Exploring the Science of Thermoplastic Polymers
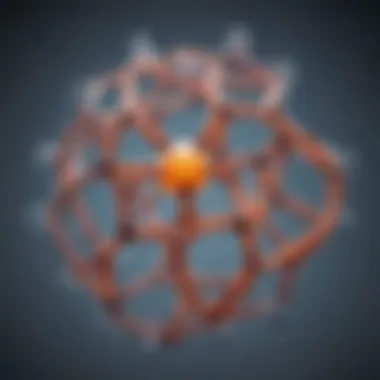
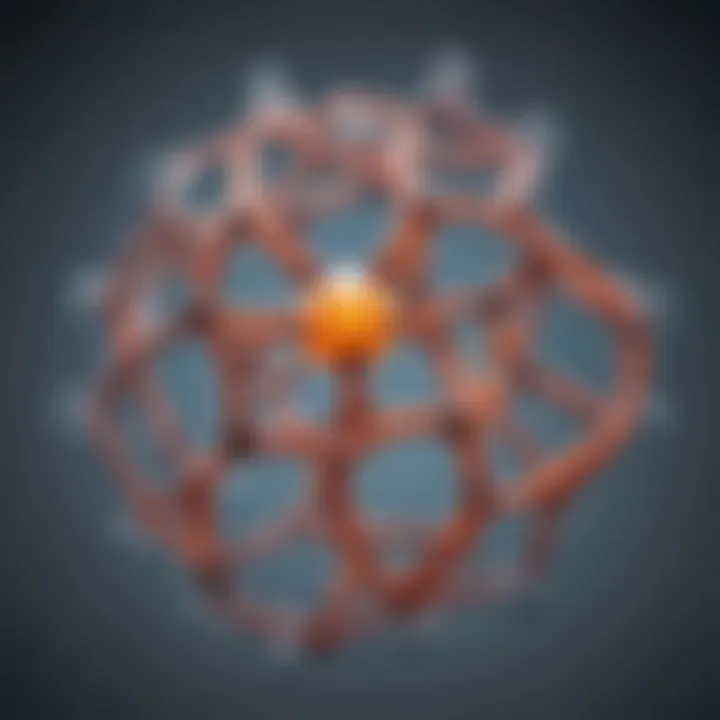
Intro
Thermoplastic polymers are unique materials, widely used in industry and daily life. They can be melted and reshaped multiple times without changing their chemical structure. This feature presents notable advantages in manufacturing and design.
By exploring their production processes, applications, and recent advancements, readers can gain a better insight into these versatile materials. Furthermore, this guide will also address recycling and sustainability issues tied to thermoplastics.
Recent Advances
Latest Discoveries
Recent research in the field of thermoplastic polymers has focused on enhancing their properties. Innovations in molecular structure have led to improved strength and flexibility. These advancements pave the way for applications in sectors such as aerospace and renewable energy.
Researchers have also uncovered new ways to combine thermoplastics with other materials. This fusion could yield materials with enhanced performance characteristics. For example, the merging of thermoplastics with nanomaterials offers promising results.
"The ability to mold thermoplastic polymers more efficiently is a game-changer for the manufacturing sector."
Technological Innovations
New technologies are emerging that revolutionize how thermoplastic polymers are processed. 3D printing has gained traction, allowing for customized applications. This method reduces waste and enables intricate designs that were impractical before. Moreover, advancements in extrusion and injection molding are streamlining production.
Development of bioplastics is another notable trend. These materials, derived from renewable biomass sources, aim to mitigate environmental impacts. Their integration into conventional plastic products is still in early stages, but shows promise for the future.
Analytical Approaches
Accessing the full potential of thermoplastic polymers requires a structured methodology. Through research design and data collection techniques, valuable information can be gathered. These techniques not only enhance understanding but also encourage innovation in the field.
Research Design
When studying thermoplastic polymers, a systematic research design is necessary. This approach includes defining objectives, choosing the right materials, and setting parameters for testing. Clearly structured experiments yield reliable data and enable reproducibility.
Data Collection Techniques
Various techniques are employed for data collection. Common methods include:
- Mechanical Testing: Evaluating tensile strength and elasticity.
- Thermal Analysis: Understanding behavior at various temperatures.
- Rheological Measurements: Assessing flow properties under different conditions.
By applying these techniques, researchers can effectively analyze thermoplastic polymers, paving the way for future breakthroughs.
