Exploring Ultrasonic Soldering: Innovations in Electronics
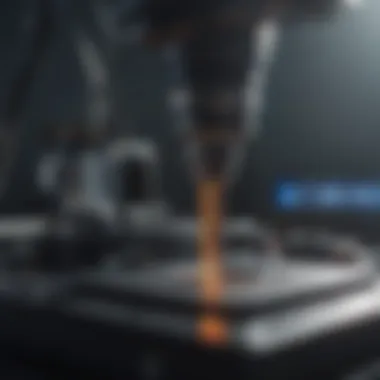
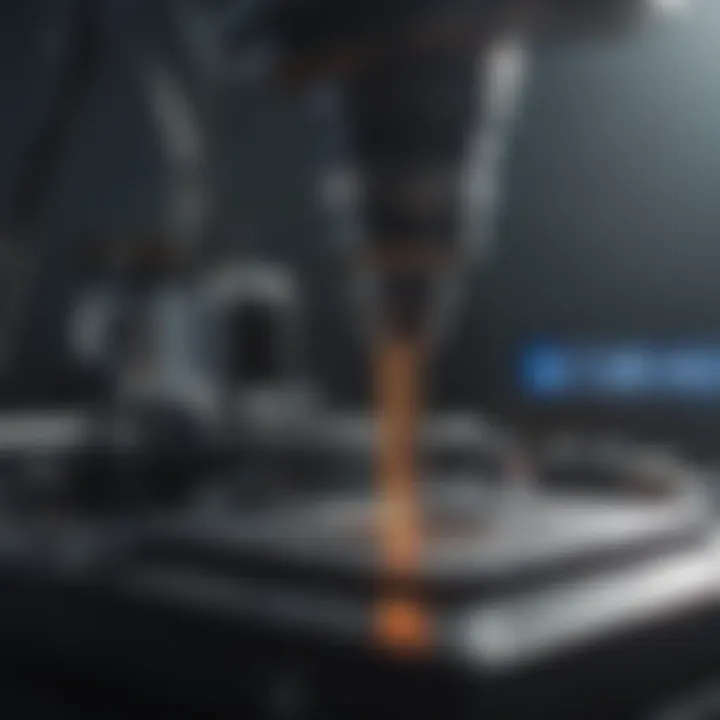
Intro
In the intricate world of manufacturing and electronics, the method of connecting components can make or break the effectiveness and longevity of a device. One such innovative technique that has recently made waves is ultrasonic soldering. This advanced process, which leverages acoustic energy, not only enhances the quality of solder joints but also offers unique solutions where conventional soldering might falter. With rising complexities in electronic device design and miniaturization, understanding ultrasonic soldering becomes imperative. This article aims to provide a well-rounded exploration of its underlying principles, various applications, and the recent innovations that are shaping its future.
Recent Advances
Latest Discoveries
The realm of ultrasonic soldering has seen some fascinating innovations. Recent studies have shown improved thermal efficiency, hence allowing components to be joined at lower temperatures without compromising the integrity of sensitive materials. Such breakthroughs are crucial in protecting heat-sensitive components like those often found in medical devices and compact electronic gadgets. Researchers have broke new ground by experimenting with various materials, like hybrid soldering compounds, that can significantly enhance the longevity and performance of solder joints.
"Understanding ultrasonic soldering is akin to peeling back the layers of an onion; each discovery reveals a new layer of possibilities and improvements in manufacturing techniques."
Technological Innovations
With the advancement of technology, ultrasonic soldering equipment has adopted more sophisticated features. For example, modern machines now come equipped with programmable ultrasonic generators, allowing greater control over frequency and amplitude settings during soldering. This precision can lead to more reliable and repeatable results, a necessity in industries where quality assurance is non-negotiable. Moreover, the integration of AI and machine learning into these systems promises to refine the process further, minimizing human error and promoting consistency across production lines.
Methodology
Research Design
Investigating the advancements and applications of ultrasonic soldering requires a multi-faceted approach. The research combines theoretical physics with practical engineering. By understanding the mechanics of ultrasonic waves and how they interact with solder, researchers can optimize the process. Additionally, case studies across different industries provide insights into real-world applications and the effectiveness of ultrasonic soldering in varying contexts.
Data Collection Techniques
Data gathering for this topic involves both experimental and survey methods. Laboratory experiments help in quantifying performance metrics of ultrasonic solder joints compared to traditional methods. Surveys of industry professionals shed light on the widespread adoption and real-life effectiveness of this technique. Ultimately, this blend of qualitative and quantitative research paints a comprehensive picture of ultrasonic soldering's current state and its potential moving forward.
