X-Ray Welding: Advanced Techniques and Applications
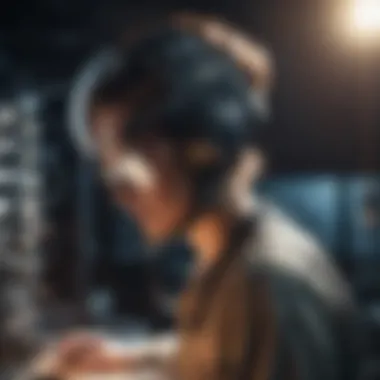
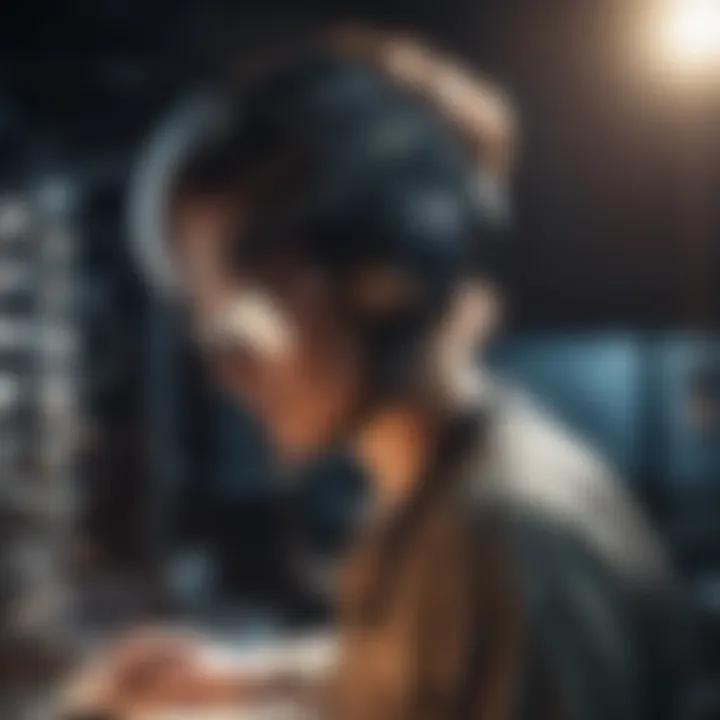
Intro
X-ray welding represents a notable advancement in the field of welding technology. This technique leverages the unique properties of electromagnetic radiation to join materials at a molecular level. This article investigates various aspects of x-ray welding that make it an exceptional method in the welding industry today. It aims at providing a well-rounded analysis that encompasses not just the principles and methodologies but also the safety protocols critical to its adoption.
Recent Advances
In recent years, x-ray welding has witnessed several significant advancements that enhance its effectiveness and applicability in multiple sectors.
Latest Discoveries
Research indicates that x-ray welding can achieve deeper penetration compared to traditional welding methods. This allows it to bond thicker materials effectively, making it suitable for industries such as aerospace and automotive. New studies show that optimizing the frequency and duration of x-ray exposure can result in stronger bonds while minimizing heat-affected zones.
Technological Innovations
Innovations in x-ray source technology have improved the efficiency of the welding process. For instance, the introduction of high-frequency generators has allowed welders to produce more consistent and higher quality welds.
Additionally, automated systems that utilize artificial intelligence are beginning to emerge in x-ray welding operations. These systems use real-time data to adjust parameters, ensuring optimum welding conditions are maintained throughout the process.
Methodology
Understanding the methodology behind x-ray welding is essential for appreciating its advantages and implications in various fields.
Research Design
The research on x-ray welding has primarily focused on both theoretical and practical analyses. Experimental setups in controlled environments allow researchers to study the interactions between x-ray radiation and different materials.
Data Collection Techniques
Data related to x-ray welding is usually collected through both direct observation and advanced imaging techniques. This includes techniques such as radiographic testing and metallographic examination. These methods provide critical insights into weld quality and help in assessing the feasibility of using x-ray welding in specific applications.
X-ray welding not only improves the strength of welds but also reduces the need for post-weld treatments, streamlining production.
