Understanding Electricians Alloy: Properties and Applications
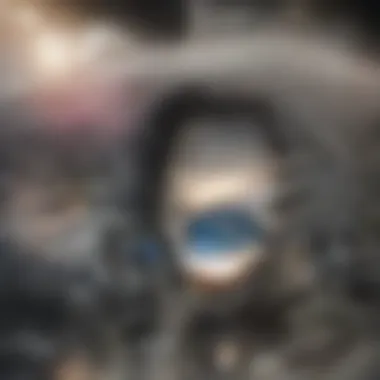
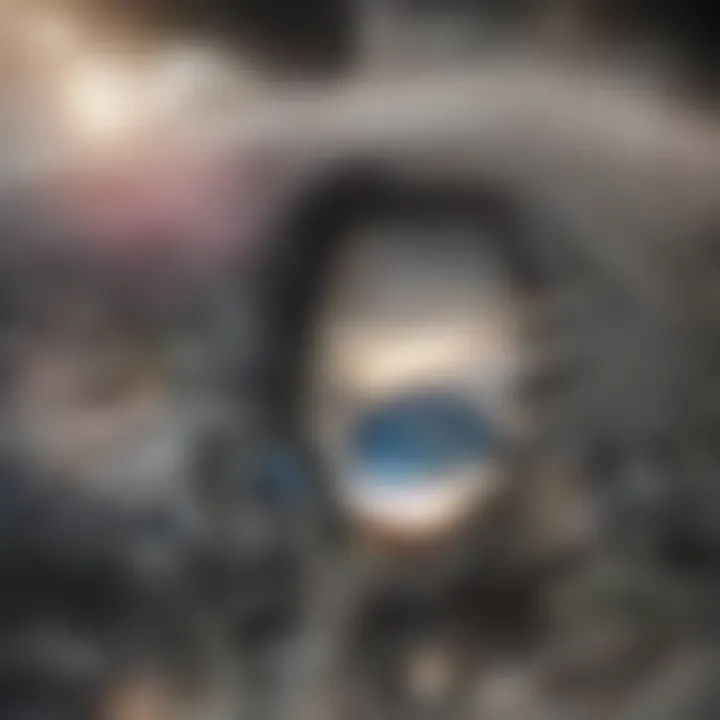
Intro
Electricians alloy plays a vital role in the electrical industry, providing essential characteristics for connectivity and durability. From its composition to its applications, understanding this material can lead to significant advancements in how electrical systems are designed and implemented. By examining the unique properties and implications of electricians alloy, stakeholders can make informed decisions about its application in various contexts.
Advancements in material science have propelled electricians alloy into a spotlight it rightly deserves. As the demand for efficient and reliable electrical connections increases, so does the need to comprehend its properties and implications thoroughly. This article aims to illuminate these aspects, breaking them down into easily digestible segments. Moreover, it will look at the future potential of electricians alloy, including environmental considerations and innovative solutions that may emerge.
Recent Advances
Latest Discoveries
Recent research has unveiled new combinations and treatments for electricians alloy that enhance its conductivity and resilience. Studies indicate that certain blends of copper and aluminum not only maintain high conductivity but also improve mechanical strength. These innovations are crucial for applications requiring high-performance materials.
Another significant discovery involves surface treatments that reduce oxidation. The treated alloys show an impressive increase in longevity and performance in harsh environments. As environmental conditions can greatly impact electrical materials, these findings provide a critical advantage.
Technological Innovations
Technological innovations in the production of electricians alloy are paving the way for not only increased efficiency but also sustainability. Advances in manufacturing techniques, such as 3D printing, enable more precise control over the alloy's microstructure, yielding better electrical performance.
Additionally, digital simulations and modeling are shaping the future of materials development. Engineers can now predict how different alloy combinations will behave under various conditions. This predictive capability significantly reduces the trial-and-error phase commonly associated with material development.
"Harnessing the power of technology in materials research opens doors to possibilities previously unseen in the electrical industry."