Prologue to Ultrasonic Soldering
Ultrasonic soldering is carving out its own niche in the world of manufacturing and electronics. This technique takes the notion of joining metal pieces to a whole new level, integrating sound waves with tangible benefits that resonate across multiple industries. As technological advancements continue to evolve, understanding the core elements and capabilities of ultrasonic soldering becomes crucial for students, researchers, and professionals alike.
Definition and Overview
At its simplest, ultrasonic soldering employs high-frequency sound waves to enhance the welding process of metal components. By generating vibrations that cause rapid heating and melting of solder materials, it minimizes the amount of heat needed for effective joins. This approach not only creates strong bonds but also reduces the risk of damaging sensitive components, particularly in electronics. The following key points summarize this innovative practice:
- Precision: Ultrasonic soldering delivers precise control, allowing for localized heating.
- Strength: Joints made using this method tend to be structurally sound and reliable under stress.
- Efficiency: Reduced processing times translate to higher throughput in manufacturing.
A clear understanding of these foundational concepts can help grasp the broader implications and advancements in this domain. The effectiveness of ultrasonic soldering sets it apart from traditional methods, marking a paradigm shift in how professionals approach soldering challenges.
Historical Context
The roots of ultrasonic soldering trace back to advancements in sound wave technology during the mid-20th century. Initially employed in the field of welding, researchers began exploring its potential applications in soldering during the 1960s. The significant leap came when manufacturers started realizing the benefits it could offer in terms of heat reduction and efficiency.
In the early days, many were skeptical about abandoning traditional soldering methods. However, through experimental trials and increasing exposure to electronics and circuit board manufacturing during the 1980s, ultrasonic soldering began to gain traction. Its adoption in high-frequency circuit boards led to a tidal wave of interest across various sectors, including:
- Aerospace: For its reliability and strength in critical components.
- Telecommunications: Given the delicate nature of the circuitry in devices.
The journey of ultrasonic soldering reflects the ingenuity of engineers and technologists who pushed boundaries. As the techniques were refined, the financial incentives, environmental impact, and performance attributes became favorable enough to entice industry giants. Today, it is celebrated as a vital methodology that not only enhances product longevity but also aligns with modern sustainability efforts.
The Science Behind Ultrasonic Soldering
The realm of ultrasonic soldering combines physics and engineering in a unique marriage of efficiency and precision. Understanding the science behind this process is not merely an academic exercise; it brings to light a multitude of benefits in the manufacturing world. One of the primary elements of ultrasonic soldering is its ability to enhance the durability and quality of the joints formed. Moreover, the application of ultrasonic waves makes it possible to join materials that traditional soldering methods struggle with. By addressing the mechanisms and components that make ultrasonic soldering tick, manufacturers can leverage this technology to gain a competitive edge in various industries.
Mechanics of Ultrasonic Waves
At the heart of ultrasonic soldering is the generation of ultrasonic waves. These waves, operating at frequencies above 20 kHz, create high-energy oscillations that fundamentally alter the surface properties of the materials involved. When these waves interact with the solder and the surfaces of the components, they cause microscopic vibrations that help to break down oxidation and contaminants, promoting better bonding. This phenomenon allows for soldering to take place at lower temperatures, reducing thermal stress that might otherwise damage sensitive components.
Understanding how these sound waves behave can be likened to tuning a musical instrument; the precision with which they resonate determines the quality of the outcome. It is this intricate dance of sonic energy that transforms solder from its physical state into an effective joining agent, thereby enhancing manufacturing efficacy.
Key Components of Ultrasonic Equipment
For ultrasonic soldering to function optimally, several critical components work in concert. Each plays its role, contributing to the overall success of the soldering process.
