Understanding CKD Air Regulators in Pneumatic Systems
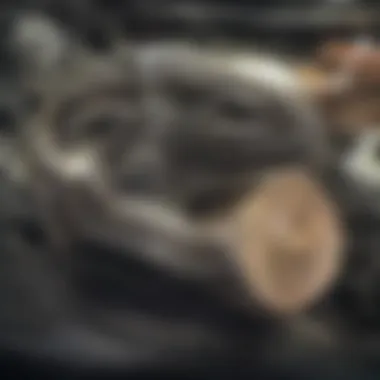
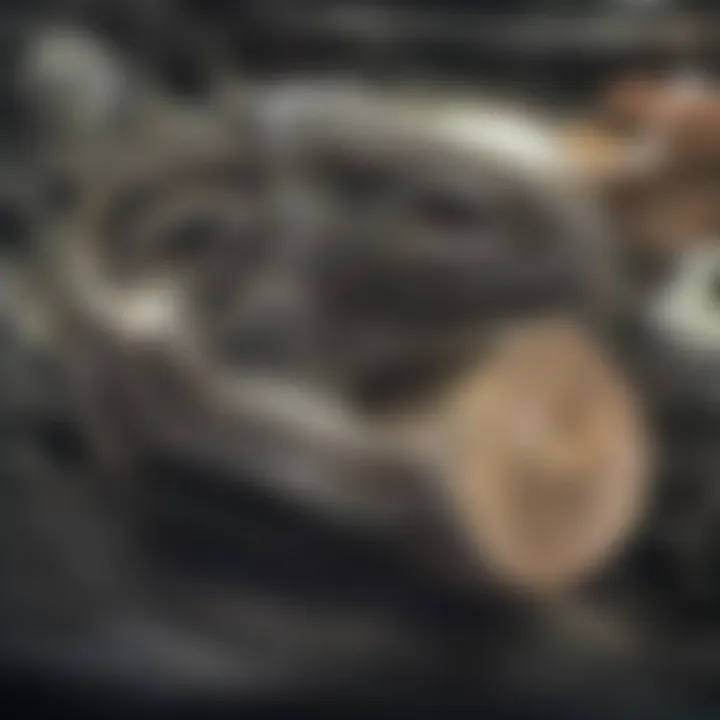
Intro
Understanding CKD air regulators is fundamental to grasping the nuances of pneumatic systems. These components regulate air pressure and flow in various applications, ensuring efficiency and reliability. Their role cannot be overstated, as improper regulation can lead to system failures or inefficiencies, which in turn can affect productivity and safety.
The significance of air regulation is evident in industries that rely heavily on pneumatic devices. Engineers and technicians depend on proper functionality to maintain optimal performance in systems such as assembly lines, packaging, and automation machinery. Given this importance, a systematic exploration of CKD air regulators offers valuable insights into their design, functionality, and operational context.
This article covers essential topics, including the advancements in CKD air regulators, their practical applications, and the methodologies related to selecting and maintaining these devices. Furthermore, it addresses relevant troubleshooting techniques and the future trends shaping this sector.
Recent Advances
Recent developments in the field of CKD air regulators mirror broader technological trends in engineering. This section will discuss the latest discoveries and technological innovations that have emerged, influencing their design and application.
Latest Discoveries
Research has revealed new materials that enhance the durability and efficiency of air regulators. For instance, lightweight alloys and advanced polymers are increasingly utilized to reduce weight without compromising strength. Such innovations not only improve performance but also extend the lifespan of the regulators, making them more cost-effective in the long run.
Another significant discovery lies in the precision of air flow measurement technologies. Enhanced sensors are now integrated into CKD regulators, providing real-time data that enable better control and efficiency in pneumatic systems. This advancement allows operators to adjust settings dynamically, leading to improved productivity.
Technological Innovations
The integration of digital technologies has revolutionized CKD air regulators. The advent of IoT (Internet of Things) enables remote monitoring and control of these devices. Operators can now track performance metrics and receive alerts about maintenance needs, reducing downtime and optimizing operational efficiency.
Furthermore, advancements in AI (Artificial Intelligence) are paving the way for predictive maintenance. By analyzing data trends, AI algorithms can determine when a regulator might fail, allowing timely interventions and avoiding costly breakdowns. Such innovations exemplify how CKD air regulators are evolving to meet the demands of modern industry.
Methodology
The study of CKD air regulators necessitates a robust methodology to ensure thorough understanding and accurate application. This section discusses research design and data collection techniques appropriate for this field.
Research Design
A systematic approach is essential when exploring CKD air regulators. This may involve both qualitative and quantitative methods. Qualitative research could involve interviews with industry experts, while quantitative research may focus on experimental setups to gather data on performance metrics.
Data Collection Techniques
Data collection for CKD air regulators can be done in various ways. Field studies are critical for observing real-world performance under different conditions. Additionally, laboratory testing gives insights into specific design features and their contributions to overall efficiency. Surveys can also be employed to gather user feedback on performance and areas of improvement.
Research in this area helps pinpoint effective applications and guides future developments in air regulator technology.