Culmination
This analysis provides a broad understanding of x-ray welding and its potential impact across various industries. As technology progresses, x-ray welding will likely expand its influence, driven by innovations and an increasingly skilled workforce. The future holds promising developments that could refine this method further, opening doors to new applications and unprecedented efficiencies.
Prolusion to X-Ray Welding
X-ray welding represents a significant innovation in the field of welding technology. This section underscores the relevance of understanding this advanced technique, especially for those practicing in various industrial sectors. X-ray welding is not merely a technical skill; it integrates physics, materials science, and engineering principles, making it essential for students, researchers, educators, and professionals alike.
By exploring the importance of x-ray welding, we can appreciate its advantages over traditional methods. It produces high precision welds with minimal thermal distortion, catering particularly well to challenging materials and complex geometries. Moreover, the increasing demand for materials with superior performance characteristics in industries such as aerospace, electronics, and medical devices necessitates a thorough comprehension of x-ray welding.
As innovations continue, familiarity with the principles and applications of x-ray welding becomes imperative for professionals aiming to stay ahead in their fields.
Definition and Overview of X-Ray Welding
X-ray welding is a technique that employs x-ray radiation to fuse materials together. This process operates through the directed beam of x-rays that penetrate the materials, generating heat at the joint and encouraging them to bond. It is particularly effective for joining metals and other materials that traditional welding may not handle well. The use of x-rays allows for localized heating, minimizing the thermal impact on surrounding areas, which is crucial in processes where material integrity is paramount.
The primary advantage of x-ray welding lies in its precision. The technology enables small weld pools which lead to reduced thermal distortion. Additionally, x-ray welding can reach areas that are often challenging for conventional methods, expanding the potential applications of this technique. It has gained traction in sectors where precision and quality are non-negotiable, thus ensuring its position as a pivotal welding method in modern manufacturing.
Historical Background
The concept of x-ray welding originated in the early 20th century, coinciding with advances in x-ray technology. Initial experiments focused on understanding the effects of high-energy radiation on materials. As physics and materials science evolved, practical applications for these principles began emerging.
In the 1950s, researchers began to develop specialized equipment that could generate high-intensity x-ray beams. Their work marked a pivotal moment in the welding landscape, as industries started experimenting with this new method for precision tasks. Companies recognized the potential for x-ray welding to improve production efficiencies while maintaining the quality and reliability of their products.
The subsequent decades saw advancements in technology and technique as various industries adopted x-ray welding. Today, it stands as a refined technique, merging theoretical knowledge with robust practical execution. Understanding the historical context of x-ray welding enriches our grasp of its current implications and future possibilities.
Principles of X-Ray Welding
Understanding the principles behind X-ray welding is essential for comprehending its unique advantages and potential applications in various industries. The significance of these principles lies in their ability to enhance the precision and effectiveness of the welding process. X-ray welding employs high-energy radiation to melt and fuse materials at an atomic level. As such, grasping the fundamental concepts and mechanisms involved is vital for anyone looking to innovate in this field.
Fundamental Concepts
X-ray welding operates on several key principles that distinguish it from traditional welding techniques. The primary concept centers around the use of X-rays as a means to generate heat. Unlike conventional welding methods that rely on direct contact or chemical reactions, X-rays provide a non-contact source of energy. This energy can penetrate materials, heating them internally without the need for additional external force.