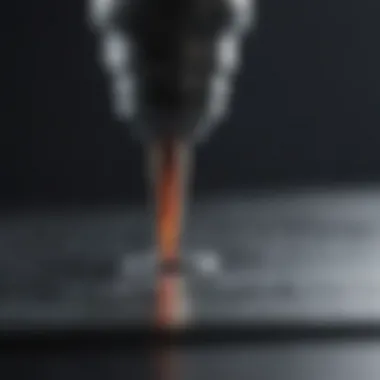
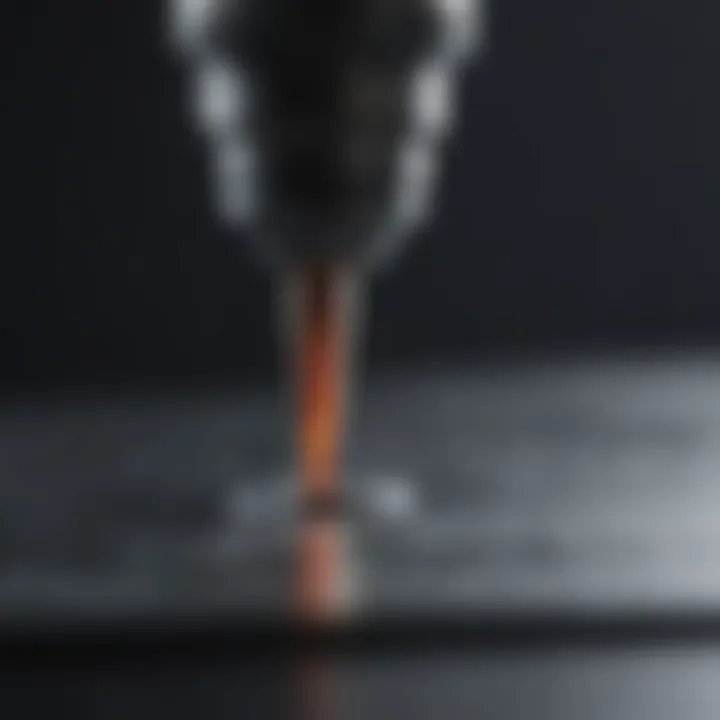
Transducer
The transducer is quite literally the heart of the ultrasonic equipment. It converts electrical energy into mechanical vibrations, setting the stage for the subsequent soldering process. Unique to ultrasonic soldering, transducers often use piezoelectric materials. This key characteristic allows them to produce high-frequency vibrations efficiently, making them a popular choice in industry.
One standout feature of a transducer is its tunability. By adjusting the electrical input, one can modify the frequency of the output vibrations, allowing for adaptability depending on the specific application. However, they can be sensitive to environmental factors, which presents a challenge in consistency. This aspect must be managed effectively for quality assurance in production environments.
Booster
The booster serves to amplify the vibrations generated by the transducer. Think of it as a sound amplifier for a concert; it takes the initial sound waves and intensifies them, making them capable of achieving the desired effect on the materials being soldered. A significant visit card of boosters is their design that maximizes energy transfer while minimizing losses.
Typically made of titanium or aluminum, boosters retain their strength while providing durability. However, their performance can diminish if not maintained properly, leading to inefficiencies in the soldering process. Tasking proper maintenance of these components can be a considerable lift but is essential for maintaining operational integrity.
Horn
The horn further channels the mechanical vibrations from the booster to the workpiece. Its design is pivotal because it can modulate the frequency and amplitude of the ultrasonic waves. Horns are generally crafted from metals that can withstand stress without bending or warping, making them effective for repeated use.
A distinct feature of horns is their specific geometry, which influences how vibrations are dissipated and where they are focused. This specialization can directly impact the quality of the solder joint, making the choice of horn a key decision for engineers. The downside? If the horn is not tailored to match the particular materials or assembly configurations, the results can be subpar, highlighting the importance of choosing correctly.
In summary, the intricate interplay of mechanics, transducers, boosters, and horns within ultrasonic soldering forms a cohesive system that provides a multitude of advantages across different industries. Understanding these components equips manufacturers with the knowledge to harness this innovative technology effectively. In the next section, comparisons between ultrasonic and traditional soldering will further elucidate the value this process offers.
Comparative Analysis: Ultrasonic vs. Traditional Soldering
In modern manufacturing, understanding the differences between ultrasonic soldering and traditional soldering is key for optimizing processes. Both methods serve the same basic purpose—joining materials—but each brings unique properties and benefits to the table. This section aims to analyze critical aspects of both techniques, focusing on efficiency, quality, and cost considerations in various applications.
Efficiency and Speed
When it comes to efficiency, ultrasonic soldering typically outperforms traditional soldering techniques. The core advantage lies in the application of high-frequency ultrasonic waves that promote rapid heating and effective bonding without the need for high temperatures. This means that assembly processes can be completed more quickly and with reduced energy consumption.