Intro to CKD Air Regulators
CKD air regulators play a vital role in the field of pneumatic systems, offering essential control over air pressure and flow. Understanding their functionality and applications is paramount for students, researchers, and professionals engaged in engineering and automation. The significance of CKD air regulators extends beyond mere technical specifications; it encompasses their historical roots and impact on modern technology.
Definition and Purpose
CKD air regulators are devices designed to maintain a consistent output pressure regardless of variations in input pressure or downstream demand. Their primary purpose is to ensure that pneumatic systems operate efficiently and reliably. By controlling the pressure of air supplied to actuators and other components, these regulators help to optimize performance and prevent potential system failures. Without effective regulation, fluctuations in air pressure can lead to instability, reduced performance, and increased wear on equipment.
Historical Development
The development of air regulators, including those manufactured by CKD, dates back to the evolution of pneumatic technologies. Initially, the reliance on mechanical devices limited the precision with which air pressure could be managed. With time, advancements in materials and engineering techniques have allowed for the creation of more sophisticated and reliable regulators. CKD, as a brand, has been instrumental in introducing innovations in design that cater to the demands of various industries, including manufacturing, robotics, and automotive. This historical framework establishes a foundation for understanding the complexities of modern air regulation technologies.
Relevance in Pneumatics
In pneumatic systems, the regulation of air pressure is crucial for maintaining effective operation of tools and machinery. CKD air regulators are relevant as they facilitate the proper functioning of components such as cylinders and valves. The modulation of air pressure impacts not only performance but also energy efficiency. As industries strive for higher productivity with lower environmental impact, the use of quality regulators becomes ever more significant. Additionally, with the rising complexity in automated systems, the demand for precise air management tools continues to grow.
"Effective regulation of air pressure is essential to achieving optimal performance in any pneumatic system."
Various sectors, including those emphasized by their dependency on pneumatic systems, benefit from the integration of CKD air regulators. Such devices enhance operational stability, prolong the lifespan of machinery, and contribute to overall efficiency. Understanding these fundamental concepts is essential for anyone looking to delve deeper into the intricacies of pneumatic engineering.
Technical Specifications of CKD Air Regulators
The technical specifications of CKD air regulators form the backbone of their functionality and efficacy. These specifications encompass several critical elements that not only dictate the performance of the regulators but also influence their applicability in various operational contexts. Understanding these details is essential for professionals and students alike, as it provides insights into the decision-making process when selecting an appropriate air regulator for specific needs.
Pressure Regulation Mechanism
A pivotal aspect of CKD air regulators is the pressure regulation mechanism. This mechanism ensures that the output pressure remains stable despite fluctuations in input pressure or varying flow demands. Typically, the pressure regulation is achieved through a diaphragm or piston system that adjusts the orifice size in response to changes in pressure.
In practice, pressure regulation mechanisms can be coarsely or finely tuned. Coarse tuning enables rapid adjustments for varied conditions, while fine tuning provides stability under constant conditions. It's crucial to select a regulation mechanism suited to the application's dynamic range; otherwise, it could lead to inefficiencies in the broader pneumatic system. Overall, the mechanism plays a crucial role in maintaining uniform pressure across pneumatic devices, which is essential for efficient operation.
Flow Characteristics
Flow characteristics describe how air or gas flows through the regulator and how those flow rates affect system performance. These characteristics are critical when it comes to system design and component compatibility. Factors such as maximum flow rate, pressure drop, and response time must all be taken into account.
A few flow characteristics to consider include:
- Flow Rate: Expressed in liters per minute or cubic feet per minute, it indicates the volume of air the regulator can handle efficiently.
- Pressure Drop: Understanding the difference in pressure before entering and after exiting the regulator is vital. A significant pressure drop may indicate limitations on flow rate and could necessitate adjustments to the pneumatic system.
- Dynamic Response: This relates to how quickly the regulator adjusts to changing demands. A slow response can lead to fluctuations and inefficiencies, compromising system performance.
Construction Materials and Durability
The longevity and reliability of CKD air regulators hinge on the materials employed in their construction. A robust design utilizing high-quality materials not only enhances durability but also improves performance. Common materials include aluminum, stainless steel, and various plastics.
Contemplating material choice involves assessments of:
- Corrosion Resistance: Regulators in harsh environments need materials resistant to corrosive elements, ensuring prolonged lifespan and consistent performance.
- Temperature Tolerance: Depending on the operating conditions, materials must withstand extreme temperatures without losing structural integrity.
- Mechanical Strength: High-pressure applications require materials with sufficient mechanical strength to avoid failure.
By prioritizing these specifications, professionals can select CKD air regulators that not only meet but exceed the demands of their specific industries.
Types of CKD Air Regulators
In pneumatic systems, understanding the variety and functionality of CKD air regulators is essential. Each type serves a distinct purpose and has unique characteristics, aligning with specific application needs. The selection of the right regulator can significantly impact system performance, efficiency, and reliability. By comprehending the different types of CKD air regulators, users can optimize their pneumatic setups and ensure consistent operation.