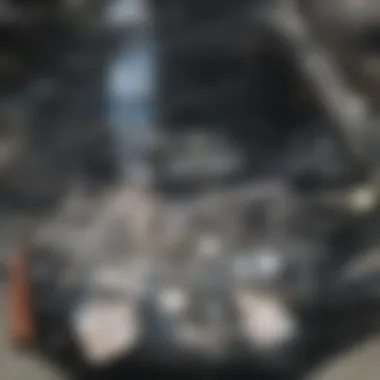
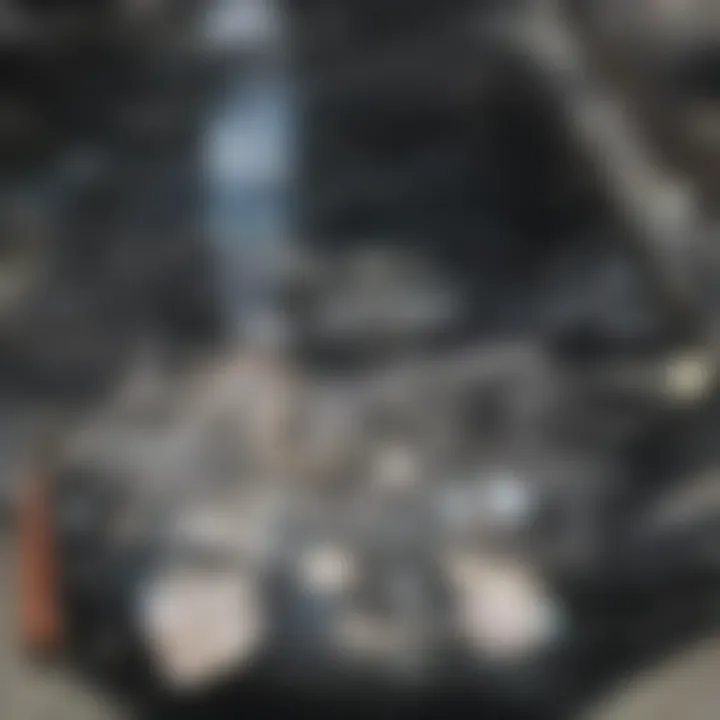
- Electromagnetic Energy: X-rays are a form of electromagnetic radiation, with shorter wavelengths than visible light. This characteristic allows them to penetrate deeper into materials and focus energy precisely where it's required.
- Heat Generation: When the X-ray beam interacts with the target material, it causes the atoms to vibrate. This molecular agitation leads to an increase in temperature, resulting in localized melting of the material surfaces that are being joined.
- Material Effects: Different materials respond distinctively to X-ray exposure. Factors such as atomic structure, density, and thermal conductivity play crucial roles in energy absorption and heat distribution.
These fundamental concepts establish the groundwork for understanding how X-ray welding is able to achieve superior bonding qualities.
Mechanisms of Energy Transfer
The mechanisms of energy transfer in X-ray welding are crucial for its application. The process primarily relies on the interactions between the X-ray photons and the material it targets. Several key aspects define this transfer of energy:
- Absorption and Scattering: When an X-ray beam strikes a material, some of the photons are absorbed while others scatter away. The absorbed photons transfer their energy, inducing heat within the material. The efficiency of this absorption varies with material types; metals generally absorb more efficiently than plastics or ceramics.
- Thermal Dynamics: Following absorption, the generated heat distributes within the material. This thermal flow can influence the depth of the weld, creating strong joints without significant surface distortion. Heat dissipation characteristics also impact the cooling rate, affecting the metallurgical properties of the bond.
- Energy Density: The focus of the X-ray beam is adjustable. A higher intensity in a concentrated area leads to better melting and bonding of materials. Controlling energy density is essential in applications requiring precision, such as in electronics and micro-fabrication.
X-ray welding allows for reduced thermal input compared to traditional welding processes, minimizing material distortion and enabling the joining of dissimilar materials effectively.
Understanding the mechanisms of energy transfer serves to emphasize the efficiency and adaptability of X-ray welding. Thereby, it becomes a critical technological choice in sectors where precision is paramount.
Methodologies in X-Ray Welding
Methodologies in X-Ray Welding are critical to the understanding and application of this welding technique. They shape the way practitioners approach various tasks, ensuring efficiency and quality. By diving into specific methodologies, one can grasp the nuances that distinguish X-ray welding from traditional methods. These methodologies also highlight the potential benefits they can bring to various industries, from precision engineering to intricate assembly lines.
Types of X-Ray Welding Techniques
X-ray welding encompasses several specific techniques, each designed for particular applications and material compatibility. Emphasis is placed on three prominent styles:
- Spot Welding: This technique is utilized primarily for joining thin materials. A focused beam of X-rays generates a small, concentrated heat source that melts the metal at specific points. It is ideal for applications requiring less distortion and high precision.
- Seam Welding: Here, the X-ray beam creates continuous welds in overlapping surfaces. This method allows for uniform distribution of heat, advantageous for materials that could warp or distort easily.