Efforts to better understand these materials will help to address ongoing environmental concerns and improve material performance. Leaders in the field must stay informed about recent trends, enabling them to contribute to the evolution of thermoplastic polymers.
Intro to Thermoplastic Polymers
Thermoplastic polymers play a crucial role in the field of materials science due to their unique properties and versatility. Understanding these materials opens the door to a myriad of applications, ranging from everyday products to specialized industrial components. Their ability to be reshaped upon heating without significant chemical change sets thermoplastics apart from other polymer types. This characteristic not only simplifies recycling processes but also enhances manufacturing efficiency, as they can be repeatedly molded into various forms.
Additionally, thermoplastic polymers exhibit a wide range of physical and chemical properties, making them suitable for diverse applications. From low-density polyethylene used in packaging to high-performance polymers like polyetheretherketone in aerospace, their adaptability is noteworthy. Understanding the characteristics of thermoplastic polymers can aid engineers and designers in selecting the right material for their specific needs.
Factors such as cost-effectiveness and ease of processing contribute to their widespread use across multiple industries. However, there are also challenges, particularly concerning environmental impact. These factors make it imperative to delve deep into the defining aspects of thermoplastic polymers, their history, and what makes them integral to contemporary manufacturing processes.
Definition and Characteristics
Thermoplastic polymers are defined as polymers that can be melted and remolded. Their molecular structure consists of long chains of molecules that do not undergo any significant change during these thermal cycles. This means they can be melted, reshaped, and cooled back into solid form multiple times. Common characteristics include:
- Reprocessability: Can be reheated and reshaped without degradation.
- Variety: Includes a range of materials, such as polyethylene, polypropylene, and polystyrene.
- Chemical Resistance: Many thermoplastics exhibit good resistance to various chemicals, making them suitable for different environments.
- Lightweight: Generally lighter than metals, which is a significant advantage in applications like transportation.
To summarize, the defining characteristics of thermoplastic polymers heavily influence their applications in various sectors.
Historical Context
The history of thermoplastic polymers dates back to the early 20th century with the advent of synthetic materials. The first synthetic polymer, Bakelite, was developed in 1907 but was a thermosetting plastic. It wasn't until the 1920s and 1930s that true thermoplastics began to emerge. With the introduction of polyethylene in the 1930s and later polypropylene in the 1950s, these materials gained traction in the marketplace.
The post-World War II era saw significant advances in polymer science. The development of new processing technologies and the invention of copolymers expanded the applications of thermoplastics, making them essential in sectors like packaging, automotive, and consumer goods. The ability to mass-produce these materials enabled economies of scale, lowering costs and increasing accessibility.
As environmental concerns rose in the late 20th century, the focus on recycling and sustainability of thermoplastic polymers also increased. This historical evolution underscores the importance of understanding how these materials developed and adapted over time, influencing current practices and innovations in the field.
Molecular Structure of Thermoplastic Polymers
The molecular structure of thermoplastic polymers is fundamental to understanding their properties and applications. The way these polymers are built at a molecular level greatly influences their physical characteristics, including melting temperature, flexibility, and strength. Therefore, exploring the intricacies of polymer chains and how they affect the overall behavior of thermoplastics is crucial.
Polymer Chains and Configuration
Thermoplastic polymers consist of long chains of repeating molecular units known as monomers. These chains can vary in length and arrangement. The configuration of these polymer chains can be linear, branched, or cross-linked, each leading to different material properties.
- Linear Chains: In linear polymers, such as polyethylene, the chains are straight and can pack closely together. This configuration usually results in higher density and greater strength.
- Branched Chains: Polymers like low-density polyethylene have branches off the main chain. This structure can lead to lower density and more flexibility, making them suitable for applications requiring resilience and adaptability.
- Cross-Linked Chains: Some thermoplastics can have cross-linked structures, which create a network of chains. This configuration can enhance thermal stability and impact resistance but also alters the thermoplastic nature, making them sometimes behave like thermosetting polymers instead.
Understanding these configurations allows industries to select the appropriate polymer for specific functions, optimizing performance in various environments and applications.