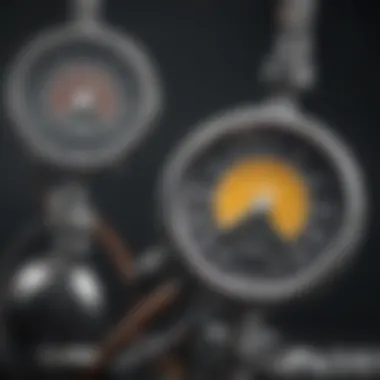
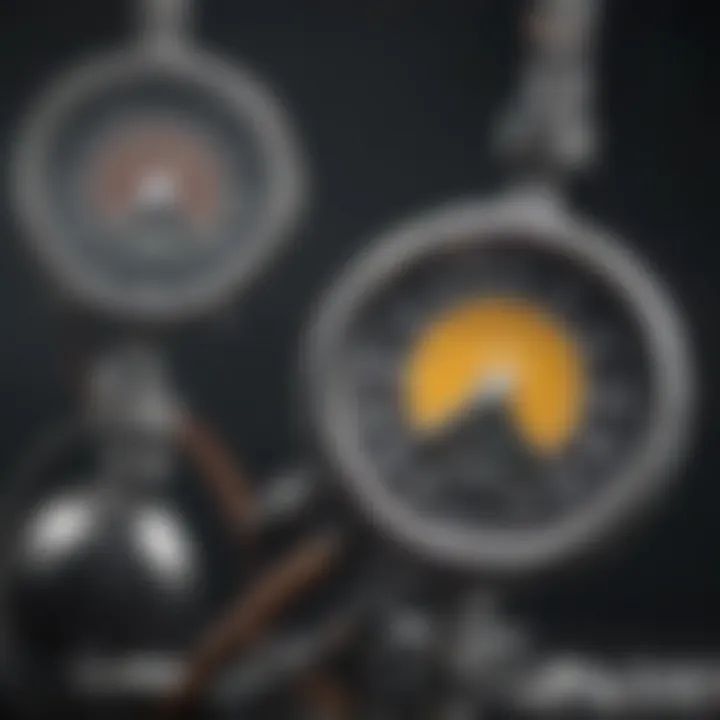
Standard Air Regulators
Standard air regulators are the most commonly used in various applications. They are designed to maintain a steady output pressure despite variations in input pressure. This functionality is critical in pneumatic systems where fluctuations can lead to equipment malfunction or inefficiency.
Key benefits of standard air regulators include:
- Stability: They provide consistent pressure, supporting sensitive equipment operations.
- Simplicity: Their straightforward design facilitates easier installation and maintenance tasks.
- Cost-Effective: Usually, they are less expensive compared to specialty regulators, making them accessible for many users.
Standard air regulators generally have a limited range of pressure regulation, which is adequate for many applications. However, users must ensure that the specifications align with their operational requirements to avoid issues such as pressure drops or surges.
Relieving and Non-Relieving Regulators
Relieving regulators are designed to manage excess pressure by venting it away, preventing potential damage to the system. This can be especially important in applications where pressure can easily exceed safe limits. On the other hand, non-relieving regulators do not vent excess pressure. They instead maintain output pressure by adjusting flow, often suitable for systems where pressure relief is not a concern.
Considerations when choosing between these types include:
- Safety Needs: If the system requires venting to avoid overpressure, a relieving regulator is essential.
- System Design: Non-relieving regulators can be integrated into more complex circuits without the need for pressure relief mechanisms.
Understanding the application environment is crucial when selecting between these two types. Users must assess the risks associated with pressure levels to make an informed decision.
Precision Regulators
Precision regulators offer high accuracy and responsiveness, particularly in applications demanding tight pressure control. They are equipped with advanced features that allow for fine-tuning of output pressure, making them ideal for sensitive equipment like actuators and pneumatic tools.
Advantages of precision regulators include:
- Accurate Control: They can maintain exact pressure levels, which is crucial for processes that rely on specific pressures.
- Quick Response: Their design allows for rapid adjustments to pressure changes, enhancing system responsiveness.
- Improved Performance: By providing stable conditions, they contribute to better overall machine functionality.
However, the complexity and cost of precision regulators are higher than standard ones. Users should evaluate if the additional performance justifies the investment.
"Selecting the right type of air regulator not only ensures optimal performance but also safeguards equipment integrity in pneumatic systems."
Applications of CKD Air Regulators
CKD air regulators play a pivotal role in a variety of applications across different sectors. Their function ensures consistent pressure and flow of air, which is crucial in pneumatic systems. An efficient air regulator can significantly improve performance while minimizing energy loss, making them indispensable in modern day engineering. Understanding the applications of CKD air regulators provides insight into their versatility and importance in industries.
Industrial Automation
In industrial automation, CKD air regulators contribute to the efficient operation of pneumatic actuators and tools. They maintain stable pressure levels, which leads to enhanced productivity and precision in manufacturing processes. For instance, they are used in assembly lines where robots need consistent force to perform tasks such as fastening or soldering.
The application of air regulators in this sector eliminates pressure fluctuations that can cause performance issues. By controlling air supply, CKD regulators help to reduce wear and tear on equipment, improving the overall lifespan of machines. Notably, their integration in automated systems contributes to lower operational costs through energy savings.