A standard traditional soldering process often requires prolonged exposure to heat, which can affect surrounding components, risking damage. Ultrasonic soldering, however, limits thermal exposure. As a result, not only do processes run faster, but they also enhance overall productivity by minimizing downtime.
- Faster cycle times: The use of ultrasonic energy allows for quicker joint formation, leading to high throughput.
- Less thermal fatigue: Components aren't exposed to prolonged heat, decreasing the likelihood of thermal stress.
- Reduced dependencies: Modern production lines can operate with less reliance on flux, further streamlining workflow.
"Efficiency isn't just about speed; it's about optimizing every aspect of the production line."
Quality of Joints
Quality is paramount in soldering applications. One of the striking advantages of ultrasonic soldering is the enhanced quality of joints formed. This technique fosters superior metallurgical bonds because it effectively removes surface contaminants during the joint formation process. The mechanical vibrations disrupt oxides and impurities, enabling cleaner and tighter joints when compared to traditional techniques.
- Stronger joints: The resultant bonds are often more resilient, further extending product lifespan and reliability.
- Consistent results: Compared to traditional methods where variations can occur due to operator skill, ultrasonic soldering provides consistency.
- Reduced defects: The faster joint formation reduces the chances of defects that often propagate in long soldering processes.
This combination of superior cleanliness and strength ultimately results in components that perform better under stress and require less frequent replacements.
Operational Costs
While it may seem that the initial investment in ultrasonic soldering equipment is higher, a deeper analysis reveals potential long-term savings. Operational costs may decrease due to several factors:
- Lower energy consumption: Ultrasonic soldering generally uses less energy due to its efficiency.
- Reduced soldering material: The requirement for flux is minimized, thus lowering the material cost over time.
- Durability of the joints: With increased joint quality, products that rely on ultrasonic soldering are less likely to fail, reducing warranty claims and repairs.
Applications of Ultrasonic Soldering
In the ever-evolving landscape of manufacturing technologies, ultrasonic soldering stands out for its remarkable versatility. This method, at its core, leverages high-frequency sound waves to enable precise soldering, minimizing the risk of damaging sensitive components. The applications of ultrasonic soldering are not just confined to one sector; they span across various industries, each experiencing unique benefits. Understanding these applications can illuminate its significance in today’s manufacturing processes, helping professionals make informed decisions.
Electronics Manufacturing
Electronics manufacturing remains the most prominent domain for ultrasonic soldering. This method addresses the need for speed and precision, particularly in assembling microelectronics and PCB (printed circuit board) connections. In traditional soldering, the high temperatures can jeopardize the integrity of delicate components. Ultrasonic soldering offers a solution here, allowing for lower thermal exposure, which is crucial for components that are heat-sensitive.
The process enhances the reliability of joints, resulting in improved overall product quality. For instance, mobile phones, laptops, and other consumer electronics adopt this technique to ensure the longevity of their internal connections. According to a report from the IEEE, ultrasonic soldering can reduce assembly time by as much as 25%, accelerating production without compromising on quality.
Moreover, the minimal usage of flux in ultrasonic soldering not only reduces costs but also leads to cleaner manufacturing processes. The technology’s ability to create consistent joints enhances consumer trust in product reliability, making it a favored method in the electronics landscape.