Methodology
Research Design
This exploration into electricians alloy leverages a multifaceted research design. By combining both qualitative and quantitative methodologies, a comprehensive understanding of material properties and trends can be achieved. For instance, analyzing performance data alongside interviews with material scientists offers a balanced view.
Data Collection Techniques
Several data collection techniques are employed in this study. Laboratory experiments help establish basic performance metrics, while field studies provide insights into real-world applications. Surveys and interviews with industry professionals offer anecdotal evidence that complements more formal data sources. This allows for a nuanced understanding of how electricians alloy is utilized in practice.
Prelude to Electricians Alloy
Electricians alloy refers to a specific category of alloys that play a crucial role in the electrical industry. This section aims to elaborate on the significance of electricians alloy, focusing on its composition, properties, and applications. In the ever-evolving landscape of technology, understanding these alloys becomes essential for anyone involved in electrical engineering, manufacturing, or sustainability efforts within the sector.
The importance of electricians alloy lies in its ability to provide efficient electrical connectivity. The alloys are specifically designed to meet the demanding requirements of electrical applications, including conductivity, temperature stability, and corrosion resistance. These metals offer unique advantages that can enhance system performance while helping to mitigate potential failures during operation.
When we explore the properties of electricians alloy, we see that it combines various base metals and alloying elements to optimize their features. Key characteristics such as high thermal and electrical conductivity make these alloys indispensable in producing quality electrical components. Furthermore, their resistance to corrosion ensures longevity and reliability in high-demand environments.
The need for efficient electrical systems drives the demand for electricians alloy in modern applications. As industries shift toward greener technology and renewable energy solutions, the relevance of this topic increases. This article will delve deeper into the composition, applications, and implications of electricians alloy, providing valuable insights into how they contribute to the electrical landscape today.
Definition and Overview
Electricians alloy generally refers to a blend of metals that are specifically formulated to be used in electrical applications. These alloys typically consist of primary metals like copper or aluminum, combined with alloying elements such as nickel or tin. Each component within the mixture serves to enhance the overall performance of the material.
One of the defining traits of electricians alloy is its capacity for high electrical conductivity. This characteristic ensures minimal resistance to the flow of electricity, which is critical in applications that require efficient power delivery. In addition to conductivity, electricians alloy usually possesses excellent corrosion resistance. This property prevents deterioration over time, making these alloys suitable for long-term use in various environments.
Another essential aspect is the versatility of electricians alloy. It can be molded and shaped into a variety of forms, from connectors to wires, depending on the specific requirements of the application. This adaptability further validates the importance of understanding electricians alloy, as different formulations may be better suited for particular uses.
"Electricians alloys are foundational components in modern electrical systems, offering unparalleled performance and reliability."
In summary, electricians alloy is a vital topic for students, researchers, and professionals alike. Understanding this subject not only helps in making informed choices regarding material selection but also fosters innovation and improvement in electrical engineering practices. As such, a thorough examination of electricians alloyβs properties, applications, and future prospects will be beneficial to all engaged in the field.
Composition of Electricians Alloy
Understanding the composition of electricians alloy is crucial for several reasons. The specific combinations of metals used in these alloys determine their electrical and mechanical properties, which in turn affect performance in various applications. This section will analyze the base metals and alloying elements, offering insight into their roles and significance in creating effective electricians alloys.
Base Metals Used
The foundation of electricians alloys typically consists of specific base metals. These metals are selected due to their favorable characteristics. Common base metals in electricians alloy include copper and aluminum.
