Understanding 3D Printing Mechanisms and Applications
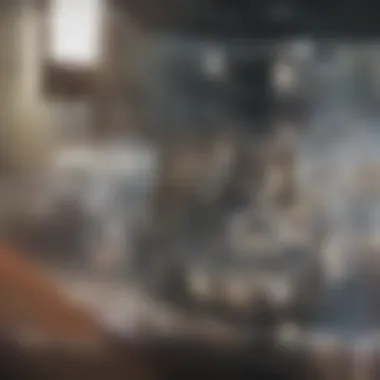
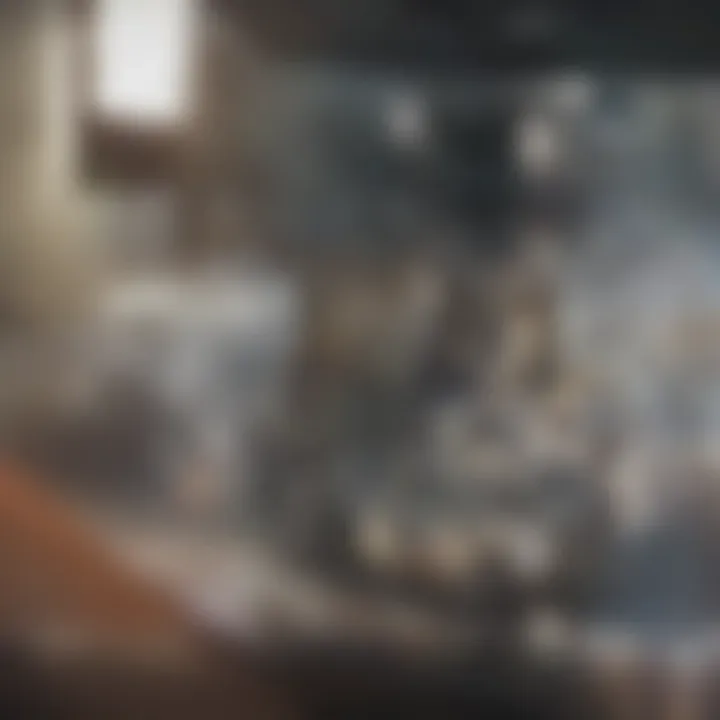
Intro
3D printing is a captivating and rapidly evolving technology. It reshapes how products are designed and manufactured. Understanding how this technology works is crucial for students, researchers, educators, and professionals engaged in various fields. This guide aims to unravel the underlying mechanisms of 3D printing, exploring its operational methodology, key components, and diverse materials. By doing so, it seeks to highlight the relevance of 3D printing in modern education, manufacturing, and innovation.
This article will explore the intricacies of the technology. The journey will begin with recent advances, detailing the latest discoveries and technological innovations shaping the 3D printing landscape. Following that, a discussion on methodology will reveal how researchers collect data and design studies to better understand this field. Each section aims to provide insightful details for readers looking to deepen their knowledge in this transformative area.
Prelude to 3D Printing
The rapid rise of 3D printing is altering numerous industries, rendering it a pivotal topic in both technological and academic spheres. Understanding the mechanisms behind this innovative technology is essential for educators, researchers, and professionals who wish to stay informed and competitive in their fields. This section delves into the core concepts of 3D printing, shedding light on its significance and practical implications in today's world.
Definition and Overview
3D printing, often called additive manufacturing, is the process of creating three-dimensional objects from a digital file. It involves laying down successive layers of materials until the desired object is achieved. This method contrasts sharply with traditional manufacturing practices, which typically involve subtracting material from a solid block. The ability to produce complex shapes and designs directly from digital sketches without the need for extensive tooling provides distinct advantages.
Moreover, 3D printing offers flexibility in design. Changes can be easily implemented in the digital design without extensive retooling, thus allowing for rapid prototyping. This means that ideas can transition to tangible products much quicker than in conventional settings. Applications span various fields, including healthcare, aerospace, automotive, and consumer goods, highlighting the versatility and potential of this technology.
