Understanding the Production of Manufactured Sand
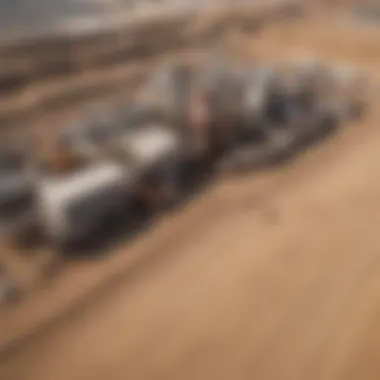
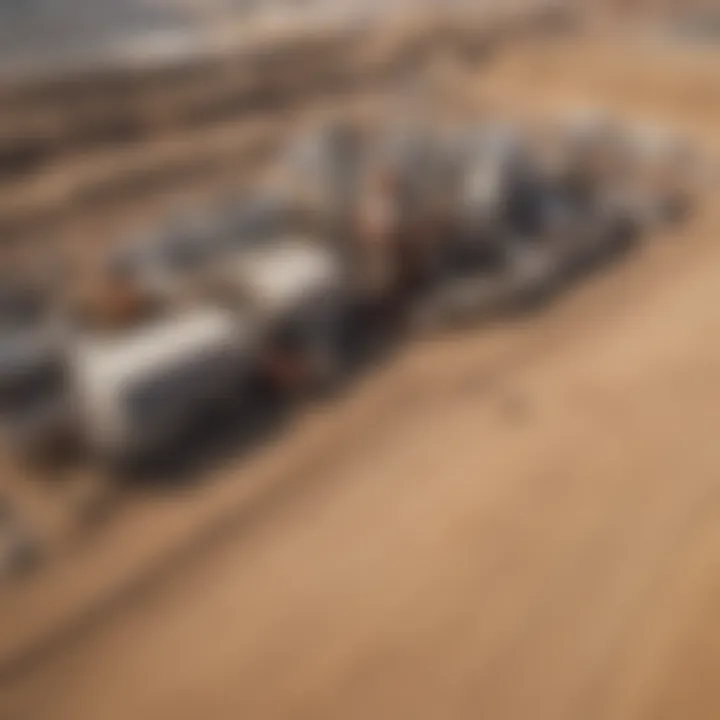
Intro
In the modern age, the construction industry increasingly relies on manufactured sand as a cornerstone material, paving the way for enhanced sustainability and efficiency. This materialโoften produced by mechanically crushing rocksโhas become crucial in addressing the dominant challenges posed by natural sand shortages. With beaches eroding and riverbeds dwindling, the shift towards manufactured sand is not just a trend; itโs a necessity, driven by the relentless demands of infrastructure development and urbanization.
Manufactured sand stands out not merely for its composition but for its potential to bridge environmental concerns with the booming construction market. It has drawn attention from engineers, architects, and environmentalists alike, igniting discussions around its role in promoting greener practices. As we delve into this topic, we find that understanding the processes, advancements, and nuances behind manufactured sand becomes pivotal for anyone interested in the future of construction.
Recent Advances
Recently, the field has seen several promising developments driving the adoption of manufactured sand in various applications. Innovations in extraction, processing, and quality assessment techniques have laid a solid groundwork for optimized production.
Latest Discoveries
A handful of studies have come to light, identifying unique properties of manufactured sand that mirror or even surpass those of natural aggregates. For instance, a recent study in Construction and Building Materials detailed how specific crushing methods can yield sand particles with angular shapes and rough textures, enhancing the bonding qualities when mixed with cement. Such characteristics enable the creation of more durable concrete structures, significantly extending their lifespans and reducing maintenance costs.
Technological Innovations
Advancements in technology also play a vital role in the manufacturing sand sector. Modern practices incorporate
- Artificial intelligence to predict the quality of sand produced during the manufacturing process.
- Automation in sorting and grading sand ensures only the highest-quality products reach the market, improving overall efficiency.
These tech-driven approaches represent a shift towards a future where data and precise analysis guide production, ultimately leading to higher performance materials in construction.
"The utilization of manufactured sand not only provides a solution to sand shortages but also holds great promise for revolutionary advancements in the construction industry."
Moreover, incorporating eco-friendly practices in the manufacturing processes complements these technological strides. By recycling waste materials from other industries, producers can reduce the environmental footprint, showcasing a model for resource optimization.