- Butt Welding: This method involves aligning two materials edge-to-edge. The X-ray beam heats the joint area, providing a strong bond while minimizing distortion. Butt welding is often preferred in high-strength applications, due to its robustness.
Understanding these techniques helps in addressing the appropriate contexts for X-ray welding applications. Each method has its benefits and limitations, which must be addressed based on the project's requirements.
Comparative Analysis with Traditional Welding
When comparing X-ray welding with traditional welding methods, several differences and advantages come to light. Traditional methods such as arc, MIG, and TIG welding use heat generated by electric arcs or gas flames. In contrast, X-ray welding uses high-energy radiation to accomplish similar results with notable efficiency.
Key Differences:
- Heat Source: X-ray welding relies on a concentrated energy beam, reducing the area affected by heat compared to traditional methods.
- Distortion: Due to the localized heating, X-ray welding produces less distortion in materials, which is vital for parts with tight tolerances.
- Speed: The precision offered in X-ray welding can lead to faster production times, as less post-weld treatment may be needed.
"X-ray welding poses solutions to challenges that are often faced in conventional processes, addressing critical needs in modern manufacturing."
While traditional methods remain valid in many contexts, X-ray welding offers unique advantages that make it an appealing option for specific applications. These include high-precision projects and sensitive materials, where X-ray welding excels without compromising the integrity of the material being worked upon. By evaluating both methodologies and their contexts, professionals can make informed decisions on the most suitable welding technique for their specific needs.
Applications of X-Ray Welding
X-ray welding's applicability spans a multitude of industries, providing advantages that enhance quality and efficiency. Understanding its diverse applications can shed light on its significance in modern practices. This section elaborates on the specific uses of x-ray welding across various sectors, highlighting technical benefits and considerations.
Industrial Uses
In industrial settings, x-ray welding is crucial for fabricating complex components. Aerospace and automotive industries make significant use of this technique. These fields require components that endure extreme stresses and environmental conditions. X-ray welding meets this by ensuring strong bonds with minimal distortion. Components such as turbine blades and structural frames can be produced with high precision. Additionally, x-ray welding allows for the joining of dissimilar materials, broadening design options.
The electronics industry also benefits from x-ray welding. It is used for assembling delicate components like circuit boards. The precision of x-ray welding minimizes heat exposure, reducing the risk of damaging sensitive electronic parts.
Key highlights of industrial uses include:
- High precision in complex welding tasks.
- Capability to join dissimilar materials effectively.
- Reduced risk of thermal damage in sensitive applications.
Research and Development Applications
In research and development, x-ray welding showcases its versatility. It serves as a tool for innovation, allowing researchers to experiment with new alloys and techniques. By combining materials that may not typically bond well, researchers can discover enhanced material properties. This exploration is vital in fields such as nanotechnology and materials science, where the goal is developing advanced composites.
Furthermore, x-ray welding facilitates rapid prototyping. The ability to create test models quickly allows engineers to move from concept to testing phases smoothly. This accelerates the development timeline for new products and technologies.
Research applications include:
- Exploration of new materials and weld techniques.
- Supports rapid prototyping in engineering projects.
- Facilitates development of advanced material composites.
Medical Applications
The medical field also benefits significantly from x-ray welding. This technique is employed in the manufacturing of medical devices and components requiring stringent quality standards. For example, surgical instruments and implants must be reliable and durable. X-ray welding ensures that these devices can withstand rigorous conditions without failure.