Historical Context
The origins of 3D printing can be traced back to the early 1980s. Chuck Hull, an American engineer, created the first functional 3D printer in 1983, developing a technique called stereolithography. This technique used ultraviolet light to harden liquid resin layer by layer, forming solid objects. Over the years, the field has grown, with advancements leading to various methods of 3D printing, including Fused Deposition Modeling and Selective Laser Sintering.
As technology advanced, the costs associated with 3D printing began to decrease, making it accessible to smaller businesses and individual users. By the late 2000s, desktop 3D printers began to emerge, enabling hobbyists and entrepreneurs to explore 3D printing at home or within small companies. This democratization of technology has fueled innovation and creativity, providing opportunities for new startups and advancing research in various scientific fields.
"3D printing is not just a trendβit's a platform for innovation."
Understanding the historical context helps to appreciate the evolution of 3D printing and its current relevance. Today, it continues to evolve rapidly, influencing manufacturing processes and encouraging new business models with significant potential for future growth.
Core Principles of 3D Printing
Understanding the core principles of 3D printing is essential for grasping how this technology transforms various industries. These principles form the foundation of how objects are created layer by layer, which is the hallmark of additive manufacturing. This section will clarify these principles, including the additive manufacturing process, digital modeling, and layering techniques. Each element is vital for accurately producing complex shapes and functional parts.
Additive Manufacturing Process
The additive manufacturing process is the central concept behind 3D printing. Unlike traditional subtractive methods, which remove material to create an object, additive manufacturing builds it up from nothing. This method allows for complex geometries that would be impossible to achieve otherwise. The process generally involves designing a 3D model with specialized software, which is then sliced into thin layers for printing.
One significant benefit of this method is material efficiency. As only the necessary material is used, there is less waste compared to traditional manufacturing techniques. Furthermore, additive manufacturing encourages innovation in design and functionality, as engineers and designers can create parts tailored to specific needs.
Digital Modeling
Digital modeling serves as the starting point for any 3D printed object. This process involves creating a virtual blueprint of the desired item using Computer-Aided Design (CAD) software. The accuracy of this model is crucial, as it dictates the final output. By manipulating geometrical parameters, designers can experiment with different shapes and sizes.
Moreover, the choice of software impacts the design capabilities. Some tools offer advanced features like simulation, which allows users to visualize how the design performs under stress before it's even printed. This negates potential errors and improves efficiency, making the digital modeling stage a critical step in the 3D printing workflow.
Layering Techniques
Layering techniques are at the very heart of 3D printing. In the additive manufacturing process, the object is constructed layer by layer, starting from the base up. This technique allows for intricate details and structures.
Different technologies employ various layering methods. For instance, Fused Deposition Modeling (FDM) extrudes melted plastic to form each layer, while Stereolithography (SLA) uses ultraviolet light to cure resin layer by layer. Each technique presents unique advantages and is suited for different applications. Thus, understanding these methods provides insight into the capabilities and limitations of 3D printing.
"The adaptability of layer-based construction dramatically enhances design flexibility, allowing for the creation of virtually any shape."
In summary, the core principles of 3D printing encompass the innovative additively driven manufacturing process, effective digital modeling, and strategic layering techniques. Grasping these principles is crucial for anyone looking to implement or study this transformative technology effectively.
Types of 3D Printing Technologies
Understanding the different 3D printing technologies is crucial for grasping how this method operates across various industries. Each technique has its unique processes, benefits, and practical considerations. Recognizing these can help users to select the most suitable technology based on their specific needs, whether they are educators, students, researchers, or industrial professionals.
Fused Deposition Modeling (FDM)
Fused Deposition Modeling, or FDM, is one of the most widely used 3D printing technologies. It works by melting thermoplastic filaments and extruding them layer by layer to create a 3D object. This method is popular due its affordability and accessibility. It allows for a wide range of materials, especially common plastics like PLA and ABS.