Medical Device Assembly
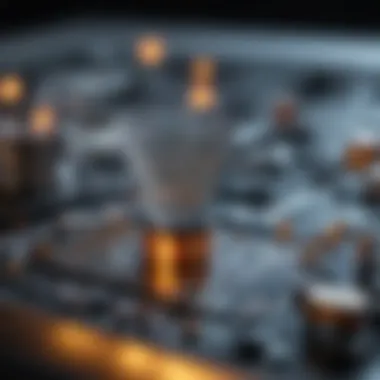
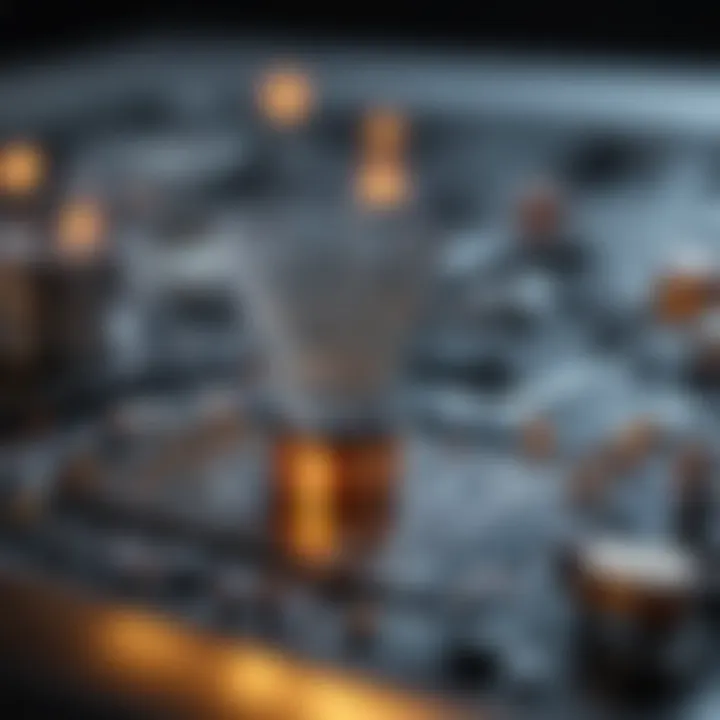
In the medical field, precision can be a matter of life and death. Here lies another significant application for ultrasonic soldering. The medical device industry is notorious for its stringent regulations and high-performance standards. Ultrasonic soldering meets these challenges effectively by providing a process that ensures robust and reliable connections within devices like catheters, surgical instruments, and diagnostic equipment.
Ultrasonic soldering also simplifies the assembly of complex components. For example, when producing implants or other devices requiring biocompatibility, using high temperature can lead not only to material degradation but also to compromised functionality. The ultrasonic method helps mitigate these risks by allowing for cleaner joints without excessive thermal stress.
Additionally, the adaptability of ultrasonic soldering means that different materials can be joined together seamlessly. For instance, combining plastic and metal elements in a device using ultrasonic methods enables manufacturers to innovate and develop new treatment tools or devices that adapt to varying medical needs. It’s a technology that not only optimizes manufacturing but also enhances patient safety and device reliability.
Automotive Industry
The automotive industry has rapidly embraced ultrasonic soldering, particularly for electronic components integral to vehicle operation and safety. Sensors, control units, and wiring harnesses are just a few examples of where this technology shines. The ever-increasing complexity of modern vehicles necessitates a soldering method capable of high precision, and ultrasonic soldering boldly fits that bill.
In terms of safety, minimizing thermal impact during soldering can significantly enhance the durability of electronic assemblies. This is particularly important for components exposed to varying temperatures or environmental conditions, such as those found in engine bays or external sensors.
Additionally, ultrasonic soldering contributes to sustainability efforts in the automotive sector. With rising awareness of environmental implications, manufacturers are seeking methods that reduce material waste and energy consumption. The efficiency of ultrasonic soldering aligns well with these goals, enabling faster production cycles while also accommodating complex designs that traditional methods might struggle to achieve.
"Ultrasonic soldering not only revolutionizes manufacturing techniques but also aligns with sustainability goals in multiple industries, proving its multidimensional capacity."
In summary, the applications of ultrasonic soldering extend significantly beyond mere production techniques. Whether in electronics, medical devices, or automotive manufacturing, this method provides critical advantages that improve performance, sustainability, and reliability—paving the way for innovation across various fields.
Advantages of Ultrasonic Soldering
Ultrasonic soldering presents a compelling case in modern manufacturing landscapes. Its unique characteristics come together to offer several significant advantages over traditional techniques. This process is essential not just for its efficiency but also for the quality it brings to different industries. In this section, we’ll delve deeper into the benefits that make ultrasonic soldering a leader in the realm of assembly and soldering solutions.
Reduced Thermal Impact
A significant concern in soldering has always been the thermal stress imposed on components. Ultrasonic soldering mitigates this through its low operational temperatures.
- Lower Heat Levels: The energy generated through ultrasonic vibrations reduces the need for high temperatures that conventional soldering requires. Consequently, sensitive electronic parts are less likely to suffer damage or derating.
- Material Preservation: Different materials, such as plastics or heat-sensitive substrates, can experience structural weakness when exposed to excessive heat. Using ultrasonic soldering, manufacturers maintain the integrity of such materials, allowing for more diverse applications.
The thermal benefits help to prolong lifespan and reliability in electronic devices. As a result, manufacturers witness a decrease in warranty claims and repairs, leading to increased customer satisfaction.
Minimal Flux Requirements
Traditional soldering typically relies on flux to promote wetting and reduce oxidation. Ultrasonic soldering sidesteps much of this hassle.
