufacturing processes, material selection, and surface coatings. Understanding how surface profiles affect functionality is not simply an academic pursuit; it has real-world implications across engineering and manufacturing sectors. By exploring specific applications, we elucidate the importance of RMS roughness in practical scenarios, enhancing quality assessments and improving material performance.
In Manufacturing Processes
RMS roughness directly influences manufacturing processes, from machining to casting. The roughness of a surface can affect the method of production and the equipment used. For instance, in precision machining, a surface with inappropriate roughness can result in poor fits in assemblies, leading to operational inefficiencies.
Key Considerations:
- Tolerance and Fit: Tight tolerances often require smoother surfaces. For parts that fit together, RMS roughness must meet specific standards, as rough surfaces can hold contaminants, affecting performance.
- Cost Efficiency: Smoother surfaces often reduce friction, which can decrease wear on tools and machinery, leading to lower maintenance costs.
- Surface Integrity: Manufacturing processes aimed at minimizing surface defects often lead to a reduction in residual stress, enhancing the durability of components.
Role in Material Selection
Material selection is heavily influenced by RMS roughness, as it can dictate the suitability of materials for various applications. Different materials exhibit varied surface properties, which can change based on the treatment methods employed.
Factors to Consider:
- Material Compatibility: When selecting materials, one must consider how the surface roughness will interact with other elements. For instance, certain coatings may adhere better to smoother surfaces, thus requiring a careful selection approach.
- Performance Criteria: Applications demanding high performance often specify roughness profiles to ensure materials can withstand operating conditions without degradation.
- Cost-Effectiveness: Selecting a material that meets the desired roughness within a budget is crucial. The implications of roughness extend beyond performance and touch upon economic viability as well.
Effect on Surface Coatings
RMS roughness plays a pivotal role in the adhesion of surface coatings. The integrity of bonding between coating and substrate can significantly affect the durability and longevity of the coated surface. Understanding these relationships is vital for industries relying on coatings for protection and aesthetics.
Understanding the Effect:
- Adhesion Quality: Rough surfaces may provide better mechanical interlocking for adhesives, but if excessively rough, may lead to poor performance due to flaws in the bonding area.
- Surface Preparation: Coating applications often involve surface treatments to achieve a specific roughness level suited for the intended coating, enhancing not just bond strength but also corrosion resistance.
- Overall Aesthetics: The desired appearance of a finished product is influenced by surface roughness, impacting marketability and consumer perceptions.
"Controlling RMS roughness is fundamental to achieving the desired functional properties in materials and coatings. Without addressing this, one risks undermining performance and durability."
Implications for Material Performance
The implications of RMS roughness on material performance are multifaceted and profound. Understanding surface texture plays a critical role in various engineering applications. The roughness of a material's surface can significantly influence its physical properties, including adhesion, friction, and wear resistance. Thus, assessing surface roughness is not merely an academic exercise; it is essential for optimizing material performance in practical applications. Recognizing these implications allows engineers and manufacturers to design more effective components tailored to specific uses.
Influence on Adhesion Properties
Adhesion is a fundamental characteristic in the interaction between surfaces. The RMS roughness of a material greatly impacts its adhesion properties. A smoother surface generally provides less mechanical interlocking, which can reduce adhesive strength. Conversely, a rougher surface introduces additional area for contact and increases mechanical interlocking, enhancing adhesion.
In adhesive bonding, the following considerations are essential:
- Surface Roughness Measurement: It is crucial to evaluate the roughness accurately. Instruments like profilometers can provide the precise RMS values that determine the surface quality.
- Material Compatibility: The combination of adhesive and substrate surfaces can either promote or hinder adhesion depending on their roughness profiles.
- Environmental Factors: Conditions such as humidity and temperature can alter the roughness impact, influencing the adhesion over time.
Ultimately, understanding how RMS roughness affects adhesion can lead to better design choices in various applications, especially in industries such as automotive and aerospace.
Impact on Friction and Wear
Friction and wear are critical considerations in the functionality and longevity of mechanical components. The relationship between RMS roughness and these two properties is important for material selection and component design.