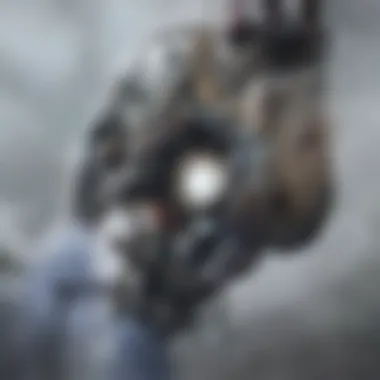
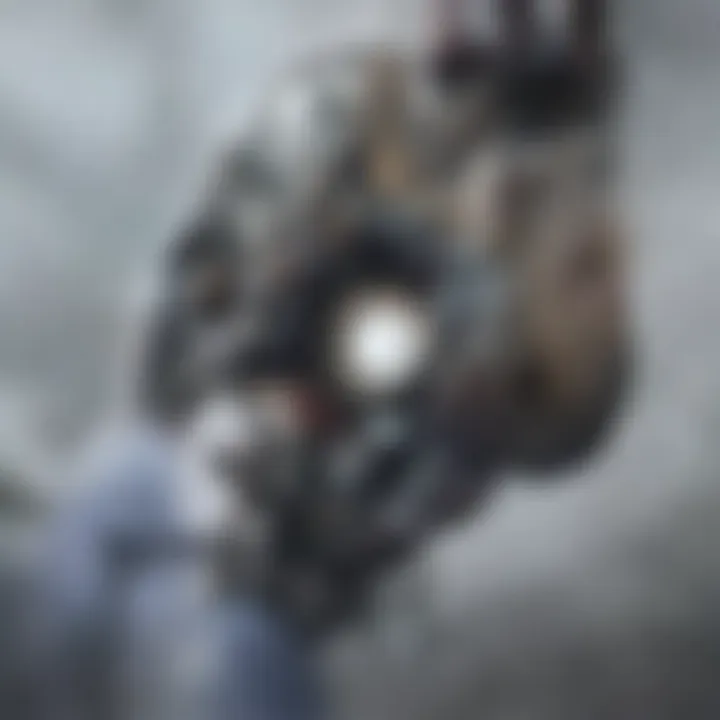
Additionally, x-ray welding plays a role in developing diagnostic equipment. Devices such as MRI machines or CT scanners require precision in their construction. Using x-ray welding, manufacturers can integrate components accurately, enhancing overall performance.
Advantages in medical applications are:
- Ensured reliability in critical medical devices.
- Precision in the fabrication of diagnostic equipment.
- Ability to create complex geometries in medical implants.
X-ray welding stands as a bridge connecting innovative design with stringent quality requirements across industries.
Through an analysis of x-ray welding applications, it becomes clear that this technology is vital for various sectors. Industrial, research, and medical uses illustrate its capability to enhance product quality and efficiency. As x-ray welding continues to evolve, its importance in modern technology will likely increase.
Advantages of X-Ray Welding
X-Ray welding presents significant advantages that distinguish it from traditional welding methods. Understanding these benefits is crucial for professionals, researchers, and students interested in advanced welding techniques. X-Ray welding not only enhances the quality of welded joints but also addresses various challenges faced in conventional welding.
High Precision and Quality
One of the most noteworthy advantages of X-Ray welding is the high precision it offers. Utilizing X-Ray technology allows for accurately focusing energy on specific areas, leading to better control over the welding process. This precision results in high-quality welds and minimizes defects such as porosity or cracks. The ability to achieve fine tolerances is particularly vital in sectors demanding stringent quality assurance, such as aerospace and medical device manufacturing.
Moreover, this method ensures a cleaner weld interface due to reduced heat input. The lower thermal impact means that the surrounding material is less likely to be altered during the welding process. Research indicates that the overall mechanical properties of the welded material often improve as a result of this innovative approach.
Reduced Distortion and Stress
X-Ray welding significantly reduces both distortion and residual stress in the materials being joined. Traditional welding methods often generate substantial heat, which can lead to warping or deformations. In contrast, X-Ray welding operates at lower temperatures, which minimizes thermal expansion and contraction. This characteristic is especially beneficial when working with thin or delicate components, as these materials are more susceptible to distortion.
By controlling the welding environment more effectively, X-Ray welding also mitigates the development of internal stresses. These stresses can potentially compromise the integrity of the welded structure over time. Industrial applications can benefit from using X-Ray welding, as it extends the lifespan and durability of critical components.
Enhanced Material Compatibility
X-Ray welding showcases enhanced compatibility with a wide array of materials. This versatility is a vital advantage in todayβs global market, where manufacturers often work with different types of alloys and composites. The technique can be effectively applied to metals, advanced ceramics, and even certain plastics, making it ideal for complex assemblies that require joining dissimilar materials.
Furthermore, this welding method demonstrates its capability in achieving effective joints in challenging situations. Some materials that are difficult to weld using conventional methods can be joined seamlessly through X-Ray technology. This capability opens up new avenues for innovation in product design and manufacturing, as engineers can explore more composite uses for their projects without being limited by traditional welding constraints.