- Reduced Contamination: With lower or even no flux needed, the process results in cleaner finishes. This reduces the potential for defects or functionality issues caused by flux residue.
- Simplified Cleanup: Fewer flux materials mean less cleaning afterwards, streamlining the entire manufacturing process and reducing labor costs.
This not only simplifies the production but also results in a more environmentally friendly process, as the need for chemical cleaning agents is minimized. It aligns with the growing emphasis on sustainability in manufacturing.
Enhanced Control and Precision
Control and precision define the quality of any soldering joint. Ultrasonic soldering stands out in this regard, offering precise manipulation of the soldering process.
- Fine-tuning the Parameters: Operators can adjust ultrasonic frequency, amplitude, and duration to optimize each solder join. This flexibility allows for tailored approaches depending on the specific task at hand.
- Consistency and Repeatability: A consistent application of ultrasonic energy leads to uniform bonds. This reliability is particularly crucial in high-stakes environments such as medical device assembly or aerospace manufacturing, where tolerance levels are considerably stringent.
Every detail matters, and ultrasonic soldering addresses this with finesse, paving the path toward superior reliability in manufacturing products.
Ultrasonic soldering is not just a technology; it's a game-changer that redefines how industries view soldering efficiency and quality.
With these advantages, it becomes clear that ultrasonic soldering initiates a shift in perspective on how manufacturers can leverage cutting-edge technology to solve long-standing challenges. The strategic benefits not only elevate production quality but also align with market demands for sustainability, efficiency, and precision.
Challenges in Ultrasonic Soldering
While ultrasonic soldering offers a multitude of benefits, it isn't without its own set of hurdles. Understanding these challenges is crucial for anyone looking to implement this technology. They span various dimensions including material compatibility and the costs associated with the equipment involved.
Material Compatibility
One significant challenge in ultrasonic soldering relates to material compatibility. Not every material can withstand the unique conditions produced by ultrasonic waves. The energy emitted can induce significant vibrations that may not be suitable for all components. For instance, some materials might experience unwanted deformation or thermal degradation when exposed to the high-intensity ultrasonic field.
Manufacturers must conduct thorough testing to ensure that both the solder and base materials can withstand the ultrasonic process without compromising structural integrity. This often necessitates a clear understanding of the physical and chemical properties of the materials involved. Components made from plastics, for instance, may melt or warp under such conditions, while other metals could exhibit poor adhesion, jeopardizing the quality of the solder joint.
In addition, variability in material thickness can further complicate matters. If components vary significantly in thickness, it can create issues with solder penetration, making it difficult to achieve a reliable bond.
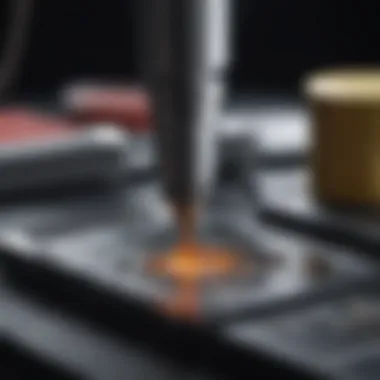
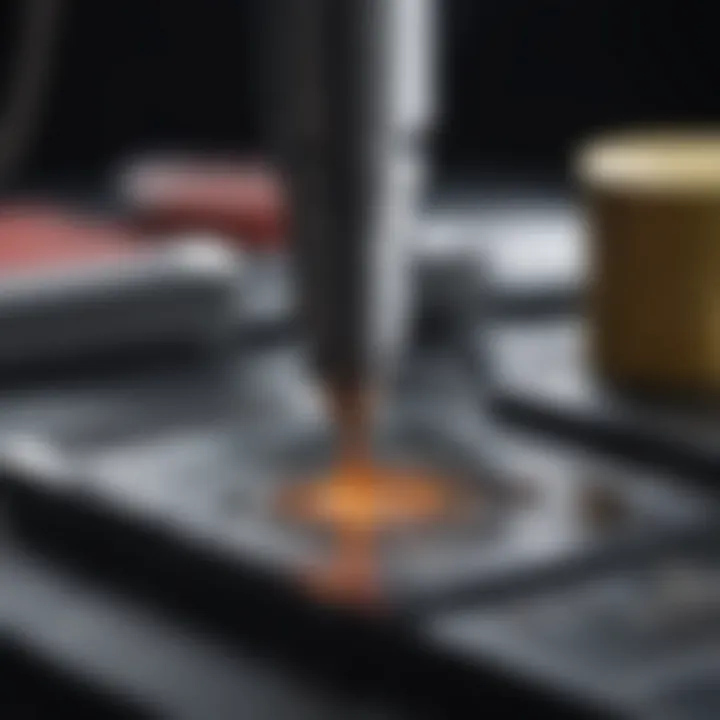
Equipment Costs and Maintenance
When it comes to equipment costs and maintenance, the initial investment in ultrasonic soldering equipment can be steep. The specialized machines—incorporating advanced transducers and other components—require not just a considerable upfront expense but also ongoing maintenance costs. The equipment must be kept in optimal condition to avoid unexpected breakdowns.