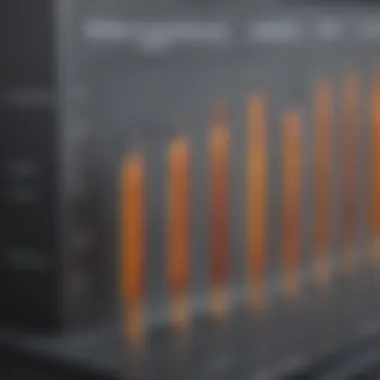
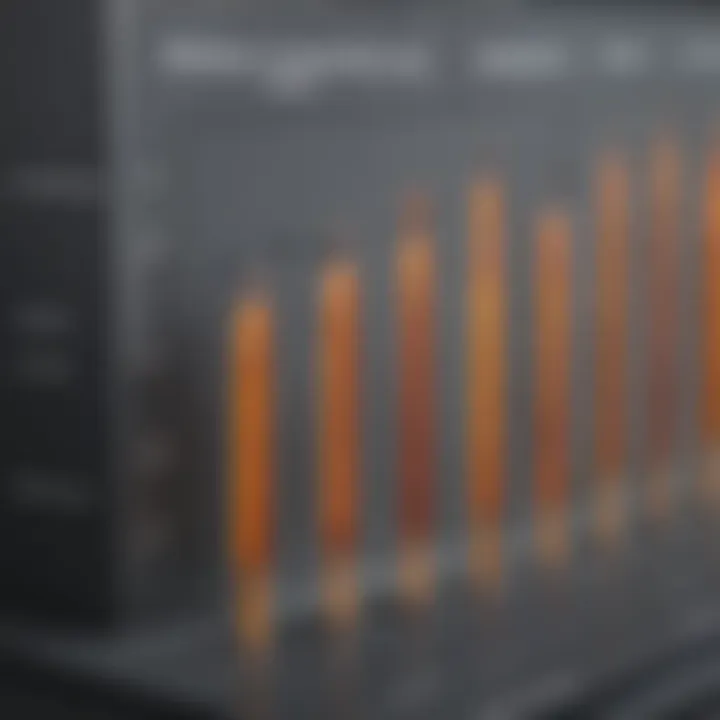
- Copper is renowned for its high electrical conductivity. This property makes it a preferred choice for electrical applications, as it allows efficient transmission of electric current. Additionally, copper's resistance to corrosion contributes to long-term performance in electrical connections.
- Aluminum, while having lower conductivity than copper, is lighter and often more cost-effective. It is also resistant to corrosion, making it suitable in environments where exposure to moisture is a concern.
Understanding the choice and role of these base metals is essential for optimizing the functionalities of electricians alloys.
Alloying Elements
In addition to base metals, various alloying elements enhance and customize the properties of electricians alloys. These elements adjust the physical and mechanical attributes to meet specific requirements in electrical applications. Common alloying elements include nickel, zinc, and silicon.
- Nickel is added to improve corrosion resistance, especially in harsh environments. It can also enhance the alloy's strength and fatigue resistance, making it suitable for demanding electrical applications.
- Zinc is often used to enhance strength and enable better bonding properties. This is particularly important in applications where durability is critical to ensure performance over time.
- Silicon can be included to improve the fluidity of the molten alloy during casting. It reduces the likelihood of defects, ensuring a smoother final product.
These alloying elements play a pivotal role in tailoring the specific characteristics of electricians alloys. Their judicious selection allows engineering teams to devise materials that can withstand the environmental and operational challenges faced in the electrical industry.
"Understanding the meticulous balance of base metals and alloying elements in electricians alloy is key for developing materials that meet modern demands in electrical applications."
In summary, a deep understanding of the composition of electricians alloy is essential. The base metals and alloying elements each contribute unique properties that enhance functionality and performance. This knowledge is vital for students, researchers, and professionals seeking to innovate and improve electrial materials.
Physical Properties of Electricians Alloy
Electricians alloy exhibits several physical properties that are integral to its performance in electrical applications. Understanding these properties is essential for professionals who work with these materials. The unique characteristics of electricians alloys can significantly influence their effectiveness in various roles, from conductors to connectors. The main properties of interest include conductivity, corrosion resistance, and mechanical properties. Each of these aspects plays a crucial role in ensuring the efficiency and reliability of electrical systems.