Key aspects of FDM include:
- Cost-Effectiveness: FDM printers are often less expensive than other types of 3D printers, making them ideal for schools and small businesses.
- Ease of Use: Many FDM printers come with user-friendly software, which helps novices get started quickly.
- Material Versatility: Besides standard filaments, some advanced FDM printers can use composite materials, enhancing functionality in end products.
However, FDM has limitations. The layer adhesion may not be as strong compared to other methods. Also, the precision might fall short in complex designs.
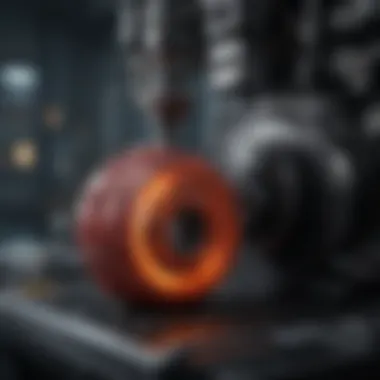
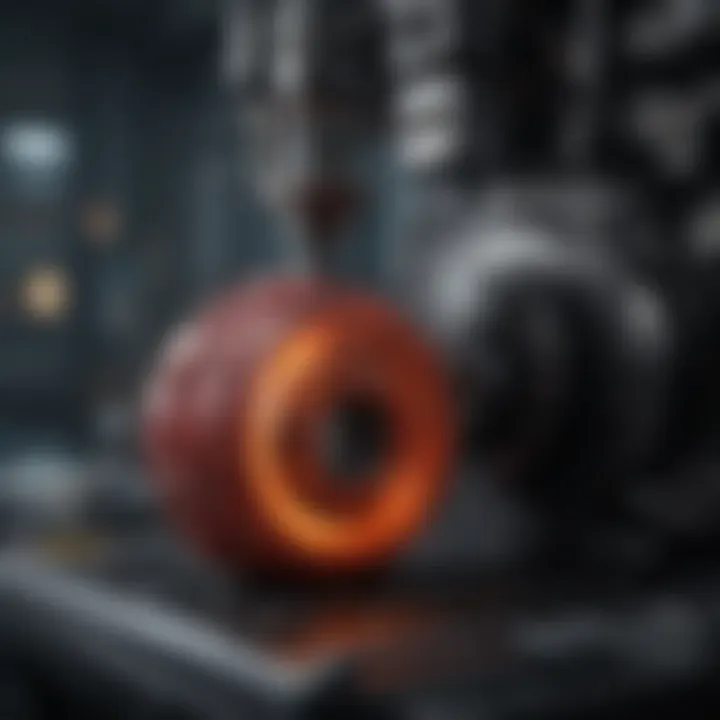
Stereolithography (SLA)
Stereolithography is another fundamental technology in the realm of 3D printing. It employs a laser to cure liquid resin into solid plastic, layer by layer. This method stands out due to its high precision and ability to produce intricate details.
Important considerations of SLA include:
- Detail Accuracy: SLA can create parts with very fine details, often suitable for prototypes and jewelry making.
- Surface Finish: The finish of SLA parts is typically smooth, reducing the need for extensive post-processing.
- Material Options: With various resins available, SLA can yield parts with unique properties, including flexibility or heat resistance.
Despite its advantages, SLA printing requires more careful handling. The materials are often more expensive, and post-processing can be more time-consuming. Additionally, resin can be toxic, necessitating proper safety measures by users.
Selective Laser Sintering (SLS)
Selective Laser Sintering utilizes a powerful laser to fuse powdered material into solid structures. It is recognized for its capability to produce highly durable parts that are functional and can serve in end-use conditions.
Points of interest regarding SLS include:
- No Support Structures: Unlike FDM and SLA, SLS parts can be printed without needing support structures, allowing for complex geometries that are challenging other methods.