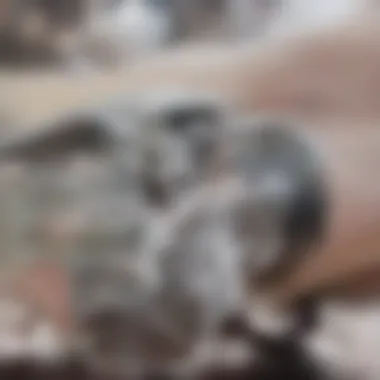
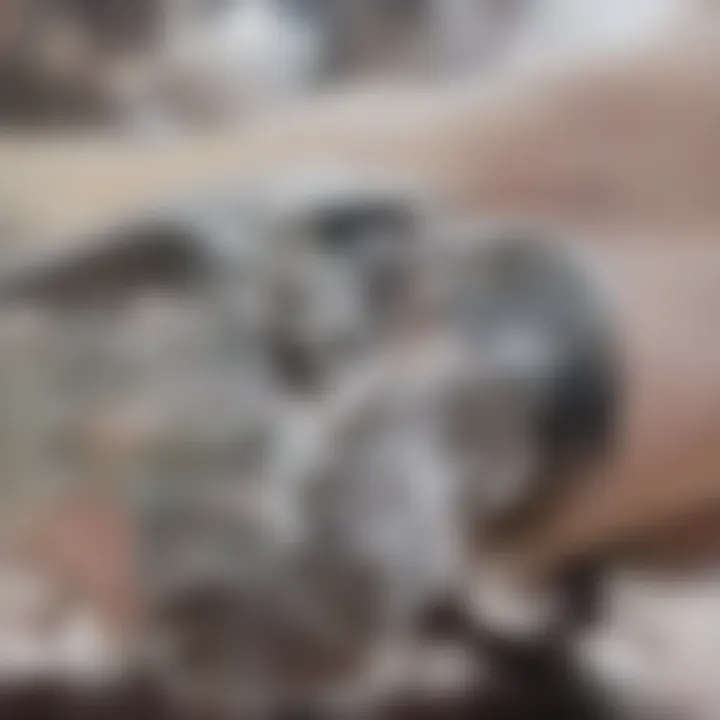
Effects of Molecular Weight
The molecular weight of a thermoplastic polymer is another significant factor influencing its properties. Molecular weight refers to the mass of a single polymer molecule and can have profound ramifications on the behavior and applications of the material.
Higher molecular weight generally correlates with improved physical properties such as:
- Increased Strength: A higher density of chains within the structure typically results in improved tensile strength and impact resistance.
- Enhanced Thermal Stability: Materials with a greater molecular weight often exhibit higher melting and glass transition temperatures.
- Increased Viscosity: The melt flow rate decreases with higher molecular weight, impacting processing methods, such as injection molding and extrusion.
Conversely, lower molecular weights can allow for easier processing but may lead to diminished mechanical performance. Thus, a careful balance is necessary for generating effective thermoplastic materials.
Understanding the interplay between molecular structure and performance is essential for predicting polymer behavior under various conditions.
By analyzing the chain configurations and their associated molecular weights, one can better appreciate how thermoplastic polymers can be tailored to meet specific needs across a wide spectrum of applications.
Thermal Properties of Thermoplastic Polymers
The thermal properties of thermoplastic polymers are essential to understand their performance and application in various fields. These properties influence how these materials behave under different temperature conditions, guiding material selection for specific applications. An insight into the thermal characteristics allows engineers and designers to anticipate the functional limits of thermoplastics in practical scenarios. Key aspects such as melting temperature, glass transition temperature, and thermal conductivity play pivotal roles in defining the usability of thermoplastic materials.
Melting Temperature and Glass Transition Temperature
Melting temperature (Tm) is a critical point in the thermal properties of crystalline thermoplastic polymers. It represents the temperature at which a solid material transitions to a liquid. This property is significant because it directly impacts processing temperatures during manufacturing. Understanding the melting temperature allows for optimal processing conditions, ensuring adequate flow and shaping without degrading the material.
In contrast, the glass transition temperature (Tg) marks the change from a hard and relatively brittle state to a viscous or rubbery state in amorphous polymers. For thermoplastic polymers, the glass transition temperature is particularly important when considering their flexibility and ability to be processed. A material’s applications often depend on whether it remains plastic during use or becomes rigid, impacting its performance in products ranging from packaging to medical devices.
Both melting and glass transition temperatures vary significantly based on molecular structure, composition, and other factors. For example, Polyethylene exhibits a lower melting temperature compared to Polycarbonate, which affects product design and utility in thermal applications. It is critical for designers to be aware of these temperatures, as they dictate the maximum service temperature and the operational stability of materials under heat exposure.
Thermal Conductivity
Thermal conductivity is another vital thermal property of thermoplastic polymers. It refers to the material’s ability to conduct heat, which can be crucial for applications where temperature control is necessary. Polymers with high thermal conductivity are used in situations where heat dispersion is needed, such as in electronics or automotive components, helping manage thermal loads effectively.