Conductivity
Conductivity is one of the foremost properties of electricians alloy. It defines how well the alloy can transmit electrical currents. High conductivity is essential for reducing energy losses in electrical systems, which is a key factor in improving overall efficiency. Electricians alloys are designed to exhibit optimal conductivity, often surpassing conventional copper or aluminum alloys. This functionality is critical in applications like electrical connectors or wiring, where any loss in conductivity can lead to overheating or system failures.
The design of electricians alloy ensures the seamless flow of electrons while balancing other physical properties. When analyzing conductivity, it is important to consider not just the alloy's composition but also its geometrical configuration. For example, thinner wires in particular alloys can enhance conductivity further due to decreased resistance across the surfaces.
Corrosion Resistance
Corrosion resistance is another vital physical property of electricians alloys. In many electrical applications, factors such as moisture, temperature, and surrounding chemicals contribute to the degradation of metal components. Electricians alloys are often engineered to withstand these environmental stresses. Stronger corrosion resistance extends the life of electrical components, reducing maintenance costs and improving reliability.
For instance, certain alloys possess protective coatings that prevent oxidation. This is significant in outdoor or extreme condition installations where conventional materials would quickly deteriorate. Additionally, corrosion can impact conductivity over time, so improved resistance helps maintain the alloy's performance.
"Corrosion resistance not only protects the alloys but also plays a key role in ensuring long-term electrical reliability."
Mechanical Properties
Mechanical properties also influence the practical applications of electricians alloy. These include factors such as tensile strength, ductility, and fatigue resistance. The balance of these properties determines how an alloy will perform under stress or strain in the real-world scenarios. High tensile strength is necessary for situations where the alloy must endure physical impacts without deforming.
Moreover, ductility enables the material to be formed into the required shapes, such as in wiring or connectors. Thus, electricians alloys should possess enough malleability to be shaped while still maintaining structural integrity. Fatigue resistance is particularly crucial in dynamic applications where materials can experience repeated load cycles. This aspect is important for ensuring the longevity of connections in applications involving movement or vibration.
In summary, the physical properties of electricians alloy are multi-faceted and significantly contribute to its applicative success. Conductivity, corrosion resistance, and mechanical properties must work together to ensure optimal performance in electrical systems.
Manufacturing Processes
The manufacturing processes of electricians alloy are crucial for ensuring the integrity and performance of these materials in various applications. The way these alloys are melted, cast, drawn, and formed determines their physical properties, which in turn affects their effectiveness in electrical systems. Understanding these processes helps in assessing how to use electricians alloy efficiently while also considering cost and environmental impact.
Melting and Casting Techniques
Melting and casting are foundational processes in the creation of electricians alloy. The melting process involves heating base metals and alloying elements to their melting points until they reach a liquid state. This stage requires precision to maintain appropriate temperatures and avoid contamination. The molten alloy is then poured into molds designed to form specific shapes, which can include rods, sheets, or custom components for electrical applications.
Effective melting methods, such as induction melting or arc melting, are essential. Induction melting provides quick temperature control and reduces oxidation. Casting techniques, including sand casting and die casting, determine the final structure and mechanical properties of the alloy.
Benefits of advanced melting and casting techniques include:
- Improved consistency in alloy properties.
- Reduced defects and impurities, leading to enhanced performance.
- Capability to produce complex shapes that meet specific application needs.
Drawing and Forming Processes
Once the alloys are cast, they undergo drawing and forming processes to achieve desired dimensions and attributes. Drawing involves pulling metal through a die to reduce its cross-section, which increases its strength and conductivity. This process is critical for producing wires and connectors made from electricians alloy.
Forming processes, such as bending or stamping, allow for the creation of components that fit within electrical devices or systems. These processes must be carefully controlled to maintain the alloyβs integrity and performance.