Methodology
Understanding how manufactured sand is produced involves dissecting the underlying methodologies used throughout the industry. Researchers often employ varied methodologies to study this subject, focusing not only on the physical properties of the material but also its environmental impact.
Research Design
The design of research studies tends to emphasize a multidimensional approach. This might include laboratory tests on sand quality, field trials assessing performance in construction projects, and case studies examining recovery rates from natural sand sources. Such research offers a comprehensive view of the implications of widespread manufactured sand use.
Data Collection Techniques
Data collection surrounds and complements these designs, employing an array of techniques:
- Surveys among construction professionals to gauge perspectives on manufactured sand.
- Site assessments to evaluate the implementation of manufactured sand in real-world contexts.
- Experimentation, including controlled setups to assess durability and performance metrics.
Through these methodologies, the intersection of practical use, analytical insight, and environmental concern is exploredโensuring that future advancement in this arena aligns with broader sustainability goals.
Prologue to Manufactured Sand
Manufactured sand, often dubbed as crushed stone sand or sand made through the crushing of rocks, is carving out a pivotal space in the modern construction landscape. Understanding this topic is essential as it addresses some pressing challenges in the construction industry. With dwindling natural sand reserves owing to excessive extraction and environmental degradation, manufactured sand emerges as a practical substitute. This article aims to delve into the nuances surrounding manufactured sandโits production processes, environmental impact, and the myriad applications in construction.
Definition and Importance
Manufactured sand refers to sand produced by mechanically crushing rocks or stones. Unlike natural sand that is sourced from riverbeds, lakes, or ocean floors, manufactured sand is artificially created, offering a more sustainable solution to meet the growing demand for fine aggregates in construction. This type of sand often contains finer granules compared to natural sand, making it suitable for a range of applications from concrete production to asphalt paving.
The significance of manufactured sand cannot be overstated. It not only reduces the reliance on naturally occurring sand, which is often harvested unsustainably, but it also allows for more controlled grading and quality assurance. Furthermore, it contributes to reducing overall construction costs, particularly in regions where natural sand is in short supply or overly expensive.
Historical Context
The practice of creating sand through artificial means is not a recent invention. The roots of manufactured sand can be traced back to the mid-20th century when the demand for concrete began to surge due to urbanization and infrastructure expansion. Early on, the focus was primarily on utilizing waste products from other mining operations. Over time, as technology advanced, processes for producing high-quality manufactured sand became more sophisticated.
In the 1970s, the world witnessed a greater emphasis on sustainable practices. This shift prompted the construction industry to reevaluate its materials, leading to a heightened interest in manufactured sand. By the late 1990s, significant research and development concluded that manufactured sand could serve as a viable alternative to natural sand, further enhancing concrete's properties.
Today, manufactured sand is no longer just a niche solution; it's an integral part of construction materials. Countries like Sweden and the Netherlands have incorporated it into their standards, demonstrating how global trends shaped policies toward the adoption of manufactured sand.
To sum up, the importance of manufactured sand is underscored by its ability to meet the increasing demands of construction while addressing ecological concerns associated with natural sand extraction.
"The transition from natural to manufactured sand is not merely a trend; it reflects a paradigm shift in how we view construction materials and sustainability."