The level of thermal conductivity in thermoplastics often influences insulation properties, affecting energy efficiency in building materials or consumer goods. Understanding this characteristic helps in selecting the right material to achieve desired thermal performance, whether it is for insulation, heat resistance, or heat management.
"Thermal properties determine usability and service life of thermoplastic polymers in diverse applications."
Production Techniques
The production techniques of thermoplastic polymers play a crucial role in determining their final properties, usability, and overall efficiency in various applications. Understanding these production techniques is essential for researchers and professionals within material science and engineering. They not only influence the mechanical characteristics of the polymers but also their compatibility with specific applications and their performance in diverse environments. By exploring polymerization methods and processing technologies, one can grasp how thermoplastic polymers are created and how their production affects their subsequent applications.
Polymerization Methods
Addition Polymerization
Addition polymerization is a key method in the production of thermoplastic polymers. This process involves the joining of monomers with unsaturated bonds, resulting in a large polymer chain. One notable characteristic of addition polymerization is its ability to create polymers swiftly and efficiently, which is often appealing in industrial contexts.
The unique feature of addition polymerization is that no by-products are formed during the reaction. This efficiency contributes to its popularity as a method for producing specific polymers such as polyethylene and polypropylene. The advantages of this method include a straightforward process and high yield. However, one drawback can be that it may not always offer the level of variation in polymer structure compared to other techniques.
Condensation Polymerization
Condensation polymerization is another significant method for producing thermoplastic polymers. In this process, monomers bond together, and typically, a small molecule, such as water, is released as a by-product. The key characteristic of condensation polymerization is its ability to create polymers with a varying degree of functionalities, leading to a diverse range of polymer structures.
This method is beneficial for synthesizing materials like nylon and polyesters. The unique feature here is the potential for different chemical functionalities in the polymers, which can influence the properties significantly. On the downside, the formation of by-products may complicate purification processes and affect yields. This aspect is particularly important when considering large-scale production scenarios.
Processing Technologies
Extrusion
Extrusion is a vital processing technology for thermoplastic polymers, enabling the continuous forming of products. This method involves forcing melted polymer through a die to create various shapes, such as sheets or tubes. Its key characteristic is efficiency in producing large quantities of products with consistent cross-sectional profiles.
Extrusion has gained popularity due to its high output and ability to process a variety of thermoplastic materials. The unique feature lies in its versatility, allowing complex shapes and structures to be formed. However, care must be taken with temperature control to avoid degrading the material, posing a challenge in maintaining quality during production.
Injection Molding
Injection molding is a widely used method for producing complex and precise shapes in thermoplastic polymers. In this process, melted polymer is injected into a mold, where it cools and solidifies to form the desired product. Its key characteristic is the ability to create intricate designs at a scale that is economically viable.
The benefits of injection molding include rapid production cycles and excellent repeatability. This method is particularly favored for creating consumer goods and automotive components. Despite this, the initial cost of mold design and fabrication can be high, which may limit its usage for low-volume production runs.
Blow Molding
Blow molding is another processing technique critical to creating hollow thermoplastic products, such as bottles. The process involves inflating a heated plastic tube inside a mold, allowing the plastic to take the shape of the mold. A significant characteristic of blow molding is its efficiency in producing lightweight, strong structures.
It is a popular choice for industries focused on packaging, due to its ability to create seamless and lightweight containers. The unique feature of blow molding is the capacity to produce items in high volumes with minimal waste. However, it also requires precise temperature control and may not be suitable for all thermoplastic types.
The production techniques of thermoplastic polymers determine not just the viability of material in production, but also the end-use performance, making it essential to master these methods.