Key considerations in drawing and forming include:
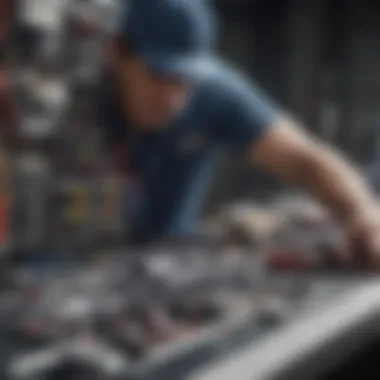
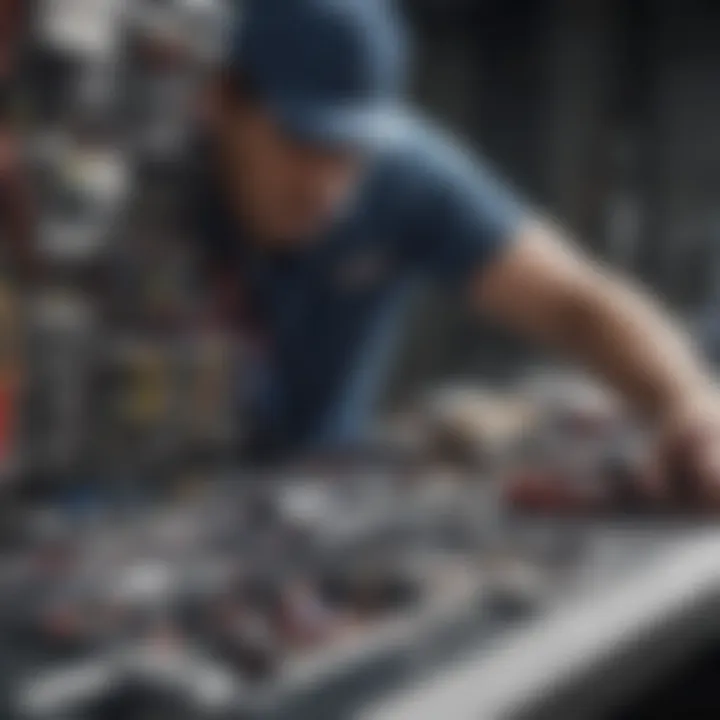
- Temperature control to avoid unexpected strengthening or softening.
- Strategies for reducing waste, which contribute to sustainability.
- Techniques to ensure the uniformity of finished products, which is vital for reliability in applications.
In summary, the manufacturing processes directly affect electricians alloy's usability and efficiency. Understanding melting, casting, drawing, and forming methods leads to better material performance, ultimately benefiting the electrical industry.
The precision in manufacturing processes greatly influences the physical properties and applications of electricians alloy.
Applications of Electricians Alloy
The applications of electricians alloy are essential to understand its role in the electrical industry. This material offers specific benefits that enhance its usability across various applications. The increased demand for reliable electrical connections drives the need for superior materials such as electricians alloy. This alloy not only serves critical functions but also impacts performance and efficiency in both residential and industrial settings.
Electrical Connectors
Electrical connectors are one of the most significant applications of electricians alloy. They are used in a variety of electrical systems to join wires and circuits. The conductivity of electricians alloy enables efficient electric flow. This results in reduced energy loss, which is crucial for modern electronics. When connections are reliable, the overall system performance improves.
Moreover, electricians alloy possesses excellent resistance to corrosion, which is important for maintaining long-term connection integrity. In environments subject to moisture and chemicals, the durability of these connectors canβt be overstated. Hence, choosing the right alloy contributes to the longevity and effectiveness of electrical connections.
Heat Sinks
Heat sinks play a vital role in thermal management. These components dissipate heat generated by electronic devices, which is necessary to prevent overheating and potential failures. Electricians alloy is often preferred for heat sinks due to its remarkable thermal conductivity. Its ability to transfer heat away from sensitive components ensures that electronic devices operate efficiently.
In addition, the lightweight nature of electricians alloy makes it ideal for applications where weight is a concern, such as in telecommunications or aerospace industries. Using a material that combines efficient heat dissipation with reduced weight is an advantage that improves device longevity and performance.
Wiring and Cabling
Wiring and cabling systems are the backbone of any electrical network. The use of electricians alloy in these applications helps in building reliable networks that can accommodate various power demands. The resistance to electrical wear and breaking during installation and use is another strong point of electricians alloy.