- Material Variety: SLS works with multiple materials such as nylon, polyamide, and certain metals, allowing for versatility in applications from prototypes to production.
- Strength and Durability: Parts produced through SLS are known for their strength, making them preferable in industries like aerospace.
Nonetheless, SLS printers tend to have a higher cost of entry and operational price. They also require post-processing, which can involve additional steps like powder cleaning and finishing.
In summary, the choice of 3D printing technology is significant as each has its distinct advantages and limitations. Depending on the end application, understanding these technologies ensures that users can make informed decisions.
For further information about 3D printing technologies, visit Wikipedia.
Key Takeaways
- FDM is cost-effective and easy to use but may lack precision.
- SLA provides high accuracy and a smooth finish, with more expensive materials.
- SLS offers durability and complex design possibilities but has a higher operational cost.
Materials in 3D Printing
The significance of materials in 3D printing cannot be overstated. The choice of material directly influences the capabilities of the printed object, including its durability, flexibility, and overall appearance. As the technology evolves, the range of materials utilized in 3D printing is expanding rapidly. This section examines the primary materials employed in 3D printing, highlighting their unique characteristics, advantages, and any considerations necessary for users.
Plastic Filaments
Plastic filaments are among the most common materials used in 3D printing, particularly in Fused Deposition Modeling (FDM). They come in various types, including PLA, ABS, PETG, and TPU. Each type offers distinct properties that make them suitable for different applications.
- PLA (Polylactic Acid):
- ABS (Acrylonitrile Butadiene Styrene):
- PETG (Polyethylene Terephthalate Glycol):
- TPU (Thermoplastic Polyurethane):
- Biodegradable and easy to print
- Ideal for beginners due to lower printing temperatures
- Less durable than other plastics, not suitable for high-temperature applications
- Known for its toughness and higher heat resistance
- Can be prone to warping during printing
- Commonly used for functional prototypes and automotive parts
- Good balance of strength and flexibility
- Resistant to moisture and chemicals
- Recommended for outdoor applications
- Highly flexible and durable
- Often used for parts that require elasticity or impact resistance
Metals and Alloys
Metal 3D printing has gained significant traction in recent years, especially in industries such as aerospace and automotive. Techniques like Selective Laser Sintering (SLS) and Direct Metal Laser Sintering (DMLS) are commonly employed to fuse metal powders into objects. Common metals used include titanium, aluminum, and steel.
- Titanium:
- Aluminum:
- Steel:
- High strength-to-weight ratio, excellent for aerospace applications
- Corrosion resistant but can be more expensive
- Lightweight and good thermal conductivity
- Used in automotive and machinery parts
- Strong and versatile; can be used for a wide range of applications
- Considered heavy but very durable
Metal 3D printing allows for complex geometries that are often impossible to create using traditional manufacturing methods. This provides greater design freedom but requires careful consideration of the printing process and material properties.
Bio-compatible Materials
Bio-compatible materials are essential for applications in the medical field. These materials must not only support the structure of a printed object but also interact safely with biological systems.
- PLA: Some PLA variants are approved for certain medical uses due to their biocompatibility.