"The ability to weld diverse materials with precision makes X-Ray welding a game-changer in modern manufacturing."
Safety Protocols in X-Ray Welding Operations
X-ray welding is an innovative technology that requires stringent safety protocols to protect those involved in the welding process. The importance of adhering to safety protocols cannot be overstated. These measures minimize health risks not only for the operators but for anyone in proximity to the welding area. The protocols include various strategies to ensure that exposure to harmful radiation is kept to a minimum.
Health Risks Associated with X-Ray Exposure
Exposure to X-ray radiation poses several health risks. The most significant concerns are related to the increased likelihood of developing cancer and other radiation-induced illnesses. Long-term exposure can lead to cumulative damage to biological tissues, resulting in conditions such as skin burns, cellular mutations, and potential harm to reproductive organs. It is crucial for individuals working in x-ray welding environments to be informed about these risks.
- Potential effects include:
- Increased cancer risk
- Skin burns
- Mutations in DNA
- Reduced fertility
Regulatory bodies such as the International Atomic Energy Agency (IAEA) and local health departments provide guidance on permissible exposure limits. Workers must stay aware of these guidelines to maintain their health while performing their job duties.
Preventative Measures and Statistical Guidelines
Implementing preventative measures can significantly reduce the risks associated with x-ray exposure. These measures should include:
- Regular training for all personnel in x-ray welding processes and safety protocols.
- Use of protective equipment, such as lead aprons, gloves, and barriers that shield against radiation.
- Monitoring radiation levels using dosimeters to ensure exposure does not exceed regulatory limits.
- Establishing safety zones around welding operations to minimize exposure risk to non-essential personnel.
Statistical guidelines provided by health agencies can help organizations to track exposure levels and incidents. Accurate record-keeping helps in evaluating the effectiveness of safety measures over time.
Technological Advancements in X-Ray Welding
Technological advancements play a pivotal role in the evolution of x-ray welding. As industries increasingly demand precision and efficiency, the innovations in this field allow for significant improvements in processes and outcomes. The fusion of advanced technology with traditional welding practices enhances the capabilities of x-ray welding, making it suitable for a range of applications that require high-quality joinery.
Innovations in Equipment and Techniques
Recent innovations in x-ray welding equipment have transformed how welders approach their tasks. Modern x-ray welders now incorporate sophisticated systems that automate various processes, thereby reducing the likelihood of human error. Equipment such as advanced x-ray sources, real-time imaging systems, and enhanced control mechanisms allow for more accurate placement and alignment during welding operations.
Moreover, improvements in shielding technology have significantly reduced the exposure to radiation for operators. The introduction of safety features like automatic shutoff systems and safety interlocks ensures that the working environment remains secure. Additionally, new software solutions enable better monitoring of weld integrity, allowing for timely adjustments during the welding process.
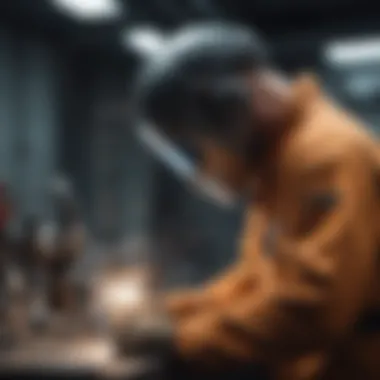
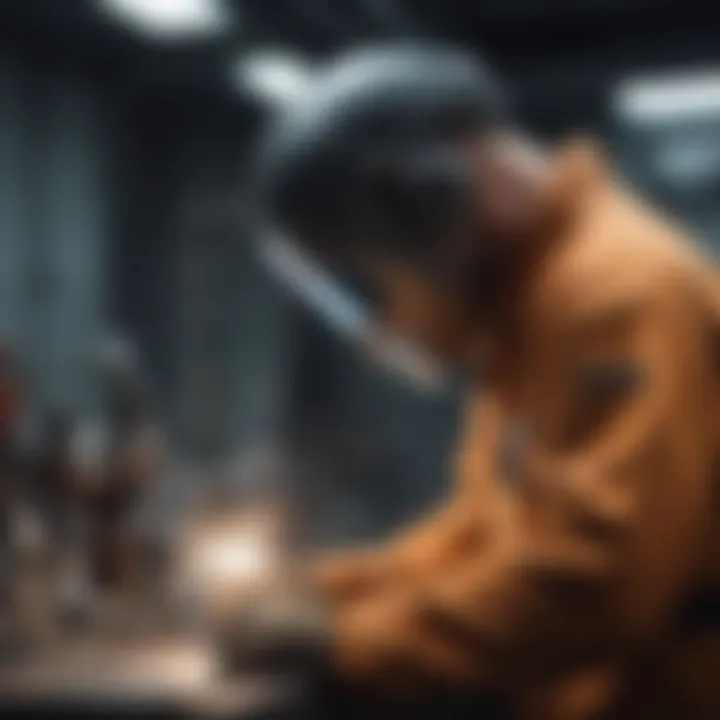
The adoption of hybrid welding technologies, combining x-ray methods with laser and electron beam welding, is also noteworthy. This integration provides a more versatile approach, expanding the range of materials that can be successfully welded while maintaining structural integrity. As a result, industries can now implement x-ray welding techniques in applications that were previously deemed impractical.