Robotics and Machinery
CKD air regulators are essential in the robotics and machinery realm. They ensure that robotic systems operate smoothly by providing regulated air pressure to components like pneumatic grippers and sensors. This consistency in airflow is vital for maintaining the functionality of these systems, which rely on precise movements and reactions.
Furthermore, the fine-tuning capability of CKD air regulators allows for programming of robots to perform complex tasks efficiently. As a result, they play a crucial role in enhancing the adaptability of robots across various functions, from material handling to intricate assembly tasks.
Packaging Sector
In the packaging sector, CKD air regulators facilitate the automation of packaging processes, ensuring that machines operate with the required air pressure for optimal performance. Packaging lines often use multiple pneumatic devices, such as conveyor belts and sealing machines, which require stable air supply to function effectively.
By controlling the air pressure, CKD regulators help to increase the efficiency of packaging operations. This leads to faster production rates and reduced downtime. Additionally, they play a significant role in minimizing product defects, as consistent pressure provides uniform sealing and filling processes.
"Efficient air regulation is crucial for achieving high standards in packaging quality and process reliability."
Choosing the Right CKD Air Regulator
Selecting the appropriate CKD air regulator is critical for ensuring optimal performance in pneumatic systems. The right choice impacts not just functionality but also efficiency and longevity of the entire system. It is essential to assess various factors before making a decision, as improper selection can lead to operational inefficiencies or even equipment failures.
Key Selection Criteria
When evaluating CKD air regulators, it is vital to consider several key criteria. These criteria include:
- Flow Rate: The regulator must support the required flow rate to maintain efficiency in the system. An inadequate flow rate can cause delays and affect the overall performance.
- Pressure Range: Understanding the operational pressure range is crucial. The selected regulator should work within the specific pressure limits of the application to avoid operational risks.
- Size and Port Configuration: The dimensions and port arrangements should match the systemβs requirements. Selecting the wrong size may incur additional costs or create installation challenges.
- Performance Features: Various features such as lockable adjustments or gauges can significantly improve usability. Selecting regulators with beneficial features may enhance day-to-day operations.
Compatibility with System Components
Compatibility with existing system components cannot be overlooked. A CKD air regulator must integrate seamlessly with valves, cylinders, and fittings used in the application. Ensuring compatibility can minimize the risk of leaks and system malfunctions. When assessing compatibility, consider factors such as:
- Operating Medium: Confirm that the materials of the regulator are suitable for the specific type of air or gas being used.
- Connection Types: Verify that the connector types on the regulator match those of other components in the system to facilitate easy installation and proper functioning.
- System Layout: Evaluate the physical orientation of the components in relation to the regulator. This ensures proper alignment and ease of access for maintenance.
Cost vs Performance Analysis
Conducting a cost versus performance analysis is a necessary step before finalizing the choice of regulator. While it might be tempting to select a regulator based solely on a lower price, this approach often overlooks essential performance aspects. Factors to scrutinize in this analysis include:
- Initial Costs: The up-front purchase price differs among models. However, understanding the long-term value is essential.
- Operational Efficiency: A more expensive regulator may offer better performance, leading to cost savings in operational expenses in the long run.
- Maintenance Requirements: Evaluate the ongoing maintenance costs associated with different models. Some regulators may require more regular attention, impacting overall expense.
Installation and Setup
The installation and setup of CKD air regulators are critical steps in ensuring effective operation within a pneumatic system. Proper installation not only enhances the performance of the regulator but also improves system reliability. Many factors influence how well the air regulator functions, which makes understanding the installation process necessary for optimal outcomes. A little attention during setup can lead to significant operational advantages.
Pre-Installation Considerations
Before beginning the installation of a CKD air regulator, several factors must be evaluated. These considerations help ensure that the regulator operates effectively and integrates seamlessly with the rest of the pneumatic system. Some of the essential pre-installation points include:
- System Compatibility: Ensure the air regulator matches the specifications of other components within the system.
- Location: Choose an installation site that allows for easy access for future maintenance and testing. Environments that are overly dusty or humid can impact performance.
- Pressure Ratings: Verify that the regulator can handle the necessary pressure ranges required for the system. This is paramount to avoid malfunction.
- Air Quality: Assess the quality of the compressed air being supplied. Contaminants can damage internal components, affecting the longevity of the regulator.
Each of these considerations directly impacts the longevity and efficiency of CKD air regulators.