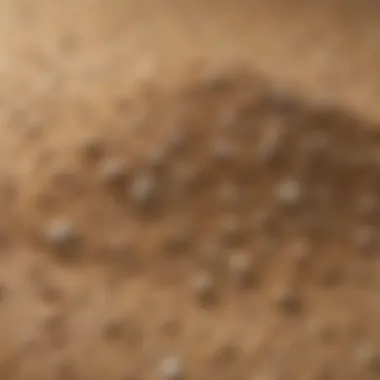
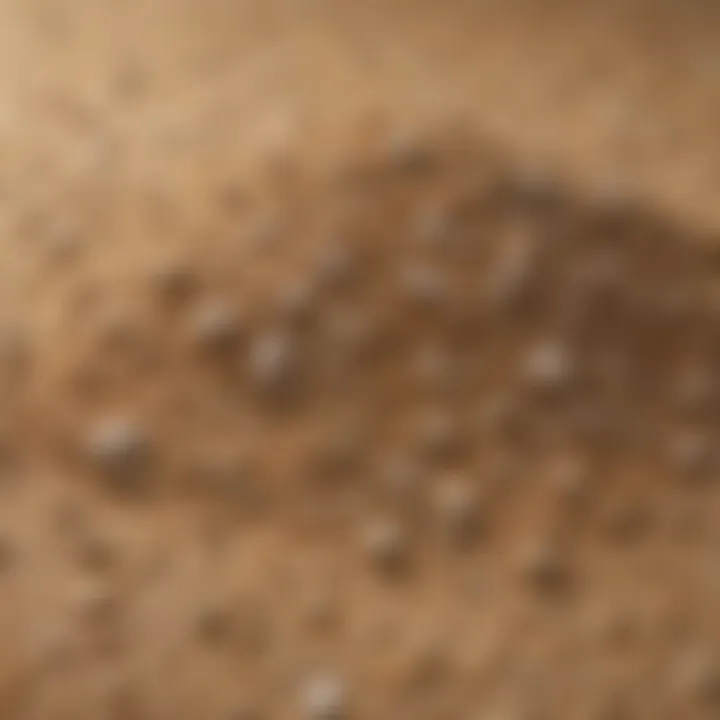
Through this exploration, readers will grasp the intricacies, significance, and historical evolution of manufactured sand, setting the stage for deeper insights into its production methods and applications.
Methods of Manufacturing Sand
Understanding how manufactured sand is created plays a crucial role in appreciating its applications and benefits in construction. The methods of manufacturing sand determine its quality, sustainability, and how well it performs in various uses. Each technique offered in this section presents unique advantages, all of which contribute to the overall effectiveness of manufactured sand as a viable alternative to natural sand. Most importantly, these manufacturing methods help address the growing concern over sand depletion, ensuring that construction industries worldwide can maintain a steady supply without exhausting environmental resources.
Crushing Techniques
One of the primary steps in producing manufactured sand is crushing large rocks into smaller pieces. Different crushing methods can be employed, each yielding different grades of sand. For instance, impact crushers are optimal for creating fine aggregates due to their ability to break down material through high-velocity impacts. Comparing that to jaw crushers, where the material is squeezed between two plates, the end product tends to be coarserโa detail that architects and engineers might find significant when assessing materials for specific projects.
When choosing a crushing technique, it's essential to consider the properties of the source rock and the desired sand end product. Rocks like granite or basalt include high silica content, making them excellent candidates for high-quality manufactured sand. While lesser-quality stones may lead to weaker aggregates, using high-calcium limestone can result in a finer texture but with potential challenges related to durability.
Also noteworthy is the size reduction ratio, which varies based on the machine's specifications and design. A higher ratio means more efficiency but often leads to increased energy consumption. In sum, the balancing act between efficiency, energy costs, and final sand quality presents a fascinating challenge for manufacturers.
Screening and Grading
Once the crushing process is complete, the sand undergoes screening and grading to ensure that it meets specific size requirements and quality standards. Screening is a critical step. It separates the crushed material based on particle size, enabling manufacturers to produce aggregates that conform to standards for various applications. This sieving can be performed using vibrating screens or shaker screens, which allow the sand to be categorized appropriately.
Grading affects the performance of concrete mixtures. Properly graded sand leads to better packing, reducing void spaces and enhancing strength. Itโs like fitting the pieces of a puzzle togetherโwhen they fit well, the overall composition becomes sturdier. To achieve such precision, it's common to have multiple screens set in a cascade, allowing for an efficient means of obtaining various grades of sand in one batch.
"Proper grading enhances the durability of the final product, making it crucial for reliable construction outcomes."
Processing Technologies
The final stage in the creation of manufactured sand involves advanced processing technologies, which help refine the product further and enhance its suitability for specific applications. Innovations have transformed how we think about aggregates. For instance, air classification systems can remove impurities and dust, resulting in cleaner sand, which is vital for high-quality concrete formulations.
Another technique gaining traction is the use of washing systems to eliminate silt and clay particles. Not all sand-making operations include this step; however, washing can significantly improve the sand's performance by ensuring a higher strength and durability when mixed with cement.
Hydraulic classifiers are also a popular method to separate sand based on density, allowing manufacturers to obtain consistent results for each batch. In addition to improving quality, these systems can enhance efficiency and reduce wastage, a vital consideration as environmental regulations tighten worldwide.