Future Trends in X-Ray Welding Technology
Looking ahead, several trends are emerging in the field of x-ray welding technology. One of the most significant is the increasing use of artificial intelligence (AI) and machine learning algorithms. These tools can analyze data patterns to optimize welding parameters, predict potential failures, and facilitate predictive maintenance. As a result, manufacturers can improve output quality while minimizing downtime.
Furthermore, there is a growing emphasis on sustainability within manufacturing processes. Engineers and researchers are exploring x-ray welding methods that consume less energy and produce fewer emissions. This aligns with global goals of reducing environmental impact, making x-ray welding an attractive option for eco-conscious businesses.
Another important trend is the rise of remote monitoring and control capabilities. With advancements in internet connectivity, welders can now operate and oversee welding processes from distant locations. This innovation is particularly valuable in industries where physical access to equipment may be limited, allowing for greater flexibility and responsiveness to issues as they arise.
"Embracing the latest advancements in x-ray welding not only improves efficiencies but also prepares industries for the future of manufacturing."
In summary, technological advancements in x-ray welding are integral to its development and acceptance in various sectors. The innovations in equipment and techniques, combined with future trends focusing on AI, sustainability, and remote operations, position x-ray welding as a crucial component in modern manufacturing.
Challenges in X-Ray Welding
X-ray welding presents unique challenges that are crucial to consider for effective implementation. Understanding these challenges helps stakeholders identify strategies for overcoming obstacles in both operational and economic aspects. Each factor contributes significantly to the overall potential of this welding method, ensuring it meets industry standards while serving practical applications.
Technical Limitations
Despite its advantages, x-ray welding comes with technical limitations. One of the most evident challenges is the requirement for precise alignment during the welding process. Any misalignment can lead to inconsistent weld quality or even structural failures. This demands advanced machinery and skilled operators, which may not be available in every production setting.
The type of materials also influences the efficacy of x-ray welding. Not all metals respond equally well to x-ray techniques, and certain high-density materials pose problems for efficient energy transfer. For instance, metals with high atomic numbers might absorb x-rays differently, leading to unwanted outcomes.
Additionally, achieving a uniform weld depth can be difficult. Variations in material thickness create areas where the x-rays may not penetrate fully, compromising the joint integrity. Continuous monitoring and adjustments are needed, further complicating the process.
Economic Considerations
The economic aspects of x-ray welding also warrant attention. The initial setup costs for x-ray welding systems are substantial. The specialized equipment, safety features, and training necessary can result in a high barrier to entry. Several small to medium enterprises find it hard to justify these expenditures, especially when traditional welding methods appear more economical.
Moreover, maintenance of x-ray welding machines can be costly. Regular servicing and the potential need for the replacement of components might strain budgets. These ongoing expenses can discourage businesses from adopting this advanced technology.
Another critical economic factor is the market demand for x-ray welded components. Industries must ensure that the benefits of this technique translate into perceived value for customers. If clients prefer traditional welding due to lower costs, it may directly impact the financial viability of adopting x-ray welding processes.