A few important points to note include:
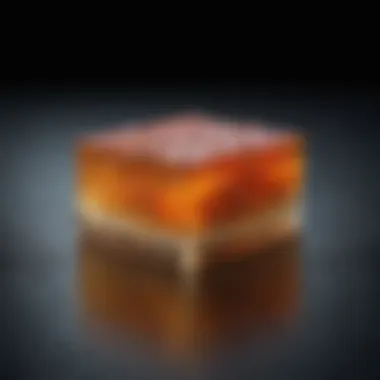
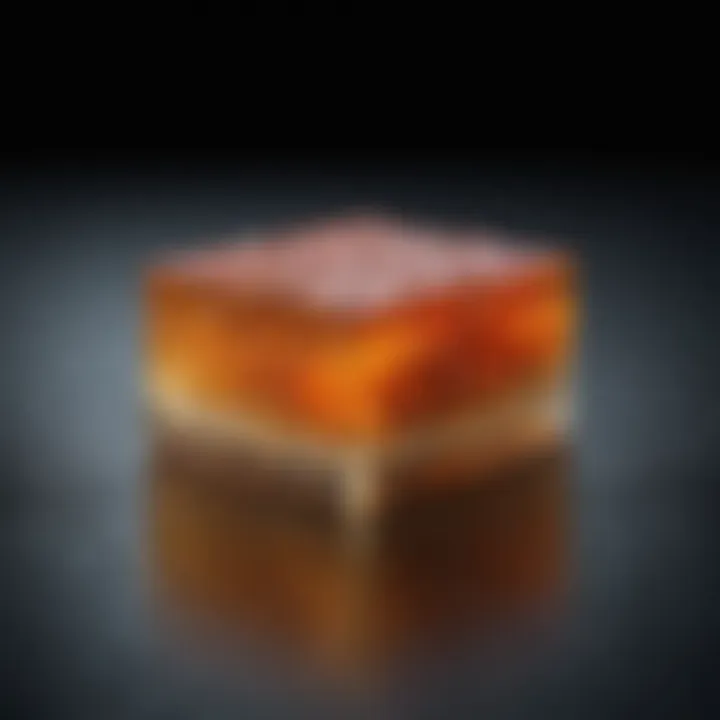
- Friction Coefficients: Surfaces with higher roughness can exhibit increased friction. However, the relationship is complex. Sometimes, increased roughness may lead to lower friction due to the formation of lubricant pathways.
- Wear Resistance: Materials with appropriate roughness can enhance wear resistance. A too-smooth surface may wear down quickly due to minimal stress distribution. On the other hand, rough surfaces can lead to increased wear under some conditions.
- Lubrication: Optimal surface roughness can also support effective lubrication. Properly designed surfaces can help retain lubricant, minimizing wear.
When considering friction and wear, the overall performance of a mechanical assembly can be optimized by comprehensively understanding RMS roughness and its implications. As a result, engineers can make informed decisions that improve reliability and efficiency of systems in various applications.
"In precision engineering, understanding the implications of RMS roughness can differentiate between failure and success in component performance."
Case Studies
Case studies provide a practical lens through which the implications of RMS roughness can be explored. Analyzing real-world applications enhances understanding of how surface profile impacts performance in various industries. By examining specific instances, it is possible to identify the benefits of monitoring RMS roughness and the critical insights that can be gained.
When evaluating case studies, one must consider several elements:
- Relevance: The case should relate directly to the impact of surface roughness on performance.
- Data Collection: Quality and methods of data collection are essential for credibility.
- Measurement Techniques: The methods employed to measure RMS roughness should be clearly outlined.
The importance of these elements cannot be overstated. A well-documented case study can serve not only as a learning tool but also as a benchmark for future investigations.
RMS Roughness in Precision Engineering
Precision engineering operates at tight tolerances where every microscopic detail matters. In this field, the RMS roughness is significant in determining how components fit together and function in real-world applications. For example, in the production of gears or bearings, surface roughness can have a direct correlation with the mechanical performance of the final product. If a surface is too rough, it can lead to increased friction, reduced lifespan, and even catastrophic failure.
Various techniques to measure RMS roughness are employed in this sphere, including contact profilometry and optical methods. Each method may yield different results, thus it is important to choose one based on the specific requirements of the component being analyzed.
Real-world applications, for instance, include:
- Machined components: Often optimized based on RMS roughness values to ensure smooth operation and longevity.
- Micro-manufacturing: Where even minor variations in surface finish can have outsized impacts.
Maintaining tight control over RMS roughness leads to improved product reliability and can be a competitive advantage in markets demanding high precision.
Impact Assessment in Aerospace Materials
In the aerospace sector, where safety and performance are crucial, the assessment of RMS roughness is vital. Surfaces subjected to high stress, such as those on aircraft wings or turbine blades, necessitate rigorous analysis of surface characteristics. The roughness values can influence aerodynamic performance and fuel efficiency, thereby affecting operational costs.