In summary, the methods of manufacturing sand showcase the intricate processes that contribute to its quality and usability. Each techniqueโwhether crushing, screening, or processingโworks hand in hand to produce sand that meets the rigorous demands of modern construction while addressing pressing environmental concerns. As industries evolve and seek sustainable options, understanding the art and science behind sand manufacturing becomes increasingly important.
Comparative Analysis of Natural and Manufactured Sand
In the realm of construction and civil engineering, comparing natural and manufactured sand is more than just a technical diversion; itโs a cornerstone of sustainable practices. Understanding the differencesโspanning physical attributes, chemical makeup, and practical performanceโguides professionals in making informed choices that influence both immediate project outcomes and long-term ecological implications.
Physical and Chemical Properties
When diving into the physical and chemical aspects, we encounter a myriad of contrasts that significantly impact how these sands are utilized. Natural sand, formed through the gradual erosion of rocks, boasts a rounded grain shape arising from water action. This rounding enhances its flow and packing capabilities within concrete mixtures. On the flip side, manufactured sand typically results from crushed rock or gravel. The sharp, angular particles donโt pack as seamlessly, potentially leading to different behaviors in construction applications.
- **Grain Shape:
- Natural Sand: Rounded, leading to better workability.
- Manufactured Sand: Angular, often requiring adjustments in mix designs.**
Moreover, the chemical properties differ, largely hinging on the source materials. Natural sand often has fewer impurities but carries trace minerals that can perform variably in specific environments. Manufactured sand can be engineered to reduce these contaminants, thus standardizing quality across batches. The control over composition can enhance properties like pH levels, thereby influencing the durability of the final concrete mix.
"The choice between natural and manufactured sand isn't just about availabilityโit's a decision that can substantially affect sustainability and structural integrity."
Performance in Construction
When the rubber meets the road in construction practices, the performance of sandโand the choice between natural and manufactured typeโcomes under the spotlight. Each type has its merits depending on application needs. Natural sand is often preferred for projects demanding high workability, such as fine concrete elements, due specifically to its rounded granules.
However, manufactured sand is gaining ground thanks to its potential for consistency and quality control. Builders are increasingly recognizing its value in producing high-strength concrete, especially when compressive strength is a priority.
- Advantages of Natural Sand:
- Advantages of Manufactured Sand:
- Enhanced workability due to smooth particles.
- Lower variability, more predictable performances in field conditions.
- Standardized quality for consistent results.
- Reduced travel times from local source availability.
As projects grow more complex and sustainability emerges as a guiding principle, the decision matrix for selecting sand type continues evolving. Both options have valid roles, dependent on specific project requirements, environmental considerations, and the end-use dictates in construction endeavors.
Environmental Considerations
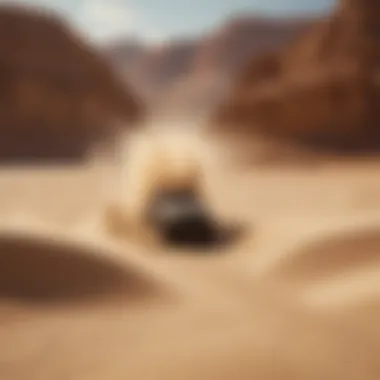
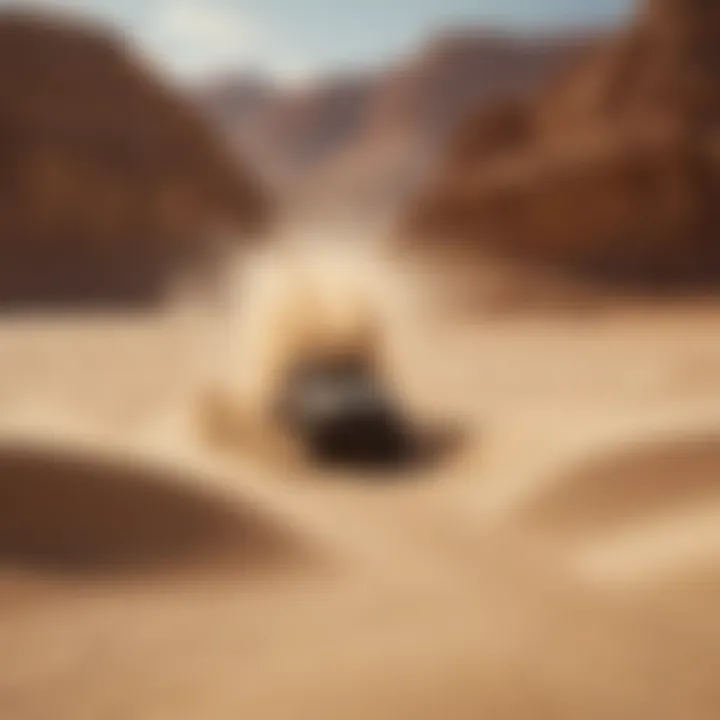
In the face of rapid urbanization and increased demand for construction materials, understanding the environmental considerations surrounding manufactured sand becomes essential. The production of this material doesnโt exist in a vacuum. As the construction industry leans heavily on manufactured sand, it becomes pivotal to weigh both its benefits and the potential ecological impacts. This examination not only ensures responsible resource management but also aligns with global sustainability goals.