- PCL (Polycaprolactone):
- Hydrogels:
- A highly biocompatible material that degrades slowly in the body
- Used for tissue scaffolds and in other biomedical applications
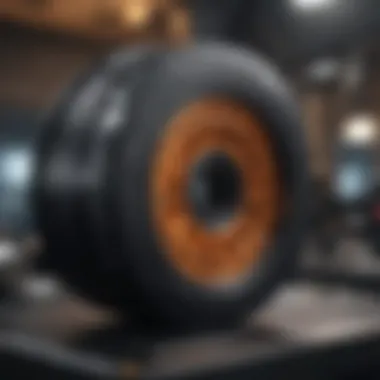
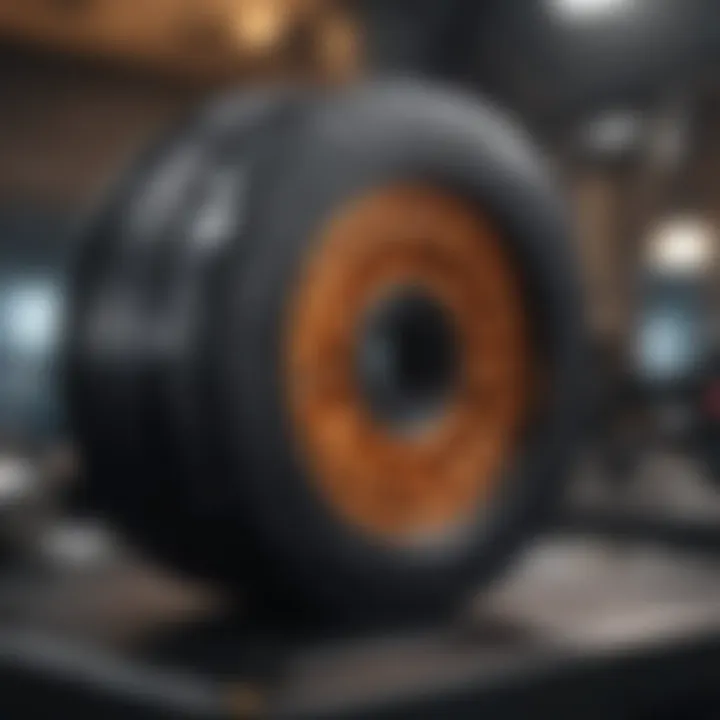
- Used in printing tissues and organs
- Mimics the natural environment of cells and supports cell growth
The development of bio-compatible materials opens new avenues in personalized medicine and regenerative therapies, reflecting the expanding potentials of 3D printing.
The advancement of material science will ultimately dictate the progression of 3D printing technology, influencing its applications across various fields.
The 3D Printing Workflow
The workflow in 3D printing is a critical sequence that transforms a digital model into a physical object. Understanding this workflow is essential for anyone involved in 3D printing, whether they are educators, students, or industry professionals. It encapsulates the entire process, emphasizing the importance of precision and collaboration between different stages. By focusing on three main componentsβdesign preparation, slicing software, and printer calibrationβthis section provides a clear perspective on how to maximize efficiency and ensure high-quality output in 3D printing projects.
Design Preparation
Design preparation is the initial step in the 3D printing workflow. It involves creating or selecting a digital model using Computer-Aided Design (CAD) software. This model must be suitable for 3D printing, which means it needs to meet specific criteria. For instance, the model should be manifold, meaning it must be a closed surface without holes or self-intersections.
While preparing a design, attention to detail is key. The scale of the model should match the desired size of the final product. Proper design consideration can prevent common mistakes, such as dimensional inaccuracies that could affect the fit of components in assembly. Additionally, support structures might be required based on the complexity of the design. Such preparations ensure that the final product will possess the intended properties and functionality.
"The success of the 3D printing process heavily relies on the quality of the initial digital model."
Slicing Software
After design preparation, the next phase is slicing. Slicing software converts the 3D model into a series of 2D layers. This step is crucial because it determines how the model will be printed. The slicing software will produce G-code, which contains instructions for the 3D printer regarding movement, extrusion speed, and layer height.
There are various slicing software options available, such as Ultimaker Cura and PrusaSlicer. Users should choose software compatible with their 3D printer. Optimization settings within the slicer can significantly influence the printing speed and quality. Therefore, understanding these settings is beneficial, allowing users to balance speed with quality.
This software can also help simulate the printing process to identify potential issues before actual printing begins. Such foresight can save time and resources.
Printer Calibration
The final component of the workflow is printer calibration. Proper calibration is vital for ensuring accurate prints. This process involves adjusting various printer settings to align the printer's hardware with the specified requirements from the sliced model. Key aspects include bed leveling, nozzle height, and temperature settings.