Installation Process Overview
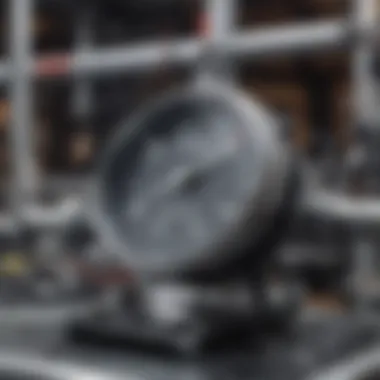
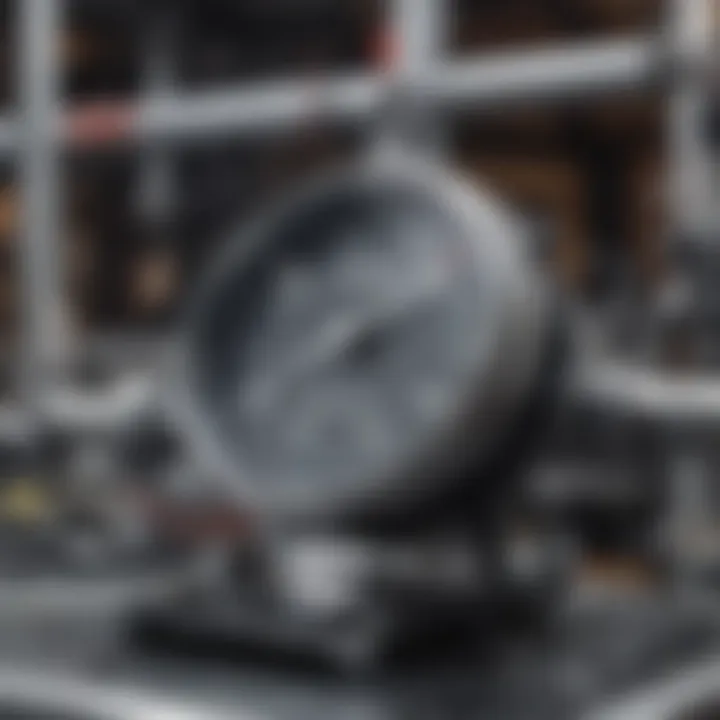
The actual installation of CKD air regulators involves straightforward steps but requires precision. Following these steps will set the foundation for successful performance:
- Prepare the Work Area: Clear the area of any obstructions and gather all necessary tools, including wrenches, sealant tape, and safety gear.
- Turn Off the System: Ensure the entire pneumatic system is turned off to prevent pressure release during the installation.
- Mount the Regulator: Secure the regulator to the designated bracket or surface, ensuring it aligns properly with existing piping. Tighten carefully without over-torquing to prevent damage.
- Connect Inlet and Outlet: Using the proper fittings and sealant tape, make the air connections. Ensure all fittings are sealed to avoid leaks.
- Configure Settings: Adjust the regulatorβs settings as per system requirements. This may include setting the desired output pressure based on system needs.
Following these steps systematically promotes a sound installation process.
Testing for Functionality
Once the installation is complete, testing the functionality of the CKD air regulator is essential to confirm it operates as intended. Functional testing helps identify any immediate issues that may be present.
- Check for Leaks: Before applying pressure, inspect all connections to ensure no leaks are present. This is crucial for a secure operation.
- Gradually Apply Air Pressure: Slowly increase the air pressure to allow the regulator to adjust to its working conditions. Monitor the output gauge closely for fluctuations.
- Inspect Output Pressure: Once the desired pressure is reached, verify that the regulator maintains it consistently. Any significant deviation may require re-evaluation of the installation or settings.
- Perform Regular Monitoring: After the initial test, regular checks can prevent future issues, ensuring the regulator functions within the required parameters.
"Effective installation and testing protocols are essential for maintaining the operational integrity of CKD air regulators."
In summary, installation and setup of CKD air regulators are vital for maximizing their efficiency in pneumatic systems. Attention to detail, thorough testing, and regular monitoring contribute significantly to long-term performance.
Maintenance of CKD Air Regulators
Maintenance of CKD air regulators is a crucial aspect that ensures their optimal performance and longevity. A well-maintained air regulator helps maintain consistent pressure and flow rates within pneumatic systems. This reduces the likelihood of system failures that can disrupt operations, leading to possible financial loss. Furthermore, regular maintenance can enhance safety by preventing dangerous malfunctions caused by uncontrolled air pressure.
Proper maintenance involves various tasks and checks that allow users to identify and resolve potential issues before they escalate. By investing time in routine care, operators not only extend the life of the equipment but also ensure the overall efficiency of the pneumatic system. This section delves into the primary maintenance tasks, signs of wear, and the process of replacing components.
Routine Maintenance Tasks
Routine maintenance tasks for CKD air regulators should occur on a regular schedule to ensure reliability. Here are some common tasks:
- Visual Inspections: Regularly check for any visible signs of damage, leaks, or corrosion.
- Cleaning Filters: Clean or replace filters to prevent contaminants from entering the system, which can affect the regulator's performance.
- Lubrication: Apply recommended lubricants to moving parts according to the manufacturerβs guidelines to ensure smooth operation.
- Pressure Checks: Monitor output pressure periodically to confirm that it remains within specified limits.
- Calibration: Regularly calibrate the regulator to maintain accuracy in pressure settings and ensure proper operation.
Performing these routine tasks can lead to improved reliability and reduced downtime in industrial systems.
Identifying Signs of Wear
Identifying signs of wear on CKD air regulators is paramount in ensuring the equipment's functionality. Some common indicators of wear include:
- Unusual Noise: Any strange or excessive noise during operation may signal mechanical wear or internal friction.
- Pressure Instability: Fluctuations in output pressure can indicate internal valve wear or blockage within the regulator.