Sustainability in Sand Production
Sustainability in sand production is a multi-faceted topic that revolves around the balance between resource extraction and environmental preservation. Unlike traditional natural sand sources that are gradually depleting, manufactured sand presents a renewed opportunity to mitigate ecological damage. The key elements of sustainability include:
- Resource Efficiency: Using by-products from various industries to create manufactured sand conserves natural materials and reduces waste in landfills.
- Renewable Practices: Techniques involving the recycling of concrete waste can yield new sand products, thus closing the loop in material usage.
- Energy Consumption: Modern manufacturing techniques prioritize energy efficiency, utilizing renewable energy sources to lessen the carbon footprint.
By promoting these practices, the manufacturing process of sand can transition closer to a more circular economy.
Ecological Impact Assessment
Conducting an ecological impact assessment is crucial in understanding how the production of manufactured sand interacts with the environment. This evaluation dives into various dimensions:
- Biodiversity Effects: Assessing how mining activities or factory operations might affect local wildlife and flora. For instance, dust from manufacturing plants can settle on surrounding vegetation, impacting photosynthesis and growth.
- Water Usage: The extraction process for sand often involves considerable water usage, which can strain local water resources. Evaluating the conservation methods employed in the production process is essential to mitigate this impact.
- Air Quality: Dust pollution from sand manufacturing can lead to significant air quality degradation. Analyzing the types of emissions released during production and implementing filtration systems can help alleviate this issue.
"Sustainable practices in manufactured sand production can serve as a benchmark for ecological preservation while meeting the construction industry's growing demands."
Overall, the ecological impact assessment related to manufactured sand should guide industries toward adopting practices that prioritize environmental health. By integrating these assessments into production methodologies, stakeholders can achieve a more harmonious balance between development and nature.
Quality Control in Manufactured Sand
Quality control in manufactured sand is a cornerstone of both construction efficacy and sustainability. In a world that increasingly leans towards building practices that minimize environmental impact, maintaining high standards in manufactured sand is paramount. This section delves into the specific elements that make quality control a priority in this industry, highlighting its benefits and the considerations it demands.
The importance of quality control manifests in multiple ways:
- Consistency of Material: Manufactured sand must have uniform properties to ensure compatibility with various construction applications. An inconsistent sand mix can jeopardize the structural integrity of projects, ranging from residential buildings to large infrastructure.
- Enhanced Performance: High-quality manufactured sand contributes to better performance in construction. This includes improved bonding in concrete, which can significantly impact durability and strength.
- Environment Considerations: Adhering to strict quality standards helps minimize wastage and promotes sustainable manufacturing practices, aligning with global environmental goals.
Implementing a stringent quality control process can involve various testing protocols, which leads us to the next section that focuses on testing standards and protocols.
Testing Standards and Protocols
Testing standards are the benchmarks by which the quality of manufactured sand can be evaluated. These often include:
- Grain Size Distribution Tests: Assessing whether the sand particles are within the desired range enhances capillary action in concrete, thereby influencing overall strength.
- Shape Analysis: The shape of the particles used in construction materials can affect workability. Tests such as the flakiness index can determine suitability.
- Chemical Composition Tests: Chemical analysis ensures that the sand is free from harmful substances. Contaminants can adversely affect the setting and durability of cement.
Adhering to protocols helps in maintaining a high level of quality and gives stakeholders confidence in the material theyโre using. As seen often, documentation and certification play a critical role in tracking these standards, impacting client trust and marketability.