Bed leveling ensures that the build plate is level relative to the nozzle, preventing warping and adhesion issues. If this step is overlooked, the print can fail or have defects. Similarly, setting the correct nozzle height is crucial for achieving proper extrusion of the material. Each material might also require specific temperature settings, making it essential for users to refer to material guidelines.
Calibration may seem tedious but is necessary for achieving quality prints. Regular checks also maintain the printer's performance over time.
Applications of 3D Printing
The application of 3D printing in various fields demonstrates the technology's transformative potential and versatility. This section outlines how 3D printing is reshaping industries by enabling innovations, reducing costs, and improving efficiency. Understanding these applications gives insight into the significant role of 3D printing in modern practices and the future.
Medical Innovations
3D printing plays a critical role in the medical field. Its ability to create customized solutions is invaluable. Many hospitals now use 3D printing for orthopedic implants, dental products, and even prosthetics. Customization of these items can lead to better patient outcomes.
- Personalized Prosthetics: One breakthrough is in prosthetics. Each prosthetic can be tailored to an individual's anatomy. This personalization improves comfort and functionality.
- Surgical Models: Surgeons use 3D printed models to practice intricate procedures. Models created from patient data allow for better preparation, reducing complications during surgery.
- Bioprinting: Researchers are exploring bioprinting, which uses living cells to create tissues. This can pave the way for organ transplants in the future.
"3D printing in medicine is not just about creation, but also about customization and innovation."
Aerospace and Automotive Industries
In both aerospace and automotive industries, 3D printing is a key driver of efficiency. The capacity to rapidly prototype parts can significantly reduce development time. Components that are complex can be created in one piece, reducing the need for assembly.
- Weight Reduction: Industries aim for lighter components for fuel efficiency. 3D printed parts tend to be lighter without compromising strength.
- Supply Chain Optimization: Manufacturers can produce parts on demand, minimizing inventory costs and reducing lead time. This flexibility is essential in fast-paced industries.
- Innovative Designs: The design freedom allowed by 3D printing fosters new design methods. Complex geometries that were impossible with traditional methods can now be realized.
Consumer Products
Consumer products have also seen a considerable shift due to 3D printing. From bespoke fashion items to tailored household goods, the market has expanded significantly.
- Customization: Brands are now able to offer customizable products. For instance, shoe companies can create shoes based on a consumerβs foot measurements, improving fit and comfort.
- Rapid Prototyping: Companies can quickly develop prototypes to gauge market interest. This speeds up the design process and allows businesses to adjust based on consumer feedback.
- Local Production: With 3D printers becoming more accessible, small businesses can produce items locally. This reduces shipping costs and times, proving beneficial to both the company and consumers.
Challenges in 3D Printing
The role of 3D printing in various industries cannot be overstated. However, navigating the complexities of this technology poses multiple challenges. Addressing these issues is crucial for both practitioners and scholars to fully grasp the technology's potential and limitations. Understanding these challenges provides valuable insights into improving processes and informing future innovations. The focus on technical limitations, regulatory hurdles, and environmental concerns is essential. These elements not only affect production efficiency but also have broader implications for sustainability and compliance in a rapidly evolving landscape.
Technical Limitations
Technical limitations in 3D printing include issues with accuracy and resolution. Many printers cannot produce intricate designs without compromising the quality of the finished product. The choice of printer technology directly impacts the achievable precision. Additionally, materials used in printing often have constraints, limiting designs' viability and functionality. Unpredictable results may occur from faulty calibration or poor print settings. Regular maintenance becomes essential to ensure operational integrity.