Common Types of Thermoplastic Polymers
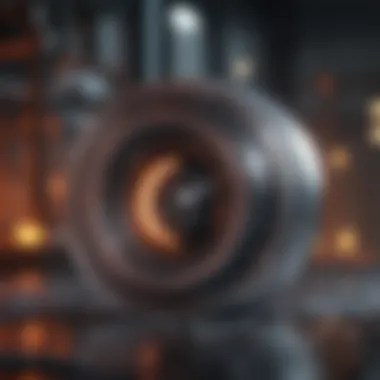
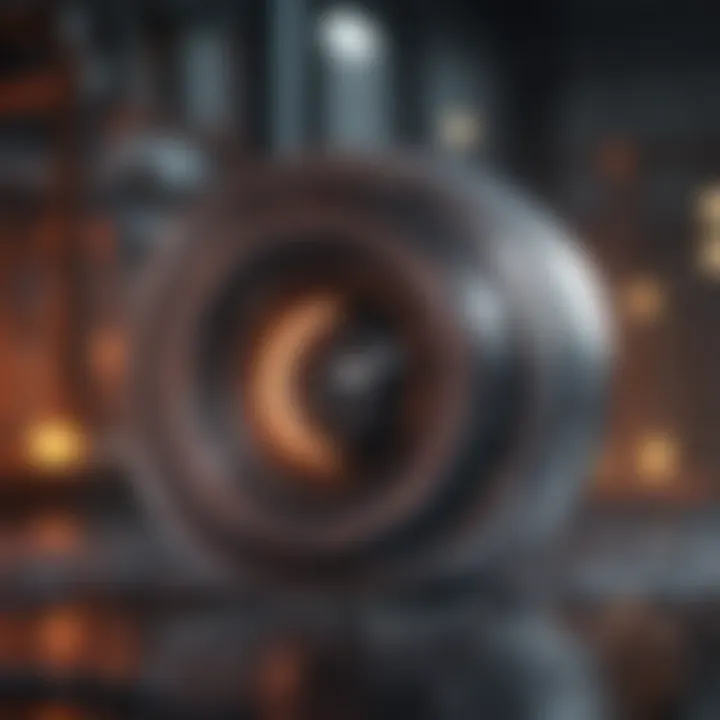
Understanding the common types of thermoplastic polymers is essential for comprehending their diverse applications and configuring relevant production processes. Each type has unique properties and characteristics that make them suitable for specific uses. The importance of this topic lies in the foundational role these polymers play in multiple industries—from packaging to automotive manufacturing. The benefits, considerations, and applicability of these thermoplastics are paramount for students, researchers, educators, and professionals alike.
Polyethylene
Polyethylene is one of the most widely used thermoplastic polymers. Its simplicity in structure allows for varying densities: low-density polyethylene (LDPE) and high-density polyethylene (HDPE).
- Properties: LDPE is flexible, while HDPE is more rigid and stronger. This versatility makes them suitable for different applications.
- Uses: Polyethylene is prominent in packaging, plastic bags, and containers due to its low cost and resistance to moisture.
- Considerations: While it is a widely used material, its environmental impact and recyclability are important aspects to consider.
Polypropylene
Polypropylene stands as another important thermoplastic, known for its toughness and fatigue resistance. It is less dense than polyethylene, making it lighter yet strong.
- Properties: Polypropylene has excellent chemical resistance and thermal stability, making it ideal for applications that require enduring strength.
- Uses: Commonly, it is found in automotive parts, textiles, and various containers since it offers good mechanical performance at a lower cost.
- Considerations: Recycling programs for polypropylene are developing but remain limited, requiring awareness of proper disposal methods.
Polyvinyl Chloride
Polyvinyl chloride, or PVC, is notable for its rigidity and chemical resistance. It exists in both flexible and rigid forms, adapting to numerous applications.
- Properties: Rigid PVC is used in construction, such as pipes and door frames, while flexible PVC is used for wiring and plumbing.
- Uses: Its waterproof nature and durability make it popular in construction, healthcare, and packaging.
- Considerations: The production and disposal of PVC have raised concerns due to toxic additives, necessitating advancements in sustainable practices.
Polystyrene
Polystyrene is recognized for its versatility, being available in solid and foam forms. This material can be rigid or foamed, enhancing its usability.
- Properties: Rigid polystyrene is often crystal clear, while foam polystyrene, often known as Styrofoam, is lightweight yet provides excellent insulation.
- Uses: It is used in packaging materials, disposable cups, and insulation in buildings.
- Considerations: The environmental impacts of polystyrene, especially in foam form, are concerning due to its inability to biodegrade.
Acrylics
Acrylics, particularly polymethyl methacrylate (PMMA), are known for their clarity and UV resistance. These properties make them ideal replacements for glass in many applications.
- Properties: Acrylics are lightweight and shatter-resistant, making them a safe alternative in various contexts.
- Uses: They are common in signage, display cases, and lenses for glasses.
- Considerations: Like other thermoplastics, acrylics also have recycling concerns but can be processed effectively using existing technologies.
With a clear understanding of these common types of thermoplastic polymers, stakeholders can effectively choose the right material for their requirements, balancing functionality and sustainability.