Regulations and Compliance
Navigating the minefield of regulations and compliance can sometimes feel like trying to find a needle in a haystack, especially for manufacturers of sand. However, following these guidelines is absolutely essential not just legally, but also ethically. Several regulations dictate how manufactured sand should be produced, tested, and supplied to the market:
- ISO Certifications: Many manufacturers comply with International Organization for Standardization (ISO) standards that govern quality management systems, ensuring products meet high quality and safety requirements.
- Local Environmental Regulations: Different regions have specific environmental laws that address the extraction and use of manufactured sand. Compliance is not just about legality; it reflects the manufacturerโs commitment to being a responsible player in the industry.
- Safety Regulations: Workers involved in the production processes must also follow safety standards to minimize risks. This includes using personal protective equipment and adhering to safe machinery operation practices.
**"Adhering to regulations not only ensures product quality but also fosters a culture of responsibility and ethics in the industry."
Economic Implications of Manufactured Sand
The theme of economic implications surrounding manufactured sand is a critical component of understanding its role in the construction industry and beyond. In a world where natural sand sources are dwindling, manufactured sand offers a vital alternative that can reshape market dynamics. The production of manufactured sand holds several advantages that go beyond mere supply, touching upon aspects such as cost efficiency, market trends, and sustainability. In todayโs construction economy, being resourceful is paramount.
Market Trends and Demand
With urbanization on the rise and infrastructure demands increasing, the market for manufactured sand is experiencing significant growth. Recent reports suggest that manufactured sand is gaining momentum, particularly in regions facing a scarcity of natural sand. This growth can be attributed to several key factors:
- Infrastructure Projects: Countries are ramping up construction initiatives to improve their infrastructure, leading to a surge in demand for concrete and other aggregate materials, where manufactured sand fits in perfectly.
- Construction Codes: As regulations evolve, particularly in environmental standards, many projects now require blends containing manufactured sand, creating a consistent demand.
- Quality Assurance: The ability to monitor the quality of manufactured sand closely leads to increased trust from builders and engineers, resulting in wider adoption.
Furthermore, as the industry continues to innovate, the demand for specific characteristics in sand becomes clearer. For instance, the need for sands with specific gradations or texture suited for high-performance concrete widens the market.
Cost Analysis
Cost remains a significant factor when evaluating manufactured sand's viability compared to natural sources. While the initial investment for setting up production may be steep, the long-term financial benefits often outstrip these costs. Here are some considerations regarding cost analysis:
- Production Costs: Manufacturing sand can involve expenses related to the operation of crushing and screening equipment. However, depending on local conditions, the cost can often be reclaimed through minimized transportation costs if the production sites are strategically located.
- Variability in Pricing: Unlike natural sand, which is subject to unpredictable supply and demand cycles, manufactured sand tends to offer price stability, which is appealing for long-term projects.
- Resource Allocation: Saving natural resources by switching to manufactured sand can significantly reduce costs associated with mining and extraction, not to mention the potential fines and legal repercussions from over-extraction efforts.
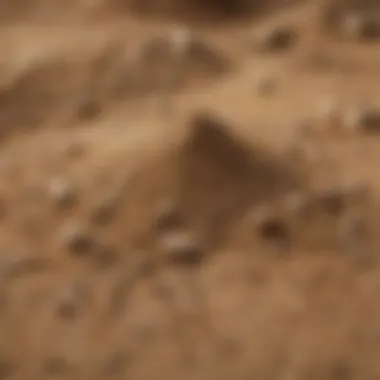
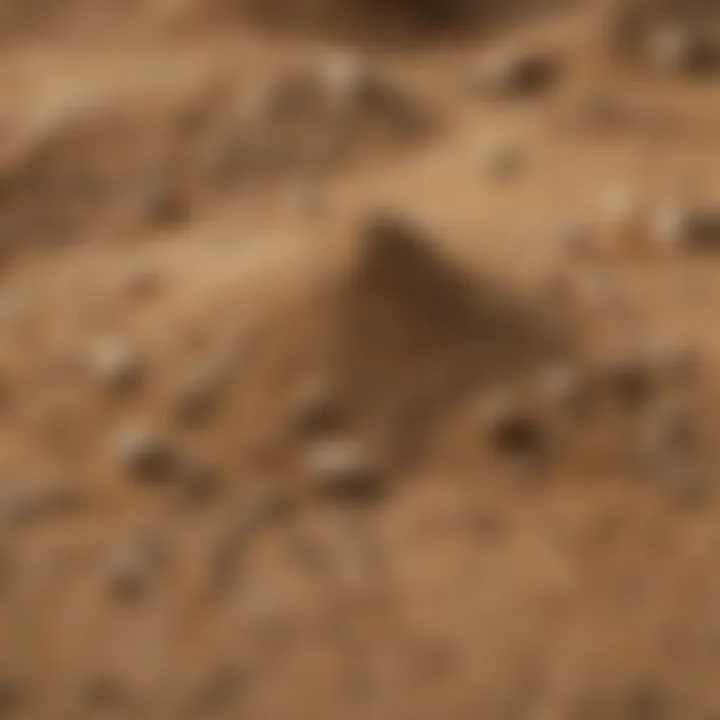
"Sustainable practices not only protect natural resources but also bolster long-term economic viability in construction."