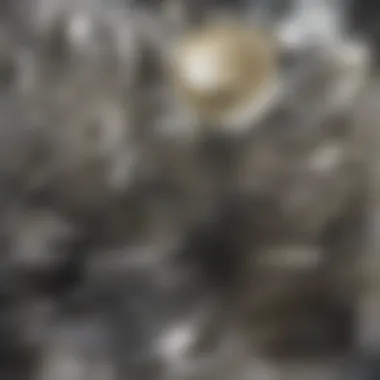
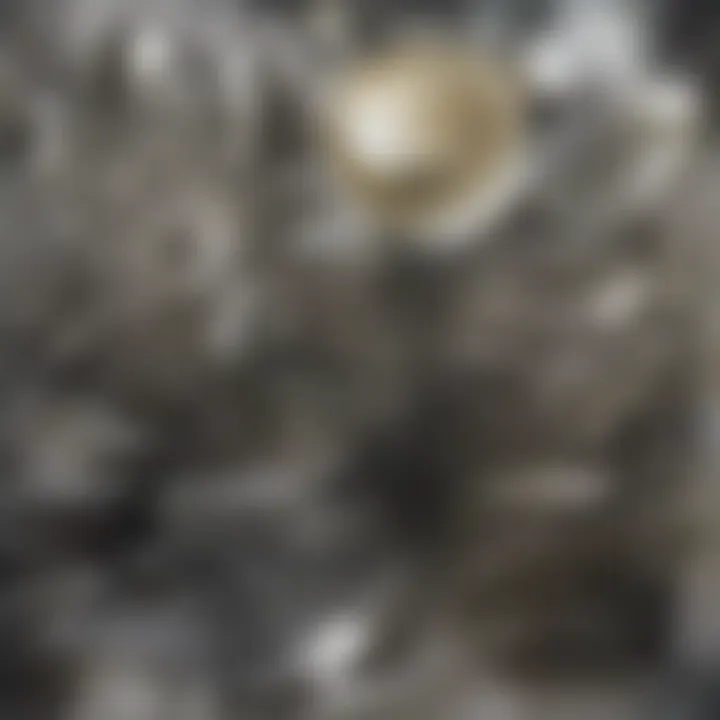
Some specific limitations include:
- Size restrictions: Many consumer-grade printers have volume limitations, which confine the scale of projects.
- Material compatibility: Not all materials work with every printer type, thus restricting options for designers.
- Print speed: Some processes like Stereolithography can take longer than desired, leading to delays in production schedules.
"As the field evolves, addressing these technical challenges will enhance the effectiveness of 3D printing across disciplines."
Regulatory Hurdles
Regulatory challenges in 3D printing stem from the lack of universally accepted standards. These hurdles can vary regionally. The absence of comprehensive guidelines can lead to inconsistencies in product quality and safety. Industries such as aerospace and healthcare face strict regulatory scrutiny. Ensuring compliance with safety standards is vital for market acceptance.
Legislative bodies are beginning to recognize the impacts of 3D printing but still lag behind innovation. Factors that must be considered include:
- Intellectual property: Issues arise over copyright and ownership of designs, complicating production scalability.
- Product liability: Determining who is liable for defective products becomes complex.
- Quality assurance: Establishing standards for quality control while maintaining creativity and flexibility in design.
Environmental Considerations
Environmental considerations pose a significant challenge in the realm of 3D printing. While additive manufacturing has the potential to reduce waste by using materials only where needed, the materials themselves can have adverse effects. Plastics used in most consumer-grade filaments can contribute to pollution if not managed properly. Additionally, the energy consumption of 3D printers raises concerns about the carbon footprint.
Important factors to keep in mind include:
- Material disposal: Ensuring sustainable disposal of failed prints or excess materials is crucial.
- Energy consumption: Understanding the energy requirements of printers can impact sustainability efforts.
- Life cycle analysis: Investigating the full environmental impact from production to disposal informs better choices moving forward.
Tackling these challenges is critical to ensuring that 3D printing technology continues to evolve in a positive and sustainable manner.
The Future of 3D Printing
The ongoing evolution of 3D printing technology holds significant potential for transforming various sectors. As new innovations emerge, understanding these developments is crucial for students, researchers, and professionals alike. This section will explore emerging technologies, examine potential market impacts, and discuss the importance of integrating 3D printing with other advanced technologies.