Applications of Thermoplastic Polymers
Thermoplastic polymers play a vital role in various industries due to their unique properties and adaptability. Understanding their diverse applications provides insight into their significance in advancing technology, improving efficiency, and meeting consumer demands. This section delves into the specific sectors where thermoplastic polymers are utilized, detailing their benefits and the factors influencing their applications.
Packaging Industry
The packaging sector is one of the largest consumers of thermoplastic polymers. Materials like polyethylene and polypropylene are widely used due to their excellent barrier properties, flexibility, and durability. Products packaged with thermoplastics are often more lightweight than those made with glass or metal, which reduces transportation costs and energy consumption during distribution.
Additionally, these materials can be easily molded into various shapes and sizes, enhancing their usability in packaging design. For instance, polyethylene terephthalate (PET) is often chosen for beverage bottles, owing to its resistance to impact and moisture.
"The packaging industry's demand for lightweight and versatile materials continues to drive innovation in thermoplastic design."
The recyclability of thermoplastic polymers further addresses sustainability concerns in packaging. More companies are pursuing eco-friendly practices by using recycled materials or designing products that can be easily recycled.
Automotive Applications
In the automotive sector, thermoplastic polymers are valued for their lightweight nature and high strength-to-weight ratio. Materials like polycarbonate and nylon are commonly employed in producing parts such as dashboards, bumpers, and under-the-hood components. Reducing vehicle weight is crucial for improving fuel efficiency and reducing emissions, making thermoplastic polymers an attractive solution.
Moreover, the processing capabilities of these materials allow for complex shapes that enhance aerodynamics. Heated thermoplastics can also be formed into components that resist high temperatures and chemical exposure, making them suitable for demanding applications within vehicles.
Medical Uses
Thermoplastic polymers find significant applications in the medical sector due to their biocompatibility and ease of sterilization. Materials such as polyvinyl chloride (PVC) and poly(lactic acid) (PLA) are often used in medical devices, surgical instruments, and packaging for sterile products.
The adaptability of thermoplastics allows for customization according to specific requirements, such as flexibility for catheters or strength for implants. Furthermore, the ability to produce intricate designs enhances the functionality of medical devices in aligning with patient needs.
Consumer Goods and Electronics
In consumer goods and electronics, thermoplastic polymers contribute to the design and production of a wide range of products. From toys to smartphone casings, polymers like acrylic and polypropylene are favored for their aesthetic appeal and durability.
These materials can be easily colored and molded, allowing manufacturers to create innovative designs that attract consumers. Thermoplastics also provide electrical insulation, making them essential in electronic components where safety is paramount. Their resilience against wear and tear improves product longevity, adding value to consumer goods.
Advantages of Thermoplastic Polymers
Thermoplastic polymers offer numerous advantages that make them a popular choice in various industries. Their unique properties, which stem from their molecular structure and processing capabilities, contribute significantly to their functionality. In this section, we will discuss three main advantages: recyclability, cost-effectiveness, and versatility in application. Understanding these benefits provides insight into why thermoplastic polymers are widely used and how they continue to evolve in response to market demands.
Recyclability
One of the most significant advantages of thermoplastic polymers is their recyclability. Unlike thermosetting polymers, which cannot be remolded after being set, thermoplastics can be continuously reheated and reshaped. This property not only allows for the recovery of material but also reduces waste in production processes. The recycling process for thermoplastics typically involves collecting used polymers, cleaning them, and then either melting them down to form new products or using them in the production of other materials.
The environmental impact of recycling thermoplastic polymers is noteworthy. For industries focused on sustainability, using recycled materials helps reduce reliance on virgin resources, minimizing the carbon footprint. Furthermore, this process aligns with global efforts to reduce plastic waste. By enhancing the economic viability of recycled products, thermoplastics contribute to a circular economy, promoting responsible consumption and production practices.