In closing, the economic implications of manufacturing sand must be viewed through the lens of sustainability and innovation within the construction industry. The shifting market dynamics, coupled with the advantages of manufactured sand, present a unique landscape for stakeholders to consider as they strategize for future building projects.
Applications of Manufactured Sand
Manufactured sand, often known as crushed sand or artificial sand, has carved out a notable niche in various sectors, primarily the construction industry. Its emergence is not merely a result of resource scarcity, but a reflection of its enhanced performance characteristics that make it adept for modern construction needs. Understanding the applications of manufactured sand is pivotal, as it highlights its multifaceted benefits, potential challenges, and the overarching significance in sustainable resource management.
Construction Industry Utilization
The construction industry stands as the most significant benefactor of manufactured sand. With urbanization on the rise and infrastructure development soaring, the demand for high-quality aggregates has surged. Manufactured sand serves as a perfect substitute for natural sand, especially in locations where natural sources are depleted or protected due to environmental legislation.
- High Compatibility: Manufactured sand blends seamlessly with various construction materials, resulting in higher bonding strength. This is especially crucial when producing concrete that requires stability and durability.
- Particle Shape: The angularity and rough texture of manufactured sand enhance the interlocking ability of particles, leading to stronger concrete compared to conventional sand. This characteristic enables structures to withstand greater loads.
- Reduced Workability Issues: Unlike some natural sands, manufactured sand doesn't typically lead to segregation or bleeding when mixed, which means it performs consistently across different batches. This consistency is a game-changer, especially on large construction sites where variations can lead to structural flaws.
Simply put, using manufactured sand in construction can lead to more durable and resilient structures, thereby contributing immensely to the long-term sustainability of built environments.
Use in Concrete and Masonry
The journey of manufactured sand through the realms of concrete and masonry is noteworthy. As construction methods evolve, the necessity for engineered materials that meet stringent standards and specifications has become fundamental. Manufactured sand fits the bill perfectly.
- Concrete Quality Improvement: In producing concrete, manufactured sand provides better control over the gradation, resulting in optimal workability and finishing qualities. This leads to reduced water-cement ratios, enhancing overall strength and durability.
- Eco-Friendly Alternative: Utilizing manufactured sand helps in minimizing environmental disturbances. Natural sand extraction often leads to ecological damage, whereas manufactured sand can be produced from waste and recycled materials. This not only reduces landfill usage but also lowers the carbon footprint associated with sand production.
- Flexibility for Masonry: In masonry applications, the finer and angular properties of manufactured sand allow for tighter compaction, thereby enhancing bond strength between bricks or blocks. This feature streamlines construction, making it faster and more efficient.
"In an era where sustainability is becoming a cornerstone of construction practices, the adoption of manufactured sand is not just a choice but a necessity."
In summary, the applications of manufactured sand within the construction and masonry sectors underline its importance as a reliable material in modern construction practices. As research expands and technologies evolve, the adoption and sophistication of manufactured sand will likely continue to grow, paving the way for innovative practices in how we build our structures.
Future Prospects in Sand Manufacturing
As we look toward the horizon of sand manufacturing, itโs clear that this field is more dynamic than it might seem at first glance. The future of manufactured sand is not merely about scaling production; rather, it encompasses a myriad of elements poised to reshape the landscape of the construction industry and beyond. The drive towards resilience against climate change, along with the growing demands for sustainable construction practices, fuels innovations in processes and technologies.