Regular calibration is key here. If the transducer isn't functioning at its peak, it can lead to inadequate soldering, making proper maintenance paramount. Moreover, the complexity of these machines makes training equally critical. Staff must be well-trained to manage both operation and troubleshooting to maximize the return on investment.
Ultimately, while ultrasonic soldering brings exciting advancements and potential efficiencies to manufacturing, the challenges associated with material compatibility and equipment maintenance cannot be overlooked. Addressing these issues head-on is essential for the successful integration and long-term viability of ultrasonic soldering processes in various industries.
Recent Innovations in Ultrasonic Solder Technology
The evolution of ultrasonic solder technology has seen remarkable strides, enhancing its practicality and effectiveness across various industries. As we step deeper into the world of tech, innovations in this field not only push the envelope but also redefine manufacturing standards. Understanding these advancements is critical for those engaged in electronics and production. The significance of these innovations cannot be overstated, as they serve to increase efficiency, enhance precision, and improve the overall quality of soldered joints, ensuring that modern demands are met with robust solutions.
Advancements in Transducer Design
Transducers play a pivotal role in ultrasonic soldering, acting as the primary interface that converts electrical energy into ultrasonic waves. Recent advancements in transducer design have been nothing short of groundbreaking. New materials and engineering techniques have emerged, leading to greater energy efficiency and durability.
- Materials Innovation: New materials like piezoelectric ceramics have elevated the performance of transducers. These materials not only enhance the conversion efficiency but are more resilient under high temperatures and pressures, ensuring longevity.
- Miniaturization: The trend towards smaller, more compact designs has allowed for integration into increasingly intricate electronic assemblies. This miniaturization enables flexibility in design while maintaining performance efficiency.
- Tuning Techniques: Innovations in tuning mechanisms mean that transducers can now be adjusted more precisely to match the specific requirements of different soldering applications. This allows manufacturers to achieve optimal performance in diverse settings, from delicate components in medical devices to heavy-duty automotive parts.
"The advancements in transducer design are not merely incremental; they represent a robust leap forward in reliably conducting high-precision soldering tasks."
Integration with Automation
As industries lean more toward automation, the integration of ultrasonic soldering with automated processes has begun reshaping manufacturing floors. Automated systems enable faster production cycles, improved quality control, and substantial cost reductions.
- Robotic Arm Integration: Ultrasonic soldering tools can now be seamlessly integrated with robotic arms, allowing for high-speed, repeatable soldering across various production lines. With vehicles or healthcare devices requiring higher precision, this synergy significantly improves output quality.
- Smart Manufacturing: Coupled with IoT technologies, ultrasonic soldering machines can be monitored and controlled remotely, allowing real-time adjustments and diagnostics. This ensures any arising issues can be addressed promptly, reducing downtime.
- Data Analytics: Incorporating data analytics within these systems promotes continuous improvement. By analyzing soldering quality metrics, manufacturers can refine their processes and achieve better outcomes on future production runs.
As ultrasonic solder technology becomes more sophisticated, its innovations are paving the way for a future filled with potential, transforming how we view soldering in modern manufacturing.
Future Trends in Ultrasonic Soldering
The sector of ultrasonic soldering is evolving rapidly, influenced by both technological advancements and changing market demands. Understanding these future trends not only highlights areas for growth but also illustrates how the technology continues to adapt to meet the needs of various industries. This section delves into key emerging markets and the increasing emphasis on sustainability in ultrasonic soldering practices.
Emerging Markets and Applications
Ultrasonic soldering is carving out significant niches across many industries, with some markets showcasing faster growth than others. The demand for precision and efficiency in manufacturing is a common thread connecting these markets, as they seek innovative solutions that can maintain quality while reducing overhead costs.