Materials used in aerospace must withstand extreme conditions, and surface roughness plays a key role in material selection. For example, titanium alloys often used in aircraft structures require specific roughness specifications to enhance fatigue resistance and overall durability.
Furthermore, thorough impact assessments are conducted to correlate RMS roughness with:
- Fatigue life: Rougher surfaces may initiate cracks more easily under cyclic loading.
- Corrosion resistance: Surface imperfections can become sites for corrosion, leading to premature failure.
By analyzing how RMS roughness influences these factors, aerospace engineers can make informed decisions in both design and material selection processes.
Future Directions in Surface Science
The realm of surface science is at a pivotal junction, wherein advancements in technology and methodologies promise to reshape how researchers and professionals approach surface characterization. Understanding the future directions in this field is crucial for continuous innovation. This section elaborates on the emerging trends and their implications in RMS roughness measurement and analysis.
Advancements in Measurement Technology
Recent years have witnessed significant advancements in measurement technology related to RMS roughness. The evolution from traditional contact methods to modern non-contact techniques illustrates this shift.
- Higher Resolution Measurements: Advanced optical and atomic force microscopy (AFM) techniques now enable researchers to obtain high-resolution images of surface profiles. This provides more accurate and granular data on surface textures.
- Real-Time Analysis: New tools allow for real-time measurements, paving the way for immediate feedback in production processes. This immediacy can greatly enhance quality control measures.
- Integration with Nanotechnology: Measurement technology is increasingly coalescing with nanotechnology, allowing for the examination of surfaces at the nanoscale. The ramifications of this integration are profound, particularly in semiconductor manufacturing and other precision engineering fields.
Moving forward, it will be important to balance sophistication with practicality, ensuring that measurement technologies remain accessible to a wider range of industries without sacrificing accuracy.
Integrating AI in Surface Analysis
The integration of artificial intelligence into surface analysis marks a transformative era in RMS roughness characterization. As data generation continues to grow, traditional methods may no longer suffice. AI provides solutions for more efficient data processing and analysis.
- Predictive Analysis: Machine learning algorithms can analyze surface roughness data to predict material performance under different conditions. This predictive capability can save time in both research and industrial applications.
- Pattern Recognition: AI can identify patterns and anomalies in surface profiles that may escape human observation. This ability enhances the reliability of quality assessments and encourages innovation in surface engineering design.
- Automation of Processes: The automation of standard measurements through AI-driven systems leads to increased throughput in manufacturing settings. This boosts efficiency and minimizes human error.
Ending
The conclusion serves as a vital synthesis of the discussions on RMS roughness throughout the article. It reinforces the idea that understanding surface profile is crucial in various industries, from manufacturing to aerospace. By summarizing the key points discussed, readers can grasp the entirety of the topic more efficiently.
Summary of Key Points
In summarizing the key elements of RMS roughness, we can highlight the following:
- Definition and Importance: RMS roughness is a quantitative measure of surface texture. It plays a significant role in determining the functional properties of materials.
- Mathematical Calculations: We explored different mathematical foundations used to derive RMS values, emphasizing the significance of accurate calculations.
- Measurement Techniques: The assessment of surface roughness can be performed using contact and non-contact methods, each with its own advantages and disadvantages.
- Industry Standards: Understanding ISO standards and ASTM guidelines is essential for professionals in ensuring quality and consistency in measurements.
- Applications Across Industries: From influencing adhesion properties to impacting friction and wear, the implications of RMS roughness extend into diverse fields, guiding material selection and manufacturing processes.
- Future Directions: Advancements in measurement technology and the integration of AI indicate a promising horizon for materials science, enhancing how RMS roughness is analyzed and utilized.
Final Thoughts on RMS Roughness
In reflection, the exploration of RMS roughness highlights its crucial role in the performance and functionality of materials. Research and development can greatly benefit from a comprehensive understanding of surface profiles.\nThe ability to measure and analyze surface roughness significantly impacts several aspects such as product durability, quality control, and material performance. As industries evolve, the focus on precision and quality will likely lead to more sophisticated methods for assessing RMS roughness. It is important for researchers, professionals, and students alike to stay informed about these developments and their practical implications.
Understanding surface roughness is not just about measurements; it reflects deeper relationships among material properties, production techniques, and application performance.