In summary, while x-ray welding offers notable advantages such as precision and reduced distortion, its challenges remain significant. A thorough understanding of both technical limitations and economic considerations allows industries to make informed choices regarding its application.
Case Studies in X-Ray Welding Practices
The significance of case studies in x-ray welding practices lies in their ability to provide real-world examples that illustrate both successes and obstacles encountered in this field. Through these studies, readers can gain insight into the practical applications of x-ray welding technology. They also highlight how theories and methodologies discussed in earlier sections manifest in actual welding projects. This exploration informs not just practitioners but also students and researchers seeking to understand the complexities of this technique.
Successful Implementations
Numerous successful implementations of x-ray welding across various industries emphasize its potential benefits. One notable example is the aerospace sector. Companies like Boeing have adopted x-ray welding to bond lightweight materials, enhancing fuel efficiency and reducing overall weight of the aircraft. In such implementations, x-ray welding allows for reduced thermal distortion, ensuring the structural integrity of aircraft components. The process also supports the requirements for stringent quality control and safety regulations in the aviation industry.
Another instance can be found in the automotive industry. Manufacturers utilize x-ray welding to join components of electric vehicles, where precision and reliable welds are crucial. Tesla and General Motors have integrated this welding method, benefiting from its ability to create strong joints while minimizing heat-affected zones. This leads to products that meet high performance standards and regulatory compliance.
Successful case studies reflect how innovations translate into practical applications, showcasing improvements in efficiency, quality, and safety.
Lessons Learned from Failures
Despite the successes, there are also lessons to be learned from failures in x-ray welding practices. One prevalent issue has been the misalignment of components prior to welding, which can lead to significant defects in the finished product. This has been observed in pharmaceutical equipment manufacturing, where stringent metal joining standards are necessary to prevent contamination. Investigation of failed welds revealed that thorough preparation and alignment checks are vital to achieving optimal results.
Another important lesson comes from a project in nuclear energy. A notable failure in a x-ray welded joint led to leaks due to improper calibration of the welding parameters. This emphasized the need for meticulous monitoring and calibration of the x-ray equipment during operations. Such incidents underscore the importance of training personnel adequately to avoid oversights that can compromise both safety and structural integrity.
End
The conclusion of this article serves as a vital recap to synthesize the major themes and insights presented throughout the exploration of X-Ray welding.
In this discussion, several key findings emerge. X-Ray welding has demonstrated itself as a leading technique, especially in sectors requiring precision and strength. The principles governing this process reveal it as not only innovative but also efficient in various applications, from industrial uses to medical technologies. One should note the importance of understanding both the advantages it offers and the challenges that can arise during its implementation.
Summary of Key Findings
- Precision and Quality: X-Ray welding allows for high-precision joins with minimal distortion. This is particularly important for components that must meet stringent quality standards.
- Safety Protocols: The health risks linked with X-Ray exposure necessitate stringent safety measures. The best practices highlighted in the previous sections emphasize the need for robust training and adherence to safety guidelines.
- Technological Advancements: The rapid rate of innovation in X-Ray welding equipment and methods indicates that this technique will continue to evolve. Keeping abreast of these advancements ensures that practitioners remain competitive and effective in their operations.
- Application Versatility: The applications of X-Ray welding span multiple fields, highlighting its versatility. Industries benefit from its use, including aerospace, automotive, and even medical sectors.
Final Thoughts on the Future of X-Ray Welding
Looking forward, the future of X-Ray welding appears promising. Continued research and development will likely unveil further enhancements to its methodology and equipment. Industries will increasingly recognize its importance as a go-to solution for complex welding tasks. With the growing emphasis on manufacturer accountability and quality assurance, techniques that assure lower defect rates will thrive.
Furthermore, educational institutions may develop curricula that focus on advanced welding technologies, fortifying the workforce with skills related to X-Ray welding processes. This aspect will ensure that professionals in the field are prepared for emerging challenges.
In summary, X-Ray welding is poised to take on an even greater role in manufacturing and research sectors globally, backed by the ongoing refinement of safety protocols and innovative technologies. It is an area worthy of exploration and investment as we anticipate its advancements.