Emerging Technologies
One of the most exciting aspects of the future of 3D printing is the advent of novel technologies. Among these is multi-material 3D printing, which enables the creation of complex objects composed of different materials. This advancement allows for enhanced functionality and properties that are tailored for specific applications.
Another noteworthy technology is 3D bioprinting. It focuses on using living cells to create tissues and organs. This could revolutionize medical treatment, potentially addressing transplant shortages and organ failures.
Further, 4D printing is another innovative concept gaining traction. This involves materials that can change shape or function over time in response to environmental stimuli. Such capabilities could lead to self-assembling structures and responsive systems used in various industries, from automotive to healthcare.
Potential Market Impacts
The implications of these emerging technologies on the market are substantial. Increased adoption of 3D printing can lead to lower production costs, particularly in sectors like aerospace and automotive manufacturing. The capacity to produce lightweight parts can improve fuel efficiency, which is an important factor in reducing operational costs.
Moreover, customizability is a significant advantage of 3D printing. Consumers now expect personalized products tailored to their needs. The ability to create unique designs and structures on demand can enhance customer satisfaction, prompting a shift in traditional manufacturing models.
"3D printing is not the future of manufacturing; it is the present that will redefine how we produce and consume goods."
In addition, as supply chains become more complex, localized manufacturing through 3D printing can minimize logistical challenges. This shift may lead industries to pursue more sustainable practices, reducing waste and resource consumption significantly.
Integration with Other Advanced Technologies
The future of 3D printing is also intertwined with other advanced technologies. The convergence with Artificial Intelligence (AI) is particularly promising. AI can optimize design processes, predict printing outcomes, and even manage supply chains more efficiently.
Additionally, the integration of Internet of Things (IoT) will enhance the monitoring of 3D printing processes. IoT can provide real-time data on production, which may increase efficiency and decrease errors during printing. This synergy will contribute to smarter manufacturing systems.
Lastly, blockchain could provide transparency in the supply chain related to 3D printing. It ensures that the materials used are ethically sourced and allows for secure transactions. This could play a key role in building consumer trust in products manufactured via 3D technologies.
Ending
The conclusion of this article plays a critical role in encapsulating the essence of 3D printing technologies and their significance across various fields. Exploring the multitude of applications, from medical innovations to aerospace engineering, this guide highlights how 3D printing techniques are revolutionizing traditional manufacturing processes. It serves to synthesize the key insights and the extensive knowledge provided in the preceding sections.
In an era where efficiency and customization are vital, 3D printing stands out. This technology not only allows for rapid prototyping but also enables intricate designs that can be difficult or impossible to achieve using conventional methods. As a result, industries can significantly reduce lead times and costs while enhancing creativity and innovation.
Summary of Key Insights
Throughout this guide, we have examined numerous facets of 3D printing, including its core principles, materials used, and the various technologies available. Here are the essential points:
- Layered construction is central to 3D printing, allowing complex geometries.
- Materials such as plastics, metals, and bio-compatible substances were key to diverse applications.
- Additive manufacturing showcases significant advantages over subtractive methods in producing bespoke parts.
- Emerging technologies point toward exciting future possibilities, including enhanced materials and automation.
Overall, the adaptability and innovation tied to 3D printing promise to reshape production as we know it.
Reflection on Industry Shifts
The landscape of manufacturing is continually changing, and 3D printing is at the forefront of this transformation. As traditional techniques face limitations, companies are increasingly incorporating 3D printing into their operations. This shift allows for reduced waste and better resource utilization, aligning with sustainable practices that are increasingly demanded by consumers.
Moreover, the rise in education surrounding 3D printing technologies has broadened access to these tools. Students and professionals alike are now able to engage with this technology, fostering new ideas and applications. The integration of 3D printing in educational institutions contributes not only to technical skills but also to creative problem solving.