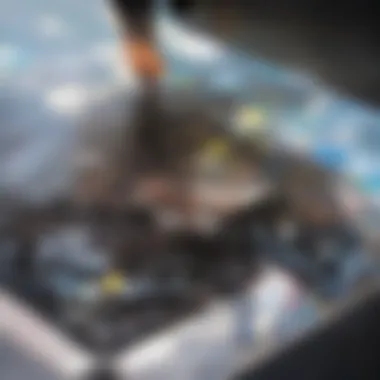
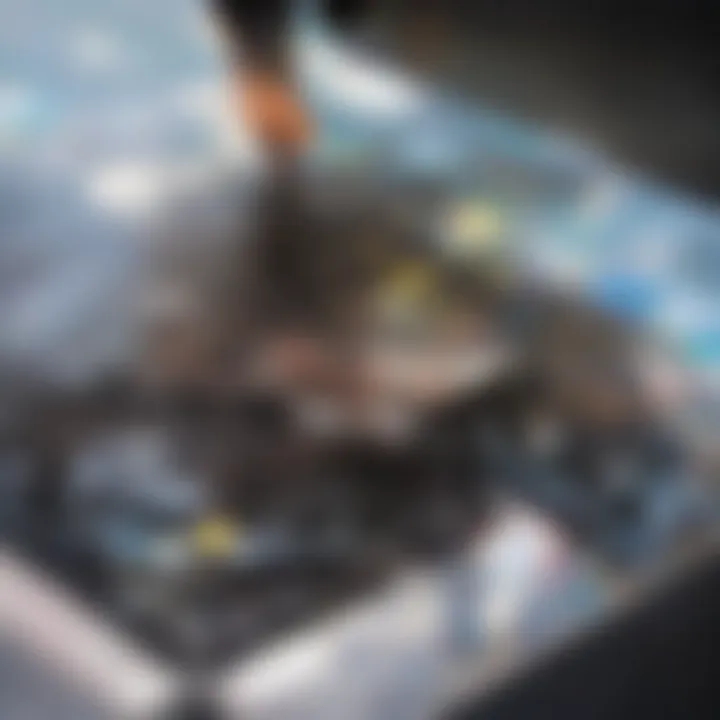
"Recyclability plays a vital role in mitigating the negative environmental impact traditionally associated with plastic use."
Cost-Effectiveness
Cost-effectiveness is another essential aspect of thermoplastic polymers. The production processes for these materials are often less complex and less energy-intensive compared to their thermosetting counterparts. The ability to reuse materials and the relatively low-cost production methods makes thermoplastics attractive for manufacturers.
In addition, when considering lifecycle costs, thermoplastics often prove to be economical solutions. They require lower maintenance costs and can offer a longer usage life, due in part to their inherent properties such as durability and resistance to various chemicals and environmental conditions. Consequently, for businesses, investing in thermoplastic materials may lead to substantial cost savings over time.
Versatility in Application
Thermoplastic polymers are renowned for their versatility, enabling their use in a wide range of applications across multiple industries. From packaging materials to automotive parts and medical devices, thermoplastics can be tailored to meet specific performance requirements. This customization is possible due to the various polymer types available, each possessing unique characteristics.
Their adaptability extends beyond mere applications. Thermoplastics can be blended with additives to enhance properties such as heat resistance, flexibility, or color stability, providing manufacturers with a vast toolkit for product development. Such versatility ensures that thermoplastic polymers are well-suited to meet evolving consumer needs while also contributing to advanced manufacturing processes.
In summary, the advantages of thermoplastic polymers lie in their recyclability, cost-effectiveness, and versatility. These characteristics make them essential materials in modern manufacturing and sustainable practices. As industries continue to seek sustainable solutions to environmental challenges, the role of thermoplastic polymers will likely expand further.
Challenges and Limitations
Understanding the challenges and limitations of thermoplastic polymers is essential for anyone involved in materials science and engineering. These factors not only impact the material's performance but also its application in various industries. While thermoplastic polymers offer numerous benefits, such as versatility and recyclability, they also face significant concerns related to environmental impact and mechanical properties.
Environmental Concerns
The environmental repercussions associated with thermoplastic polymers are a growing concern that cannot be ignored. The production process can produce substantial greenhouse gas emissions. Furthermore, the accumulation of plastic waste presents a serious challenge. Most thermoplastic polymers are non-degradable, leading to pollution in oceans and on land. Initiatives to mitigate these effects include:
- Recycling Initiatives: Efforts to improve recycling rates to keep plastics from ending up in landfills.
- Biodegradable Alternatives: Development of biodegradable polymers that could mitigate environmental impact.
- Education and Awareness: Informing the public about proper disposal and recycling methods.
Some researchers argue that without stringent regulations and improved technologies, the plastic crisis will worsen. However, many companies are working to create advanced solutions that can potentially offset the environmental challenges posed by traditional thermoplastic materials.
Mechanical Properties
The mechanical properties of thermoplastic polymers present another layer of complexity. These materials are known for their flexibility and toughness, but they also exhibit weaknesses, particularly under stress and temperature variations. High temperatures can lead to deformation, and low temperatures may make the material brittle. Some key points about mechanical properties include:
- Tensile Strength: This varies among different types of thermoplastic, impacting their application suitability.