Innovations in this sector are more than just buzzwords. They're pivotal in addressing the escalating challenges of construction materials, which underpins the effectiveness and longevity of modern infrastructures. With increasing urbanization and a critical need for responsible resource management, the sand manufacturing industry is at a crossroads. This crossroads features advancements that promise to enhance not only the quality and efficiency of manufactured sand but also its accessibility and low environmental impact.
Innovations and Emerging Technologies
Among the heartbeats of progress in sand production are the innovations that keep rolling in. This isn't just about grinding up rocks anymore; manufacturers are exploring sophisticated machinery and methods that push the envelope. For instance, vertical shaft impact (VSI) crushers are leading the charge by producing high-quality sand with lower energy consumption compared to traditional methods. Additionally, robotic automation is emerging, allowing for precision processing and reduced human error.
Other innovations include:
- 3D printing technologies, which may utilize manufactured sand in creating intricate structures layer by layer.
- Nanotechnology, enhancing the granularity and performance characteristics of sand, which have implications for concrete strength and durability.
- Waste recycling methods, where by-products from other industries are transformed into viable alternatives for sand, effectively curtailing waste.
All these innovations can result in improved material performance and a marked decrease in the environmental footprint associated with traditional sand extraction.
Predictions and Industry Outlook
Looking ahead, the industry's outlook remains cautiously optimistic, yet full of potential. Given the trends on sustainability and the circular economy, experts suggest that manufactured sand will account for an increasingly significant share of construction material. Additionally, regulatory pushes towards eco-friendliness will likely hint at a more robust demand for alternatives to natural sand.
Specifically, several predictions can be made:
- Market Growth: The manufactured sand market is expected to witness a compound annual growth rate (CAGR) of over 6% in the next decade. This reflects not only an increase in construction needs but also a shift in preference towards more sustainable materials.
- Investment Surge: Venture capital and investment money are increasingly being directed towards startups focusing on innovative sand manufacturing methods, hinting at a fertile ground for growth.
- Technological Advancements: With advancements like artificial intelligence integrated into production processes, manufacturers can expect enhanced operational efficiencies, reducing waste and improving quality further.
"The future of sand manufacturing is tied closely to our ability to innovate. Sustainable practices are no longer optional; they are integral to survival in this landscape."
As industries evolve, keeping a keen eye on these trends is crucial. Engaging with the advancements and adapting to the changing demands can lead not just to survival but to thriving in this ever-competitive market.
Culmination and Recommendations
The examination of manufactured sand in this article underscores its growing importance in contemporary construction and environmental stewardship. As we draw to a close, itโs evident that manufactured sand presents solutions for the ongoing challenges faced in the construction industry. In light of depleting natural sand resources and increasing demand for sustainable materials, the call for a thorough understanding and smart application of manufactured sand is louder than ever.
Summary of Insights
Manufactured sand is not merely a substitute for natural sand. Its distinct physical and chemical properties enhance its suitability for various construction applications including concrete and asphalt production. The advantages of using manufactured sand are multifaceted:
- Resource Efficiency: With natural sand sources dwindling, manufactured sand emerges as a critical replacement, preserving valuable ecosystems.
- Consistency in Quality: The controlled production process allows for uniformity in grain size and shape, leading to improved performance in construction projects.
- Cost-Effectiveness: Despite the initial setup costs for manufacturing facilities, the long-term savings in materials and associated logistics often outweigh these investments.
Moreover, advancements in technology, explored in previous sections, hold promise for enhancing the properties of manufactured sand. The ongoing research into the materialโs ecological impact and performance ensures its applicability continues to evolve.
Future Research Directions
Looking ahead, there are several promising avenues for further exploration:
- Innovative Production Techniques: Research into more energy-efficient and environmentally friendly methods of production could yield significant benefits.
- Performance Studies: Long-term studies on the performance of manufactured sand in various construction applications are needed to better understand its durability and resilience.
- Regulatory Frameworks: As the industry grows, the formation of comprehensive standards and regulations can help maintain quality while promoting its usage. This aligns with environmental goals and promotes sustainable practices.
- Community Engagement: Understanding public perception of manufactured sand will be crucial in addressing concerns and promoting its adoption in local building practices.