- Visible Leaks: Any moisture or air escaping from the regulator can highlight seal or connection failures.
- Physical Damage: Cracks, dents, or corrosion on the regulator body should prompt immediate attention.
By recognizing these signs early, one can take action to prevent severe damage or failure.
Replacing Components
When routine maintenance or wear identification reveals that components need replacement, follow these general steps:
- Disconnect the Power Source: Ensure that the pneumatic system is off before starting the replacement process.
- Remove the Affected Component: Carefully disassemble the regulator to access the worn parts without causing damage to other components.
- Install New Parts: Use genuine CKD parts for replacements to maintain system integrity and performance. Ensure proper alignment and fit during installation.
- Conduct Function Testing: After the assembly, gradually reintroduce pressure and check for stability and leaks.
- Document Changes: Update maintenance logs to reflect any parts replacements, ensuring a comprehensive history of maintenance activities.
Following a systematic approach to component replacement will help maintain system efficiency and safety. Regular maintenance, awareness of wear signs, and proper component management contribute significantly to the performance and reliability of CKD air regulators.
Troubleshooting Common Issues
Troubleshooting common issues in CKD air regulators is essential for maintaining optimal performance in pneumatic systems. Knowledge of potential problems allows operators and maintenance personnel to address situations swiftly and effectively. With increasing reliance on pneumatic systems in various industries, understanding these issues becomes a priority to maximize productivity and reduce downtime. An efficient troubleshooting process can lead to enhanced performance while ensuring safety and reliability in operation.
Pressure Fluctuation Problems
Pressure fluctuations in pneumatic systems can lead to various operational inefficiencies. Such fluctuations may arise from several factors, including obstructed airflow, incorrect settings of the regulator, or faulty components. It is important to monitor the pressure consistently to ensure it remains within the specified limits for a given application.
- Identify the Source: Use pressure gauges to identify where the fluctuations occur. Examine pipes, fittings, and the regulator itself for signs of wear or damage.
- Adjust Settings: Check the regulator settings. Sometimes, adjusting the pressure output can help stabilize the fluctuations.
- Inspect Air Supply: Ensure that the air supply is clean and free of contaminants. Dirty air can cause irregular fluctuations.
By systematically addressing each factor, one can typically resolve pressure fluctuation problems.
Leak Detection and Repair
Leaks in air regulators can lead to inefficiencies and increased operational costs. Detecting leaks early is critical. Leaking air not only reduces system efficiency but can also lead to equipment malfunction or failure over time.
- Visual Inspection: Regularly inspect for any visible signs of leakage, particularly around fittings, joints, and seals.
- Soap Solution Test: A common method to test for leaks is to apply a soap solution to potential leak zones. When bubbles form, this indicates air leakage.
- Component Replacement: If a leak is detected, it may be necessary to replace seals or other components that are damaged.
Addressing leaks promptly can help maintain system efficiency and prolong the life of the equipment.
Insufficient Output Pressure
Insufficient output pressure is a common issue that can significantly affect system performance. This problem can stem from multiple sources, including blockages, malfunctioning parts, or improper regulator settings.
- Check Blockages: Begin by examining the air supply line, ensuring there are no blockages or restrictions.
- Regulator Settings: Confirm that the regulator is set to the correct output pressure. It is easy to overlook adjustments, particularly if maintenance personnel have changed system configurations.
- Inspect for Damage: Examine the regulator for signs of wear or damage. It may need reconditioning or replacement if internal components are compromised.
By addressing these aspects, one can typically restore the necessary output pressure for efficient operation.
Maintaining air regulators is not just about fixing issues but also about preventing them. Routine checks can often forewarn of potential failures, saving time and resources in the long run.
Future Trends in CKD Air Regulation Technologies
The future of CKD air regulators is intertwined with the evolving landscape of technology and sustainability. As industries seek efficiency and innovation, understanding these trends is critical. The advancements not only improve functionality but also enhance integration with existing systems. This section explores significant elements driving the future of CKD air regulation.
Advancements in Digital Control
Digital control systems are becoming increasingly important in the management of CKD air regulators. These systems offer precise pressure adjustments with real-time data feedback. They enable operators to monitor and optimize performance automatically.
Key benefits include:
- Enhanced Accuracy: Digital controls provide more accurate regulation of air pressure compared to traditional methods.
- Adaptive Response: Systems can respond dynamically to changes in demand or pressure fluctuations.
- Data Logging: The ability to log performance data enhances preventive maintenance practices.
As a result, manufacturers and operators can achieve better overall efficiency and reduce energy consumption.