- Impact Resistance: Certain thermoplastics, like polycarbonate, have good impact resistance, but others may shatter under severe conditions.
- Heat Resistance: Temperature limits are crucial for many applications, affecting longevity and durability.
It’s crucial for engineers and designers to understand these properties when selecting thermoplastic materials for specific applications. Considerations such as safety, longevity, and functionality often hinge on the mechanical attributes of the chosen polymer.
"While the advantages of thermoplastics are considerable, understanding their limitations ensures informed decisions in their applications."
By recognizing these challenges and limitations, stakeholders can promote better designs and innovations that align with sustainability and efficiency objectives. Emphasizing research and development in these areas is vital to fostering improvements in thermoplastic polymers.
Future of Thermoplastic Polymers
Thermoplastic polymers play a crucial role in various industries today. As technology advances, their potential continues to expand. This section explores the future of thermoplastic polymers, emphasizing innovations, sustainability efforts, and their implications for global markets.
Innovations and Advancements
The landscape of thermoplastic polymers is evolving swiftly due to ongoing research and innovation. New materials are being developed that offer improved properties and functionalities. For instance, high-performance thermoplastics like Polyether Ether Ketone (PEEK) are gaining traction in industries demanding exceptional strength and heat resistance, such as aerospace and automotive.
Moreover, advancements in polymer processing technologies enhance product design flexibility. Techniques like 3D printing are becoming more common. This allows for rapid prototyping, customization, and the ability to create complex shapes. This change is particularly beneficial in fields like medical devices and consumer electronics where precision is critical.
Researchers are also exploring bio-based thermoplastic polymers derived from renewable resources. These materials aim to reduce dependency on fossil fuels while maintaining performance characteristics comparable to conventional thermoplastics.
Sustainability Efforts
The growing emphasis on sustainability influences the future of thermoplastic polymers significantly. As environmental concerns rise, both consumers and manufacturers are pushing for greener alternatives. This trend drives research toward biodegradable options, which could mitigate pollution and waste.
Efforts are underway to enhance the recyclability of existing thermoplastic products. Many already contain recycled content, but innovations aim to increase the rates of recycling. For example, the chemical recycling process can break down polymers into their original monomers, enabling the production of high-quality new materials.
"The transition to sustainable thermoplastic options is not just a trend; it's a necessity for the health of our planet."
To further support sustainability, companies are investing in life cycle assessments (LCA). This method evaluates the environmental impacts of their products from material extraction to end-of-life disposal. Understanding these impacts helps in making informed decisions about production methods and material selection.
The future of thermoplastic polymers is promising, driven by innovation and a commitment to sustainability. The ongoing efforts in research and development will continue to shape the industry, enabling the creation of materials that not only perform well but also align with environmental priorities.
Culmination
This section not only wraps up the discussion but also highlights the practical implications of these polymers in daily life and industry. The ability of thermoplastic polymers to be reshaped upon heating without undergoing chemical change underlines their versatility and importance in contemporary applications. Additionally, the challenges and considerations surrounding their recycling and environmental impact warrant attention, as they shape the future of materials science.
In summary, the conclusion reaffirms the significance of thermoplastic polymers, guiding the reader to reflect on both the benefits and the responsibilities inherent in their use.
Recap of Key Points
- Versatility: Thermoplastic polymers can be reshaped, contributing to a wide array of applications across industries.
- Production: Awareness of production methodologies, such as different polymerization methods, greatly impacts both quality and application.
- Thermal Properties: Understanding thermal behavior like melting temperature is essential for selecting the appropriate polymer for desired uses.
- Environmental Considerations: Challenges regarding recyclability and sustainability are critical in advancing polymer technologies.
Final Thoughts on Thermoplastic Polymers
Thermoplastic polymers represent a significant advancement in material science. Their ability to provide both performance and adaptability makes them invaluable in modern products. As industries continue to evolve, thermoplastic polymers will likely adapt alongside new technologies and societal demands.
Innovations in recycling technologies and material design could greatly enhance their sustainability profile. It is crucial for researchers and practitioners to engage with ongoing developments in this field to harness the full potential of these polymers responsibly. Such efforts will not only improve product efficiencies but also contribute to a sustainable future.
"The future of thermoplastic polymers hinges on our commitment to innovation and sustainability."
With an informed understanding of their properties and implications, stakeholders can make more educated decisions, promote responsible usage, and drive positive change.