- Consumer Electronics: This market is witnessing a surge in demand for smaller, more complex devices. Ultrasonic soldering plays a crucial role in assembling intricate components without the risks associated with traditional methods. The ability to make tiny and reliable joints ensures device longevity and performance.
- Renewable Energy: As the world shifts towards more sustainable energy sources, ultrasonic soldering finds its place in manufacturing solar panels and wind turbine components. The technology’s ability to work with different types of materials without excessive heat makes it ideal for sensitive components in renewable installations.
- Aerospace and Defense: Stringent requirements for reliability and weight reduction in aerospace components are propelling the adoption of ultrasonic soldering. The technology’s low thermal impact is crucial for maintaining the integrity of lightweight materials used in aircraft and spacecraft.
"In a world striving for innovation, ultrasonic soldering offers a solution that is both forward-thinking and efficient."
These emerging markets indicate a broader trend where efficiency and precision become the benchmarks for success. As industries continue to innovate, the role of ultrasonic soldering will become even more pivotal.
Sustainability Considerations
Another significant trend shaping the future of ultrasonic soldering is the heightened focus on sustainability. Manufacturers are examining their practices closely, attempting to balance productivity with environmental responsibility. Here are a few considerations that underscore this shift:
- Reduction of Material Waste: The precision offered by ultrasonic soldering translates into considerably lower material wastage. Precision soldering means that less solder is used, minimizing excess material and reducing costs in the long run.
- Lower Energy Consumption: Ultrasonic soldering typically requires less energy compared to traditional soldering methods. As operations become more energy-efficient, they contribute to a reduction in carbon footprints. This is a direct benefit for companies committed to sustainable manufacturing practices.
- Minimal Toxic Emissions: As traditional soldering processes can involve toxic materials such as lead, ultrasonic techniques often lead to cleaner operations. The reduced need for flux and lower operating temperatures make ultrasonic soldering a more environmentally-friendly alternative.
By addressing these sustainability aspects, the ultrasonic soldering industry is well-poised not only to innovate but also to lead by example in adopting greener practices. As companies embrace these trends, ultrasonic soldering is expected to flourish, supporting both the manufacturing quality and the global effort towards sustainability.
Closure
The topic of ultrasonic soldering holds a pivotal place in the current landscape of manufacturing and electronics. As industries strive for efficiency and precision, the merits of ultrasonic soldering become increasingly apparent. This method not only offers faster production times compared to traditional techniques but also significantly enhances the quality of solder joints. Through our exploration, we have identified several key elements that underscore the importance of this technology:
- Efficiency: Ultrasonic soldering technology reduces cycle times, allowing for swifter production rates.
- Quality: By minimizing thermal damage and improving joint strength, this method can result in more reliable products, which is crucial in sectors like healthcare and automotive.
- Versatility: From electronics to medical device assembly, the diverse applications of ultrasonic soldering highlight its adaptability to various materials and project needs.
"As the demands of modern manufacturing evolve, ultrasonic soldering stands as a beacon of innovation, guiding industries toward a more efficient future."
Summary of Key Points
In summarizing the insights gained from our exploration of ultrasonic soldering, we can highlight the following notable points:
- Principles of Operation: Ultrasonic soldering relies on high-frequency sound waves which create localized heat, allowing soldering without excessive heat exposure to sensitive components.
- Industries Impacted: Key markets benefitting from this technology include electronics manufacturing, medical device assembly, and the automotive industry—each requiring distinct qualities from soldering processes.
- Challenges: We've also acknowledged challenges such as material compatibility and the necessary investment in sophisticated equipment.
- Future Innovations: The recent advancements in ultrasonic technology and its seamless integration with automation point towards a promising future.
The Future Outlook of Ultrasonic Soldering
Looking ahead, the future of ultrasonic soldering appears promising, shaped by emerging technologies and evolving market needs. As industries increasingly pursue sustainable practices, ultrasonics aligns well due to its lower resource consumption and reduced material waste. The focus is shifting toward:
- Emerging Market Opportunities: Sectors like renewable energy and smart technology are anticipated to drive demand for advanced soldering methods.
- Technological Enhancements: Ongoing developments in transducer technology and automation are expected to increase efficiency and reduce costs, making ultrasonic soldering accessible to even smaller businesses.
- Sustainability Integration: With a growing emphasis on eco-friendly manufacturing, ultrasonic soldering’s capacity for minimal thermal impact can contribute significantly to sustainability goals.