Integration of Smart Technologies
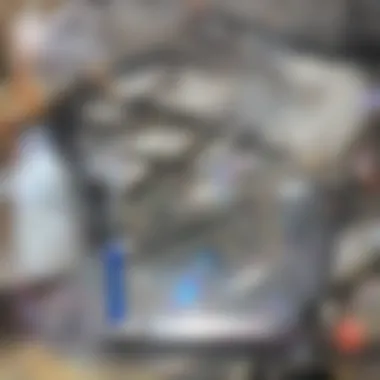
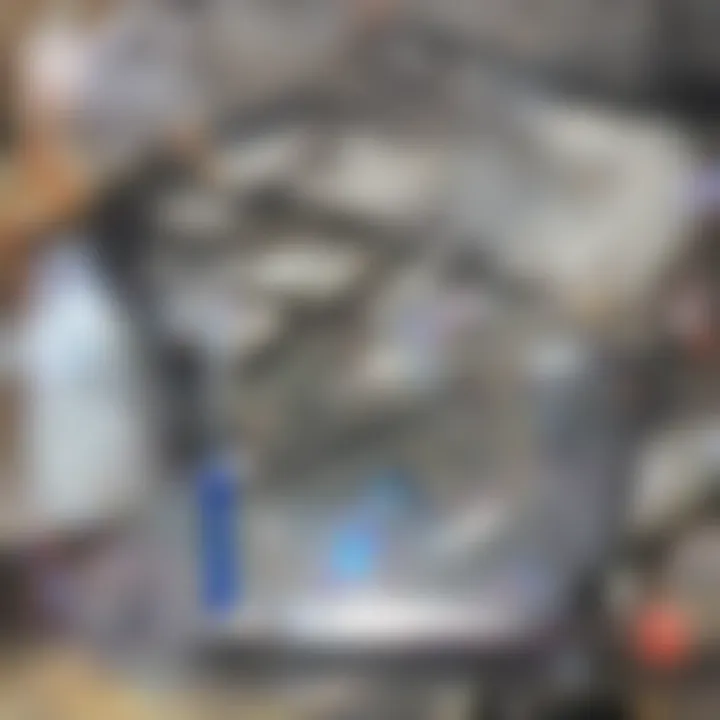
The integration of smart technologies with CKD air regulators is another pivotal trend. Smart technologies utilize sensors and the Internet of Things (IoT) to enhance system visibility and control. This connectivity allows users to analyze performance and make adjustments remotely.
Considerations for implementing smart technologies include:
- Real-Time Monitoring: Operators can oversee multiple systems and make modifications instantly.
- Predictive Maintenance: Advanced analytics can predict when maintenance is required, minimizing unexpected downtimes.
- Improved Safety Measures: Smart sensors can detect anomalies, alerting operators immediately.
Such advancements ensure that systems are not only efficient but also safer and more user-friendly.
Sustainability and Eco-Friendly Designs
Sustainability in CKD air regulation is gaining traction. Manufacturers focus on developing eco-friendly designs and materials. These designs aim to minimize environmental impact while maintaining high performance.
Key elements of sustainability in air regulators include:
- Energy Efficiency: Regulators that optimize air usage help to reduce energy consumption across systems.
- Recyclable Materials: Using materials that can be recycled reduces waste in production processes.
- Lifecycle Assessment: Evaluating the entire lifecycle of products identifies areas for improvement in sustainability.
This focus on sustainability not only aligns with global initiatives but also appeals to consumers and businesses that prioritize environmental responsibility.
"The continual evolution of CKD air regulators reflects broader industry trends. Embracing digital control, smart technologies, and sustainability will define future innovations."
Comparative Analysis of Air Regulators
The comparative analysis of air regulators is crucial in understanding the landscape of pneumatic solutions. This evaluation helps users navigate various offerings in terms of performance, reliability, and cost-effectiveness. By examining different brands, models, and their specific features, users can make well-informed decisions tailored to their needs.
A strong comparative analysis addresses several factors. First, it highlights the unique characteristics of CKD regulators versus competitors. Second, it provides insights into performance metrics that showcase efficiency and efficacy under varying conditions. Finally, customer feedback gives a real-world perspective on satisfaction and usability. This examination creates a comprehensive view that enhances understanding and optimizes choices.
CKD vs Competitor Brands
CKD air regulators have carved a reputable niche in the marketplace. However, evaluating them against competitor brands is vital for a complete understanding. Each brand offers unique attributes, making it essential to analyze points like design, functionality, and application areas.
For example, brands like SMC are known for their innovative technology, while Festo focuses on energy efficiency. When comparing CKD to these competitors, consider factors such as:
- Performance: Measure how each regulator functions under different pressure dynamics.
- Cost: Analyze the price-to-performance ratio of CKD regulators relative to peers.
- Durability: Investigate the lifespan of materials used, contributing to long-term reliability.
Performance Metrics
Performance is a core aspect of evaluating air regulators. CKD regulators typically excel in specific metrics such as stability and flow rate under varying conditions. Knowing how these metrics compare with alternatives aids users in identifying which model suits their application best. Key metrics to consider include:
- Pressure Stability: Ability to maintain set pressure despite fluctuations in input.
- Flow Rate: The volume of air a regulator can pass at a given pressure.
- Response Time: Speed to adjust when input pressures change, affecting the efficiency of pneumatic systems.
Understanding these performance metrics allows for practical assessment in application scenarios.
User Feedback and Satisfaction
Gathering user feedback is essential to gauge the effectiveness of CKD air regulators. The insights derived from the experiences of users can reveal advantages and drawbacks that traditional specifications might not cover. Surveys and reviews often mention aspects like:
- Ease of Use: Users appreciate intuitiveness during installation and operation.