In conjunction with other materials, electricians alloy enhances the flexibility and durability of wiring solutions. Its strength makes it suitable for high-stress environments, reducing the risk of faults over time. The alloy's properties are especially valuable in residential, commercial, and industrial wiring projects.
As technology continues to advance, the necessity for effective and efficient electricians alloys will only grow. Their applications across different sectors highlight the ongoing evolution of material needs in electrical engineering.
Advantages of Using Electricians Alloy
Electricians alloy offers several significant benefits that enhance its suitability for various applications within the electrical domain. Understanding these advantages is crucial for professionals and researchers alike, as they underscore the effectiveness and reliability of electricians alloys in real-world scenarios. Two of the most prominent benefits are enhanced performance and longevity or durability.
Enhanced Performance
One of the primary selling points of electricians alloy is its enhanced performance compared to traditional materials. This advantage is due to a combination of factors including excellent electrical conductivity, thermal conductivity, and low resistance levels.
- Electrical Conductivity: Electricians alloys, particularly those with copper or aluminum bases, are designed to optimize electrical flow. This quality minimizes energy loss during transmission.
- Thermal Management: The ability to dissipate heat effectively allows for higher operational efficiency in electrical systems. This is especially vital in applications like wiring and connectors where overheating can lead to failures.
- Weight Considerations: Many electricians alloys are lighter than conventional metals. This reduced weight can contribute to ease of installation and can reduce the overall load in structures.
In sum, the enhanced performance of electricians alloy makes it a preferred choice for many applications, especially where efficiency and reliability are paramount.
Longevity and Durability
Longevity and durability are other notable advantages of electricians alloy. These qualities ensure that the materials can withstand successive use over time without significant degradation. This resilience can be attributed to factors such as:
- Corrosion Resistance: Many electricians alloys exhibit strong resistance to corrosion, which prolongs their lifespan. This characteristic is crucial for components exposed to various environmental conditions.
- Stress Tolerance: The mechanical properties of these alloys allow them to endure extreme conditions. They can handle fluctuations in temperature, pressure, and electrical stresses without failure.
- Reduced Maintenance: With longevity and durability, the need for frequent replacements or repairs diminishes. This leads to lower overall costs associated with labor and materials.
"The longevity and durability of electricians alloy directly enhance overall system reliability, making it a strategic asset in both current and future electrical applications."
Environmental Considerations
Environmental considerations play a crucial role in the dialogue surrounding electricians alloy. As technology advances, the demand for sustainable and eco-friendly materials becomes more pressing. Electricians alloy, known for its electrical reliability and versatility, is also increasingly recognized for its environmental implications.
Sustainability of Materials
The sustainability of materials used in the production of electricians alloy is key. This factor can be evaluated through various lenses: extraction practices, energy consumption, and the overall lifecycle impact.
- Extraction Practices: The sourcing of base metals and alloying elements often raises concerns regarding ecological disruption and habitat loss. It is critical to ensure that these materials come from responsible mining operations to minimize the environmental footprint. Sustainable extraction methods support a balance between obtaining necessary resources and protecting ecosystems.
- Energy Consumption: The processes required to produce electricians alloy must also be assessed. Energy-intensive manufacturing can contribute significantly to carbon emissions. Implementing energy-efficient practices and utilizing renewable energy sources can reduce this impact, thus supporting global sustainability goals.
- Lifecycle Impact: Evaluating the entire lifecycle of electricians alloy, from production through end-of-life, is essential. Creating alloys designed for longevity and functionality minimizes waste. Such a principle aligns with the sustainable development goals, supporting a circular economy where materials are reused or recycled rather than discarded.
Recycling and Reusability
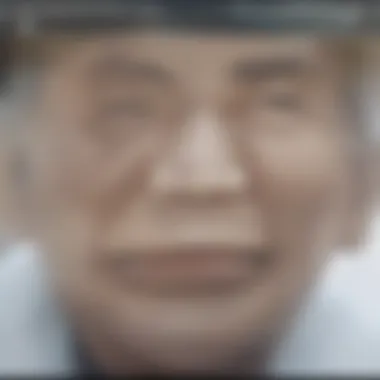
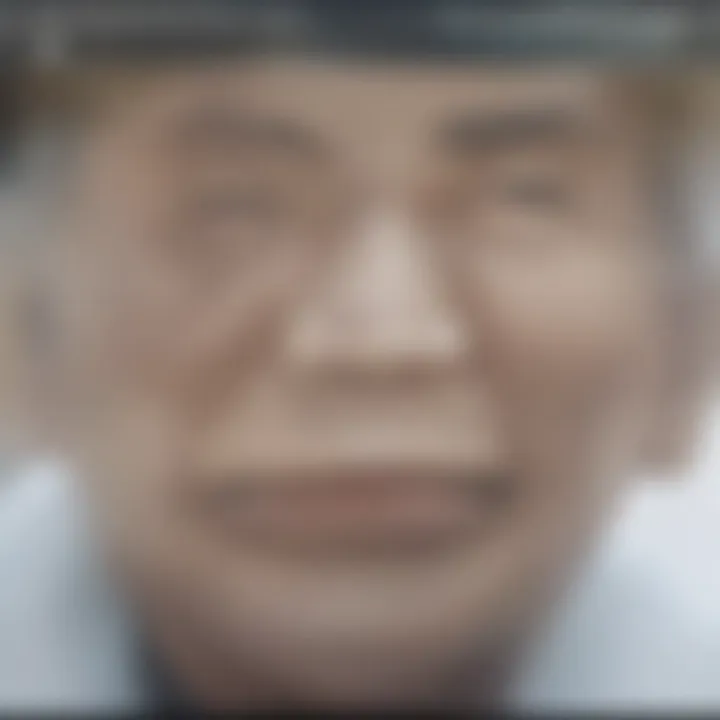
Recycling and reusability are paramount in discussions about electricians alloy. As these materials are widely used in electrical components and fixtures, their potential for reuse significantly affects environmental conservation. Recycling not only reduces waste but also eliminates much of the need for new raw materials.
- Efficient Processes: The recycling of electricians alloys, such as copper-nickel or copper-zinc alloys, involves specialized processes that can reclaim materials while maintaining their properties. When recycled, electricians alloy can retain its conductivity and durability, making it suitable for many applications.
- Economic Benefits: Emphasizing recycling and reusability can also yield economic benefits. The recovery of materials reduces the costs associated with new raw material acquisition and can provide financial incentives for companies engaged in sustainable practices.
In summary, considering the sustainability and recycling potential of electricians alloy is not merely an abstract topic but central to generating a future where materials can coexist with ecological integrity. With continued advancements and commitment to sustainable practices, the use of electricians alloy can be a model for how materials can meet industrial needs while respecting the environment.
"Sustainable materials are crucial for innovation in technology that respects our planet."
To learn more about sustainable practices in material production, see Wikipedia or Britannica.
Challenges in the Use of Electricians Alloy
Electricians alloy offers remarkable properties and applications, yet challenges persist that bureaucratically limit its utilization. Understanding these challenges is critical for the industry to enhance the efficacy and longevity of electrical systems. Key issues include temperature stability and manufacturing costs. Addressing these factors ensures the reliability of electricians alloy in practical applications and drives innovation.
Temperature Stability
Temperature stability is a vital concern for electricians alloy. This is because the performance and reliability of electrical components depend significantly on their ability to withstand varying temperatures. Many alloys experience conductivity variations at high temperatures, which results in performance degradation.
When subjected to thermal expansion and contraction, the structural integrity of the alloy can also weaken. For instance, increased temperature can lead to phase changes in the metal matrix, which might reduce overall strength. This is particularly concerning in environments with high thermal loads or rapid cycling.
Key Insight: Maintaining temperature stability is essential for ensuring that electrical components maintain their performance during operations.
Manufacturers often have to specifically design alloys that resist these issues. This requires a comprehensive understanding of the specific application and the conditions under which the alloy will operate.