- Maintenance Requirements: Consistent positive feedback often relates to lower maintenance needs.
- Overall Satisfaction: Many users describe their overall experience, which contributes to brand trust.
By considering user feedback, one can gain a holistic understanding of CKD's acceptance in the market and how it stands up against competiton.
Understanding the strengths and weaknesses of CKD air regulators compared to other brands informs decision-making, ensuring optimal selection for specific pneumatic applications.
This comprehensive analysis is vital for students, researchers, educators, and professionals in the field. It guides the reader in strategically assessing air regulators to align with their unique needs.
Case Studies: Successful Implementations
Case studies offer unique insights into the practical application and benefits of CKD air regulators in various industries. They provide concrete examples of how organizations address specific challenges, optimize operations, and achieve significant improvements in productivity and efficiency. Understanding these implementations allows readers to grasp the tangible value of air regulation technologies in real-world contexts.
By examining case studies, professionals can identify critical elements that contribute to successful utilization of CKD air regulators. These may include the choice of regulator, installation practices, maintenance routines, and operational adjustments tailored to meet specific needs. Additionally, these examples highlight the need for custom solutions in distinct environments such as manufacturing, automotive, and pharmaceutical sectors.
Manufacturing Sector Example
In the manufacturing sector, CKD air regulators play a pivotal role in ensuring consistent air pressure for machinery operation. One notable example comes from a large-scale assembly plant where inconsistent pressure levels led to production delays. The introduction of CKD air regulators resulted in enhanced stability of air pressure across the pneumatic systems. This change reduced downtime caused by equipment malfunction by over 20%. Workers reported improved operational efficiency with tasks that required precise airflow, such as automated assembly lines, now functioning smoothly.
Focusing on the correct selection of regulatory units, the plant engineers opted for standard air regulators with relieving capabilities. They integrated these regulators into their system to handle any excess pressure, ensuring safety and operational reliability.
Automotive Industry Example
The automotive industry presents a dynamic environment that demands high-performance air regulation. A case study from an automotive manufacturer demonstrates how CKD air regulators facilitated improvements in production lines that use pneumatic tools. Before regulation was implemented, variations in air supply affected tool performance, leading to inconsistent assembly quality.
By incorporating CKD precision regulators, the manufacturer could maintain optimal pressure levels. This allowed for precise tool operation, which increased overall assembly quality and reduced rework rates by 15%. The cost involved in upgrading the entire pneumatic system was offset by the savings gained from improved quality control and lower defective outputs.
Pharmaceutical Industry Example
In the pharmaceutical sector, strict regulations necessitate precise control over production environments. A pharmaceutical company embraced CKD air regulators to enhance their process reliability. They faced challenges with air quality and pressure variations, impacting both product quality and compliance with health regulations.
By installing high-performance CKD air regulators, the firm managed to provide a stable and clean air supply throughout their production processes. This change led to a 30% reduction in contamination-related incidents, greatly boosting their compliance rates with regulatory bodies. The successful implementation underscored the importance of utilizing advanced air regulation technologies in critical industries where precision cannot be compromised.
Implementing CKD air regulators in various sectors clearly illustrates their critical role in enhancing operational efficiency and ensuring product quality.
In summary, these case studies not only showcase the versatility and adaptability of CKD air regulators but also emphasize the measurable benefits that arise from their thoughtful application in real-world operations.
Finale
The conclusion of this article serves as a pivotal moment in synthesizing the intricate elements surrounding CKD air regulators. It encapsulates the essence of the discussions presented throughout the various sections, emphasizing the crucial role these components play in pneumatic systems.
Summary of Key Points
CKD air regulators are integral in controlling system pressure, ensuring efficiency, and enhancing performance in various applications. Key aspects discussed in this article include:
- Technical Specifications: Understanding the pressure regulation mechanism, flow characteristics, and the materials used in construction. Each detail matters in selecting the appropriate regulator for specific applications.
- Types of Regulators: Differentiating between standard air regulators, relieving and non-relieving options, and precision regulators. Each type serves unique functions in diverse environments.
- Applications Across Industries: The versatility of CKD air regulators is highlighted through examples in industrial automation, robotics, and packaging, demonstrating their significance in modern practices.
- Maintenance and Troubleshooting: Regular maintenance and effective troubleshooting strategies are essential for longevity and peak performance of regulators. Recognizing wear signs and knowing when to replace components prevents larger failures.
- Future Trends: The exploration of advancements in digital control and integration of smart technologies reveals an exciting future for CKD air regulators. Sustainability trends are also likely to shape the design landscape going forward.
Final Thoughts on CKD Air Regulators
In final assessment, CKD air regulators are more than mere components in pneumatic systems; they are essential players that directly influence operational efficiency and effectiveness. Professionals must select the right regulator based on system compatibility, performance needs, and cost considerations. As technology evolves, the understanding of air regulators will likely deepen, offering even greater precision and control in automation.
Ultimately, staying informed on CKD air regulators and their advancements prepares engineers and technicians to harness their full potential in optimizing system performance. This thorough analysis stands as a resource, fostering a robust understanding essential for anyone engaged in the field.