Manufacturing Costs
Manufacturing costs present another challenge for electricians alloy. The production processes for these materials can be resource-intensive and complex. This complexity arises from the need to maintain precise control over composition during the melting and alloying processes.
Higher-quality alloys, which exhibit superior properties and resilience, typically come with a higher price tag. For small-scale projects, the cost can become a deterrent for widespread usage.
Furthermore, advancements in alloying techniques and technologies are essential. Developing efficient manufacturing processes would reduce costs while ensuring high-quality products. Balancing cost-effectiveness with performance is a constant challenge in the industry.
Future Trends and Innovations
The domain of electricians alloy is evolving rapidly in response to changing technological landscapes and demands. Understanding future trends and innovations can shed light on the path forward for materials used in electrical applications. This section will explore advancements in alloy development and how these materials are integrating into emerging technologies.
Advancements in Alloy Development
Research in the area of electricians alloy focuses on enhancing performance and efficiency. New alloy formulations are being designed to meet the specific needs of modern electrical systems. These advancements aim to optimize conductivity while maintaining excellent mechanical properties.
Some current directions include the use of nanotechnology to create alloys with increased strength and conductivity. For instance, the addition of nanoscale copper particles to traditional alloys can improve their electrical performance significantly. Engineers are also experimenting with different fluxes and additives that can improve corrosion resistance and overall durability.
Furthermore, the push towards sustainability is influencing alloy development. Manufacturers are beginning to incorporate recycled metals, which not only lowers costs but also contributes to environmental responsibility. The regulators and industry leaders are actively encouraging these methods to drive sustainability in production. In this climate of innovation, crucial questions about performance, scalability, and environmental impact are at the forefront.
Integration in Emerging Technologies
As new technology surfaces, the role of electricians alloy is increasingly pivotal. These materials are finding applications in various cutting-edge sectors, such as renewable energy, electric vehicles, and advanced electronics. The rise in electric vehicle production is a significant driving force. The need for efficient wire and connector systems in batteries and drive trains demands higher performance from alloys.
Innovations in smart grid technology also create a demand for high-conductivity materials that can facilitate real-time data transfer with minimal energy loss. Electricians alloy applications are likely to expand continually as smart devices become more prevalent.
In addition, advances in energy storage systems, particularly lithium-ion technology, are generating a necessity for high-efficiency alloys that can handle the thermal management challenge while ensuring reliable operation.
"The future of electrical materials is etched in a balance between performance and sustainability."
In summary, the future of electricians alloy revolves around continual innovation and integration into emerging technologies. The ever-increasing need for efficient, reliable, and sustainable materials ensures that developments in this field will remain at the forefront of electrical engineering.
Ending
The significance of electricians alloy in modern electrical applications cannot be overstated. This alloy plays a crucial role in providing reliable and efficient electrical connections across various industries. In this article, we have explored not just the composition and unique properties of electricians alloy but also its practical applications and implications for the environment.
Summary of Key Points
Throughout this discussion, several key elements have emerged:
- Composition: Electricians alloys consist of a mix of base metals like copper, often enhanced with alloying elements that contribute to their unique properties.
- Physical Properties: These alloys exhibit desirable characteristics such as high conductivity, corrosion resistance, and superior mechanical strength, making them ideal for electrical connections.
- Applications: Widely used in electrical connectors, heat sinks, and wiring, electricians alloy ensures efficient electrical performance.
- Environmental Considerations: The sustainability of materials used in electricians alloy emphasizes their recyclability and the importance of reducing manufacturing impacts on the environment.
- Future Innovations: Ongoing advancements in alloy development and integration into emerging tech highlight the continued relevance of electricians alloy.
Final Thoughts on the Role of Electricians Alloy
The role of electricians alloy is foundational in todayβs technological landscape. As industries evolve, the reliability of electrical systems becomes even more critical. The use of electricians alloy not only enhances performance but also contributes to longer-lasting electrical components, which is vital for reducing waste and promoting sustainability.